- お役立ち記事
- Discovering the Roots of Japanese Manufacturing: From Tree Rings to Timeless Craftsmanship
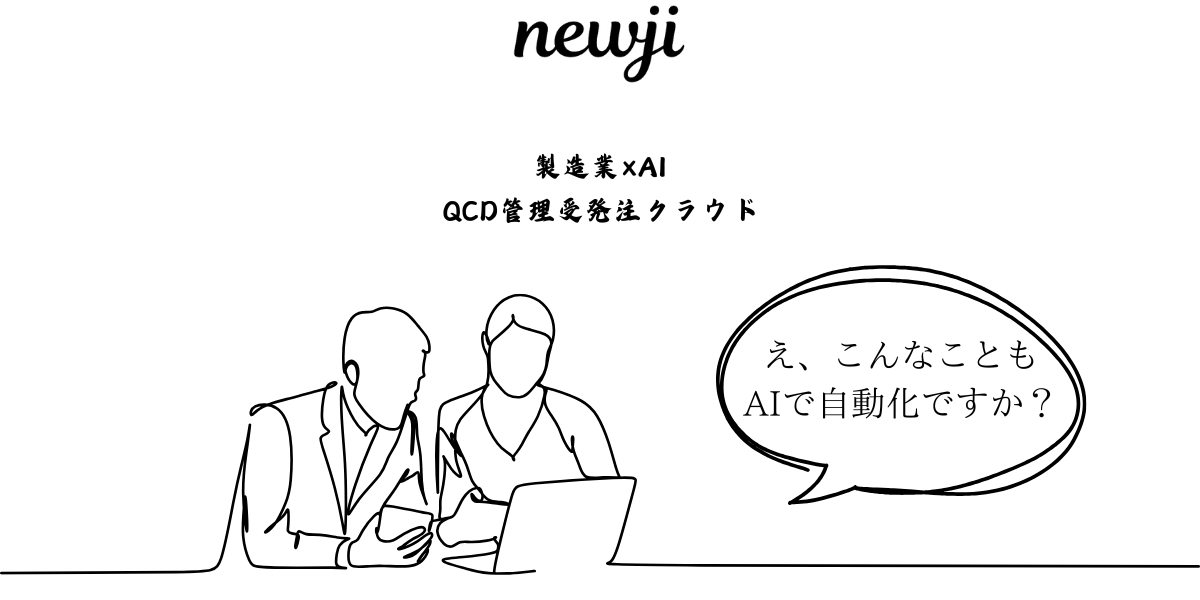
Discovering the Roots of Japanese Manufacturing: From Tree Rings to Timeless Craftsmanship
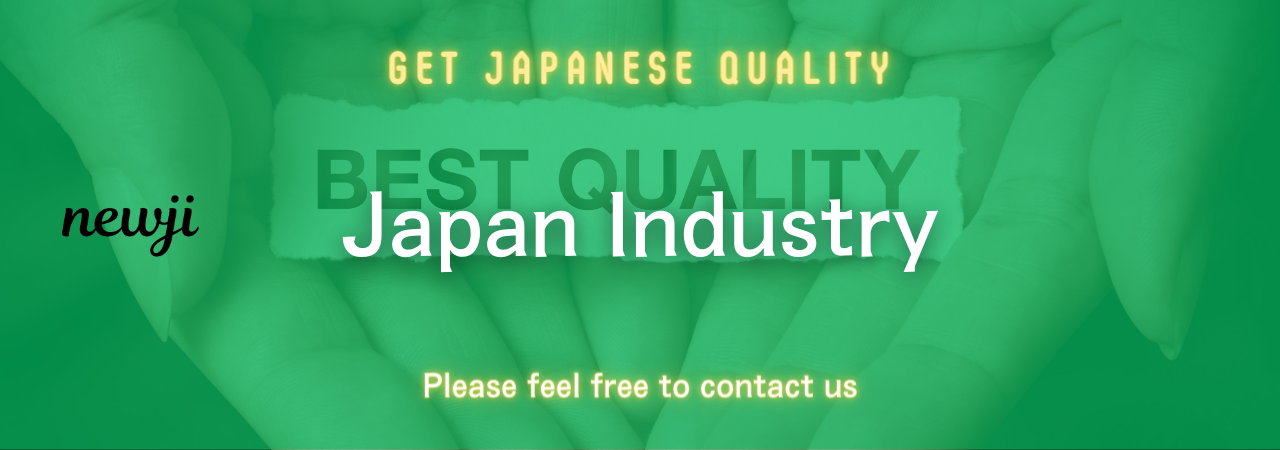
目次
Introduction to Japanese Manufacturing Excellence
Japanese manufacturing is renowned worldwide for its quality, precision, and efficiency. The roots of this excellence can be traced back to traditional craftsmanship, continuous improvement practices, and a deep-seated culture of innovation. This article explores the foundations of Japanese manufacturing, delving into the technical skills, procurement strategies, and best practices that have positioned Japan as a global leader in manufacturing.
Historical Foundations of Japanese Manufacturing
The origins of Japanese manufacturing excellence lie in centuries-old craftsmanship traditions. Artisans in Japan have long emphasized meticulous attention to detail, the pursuit of perfection, and a commitment to quality. This cultural heritage has seamlessly integrated with modern manufacturing practices, creating a unique blend of tradition and innovation.
Kaizen: The Philosophy of Continuous Improvement
Central to Japanese manufacturing is the concept of Kaizen, which translates to “continuous improvement.” Kaizen encourages all employees to seek incremental improvements in processes, products, and services. This philosophy fosters a culture where efficiency and quality are constantly enhanced, leading to sustainable growth and competitiveness.
Lean Manufacturing: Efficiency and Waste Reduction
Lean manufacturing, another cornerstone of Japanese production, focuses on maximizing value while minimizing waste. By streamlining processes and eliminating non-essential activities, Japanese manufacturers achieve higher productivity and cost-effectiveness. Techniques such as Just-In-Time (JIT) inventory and Total Quality Management (TQM) are integral to this approach.
Procurement and Purchasing in Japanese Manufacturing
Effective procurement and purchasing strategies are vital components of Japanese manufacturing success. Japanese companies emphasize building strong, long-term relationships with suppliers, ensuring reliability, quality, and mutual benefit.
Strategic Supplier Relationships
Japanese manufacturers prioritize collaboration with suppliers over mere transactional interactions. By fostering partnerships, companies can ensure consistent quality, timely deliveries, and innovation. This collaborative approach often involves sharing information, joint problem-solving, and mutual investment in process improvements.
Supplier Selection and Evaluation
The process of selecting suppliers in Japan is rigorous and thorough. Criteria include not only cost and capability but also the supplier’s commitment to quality and continuous improvement. Regular evaluations and audits are conducted to maintain high standards and address any issues proactively.
Advantages of Japanese Manufacturing Practices
Japanese manufacturing offers several advantages that contribute to its global reputation. These advantages stem from the integration of traditional values with modern techniques, resulting in superior products and efficient processes.
High Quality and Reliability
Japanese manufacturers are synonymous with high-quality products. Strict quality control measures, meticulous attention to detail, and a culture that prioritizes excellence ensure that products meet and exceed customer expectations consistently.
Cost Efficiency through Lean Practices
Through lean manufacturing and continuous improvement, Japanese companies achieve significant cost savings. By optimizing production processes, reducing waste, and enhancing efficiency, manufacturers can offer competitive pricing without compromising on quality.
Innovation and Technological Advancement
Japan’s focus on innovation drives the development of advanced technologies and manufacturing techniques. Continuous investment in research and development enables companies to stay ahead of industry trends and meet evolving market demands.
Challenges in Japanese Manufacturing
Despite its strengths, Japanese manufacturing faces several challenges that need to be addressed to maintain its competitive edge on the global stage.
Aging Workforce
Japan is experiencing a demographic shift with an aging workforce. This trend poses challenges in maintaining labor-intensive manufacturing processes and requires strategies for workforce renewal and automation.
Global Competition
As global competition intensifies, Japanese manufacturers must continuously innovate to differentiate themselves. Competing with emerging economies that offer lower production costs requires a focus on value-added activities and technological advancements.
Supply Chain Disruptions
Global supply chain disruptions, such as those caused by natural disasters or geopolitical tensions, can impact Japanese manufacturers. Building resilient supply chains and diversifying sources are crucial strategies to mitigate these risks.
Supplier Negotiation Techniques in Japan
Negotiating with Japanese suppliers requires an understanding of cultural nuances and business practices. Effective negotiation strategies can lead to mutually beneficial agreements and long-term partnerships.
Building Trust and Relationships
In Japan, trust and relationships are paramount in business dealings. Taking the time to build rapport, showing respect, and demonstrating commitment to the partnership can facilitate smoother negotiations and foster cooperation.
Patience and Consensus Building
Japanese negotiation style tends to be patient and consensus-driven. Decisions are often made collectively, requiring time and multiple discussions. Patience and persistence are essential to achieving successful outcomes.
Transparent Communication
Clear and honest communication helps in avoiding misunderstandings and aligning expectations. Providing detailed information and being transparent about needs and constraints can enhance the negotiation process.
Market Conditions Impacting Japanese Manufacturing
The global market environment significantly influences Japanese manufacturing strategies. Understanding these conditions is essential for making informed procurement and purchasing decisions.
Global Economic Trends
Economic fluctuations, such as recessions or periods of growth, affect demand for manufactured goods. Japanese companies must adapt their strategies to align with global economic conditions, ensuring resilience and sustained performance.
Technological Advancements
Rapid technological changes present both opportunities and challenges. Adopting new technologies can lead to improved processes and products, but requires investment and adaptation to stay competitive.
Trade Policies and Regulations
International trade policies and regulations impact Japanese manufacturers’ ability to export products and source materials. Staying informed about policy changes and complying with regulatory requirements are critical for maintaining market access and operational efficiency.
Best Practices in Japanese Procurement and Purchasing
Adopting best practices from Japanese procurement and purchasing can enhance the efficiency and effectiveness of supply chain operations.
Integrated Supply Chain Management
An integrated approach to supply chain management ensures seamless coordination between procurement, production, and distribution. This integration leads to better forecasting, inventory management, and responsiveness to market changes.
Supplier Development Programs
Investing in supplier development helps improve the capabilities and performance of suppliers. Providing training, resources, and support enables suppliers to meet quality standards and contribute to mutual growth.
Data-Driven Decision Making
Leveraging data and analytics in procurement processes leads to more informed and strategic decisions. Analyzing market trends, supplier performance, and cost structures can optimize purchasing strategies and enhance overall efficiency.
Quality Control and Assurance in Japanese Manufacturing
Quality control is a fundamental aspect of Japanese manufacturing, ensuring that products consistently meet high standards.
Total Quality Management (TQM)
TQM involves the continuous improvement of processes, products, and services by involving all employees. This holistic approach ensures that quality is embedded in every aspect of the manufacturing process.
Statistical Quality Control
Using statistical methods to monitor and control quality helps in identifying and addressing defects early in the production process. This proactive approach minimizes waste and enhances product reliability.
Customer Feedback Integration
Incorporating customer feedback into the manufacturing process allows companies to align their products with customer expectations. Continuous feedback loops ensure that quality improvements are relevant and impactful.
Logistics and Supply Chain Management
Efficient logistics and supply chain management are critical for the success of Japanese manufacturing operations.
Just-In-Time (JIT) Inventory
JIT inventory systems aim to reduce inventory costs by receiving goods only as they are needed in the production process. This approach minimizes storage costs and reduces waste, contributing to overall efficiency.
Advanced Logistics Solutions
Adopting advanced logistics solutions, such as automated warehousing and real-time tracking systems, enhances the speed and reliability of supply chain operations. These technologies improve coordination and reduce lead times.
Risk Management Strategies
Implementing robust risk management strategies helps in identifying potential disruptions and developing contingency plans. This preparedness ensures continuity and resilience in supply chain operations.
Production Management and Engineering
Effective production management and engineering practices are essential for maintaining high levels of efficiency and quality in manufacturing.
Process Optimization
Optimizing production processes through techniques like value stream mapping and bottleneck analysis leads to increased productivity and reduced cycle times. Continuous evaluation and improvement are key to sustaining operational excellence.
Automation and Advanced Manufacturing Technologies
Integrating automation and advanced manufacturing technologies, such as robotics and smart manufacturing systems, enhances precision and efficiency. These technologies enable manufacturers to scale production while maintaining quality standards.
Workforce Development
Investing in workforce development ensures that employees possess the necessary skills and knowledge to operate advanced manufacturing systems. Continuous training and education foster a capable and adaptable workforce.
Factory Efficiency and Automation
Factory efficiency and automation are integral to modern Japanese manufacturing, driving productivity and reducing operational costs.
Smart Factory Implementation
Smart factories use interconnected systems and digital technologies to monitor, control, and optimize manufacturing processes in real-time. This integration leads to higher efficiency, flexibility, and responsiveness to changes.
Robotics and Automation
Robotic systems and automated machinery enhance production capabilities by performing repetitive and precise tasks with high accuracy. Automation reduces human error, increases output, and allows for the reallocation of human resources to more complex tasks.
Energy Efficiency and Sustainability
Focusing on energy-efficient practices and sustainable manufacturing processes not only reduces operational costs but also aligns with global sustainability goals. Implementing eco-friendly technologies and optimizing resource usage contribute to long-term sustainability.
Case Studies: Success Stories in Japanese Manufacturing
Examining real-world examples of Japanese manufacturing success provides valuable insights into effective practices and strategies.
Toyota Production System (TPS)
The Toyota Production System is a benchmark for lean manufacturing and continuous improvement. TPS emphasizes waste reduction, just-in-time production, and respect for people, driving Toyota’s reputation for reliability and efficiency.
Panasonic’s Supply Chain Excellence
Panasonic has established a highly efficient supply chain by fostering strong partnerships with suppliers, leveraging advanced logistics, and implementing robust quality control measures. These practices ensure timely delivery and high-quality products.
Canon’s Commitment to Innovation
Canon’s focus on innovation and technological advancement has enabled the company to maintain a competitive edge in the imaging and printing industries. Continuous research and development investments drive product excellence and market leadership.
Future Trends in Japanese Manufacturing
As the global landscape evolves, Japanese manufacturing must adapt to emerging trends and challenges to maintain its leadership.
Digital Transformation
The ongoing digital transformation involves integrating digital technologies into all aspects of manufacturing. This shift enhances data-driven decision-making, improves process automation, and fosters innovation.
Sustainability and Green Manufacturing
Increasing emphasis on sustainability drives the adoption of green manufacturing practices. Japanese companies are investing in renewable energy, reducing carbon emissions, and developing eco-friendly products to meet global environmental standards.
Globalization and Localization
Balancing globalization with localization strategies allows Japanese manufacturers to expand their global footprint while catering to local market needs. This approach enhances adaptability and responsiveness to diverse consumer preferences.
Conclusion: Embracing the Legacy and Future of Japanese Manufacturing
Japanese manufacturing stands as a testament to the harmonious blend of traditional craftsmanship and modern innovation. By adhering to principles of continuous improvement, fostering strong supplier relationships, and embracing advanced technologies, Japanese manufacturers continue to set benchmarks for excellence. As the industry navigates future challenges and opportunities, the foundational values and best practices of Japanese manufacturing will remain pivotal in sustaining its global leadership.
資料ダウンロード
QCD調達購買管理クラウド「newji」は、調達購買部門で必要なQCD管理全てを備えた、現場特化型兼クラウド型の今世紀最高の購買管理システムとなります。
ユーザー登録
調達購買業務の効率化だけでなく、システムを導入することで、コスト削減や製品・資材のステータス可視化のほか、属人化していた購買情報の共有化による内部不正防止や統制にも役立ちます。
NEWJI DX
製造業に特化したデジタルトランスフォーメーション(DX)の実現を目指す請負開発型のコンサルティングサービスです。AI、iPaaS、および先端の技術を駆使して、製造プロセスの効率化、業務効率化、チームワーク強化、コスト削減、品質向上を実現します。このサービスは、製造業の課題を深く理解し、それに対する最適なデジタルソリューションを提供することで、企業が持続的な成長とイノベーションを達成できるようサポートします。
オンライン講座
製造業、主に購買・調達部門にお勤めの方々に向けた情報を配信しております。
新任の方やベテランの方、管理職を対象とした幅広いコンテンツをご用意しております。
お問い合わせ
コストダウンが利益に直結する術だと理解していても、なかなか前に進めることができない状況。そんな時は、newjiのコストダウン自動化機能で大きく利益貢献しよう!
(Β版非公開)