- お役立ち記事
- New technologies and process improvements in wind turbine blade manufacturing
月間77,185名の
製造業ご担当者様が閲覧しています*
*2025年2月28日現在のGoogle Analyticsのデータより
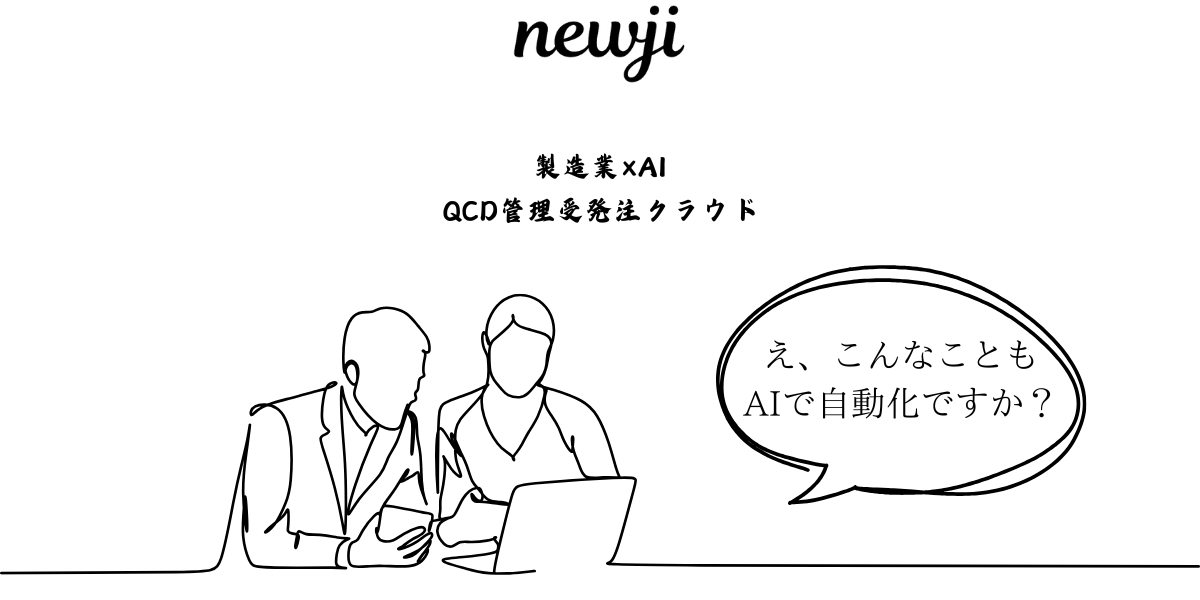
New technologies and process improvements in wind turbine blade manufacturing
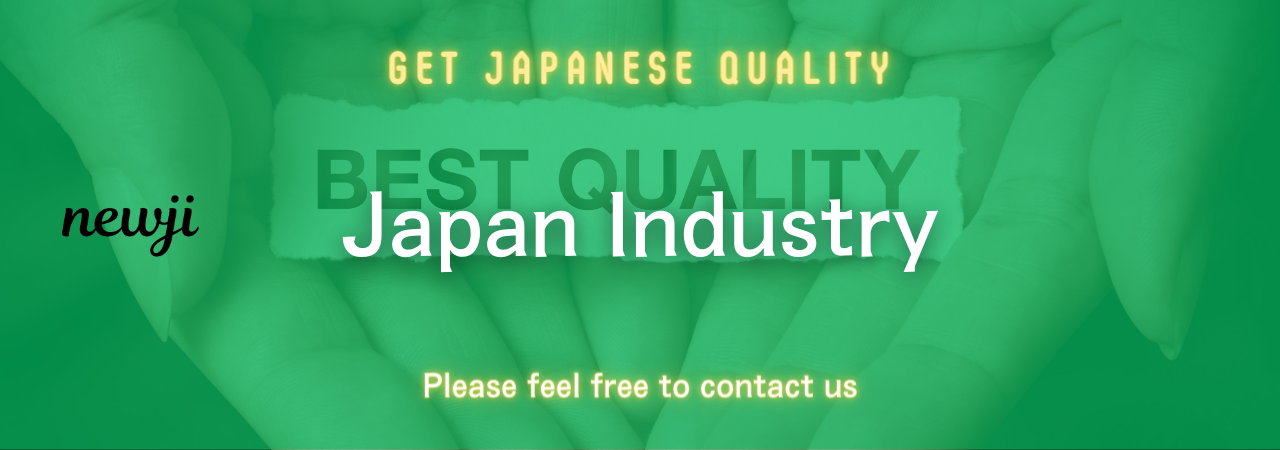
目次
Introduction to Wind Turbine Blade Manufacturing
Wind energy is one of the most promising sources of renewable energy in the world today.
Capturing wind energy effectively involves several elements, but none as critical as the wind turbine blades themselves.
As technology advances, so too does the manufacturing process for these blades.
New technologies and process improvements are transforming how these essential components are made, enhancing their efficiency and sustainability.
In this article, we’ll explore some innovations taking place in this field and why they are pivotal to the future of clean energy.
The Importance of Wind Turbine Blades
Wind turbine blades are crucial for converting wind energy into mechanical energy, which is then turned into electricity.
Their aerodynamic design allows them to capture kinetic energy from the wind with maximum efficiency.
Blades must be lightweight yet incredibly robust to endure various weather conditions.
They also need to be manufactured with precision to perform optimally without causing mechanical stress to the turbine system.
Given these requirements, innovation in their design and production processes is key to advancing wind energy as a reliable power source.
New Materials in Blade Manufacturing
One of the most significant areas of advancement in wind turbine blade manufacturing is the development of new materials.
Traditionally, blades have been made from fiberglass, a material known for its durability and cost-effectiveness.
However, newer materials like carbon fiber are being integrated due to their excellent strength-to-weight ratio.
Although carbon fiber is more expensive, its use can lead to longer blades capable of capturing more wind, thus generating more power.
Another promising material is thermoplastic resin.
Unlike the traditional thermoset composites that are hard to recycle, thermoplastics are more easily broken down and reused, aligning with the broader movement towards sustainability in the industry.
This innovation not only enhances the blade’s performance but also addresses environmental concerns regarding end-of-life disposal.
Improved Manufacturing Processes
Aside from materials, the processes used to manufacture wind turbine blades are undergoing incredible improvements.
One such breakthrough is automated and robotic systems in blade production.
Automation helps in achieving higher precision in blade manufacturing while reducing human error.
It also speeds up the production process and reduces costs over time by minimizing waste.
Additive manufacturing, commonly known as 3D printing, is another cutting-edge technology that holds great promise.
It allows for the creation of highly complex blade structures that would be challenging to manufacture using traditional methods.
3D printing can also facilitate on-site repairs and modifications, reducing downtime and maintenance costs.
Reducing Energy Consumption in Production
As the world shifts towards more sustainable practices, reducing energy consumption in manufacturing processes becomes crucial.
Wind turbine blade manufacturing is no exception.
New processes emphasize minimizing energy use, such as using advanced curing techniques for composite materials that require less heat.
Additionally, digital tools are now utilized to optimize designs before manufacturing, ensuring that resources are only used where necessary.
Quality Control and Testing Advancements
With the increase in size and complexity of blades, quality control and testing techniques have also had to evolve.
Non-destructive testing (NDT) has been enhanced to provide more accurate assessments of blade integrity and durability.
Techniques such as ultrasound, laser scanning, and thermography are now more widely used to detect internal defects that may not be visible on the surface.
These methods not only ensure the reliability and safety of blades but can also extend their operational life.
Automated inspection systems further streamline this process, enabling continuous monitoring and quick response to detected issues.
Digital Twin Technology
Another fascinating advancement in wind turbine blade manufacturing is the implementation of digital twin technology.
A digital twin is a virtual replica of the physical blade, used for simulation and analysis.
Manufacturers can simulate various scenarios and stress tests to predict blade performance and identify potential issues before the blades are even made.
This approach allows for faster iterations in the design phase and reduces costly errors that might otherwise occur later in production or operation.
Digital twins also facilitate better maintenance routines and real-time monitoring, potentially saving considerable amounts on repairs and replacements over the blades’ lifespan.
Environmental and Economic Impacts
The widespread adoption of these new technologies and process improvements does not only benefit blade performance—it also has significant environmental and economic impacts.
By shifting to more sustainable materials and processes, the wind energy sector can dramatically reduce its carbon footprint.
This aligns with global efforts to combat climate change by fostering cleaner production and recycling methods.
From an economic perspective, these advancements help reduce the cost of energy production.
As efficiency increases, the overall cost of harnessing wind energy decreases, making it more competitive with traditional energy sources like fossil fuels.
As a result, the adoption of wind energy could accelerate, driving economic growth through job creation in manufacturing, installation, and maintenance sectors.
Conclusion
In summary, the innovations in wind turbine blade manufacturing, from new materials to improved processes and technologies, represent significant steps forward in the renewable energy industry.
These advancements not only enhance the performance and efficiency of wind turbines but also contribute positively to environmental sustainability and economic viability.
As the global demand for clean energy continues to rise, these improvements in manufacturing will play a crucial role in meeting energy needs in a sustainable manner.
With ongoing research and development, the future of wind energy looks promising, powered by the next generation of wind turbine blades.
資料ダウンロード
QCD管理受発注クラウド「newji」は、受発注部門で必要なQCD管理全てを備えた、現場特化型兼クラウド型の今世紀最高の受発注管理システムとなります。
ユーザー登録
受発注業務の効率化だけでなく、システムを導入することで、コスト削減や製品・資材のステータス可視化のほか、属人化していた受発注情報の共有化による内部不正防止や統制にも役立ちます。
NEWJI DX
製造業に特化したデジタルトランスフォーメーション(DX)の実現を目指す請負開発型のコンサルティングサービスです。AI、iPaaS、および先端の技術を駆使して、製造プロセスの効率化、業務効率化、チームワーク強化、コスト削減、品質向上を実現します。このサービスは、製造業の課題を深く理解し、それに対する最適なデジタルソリューションを提供することで、企業が持続的な成長とイノベーションを達成できるようサポートします。
製造業ニュース解説
製造業、主に購買・調達部門にお勤めの方々に向けた情報を配信しております。
新任の方やベテランの方、管理職を対象とした幅広いコンテンツをご用意しております。
お問い合わせ
コストダウンが利益に直結する術だと理解していても、なかなか前に進めることができない状況。そんな時は、newjiのコストダウン自動化機能で大きく利益貢献しよう!
(β版非公開)