- お役立ち記事
- Basics of position control, speed control, and force control in robots and their applications and points for robot manipulators
月間76,176名の
製造業ご担当者様が閲覧しています*
*2025年3月31日現在のGoogle Analyticsのデータより
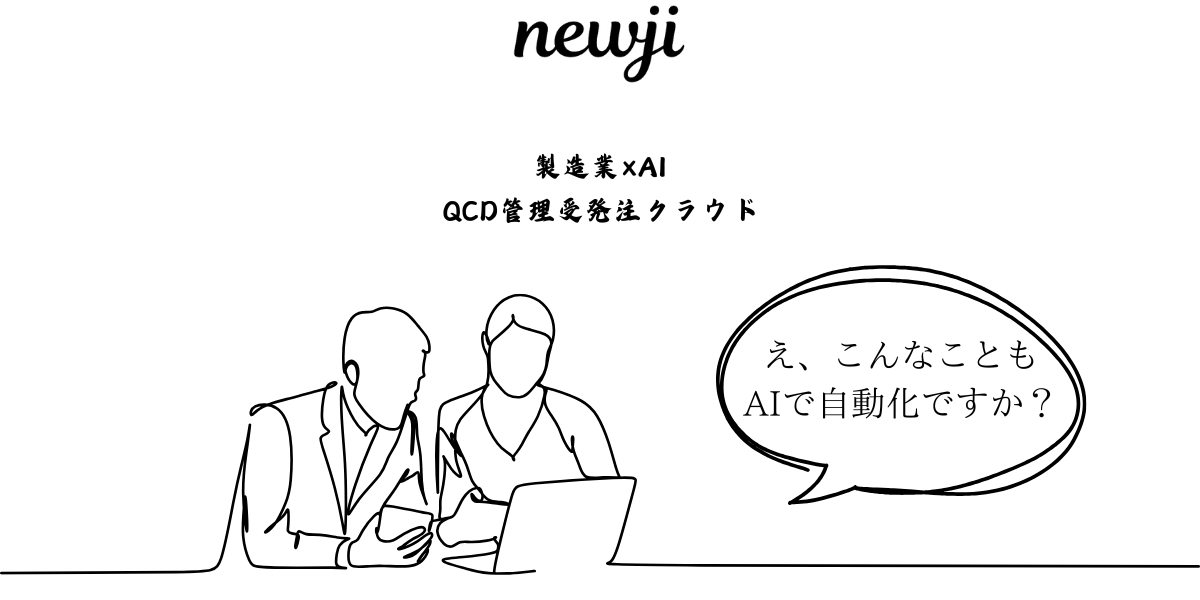
Basics of position control, speed control, and force control in robots and their applications and points for robot manipulators
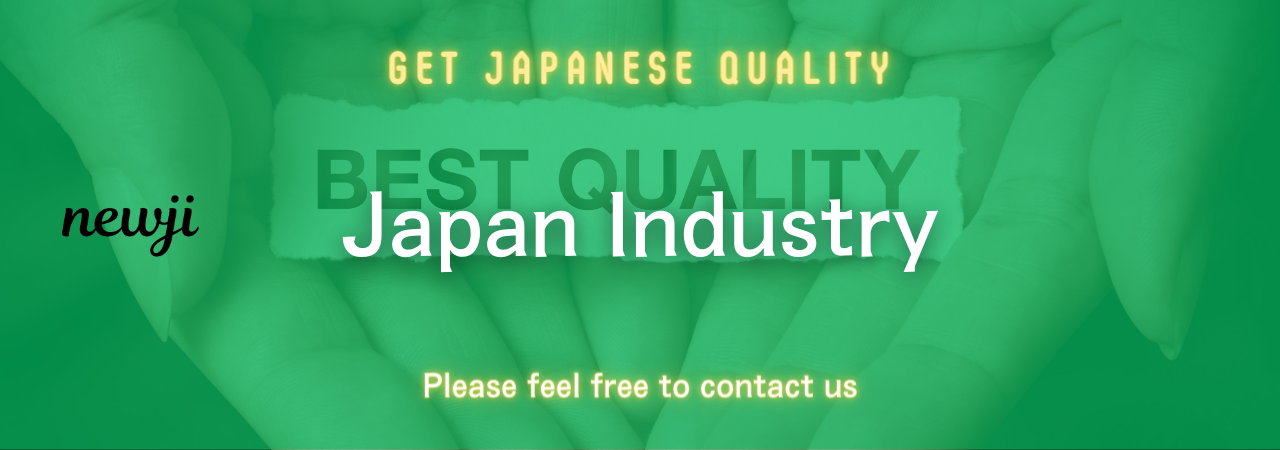
目次
Understanding Position Control in Robots
Position control is a fundamental aspect of robotics where the primary goal is to ensure that a robot or its components reach a specific location or orientation in space.
It involves calculating the precise position of a robot’s parts and controlling their movements to achieve the desired position.
This is crucial for tasks that require high accuracy, such as assembling intricate parts or performing delicate surgical procedures.
In position control systems, sensors like encoders are commonly used to measure the actual position of the robot’s joints or end-effectors.
These measurements are then compared to the desired position, and adjustments are made to reduce any discrepancies.
The use of feedback loops in position control ensures that the robot can correct its movements in real time, enhancing precision.
Such control is vital in applications like manufacturing, where robots are employed to pick and place objects in predetermined locations repeatedly.
Applications of Position Control
Position control is widely used in industries where precision is crucial.
For example, in manufacturing, robotic arms equipped with position control systems assemble products with high accuracy.
In the automotive industry, robots often perform tasks such as welding or painting, which benefit from precise positioning.
Medical applications also rely heavily on position control, particularly in robotic surgery, where parts of the robot must align perfectly to perform delicate operations.
Thus, position control is integral to applications requiring strict adherence to spatial guidelines.
Speed Control Explained
Speed control in robotics focuses on regulating the velocity of the robot’s components.
While position control emphasizes achieving a precise spot, speed control ensures that the movement towards that position occurs at a consistent and predictable rate.
The speed at which a robot moves can significantly impact its efficiency and productivity.
Too slow, and the task may not be completed in time; too fast, and there is a risk of errors or damage to sensitive components.
In speed control systems, sensors monitor the velocity of a robot’s movements.
Controllers adjust the speed based on predetermined settings to ensure smooth and efficient operation.
Speed control is particularly useful in conveyor belt operations, where products must move at a consistent rate to ensure a balanced workflow.
Applications of Speed Control
Industries that demand precise timing and synchronization often implement speed control in their robotic systems.
In logistics, for example, robots need to move packages from one place to another efficiently, which requires stringent speed management.
Automated warehouses rely heavily on speed control to ensure that inventory is moved seamlessly without causing delays in operations.
Similarly, in the food industry, packaging lines utilize speed control to align products accurately as they travel on conveyor belts.
This ensures that processes such as labeling or sealing occur precisely when needed.
Force Control in Robotics
Force control involves managing the physical pressure or force exerted by a robot.
This is essential in applications where the robot interacts with objects or environments, requiring a delicate touch or precise pressure.
In force control systems, sensors detect the amount of force being applied and adjust it as necessary.
This allows the robot to handle fragile objects without causing damage, or apply sufficient pressure to perform tasks like assembly or machining.
Using force control systems, robots can adapt to varying external conditions and maintain the right amount of force needed for different tasks.
This adaptability makes force control an essential feature in robotics applications involving human interaction or variable environments.
Applications of Force Control
Force control is crucial in scenarios where robots work closely with humans or in environments with fluctuating conditions.
In the healthcare sector, robotic systems use force control to assist in patient handling or rehabilitation exercises, offering the right balance of support and flexibility.
In manufacturing, robots equipped with force control can adjust their grip based on the size and material of the parts they handle, reducing waste and increasing efficiency.
Moreover, in tasks like polishing or grinding, robots must maintain consistent pressure for optimal results, a feat made possible through effective force control.
Considerations for Robot Manipulators
When working with robot manipulators, the integration of position, speed, and force control is essential for achieving versatile and efficient operation.
Each control type serves a unique purpose and, when combined, they provide a comprehensive approach to managing robotic movements.
Designers and engineers must consider the specific requirements of their application to determine the appropriate control systems.
For instance, a robot used in an assembly line might prioritize speed and position control to maintain efficiency, whereas a robot designed for caregiving might emphasize force control for safety and comfort.
Additionally, calibration and maintenance of sensors and controllers play a critical role in the effectiveness of these control systems.
Regular monitoring and adjustments ensure that the robot operates at peak performance.
Training and expertise in control system integration are also important for engineers looking to implement these technologies effectively.
By understanding and applying the principles of position, speed, and force control, companies can enhance the capabilities of their robot manipulators, leading to improved productivity and innovation in various sectors.
In summary, position control ensures accuracy, speed control improves efficiency, and force control enables adaptability and safety, each playing a vital role in the modern robotics landscape.
資料ダウンロード
QCD管理受発注クラウド「newji」は、受発注部門で必要なQCD管理全てを備えた、現場特化型兼クラウド型の今世紀最高の受発注管理システムとなります。
ユーザー登録
受発注業務の効率化だけでなく、システムを導入することで、コスト削減や製品・資材のステータス可視化のほか、属人化していた受発注情報の共有化による内部不正防止や統制にも役立ちます。
NEWJI DX
製造業に特化したデジタルトランスフォーメーション(DX)の実現を目指す請負開発型のコンサルティングサービスです。AI、iPaaS、および先端の技術を駆使して、製造プロセスの効率化、業務効率化、チームワーク強化、コスト削減、品質向上を実現します。このサービスは、製造業の課題を深く理解し、それに対する最適なデジタルソリューションを提供することで、企業が持続的な成長とイノベーションを達成できるようサポートします。
製造業ニュース解説
製造業、主に購買・調達部門にお勤めの方々に向けた情報を配信しております。
新任の方やベテランの方、管理職を対象とした幅広いコンテンツをご用意しております。
お問い合わせ
コストダウンが利益に直結する術だと理解していても、なかなか前に進めることができない状況。そんな時は、newjiのコストダウン自動化機能で大きく利益貢献しよう!
(β版非公開)