- お役立ち記事
- Technological improvements in manufacturing and mass production of brackets with protrusions
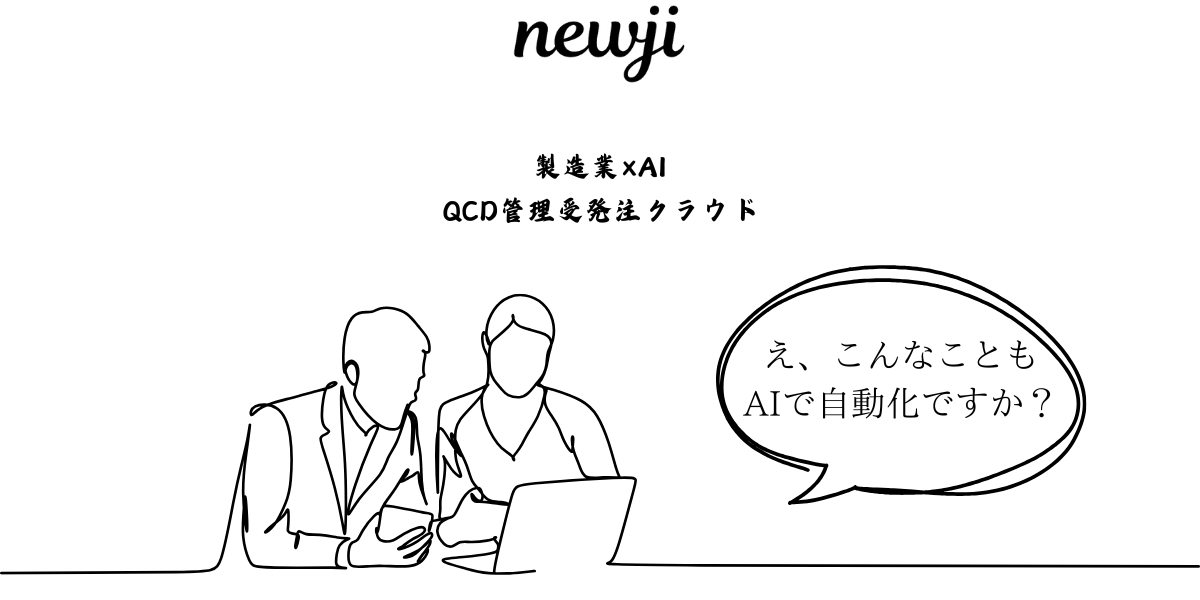
Technological improvements in manufacturing and mass production of brackets with protrusions
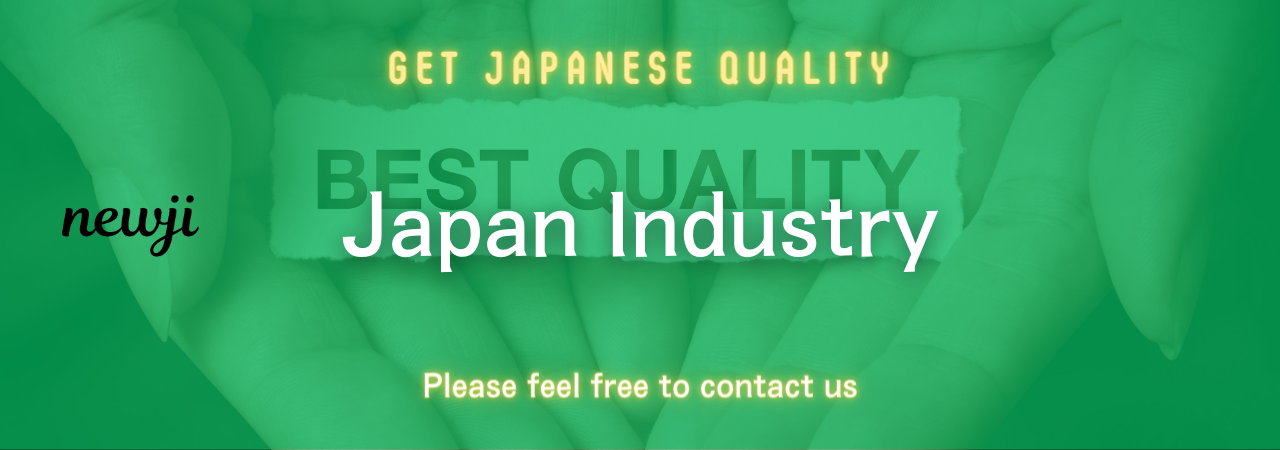
目次
Introduction to Technological Improvements in Manufacturing
Manufacturing has evolved significantly over the past few decades, especially with the advent of new technologies.
Among various products manufactured, brackets with protrusions have seen remarkable advancements.
These small yet essential components play a crucial role in a range of industries, from construction to electronics.
This article delves into the technological improvements in manufacturing and mass production of these specialized brackets.
The Role of Brackets with Protrusions
Brackets with protrusions are used to provide structural support or a fixed anchor point in various applications.
They are vital in ensuring stability and strength in construction projects, furniture assembling, machinery setups, and electronics enclosures.
Protrusions on brackets help in securing the components more effectively, reducing the risk of detachment or movement.
The demand for these brackets has increased, leading manufacturers to seek innovative ways to produce them efficiently.
Traditional Manufacturing Processes
Before modern advancements, traditional manufacturing processes for brackets with protrusions were labor-intensive and time-consuming.
These processes often involved manual labor for cutting, bending, and attaching the protrusions to the brackets.
While effective, traditional methods could not keep pace with the ever-increasing demand for precision and bulk production.
The quality control was also not as stringent, which could lead to discrepancies in the final product.
Challenges of Traditional Methods
Traditional methods posed several challenges.
Firstly, the production speed was relatively slow, which hindered the ability to meet large-scale orders promptly.
Secondly, maintaining consistency and precision in each bracket was difficult, often leading to variations that could compromise the product’s effectiveness.
Lastly, traditional methods relied heavily on skilled manual labor, which became increasingly expensive and scarce.
Advancements in Manufacturing Technology
As the demand for brackets with protrusions continued to grow, manufacturers turned to technological advancements to improve their production processes.
These innovations have revolutionized the industry, enabling faster, more precise, and more cost-effective manufacturing.
Computer-Aided Design (CAD) and Computer-Aided Manufacturing (CAM)
One of the most significant advancements in the manufacturing of brackets with protrusions is the use of Computer-Aided Design (CAD) and Computer-Aided Manufacturing (CAM).
CAD allows engineers to design highly detailed and accurate models of the brackets on a computer, reducing the room for error during the design phase.
These designs are then fed into CAM systems, which automate and control the manufacturing machines, ensuring that each bracket is produced to exact specifications.
This combination of CAD and CAM drastically reduces production time and enhances the quality and uniformity of the brackets.
3D Printing
3D printing, or additive manufacturing, has also made its mark in the production of brackets with protrusions.
This technology allows for the creation of complex shapes and designs that were difficult or impossible to achieve using traditional methods.
With 3D printing, manufacturers can produce prototype brackets quickly, test them, and make necessary adjustments before commencing full production.
This flexibility not only speeds up the production process but also allows for customization to meet specific client needs.
Automation and Robotics
The integration of automation and robotics in manufacturing lines has further enhanced the production of these brackets.
Robotic arms and automated assembly lines can handle repetitive tasks with high precision and speed, reducing human error and increasing efficiency.
This advancement allows for large-scale production while maintaining consistent quality across all products.
Automation also provides the added benefit of monitoring and quality control, as robotic systems can detect and correct deviations from set standards in real time.
Material Innovations
In addition to process improvements, there have been significant advancements in the materials used to manufacture brackets with protrusions.
Lightweight, durable materials such as aluminum alloys and high-strength plastics are now commonly used.
These materials provide the necessary strength and support while reducing overall weight, which is particularly beneficial in industries like aerospace and automotive.
Manufacturers are also exploring composite materials that offer improved resistance to environmental conditions such as corrosion and high temperatures.
Environmental and Economic Impact
Technological improvements in manufacturing also have positive environmental and economic impacts.
More efficient production methods lead to less waste, conserving resources and reducing the environmental footprint of manufacturing operations.
Economically, improved processes mean lower production costs, which can translate into lower prices for consumers and increased competitiveness for manufacturers.
Furthermore, advancements like automation reduce the reliance on human labor, which can lower operational costs and increase production scalability.
Future Directions
The future of manufacturing brackets with protrusions looks promising, with ongoing research and development aimed at further improvements.
Emerging technologies like artificial intelligence (AI) and machine learning are expected to optimize manufacturing processes even more, predicting and rectifying potential issues before they arise.
In addition, advancements in material science will likely lead to even stronger and more versatile materials for bracket production.
Conclusion
The technological improvements in the manufacturing and mass production of brackets with protrusions have brought about significant changes in how these essential components are produced.
From design innovations with CAD and CAM to the use of automation and new materials, the industry has become more efficient, cost-effective, and environmentally friendly.
As technology continues to evolve, the future holds even more exciting possibilities for manufacturing advancements.
These innovations not only meet the increasing demand but also contribute to higher standards of quality and reliability in various industries.
資料ダウンロード
QCD調達購買管理クラウド「newji」は、調達購買部門で必要なQCD管理全てを備えた、現場特化型兼クラウド型の今世紀最高の購買管理システムとなります。
ユーザー登録
調達購買業務の効率化だけでなく、システムを導入することで、コスト削減や製品・資材のステータス可視化のほか、属人化していた購買情報の共有化による内部不正防止や統制にも役立ちます。
NEWJI DX
製造業に特化したデジタルトランスフォーメーション(DX)の実現を目指す請負開発型のコンサルティングサービスです。AI、iPaaS、および先端の技術を駆使して、製造プロセスの効率化、業務効率化、チームワーク強化、コスト削減、品質向上を実現します。このサービスは、製造業の課題を深く理解し、それに対する最適なデジタルソリューションを提供することで、企業が持続的な成長とイノベーションを達成できるようサポートします。
オンライン講座
製造業、主に購買・調達部門にお勤めの方々に向けた情報を配信しております。
新任の方やベテランの方、管理職を対象とした幅広いコンテンツをご用意しております。
お問い合わせ
コストダウンが利益に直結する術だと理解していても、なかなか前に進めることができない状況。そんな時は、newjiのコストダウン自動化機能で大きく利益貢献しよう!
(Β版非公開)