- お役立ち記事
- Optimization of drying equipment design and manufacturing technology
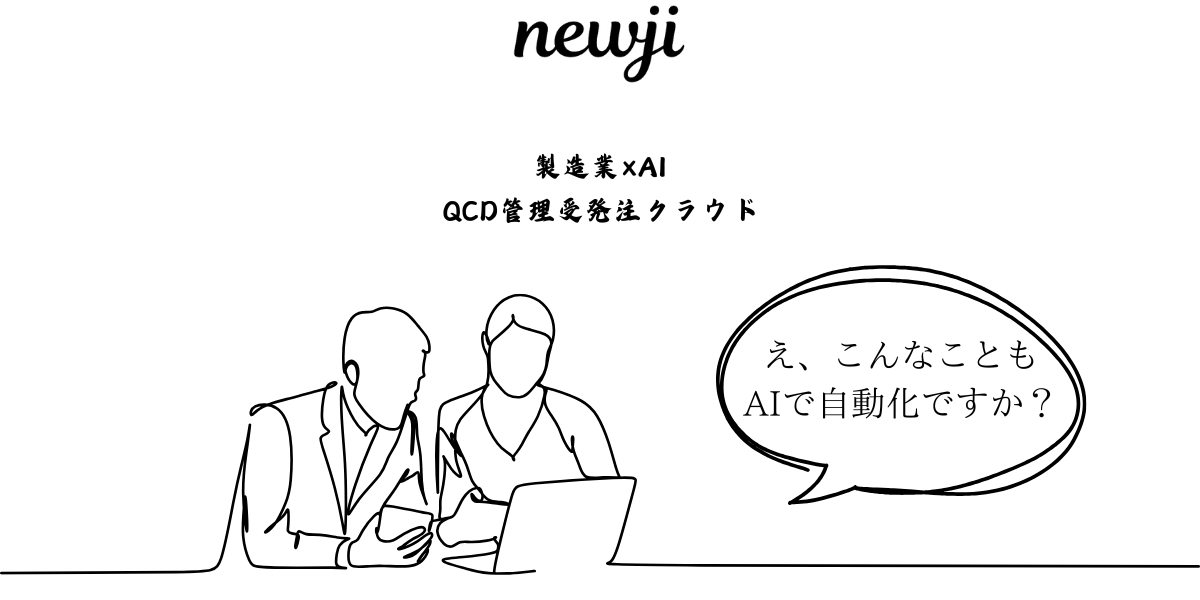
Optimization of drying equipment design and manufacturing technology
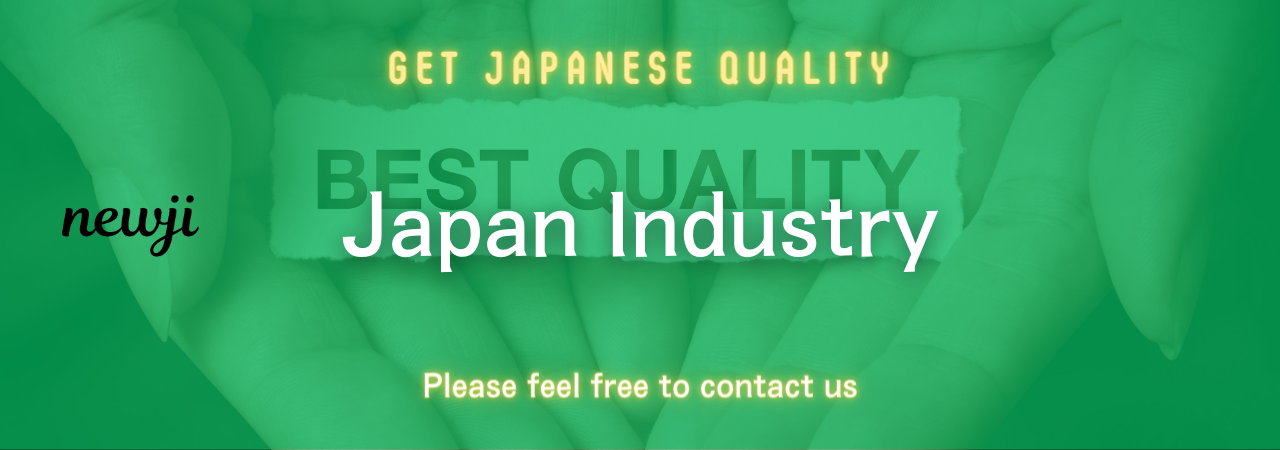
目次
Understanding Drying Equipment
Drying equipment plays a crucial role in various industries by removing moisture from materials.
This process is essential for maintaining product quality and prolonging storage life.
Commonly used in food, pharmaceutical, chemical, and industrial applications, drying equipment ensures that products are preserved and prepared for further processing or distribution.
Advancements in drying technology have revolutionized how manufacturers approach the drying process.
With the increasing demand for energy-efficient and cost-effective solutions, optimizing the design and manufacture of drying equipment has become a focal point for industry innovators.
The Importance of Optimizing Drying Equipment
Optimization of drying equipment design and manufacturing technology is important for several reasons.
First, it enhances efficiency by minimizing energy consumption.
In a world where sustainability is a priority, reducing the energy needed for drying processes significantly benefits both the environment and the bottom line of a business.
Another benefit is improving product quality.
By optimizing the drying parameters, manufacturers can better control the end product’s consistency and quality, ensuring that it meets industry standards and customer expectations.
Additionally, optimizing drying equipment helps to reduce production costs.
By streamlining operations and improving equipment longevity, businesses can lower maintenance expenses and operational downtime.
Energy Efficiency and Environmental Impact
A primary focus of optimizing drying equipment is boosting energy efficiency.
Since drying processes typically require substantial energy, there is a direct economic incentive to minimize this consumption.
Innovative design strategies in drying equipment can significantly reduce energy use.
This reduction not only lowers operational costs but also decreases the overall environmental impact of the manufacturing process.
By adopting energy-efficient technologies, companies can lessen their carbon footprint and contribute positively to sustainability objectives.
This shift helps businesses align with regulatory standards and the broader push towards environmental consciousness.
Advancements in Drying Technology
Several technological advancements have propelled the optimization of drying equipment.
One such advancement is the automation of drying processes.
Through intelligent control systems, parameters such as temperature, air velocity, and humidity can be precisely monitored and adjusted in real-time, ensuring optimal drying conditions.
Another significant advancement is the development of novel drying techniques.
These include the use of microwave drying, vacuum drying, and freeze-drying techniques, which offer improved drying rates and product quality.
These methods reduce drying time and enhance the uniformity and stability of sensitive materials.
Moreover, computational modeling and simulation have become integral in the design and optimization of drying systems.
By utilizing advanced modeling software, engineers can simulate drying processes, allowing them to identify potential issues and optimize system designs without the need for costly physical prototypes.
Optimizing the Design of Drying Equipment
The design of drying equipment is critical to its efficiency and effectiveness.
Optimizing this design involves several considerations, each addressing different aspects of the drying process.
One key consideration is the selection of materials for construction.
Using materials that can withstand desired temperatures and humidity levels without corroding or degrading enhances equipment longevity and performance.
Another design factor is the configuration of the drying chamber.
Engineers must carefully design the airflow patterns to ensure uniform distribution of heat and air, which directly impacts drying quality and speed.
Additionally, the type and placement of heating elements must be carefully considered to optimize energy use and drying performance.
Radiant and convective heating elements are often employed, and their placement can dramatically affect the uniformity of the drying process.
Manufacturing Technology Improvements
In addition to design, advances in manufacturing technology have played a significant role in optimizing drying equipment.
Precision manufacturing techniques, such as laser cutting and CNC machining, allow for the creation of components that fit more tightly, improving insulation and reducing heat loss.
The adoption of Industry 4.0 technologies in manufacturing processes further aids in optimizing equipment design.
Smart sensors and IoT devices enable real-time monitoring and diagnostics, allowing manufacturers to predict maintenance needs and address issues before they impact production.
Furthermore, the use of 3D printing in prototyping offers numerous advantages.
It reduces the time needed to test new designs and accelerates the timeline from design to deployment.
Challenges in Optimization
While many advancements have improved the optimization of drying equipment, challenges still exist.
One major challenge is the balance between reducing energy use and maintaining product quality.
While lowering temperatures can save energy, it may not achieve the desired drying outcomes for certain products.
There is also the challenge of scale.
Designs that work well on a small scale may not be directly applicable to larger industrial settings without significant adjustments.
Cost is another consideration.
While new technologies can offer efficiencies, the initial investment can be substantial.
Companies must weigh these costs against long-term savings to determine the best course of action.
The Future of Drying Equipment Optimization
Looking forward, the future of drying equipment optimization is promising.
Continuous research and development are poised to uncover further efficiencies and innovations.
One area of interest is the integration of artificial intelligence.
AI has the potential to analyze vast amounts of data, providing insights and recommendations for further improving the drying process.
Another future direction lies in material science advancements, promising the development of new materials that enhance drying efficiency and equipment durability.
Ultimately, the ongoing optimization of drying equipment design and manufacturing technology will continue to serve as an essential component for industries worldwide.
By staying abreast of technological trends and leveraging innovative solutions, businesses can significantly enhance their operational efficiency, product quality, and environmental sustainability.
資料ダウンロード
QCD調達購買管理クラウド「newji」は、調達購買部門で必要なQCD管理全てを備えた、現場特化型兼クラウド型の今世紀最高の購買管理システムとなります。
ユーザー登録
調達購買業務の効率化だけでなく、システムを導入することで、コスト削減や製品・資材のステータス可視化のほか、属人化していた購買情報の共有化による内部不正防止や統制にも役立ちます。
NEWJI DX
製造業に特化したデジタルトランスフォーメーション(DX)の実現を目指す請負開発型のコンサルティングサービスです。AI、iPaaS、および先端の技術を駆使して、製造プロセスの効率化、業務効率化、チームワーク強化、コスト削減、品質向上を実現します。このサービスは、製造業の課題を深く理解し、それに対する最適なデジタルソリューションを提供することで、企業が持続的な成長とイノベーションを達成できるようサポートします。
オンライン講座
製造業、主に購買・調達部門にお勤めの方々に向けた情報を配信しております。
新任の方やベテランの方、管理職を対象とした幅広いコンテンツをご用意しております。
お問い合わせ
コストダウンが利益に直結する術だと理解していても、なかなか前に進めることができない状況。そんな時は、newjiのコストダウン自動化機能で大きく利益貢献しよう!
(Β版非公開)