- お役立ち記事
- Mastering Electromagnetic Compatibility: Essential EMC Measures in Japanese Manufacturing for Interference-Free Electronics
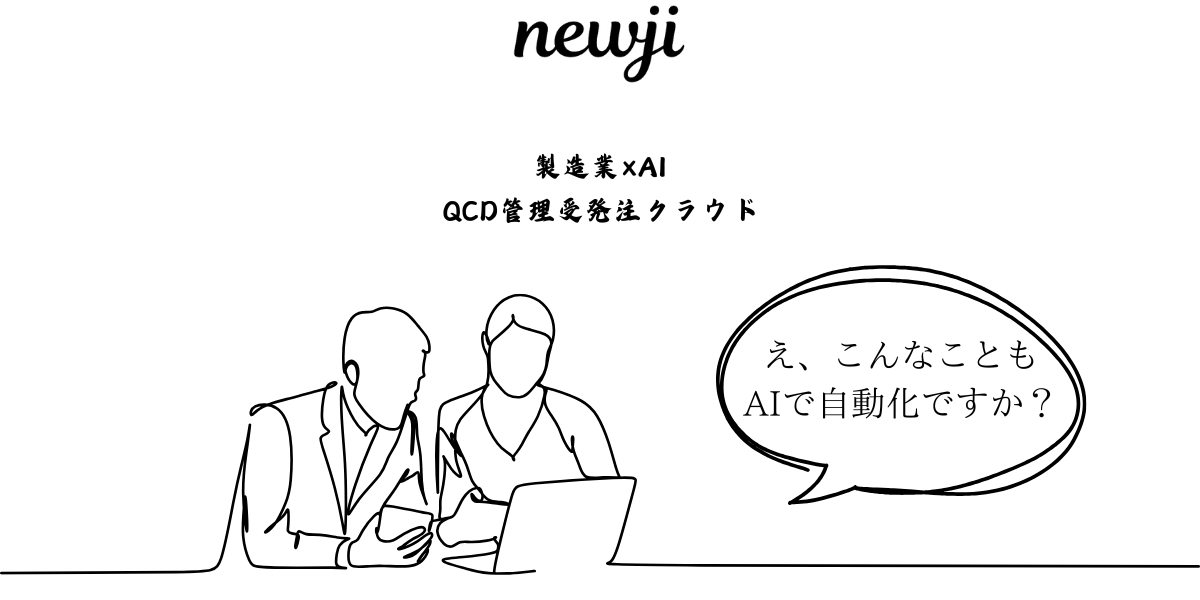
Mastering Electromagnetic Compatibility: Essential EMC Measures in Japanese Manufacturing for Interference-Free Electronics
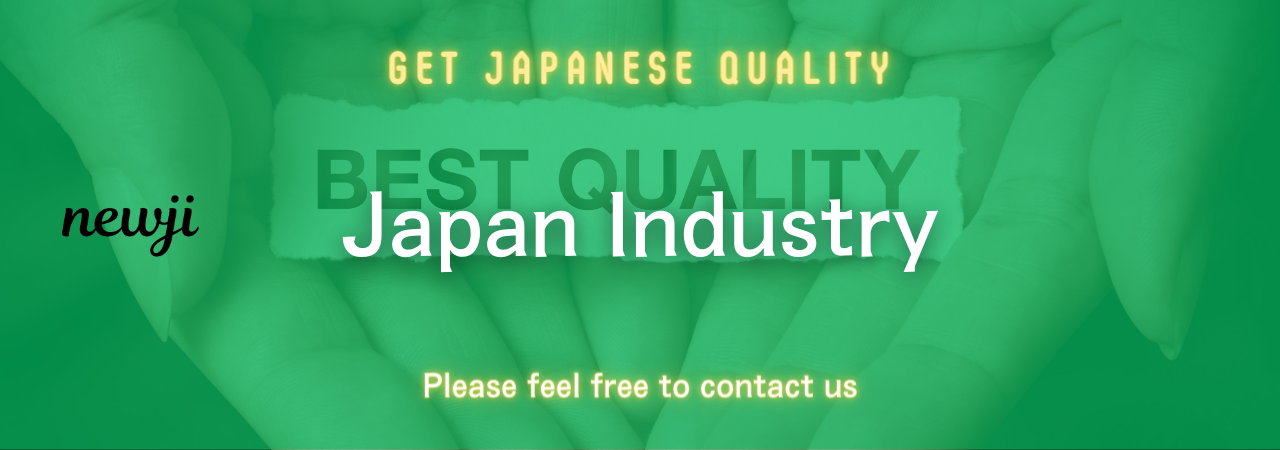
目次
Introduction to Electromagnetic Compatibility in Japanese Manufacturing
Electromagnetic Compatibility (EMC) is crucial in the manufacturing of interference-free electronics.
In the highly competitive market of electronics, ensuring that devices operate without electromagnetic interference is essential.
Japanese manufacturing is renowned for its stringent EMC standards.
This commitment to EMC ensures the production of reliable and high-quality electronic products.
Understanding and implementing effective EMC measures can significantly enhance product performance and marketability.
The Importance of EMC in Electronics Manufacturing
Electromagnetic interference can disrupt the functionality of electronic devices.
Such disruptions can lead to device malfunctions, reduced performance, and customer dissatisfaction.
In industries ranging from automotive to consumer electronics, EMC compliance is mandatory to meet regulatory requirements.
Failing to achieve adequate EMC can result in costly recalls, legal issues, and damage to a company’s reputation.
Therefore, mastering EMC is not just a technical necessity but also a strategic business imperative.
Regulatory Requirements and Standards
Japanese manufacturing adheres to international EMC standards such as CISPR and IEC.
Complying with these standards ensures that products can be sold globally without facing regulatory barriers.
Understanding regional variations in EMC regulations is essential for manufacturers aiming to enter multiple markets.
Staying updated with evolving EMC standards helps manufacturers maintain compliance and avoid penalties.
Advantages of Implementing Robust EMC Measures
Implementing strong EMC measures offers several advantages.
Firstly, it enhances product reliability by minimizing the risk of electromagnetic interference.
Reliable products lead to increased customer trust and brand loyalty.
Secondly, compliance with EMC standards facilitates smoother market entry and acceptance.
Manufacturers can avoid delays and additional costs associated with non-compliance.
Thirdly, robust EMC practices can lead to innovations in product design, improving overall performance and competitiveness.
Improved Product Performance
Effective EMC measures ensure that electronic devices operate seamlessly in various environments.
This reliability is critical for applications in sensitive areas such as healthcare and aerospace.
Manufacturers can differentiate their products through superior performance, gaining a competitive edge.
Cost Savings
Investing in EMC during the design and development phase can prevent expensive modifications and recalls post-production.
Early detection and mitigation of EMC issues streamline the manufacturing process, reducing wastage and rework.
Challenges in Achieving EMC Compliance
Despite its benefits, achieving EMC compliance poses several challenges.
Technological complexities, high costs, and the need for specialized expertise can deter manufacturers from prioritizing EMC.
Additionally, the rapid advancement of electronics technology continually raises the standards and expectations for EMC performance.
Balancing cost and compliance requires strategic planning and resource allocation.
Technological Complexity
As electronic devices become more sophisticated, managing electromagnetic emissions becomes increasingly complex.
Advanced components and high-speed circuits contribute to higher levels of potential interference.
Manufacturers must incorporate sophisticated design techniques and testing methodologies to address these challenges.
Cost Implications
Implementing comprehensive EMC measures can be expensive.
Costs associated with specialized materials, testing equipment, and skilled personnel can strain budgets, particularly for small and medium-sized enterprises.
Best Practices for Mastering EMC in Japanese Manufacturing
To effectively manage EMC, manufacturers can adopt several best practices.
These practices encompass design strategies, quality control measures, and supplier collaborations.
Implementing these strategies ensures compliance, enhances product quality, and fosters continuous improvement.
Integrating EMC Early in the Design Phase
Addressing EMC considerations during the initial design phase is crucial.
Early integration allows for the identification and mitigation of potential interference issues before they escalate.
Comprehensive Testing and Validation
Regular and thorough testing is essential to ensure ongoing EMC compliance.
Employing both in-house and third-party testing services can provide a comprehensive understanding of a product’s electromagnetic performance.
Continuous Training and Development
Investing in the continuous training of engineering and technical staff ensures that the workforce remains proficient in the latest EMC practices and technologies.
Supplier Negotiation Techniques for EMC Compliance
Effective negotiation with suppliers is key to securing components that meet stringent EMC standards.
Establishing clear communication and setting explicit expectations can lead to mutually beneficial partnerships.
Setting Clear EMC Requirements
Clearly defining EMC requirements in supplier contracts ensures that all parties understand the standards that must be met.
This clarity helps prevent misunderstandings and ensures that suppliers prioritize EMC compliance.
Evaluating Supplier Capabilities
Assessing a supplier’s ability to meet EMC standards is essential.
This evaluation includes reviewing their quality assurance processes, testing facilities, and past performance in delivering EMC-compliant components.
Building Long-term Relationships
Fostering long-term relationships with suppliers can lead to better collaboration and mutual understanding of EMC requirements.
Trust and reliability are paramount in ensuring consistent EMC compliance.
Market Conditions Influencing EMC in Japanese Manufacturing
The electronics market is dynamic, with rapid technological advancements shaping EMC practices.
Understanding market trends and customer expectations is vital for manufacturers to stay competitive.
Technological Advancements
Emerging technologies such as 5G, IoT, and electric vehicles are pushing the boundaries of EMC.
Manufacturers must adapt to new challenges posed by these technologies to maintain compliance and performance standards.
Customer Expectations
Modern consumers demand high-performance, reliable electronics.
Meeting these expectations requires manufacturers to prioritize EMC to ensure superior product functionality and longevity.
Case Studies: Successful EMC Implementation in Japanese Manufacturing
Examining real-world examples provides valuable insights into effective EMC strategies and their outcomes.
Automotive Electronics
A leading Japanese automotive manufacturer integrated EMC considerations into their vehicle electronics design.
By adopting comprehensive EMC testing and collaborating closely with suppliers, they achieved compliance with international standards.
This approach resulted in enhanced vehicle performance and customer satisfaction.
Consumer Electronics
A prominent consumer electronics company in Japan implemented early-stage EMC integration in product development.
Through rigorous testing and continuous improvement, they minimized electromagnetic interference, leading to high product reliability and market success.
Future Trends in EMC for Japanese Manufacturing
The future of EMC in Japanese manufacturing is poised to evolve with technological innovations and changing market demands.
Integration of AI and Machine Learning
Artificial Intelligence (AI) and machine learning can revolutionize EMC by enabling predictive analysis and automated mitigation strategies.
These technologies can enhance the accuracy and efficiency of EMC testing and compliance processes.
Sustainable EMC Practices
Sustainability is becoming increasingly important in manufacturing.
Developing eco-friendly EMC solutions, such as using recyclable materials and reducing energy consumption, aligns with global sustainability goals and customer preferences.
Conclusion
Mastering Electromagnetic Compatibility is essential for Japanese manufacturers striving to produce interference-free and reliable electronics.
By understanding the importance of EMC, overcoming challenges, and implementing best practices, manufacturers can ensure compliance and enhance product quality.
Effective supplier negotiations and staying abreast of market conditions further contribute to successful EMC management.
As technology continues to advance, embracing future trends will be crucial in maintaining a competitive edge in the global market.
Investing in EMC not only safeguards product functionality but also drives innovation and business growth.
資料ダウンロード
QCD調達購買管理クラウド「newji」は、調達購買部門で必要なQCD管理全てを備えた、現場特化型兼クラウド型の今世紀最高の購買管理システムとなります。
ユーザー登録
調達購買業務の効率化だけでなく、システムを導入することで、コスト削減や製品・資材のステータス可視化のほか、属人化していた購買情報の共有化による内部不正防止や統制にも役立ちます。
NEWJI DX
製造業に特化したデジタルトランスフォーメーション(DX)の実現を目指す請負開発型のコンサルティングサービスです。AI、iPaaS、および先端の技術を駆使して、製造プロセスの効率化、業務効率化、チームワーク強化、コスト削減、品質向上を実現します。このサービスは、製造業の課題を深く理解し、それに対する最適なデジタルソリューションを提供することで、企業が持続的な成長とイノベーションを達成できるようサポートします。
オンライン講座
製造業、主に購買・調達部門にお勤めの方々に向けた情報を配信しております。
新任の方やベテランの方、管理職を対象とした幅広いコンテンツをご用意しております。
お問い合わせ
コストダウンが利益に直結する術だと理解していても、なかなか前に進めることができない状況。そんな時は、newjiのコストダウン自動化機能で大きく利益貢献しよう!
(Β版非公開)