- お役立ち記事
- Pressure testing of prototype parts and leak detection technology
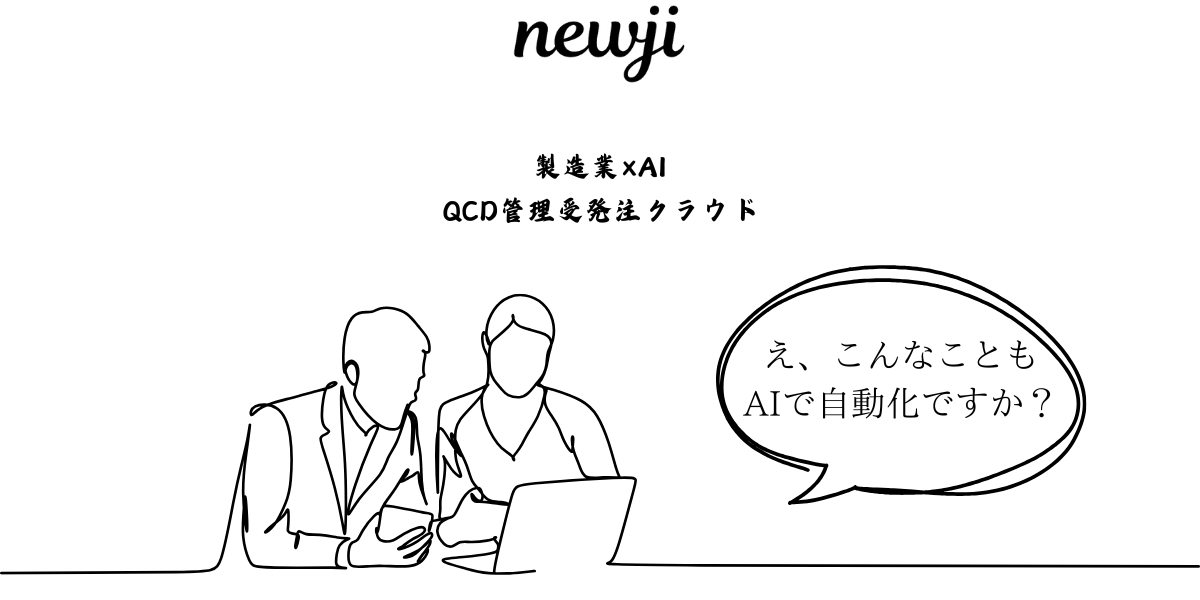
Pressure testing of prototype parts and leak detection technology
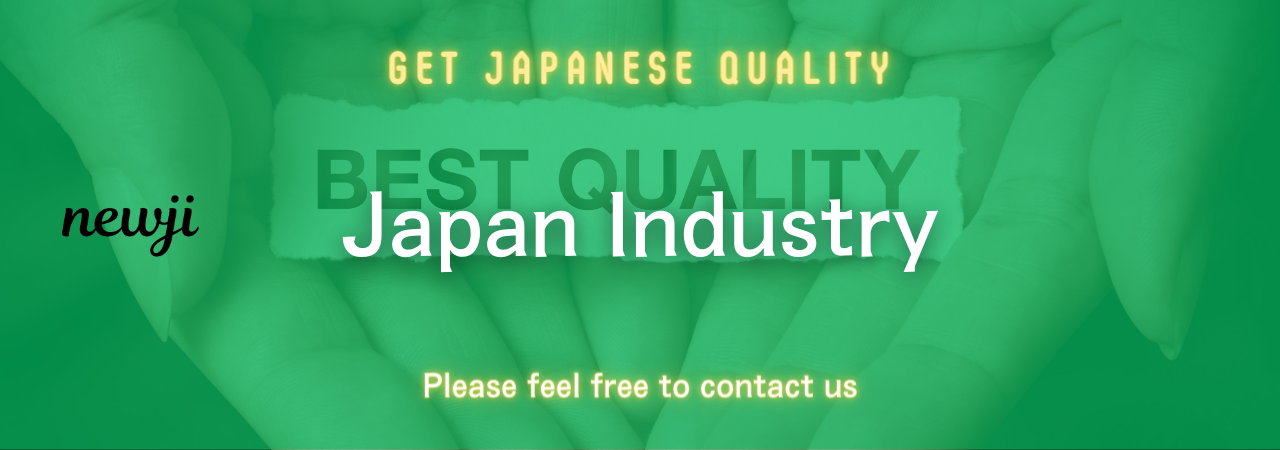
目次
Understanding Pressure Testing
Pressure testing is an essential process in manufacturing and engineering that ensures the integrity and reliability of prototype parts.
It involves subjecting components to specific pressures to verify their strength, durability, and performance under various conditions.
This testing can help identify flaws or weaknesses in a prototype, ensuring that any potential issues are addressed before mass production.
Pressure testing is crucial because it mimics the real-world conditions that a part will face during its lifespan.
By replicating these conditions, manufacturers can determine how a part will behave and ensure it meets safety and quality standards.
Testing is typically done using specially designed machines that apply controlled pressure to the prototype parts.
Key Steps in Pressure Testing
Several steps are involved in the pressure testing process.
Understanding these helps ensure the effectiveness of the testing and implementation of any necessary improvements:
Preparation
Before testing begins, the prototype parts must be prepared.
This preparation includes cleaning, inspecting, and documenting the parts to ensure there are no pre-existing defects.
Adequate preparation guarantees that the test results reflect the part’s actual performance rather than contamination or other extraneous factors.
Testing
Once prepared, the parts are subjected to a series of pressure tests.
The type of tests conducted depends on the part’s design and intended use.
Common methods include hydrostatic testing, where water or another fluid is used, and pneumatic testing, which uses air or gas.
Data Collection
During testing, data is collected to assess the part’s performance under pressure.
This information helps identify any structural weaknesses or potential points of failure.
Advanced diagnostic tools may be used to gather detailed data that offers insightful analysis.
Analysis and Reporting
After the data collection phase, the results are analyzed to determine the part’s reliability and safety.
Any anomalies or undesirable performance issues are documented, and the findings are compiled into a report.
This analysis is critical for making informed decisions on whether improvements are needed before proceeding to mass production.
The Importance of Leak Detection Technology
Alongside pressure testing, leak detection technology plays a vital role in ensuring the integrity of prototype parts.
Leaks can compromise the performance and safety of a product, making their detection critical in the early stages of development.
Leak detection technology helps identify even the smallest leaks that might go unnoticed through visual inspection.
This technology uses various methods to detect leaks, such as electronic detectors, dye injection, ultrasonic testing, and bubble testing.
Electronic Detectors
Electronic detectors are commonly used for their sensitivity and precision.
These devices can locate and measure the size of a leak by detecting the presence of gas or fluid escaping the part.
They are particularly useful in environments where visual inspection is difficult or impractical.
Dye Injection
In this method, a dye is injected into a closed system, and the part is placed under pressure.
The dye migrates to any leak sites, making them visible under specific lighting conditions.
Dye injection is particularly effective in detecting leaks that are too small to notice with the naked eye.
Ultrasonic Testing
Ultrasonic testing uses sound waves to detect leaks.
This method involves emitting high-frequency sound waves into the tested part.
When these waves encounter a leak, they create a distinct sound pattern that is captured by sensors.
Ultrasonic testing is non-invasive and provides quick results.
Bubble Testing
Bubble testing is a simple yet effective leak detection method.
Parts are submerged in a water tank, and pressure is applied.
Any escaping gas creates bubbles, indicating the presence of a leak.
This method is often used in conjunction with other techniques to confirm leak locations.
Integrating Pressure Testing and Leak Detection
The integration of pressure testing and leak detection is crucial for developing safe and reliable prototype parts.
When used together, these testing processes provide a comprehensive understanding of a part’s performance and integrity.
By identifying weaknesses and leaks early in development, manufacturers can make necessary adjustments that improve product quality and safety.
Benefits of Integration
Combining pressure testing with leak detection offers several benefits.
It enhances the reliability of testing results by providing a holistic view of a part’s structural integrity.
The combination also improves the accuracy of stress analysis and ultimately results in better-performing products.
Implementing Best Practices
To maximize the benefits of these technologies, manufacturers should adhere to best practices.
These include regular calibration of testing equipment, use of a suitable testing method based on the part’s design, and thorough analysis of test results.
Consistent application of these practices helps ensure the quality and safety of products.
Future Trends in Pressure Testing and Leak Detection
The fields of pressure testing and leak detection are continually evolving with technological advancements.
The future holds exciting possibilities as digital technologies become more integrated into these processes.
Smart Sensors and IoT
The advent of smart sensors and the Internet of Things (IoT) is expected to revolutionize pressure testing and leak detection.
These innovations will allow for real-time data monitoring and remote diagnostics, making the testing processes more efficient and accurate.
Artificial Intelligence
Artificial Intelligence (AI) is poised to make significant impacts in automating data analysis and improving decision-making processes.
With AI, predictive analytics can help foresee potential failures before they occur, enhancing product development cycles.
Conclusion
Pressure testing and leak detection are fundamental components of developing prototype parts that meet safety and performance standards.
By understanding the processes, integrating advanced technologies, and adhering to best practices, manufacturers can ensure their products are reliable and of the highest quality.
Staying informed about emerging trends will further empower industries to innovate and enhance product integrity in the years to come.
資料ダウンロード
QCD調達購買管理クラウド「newji」は、調達購買部門で必要なQCD管理全てを備えた、現場特化型兼クラウド型の今世紀最高の購買管理システムとなります。
ユーザー登録
調達購買業務の効率化だけでなく、システムを導入することで、コスト削減や製品・資材のステータス可視化のほか、属人化していた購買情報の共有化による内部不正防止や統制にも役立ちます。
NEWJI DX
製造業に特化したデジタルトランスフォーメーション(DX)の実現を目指す請負開発型のコンサルティングサービスです。AI、iPaaS、および先端の技術を駆使して、製造プロセスの効率化、業務効率化、チームワーク強化、コスト削減、品質向上を実現します。このサービスは、製造業の課題を深く理解し、それに対する最適なデジタルソリューションを提供することで、企業が持続的な成長とイノベーションを達成できるようサポートします。
オンライン講座
製造業、主に購買・調達部門にお勤めの方々に向けた情報を配信しております。
新任の方やベテランの方、管理職を対象とした幅広いコンテンツをご用意しております。
お問い合わせ
コストダウンが利益に直結する術だと理解していても、なかなか前に進めることができない状況。そんな時は、newjiのコストダウン自動化機能で大きく利益貢献しよう!
(Β版非公開)