- お役立ち記事
- Fundamentals of gears, strength design methods, and reliability evaluation techniques
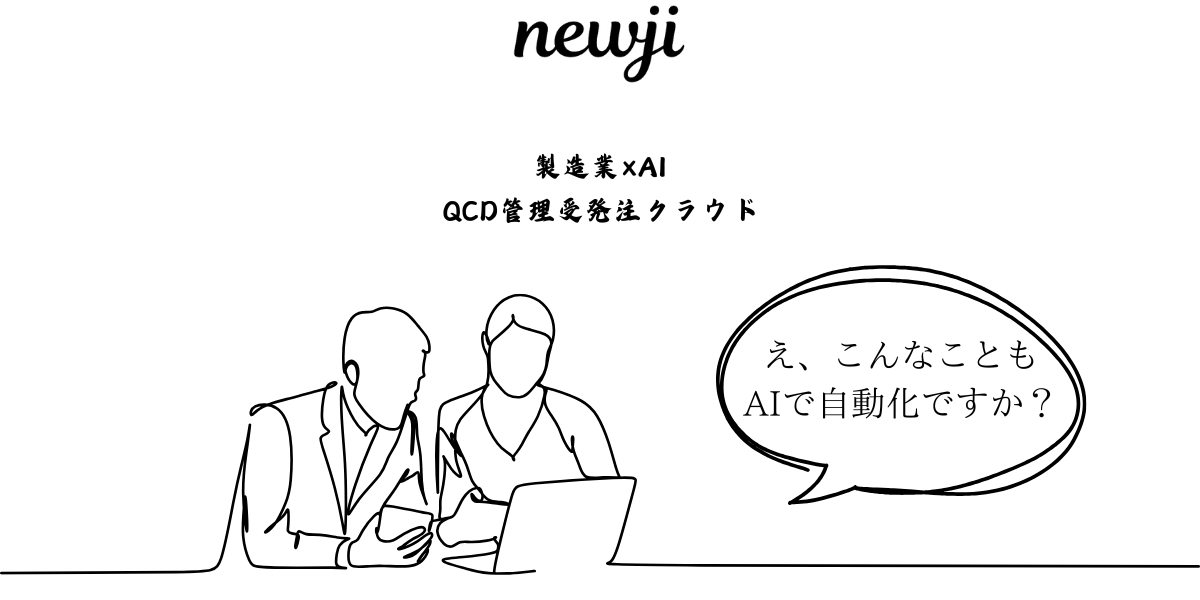
Fundamentals of gears, strength design methods, and reliability evaluation techniques
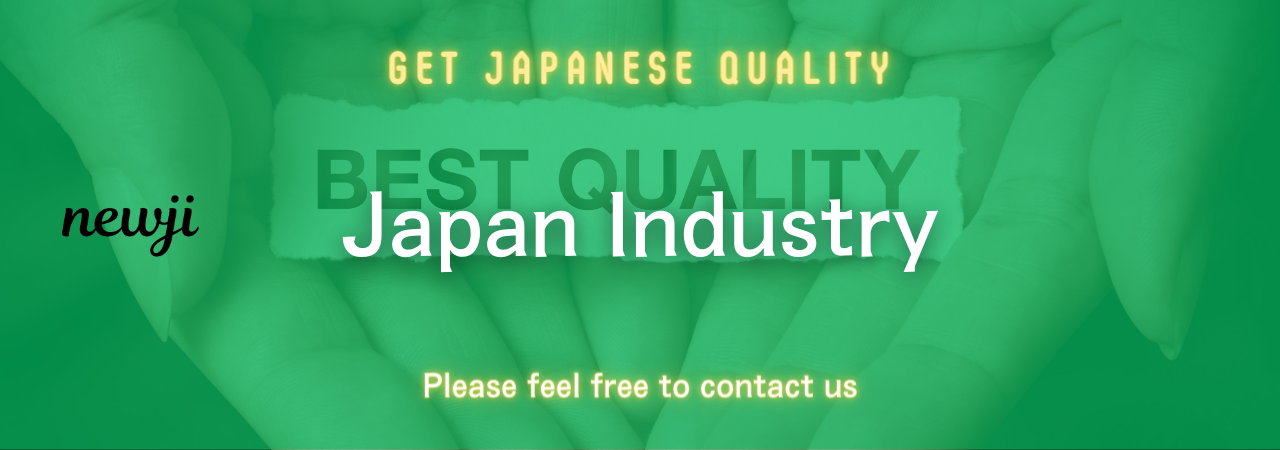
目次
Introduction to Gear Fundamentals
Gears are essential components in many mechanical systems, used to transmit power and change the speed, torque, and direction of a power source.
Understanding gears, their design methods, and how to evaluate their reliability is crucial for engineers and designers.
Let’s explore the basics of gears, delve into strength design methods, and discuss techniques for evaluating their reliability.
Types of Gears and Their Functions
Gears come in various shapes and sizes, each designed for specific functions in a machine.
Spur Gears
Spur gears are the most common type, with straight teeth parallel to the axis of rotation.
They are used in applications where noise control is not critical as they can be noisy at high speeds.
Spur gears are typically found in simple machinery like clocks and conveyor systems.
Helical Gears
Helical gears have teeth cut at an angle to the axis, creating a helix shape.
This design allows for smoother and quieter operation compared to spur gears.
They are used in applications requiring high-speed and high-power transmission like automotive transmissions.
Bevel Gears
Bevel gears are conically shaped and used to transmit power between intersecting shafts.
They can alter the direction of the shaft in a powertrain and are often used in differential systems in vehicles.
Worm Gears
Worm gears consist of a worm (a gear in the form of a screw) and a worm wheel.
These gears provide high torque reduction and are used in applications where power needs to be smoothly reduced, like elevators and conveyor belts.
Strength Design Methods for Gears
Designing gears requires a focus on their strength to ensure they can handle the intended loads without failing.
Static and Dynamic Load Analysis
When designing gears, understanding the loads they will encounter is crucial.
Static load analysis involves calculating the forces the gear will experience in a stationary state.
Dynamic load analysis considers the forces during motion, including acceleration, deceleration, and vibration effects.
Material Selection
Choosing the right material is vital for gear strength.
Common materials include steel, cast iron, and non-metals like plastics for low-load applications.
The material must withstand the stresses and environmental conditions of its intended use.
Gear Geometry and Design
The geometry of a gear, including its tooth profile and size, significantly impacts its strength and performance.
The design should focus on reducing stress concentrations and ensuring even load distribution across the gear teeth.
Surface Hardening Techniques
Surface hardening strengthens the outer surface of a gear’s teeth, enhancing wear resistance and fatigue life.
Techniques like carburizing, nitriding, and induction hardening are commonly used to improve surface properties.
Reliability Evaluation Techniques
Evaluating the reliability of gears ensures they will perform adequately throughout their service life without unexpected failure.
Finite Element Analysis (FEA)
FEA is a powerful computational tool that allows engineers to predict how gears will respond to various forces and conditions.
By modeling the gear and simulating different scenarios, FEA helps identify potential stress points and optimize the design for reliability.
Failure Mode and Effects Analysis (FMEA)
FMEA is a structured approach to identify potential failure modes in a system and assess their impact.
For gears, it involves analyzing wear, fracture, and fatigue failures to develop strategies for mitigating these risks.
This process helps engineers design more robust gears and improve their reliability.
Testing and Prototyping
Physical testing and prototyping allow engineers to evaluate the real-world performance of gears.
By subjecting prototypes to rigorously controlled testing conditions, engineers can validate the design and identify any weaknesses.
This step ensures the final product meets the desired reliability standards.
Maintenance and Monitoring
Ongoing maintenance and monitoring are crucial for maintaining gear reliability throughout its lifespan.
Regular inspections, lubrication, and condition monitoring can identify early signs of wear and allow for preventative maintenance, reducing the risk of unexpected failures.
Conclusion
Gears play a vital role in countless mechanical systems, and understanding their fundamentals, design methods, and reliability evaluation techniques is essential for engineers and designers.
By carefully selecting materials, designing robust geometries, and employing advanced analysis and testing techniques, we can ensure gears perform reliably in any application.
With the right approach, gears can deliver efficient power transmission, prolong the lifespan of machinery, and contribute to the overall success of engineering projects.
資料ダウンロード
QCD調達購買管理クラウド「newji」は、調達購買部門で必要なQCD管理全てを備えた、現場特化型兼クラウド型の今世紀最高の購買管理システムとなります。
ユーザー登録
調達購買業務の効率化だけでなく、システムを導入することで、コスト削減や製品・資材のステータス可視化のほか、属人化していた購買情報の共有化による内部不正防止や統制にも役立ちます。
NEWJI DX
製造業に特化したデジタルトランスフォーメーション(DX)の実現を目指す請負開発型のコンサルティングサービスです。AI、iPaaS、および先端の技術を駆使して、製造プロセスの効率化、業務効率化、チームワーク強化、コスト削減、品質向上を実現します。このサービスは、製造業の課題を深く理解し、それに対する最適なデジタルソリューションを提供することで、企業が持続的な成長とイノベーションを達成できるようサポートします。
オンライン講座
製造業、主に購買・調達部門にお勤めの方々に向けた情報を配信しております。
新任の方やベテランの方、管理職を対象とした幅広いコンテンツをご用意しております。
お問い合わせ
コストダウンが利益に直結する術だと理解していても、なかなか前に進めることができない状況。そんな時は、newjiのコストダウン自動化機能で大きく利益貢献しよう!
(Β版非公開)