- お役立ち記事
- Exploring Agile Manufacturing in Japan: A Game Changer in the Production Landscape
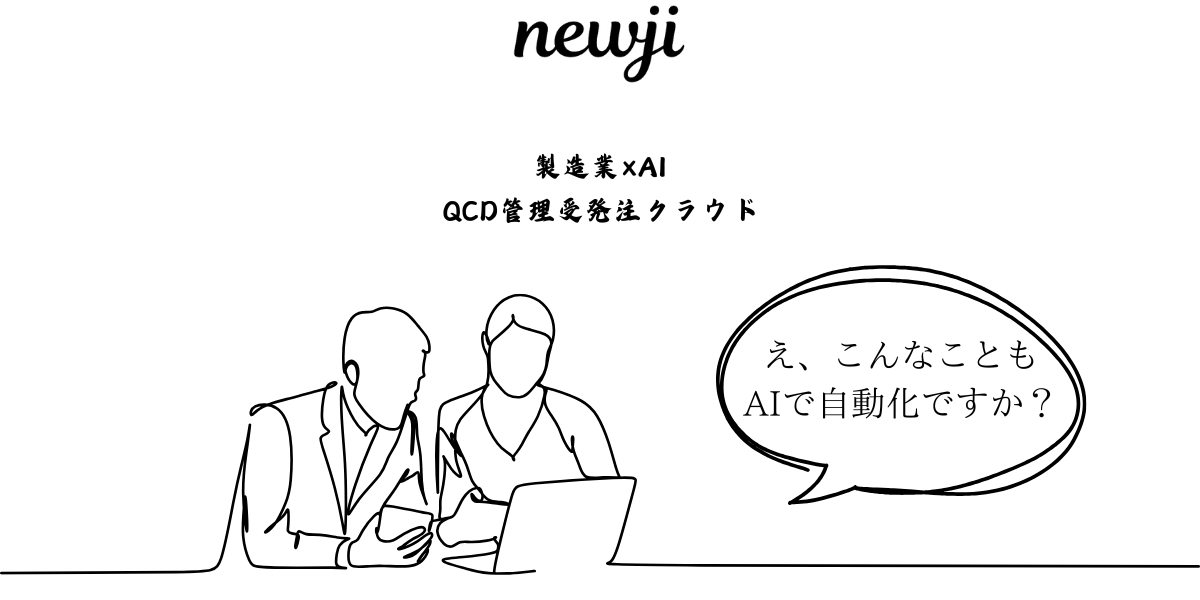
Exploring Agile Manufacturing in Japan: A Game Changer in the Production Landscape
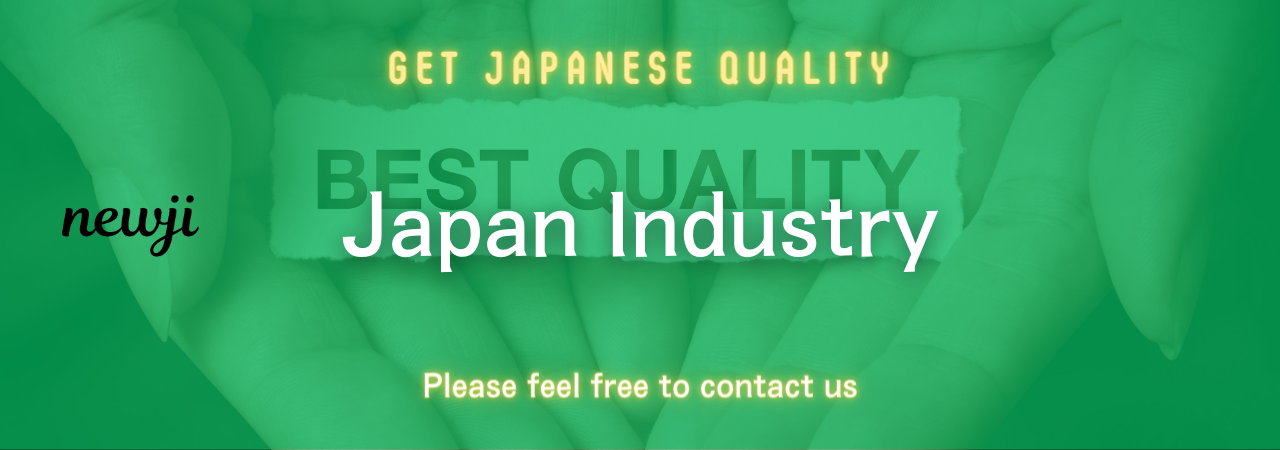
目次
Introduction to Agile Manufacturing
Agile manufacturing has emerged as a transformative approach in the production landscape, particularly within Japan’s industrial sector. This methodology emphasizes flexibility, responsiveness, and adaptability in manufacturing processes, allowing companies to swiftly respond to market changes and customer demands. By integrating agile principles, Japanese manufacturers have been able to maintain a competitive edge in the global market, ensuring efficiency and innovation in their operations.
The Evolution of Agile Manufacturing in Japan
Agile manufacturing in Japan is not a recent phenomenon; it has evolved over decades in response to both domestic and international market pressures. Traditionally, Japanese manufacturing has been synonymous with lean production and Just-In-Time (JIT) methodologies. However, as global markets became more dynamic and customer preferences shifted rapidly, the need for a more flexible and responsive manufacturing approach became evident. Agile manufacturing emerged as the natural progression, building on the strengths of lean practices while introducing greater adaptability and innovation.
Key Principles of Agile Manufacturing
Agile manufacturing is grounded in several core principles that distinguish it from traditional manufacturing approaches. These principles include:
Flexibility
Flexibility refers to the ability of manufacturing systems to quickly adapt to changes in product design, production volume, and customer requirements. This involves having versatile machinery, cross-trained employees, and modular production processes that can be reconfigured with minimal downtime.
Customer-Centricity
Agile manufacturing places the customer at the center of the production process. By closely monitoring customer feedback and market trends, companies can tailor their products and services to meet evolving demands, ensuring higher customer satisfaction and loyalty.
Rapid Response
The capacity to respond swiftly to market changes is a hallmark of agile manufacturing. This requires streamlined decision-making processes, efficient supply chain management, and the ability to implement changes quickly without compromising quality.
Continuous Improvement
Agile manufacturing fosters a culture of continuous improvement (Kaizen), where employees at all levels are encouraged to identify and implement enhancements in processes, products, and services. This ongoing pursuit of excellence helps companies stay ahead of the competition.
Advantages of Agile Manufacturing in Japan
Agile manufacturing offers numerous benefits to Japanese manufacturers, enhancing their competitiveness and operational efficiency.
Enhanced Flexibility
One of the primary advantages of agile manufacturing is the increased flexibility it provides. Japanese manufacturers can swiftly adjust production schedules, introduce new products, and customize offerings to meet specific customer needs. This adaptability is crucial in a global market characterized by rapid technological advancements and shifting consumer preferences.
Improved Quality and Innovation
Agile manufacturing promotes a culture of continuous improvement and innovation. By encouraging employees to experiment and refine processes, companies can achieve higher quality standards and develop innovative products that meet or exceed market expectations.
Shorter Lead Times
Agile manufacturing reduces lead times by streamlining production processes and eliminating inefficiencies. Shorter lead times enable companies to respond to orders more quickly, enhancing customer satisfaction and fostering loyalty.
Cost Efficiency
While agile manufacturing requires an initial investment in flexible systems and training, it ultimately leads to cost savings through improved efficiency, reduced waste, and optimized resource utilization. These cost efficiencies can be passed on to customers, making products more competitive in the global market.
Enhanced Supply Chain Management
Agile manufacturing integrates closely with supply chain management, ensuring that materials and components are available when needed and that suppliers can respond to changes in demand. This synchronization minimizes delays and disruptions, maintaining a smooth production flow.
Disadvantages and Challenges
Despite its numerous benefits, agile manufacturing also presents certain challenges that Japanese manufacturers must address to ensure successful implementation.
High Initial Investment
Implementing agile manufacturing requires significant upfront investment in flexible equipment, technology, and training programs. For some companies, especially smaller enterprises, the financial burden may be a barrier to adopting agile practices.
Complex Coordination
Agile manufacturing demands a high level of coordination across various departments and functions. Ensuring seamless communication and collaboration can be complex, particularly in large organizations with established hierarchies and processes.
Resistance to Change
Change management is a critical aspect of transitioning to agile manufacturing. Employees and management may resist changes to established workflows and practices, necessitating comprehensive training and leadership to foster a culture that embraces agility.
Supply Chain Dependencies
Agile manufacturing relies on a responsive and flexible supply chain. Dependence on suppliers who may not be equally agile can hinder a company’s ability to implement agile practices effectively, leading to delays and inconsistencies in production.
Maintaining Quality
While agile manufacturing aims to enhance quality through continuous improvement, the rapid pace of change can sometimes compromise quality control if not managed carefully. Ensuring that quality standards are maintained amidst frequent adjustments is a significant challenge.
Supplier Negotiation Techniques in Agile Manufacturing
Effective supplier negotiation is crucial for the success of agile manufacturing. Japanese manufacturers employ several techniques to build strong, collaborative relationships with suppliers, ensuring responsiveness and quality.
Building Long-Term Partnerships
Rather than transactional relationships, Japanese manufacturers focus on building long-term partnerships with suppliers. This approach fosters mutual trust, collaboration, and a shared commitment to quality and innovation, enabling more effective responses to changes in demand and production needs.
Collaborative Planning
Collaborative planning involves working closely with suppliers to forecast demand, plan production schedules, and manage inventory levels. This collaboration ensures that suppliers are aligned with the manufacturer’s production requirements, reducing lead times and enhancing flexibility.
Joint Problem-Solving
When challenges arise, Japanese manufacturers engage in joint problem-solving with suppliers to identify and implement solutions. This collaborative approach not only resolves issues more effectively but also strengthens the supplier-manufacturer relationship.
Performance-Based Contracts
Performance-based contracts link supplier compensation to specific performance metrics, such as quality standards, delivery times, and flexibility. This incentivizes suppliers to meet or exceed expectations, ensuring consistent performance aligned with agile manufacturing goals.
Investment in Supplier Capabilities
Japanese manufacturers often invest in improving their suppliers’ capabilities, providing training, technology, and resources to enhance their flexibility and responsiveness. This investment ensures that suppliers can meet the dynamic demands of agile manufacturing.
Market Conditions Influencing Agile Manufacturing in Japan
Several market conditions have driven the adoption and evolution of agile manufacturing in Japan, shaping its strategies and practices.
Globalization and Competition
Globalization has intensified competition, pushing Japanese manufacturers to adopt agile practices to maintain their market position. The ability to rapidly respond to international market changes and customer demands is essential for competing with global players.
Technological Advancements
Advancements in technology, such as automation, robotics, and digitalization, have facilitated the implementation of agile manufacturing. These technologies enable greater flexibility, efficiency, and data-driven decision-making, essential components of agile operations.
Consumer Expectations
Today’s consumers expect high-quality, customized products delivered quickly. Agile manufacturing meets these expectations by allowing for greater customization and faster turnaround times, enhancing customer satisfaction and loyalty.
Supply Chain Disruptions
Frequent supply chain disruptions, whether due to natural disasters, geopolitical tensions, or pandemics, have highlighted the need for more resilient and agile manufacturing systems. Agile practices enable companies to adapt quickly to disruptions, mitigating their impact on production and delivery.
Sustainability Concerns
Increasing emphasis on sustainability and environmental responsibility has influenced manufacturing practices. Agile manufacturing supports sustainable practices by optimizing resource utilization, reducing waste, and encouraging continuous improvement in environmental performance.
Best Practices for Implementing Agile Manufacturing
Implementing agile manufacturing requires a strategic approach, ensuring that all aspects of the organization are aligned with agile principles. Here are some best practices for successful implementation:
Leadership Commitment
Strong commitment from leadership is essential for driving the transition to agile manufacturing. Leaders must champion agile principles, provide the necessary resources, and foster a culture that embraces flexibility and continuous improvement.
Employee Training and Development
Investing in employee training and development ensures that the workforce possesses the skills and knowledge needed to operate in an agile environment. Cross-training employees and encouraging multi-functional teams enhance flexibility and adaptability.
Adoption of Advanced Technologies
Integrating advanced technologies, such as automation, IoT, and data analytics, supports agile manufacturing by enhancing efficiency, enabling real-time monitoring, and facilitating data-driven decision-making.
Flexible Production Systems
Designing flexible production systems that can be easily reconfigured to accommodate different products and production volumes is crucial. Modular machinery, adaptable layouts, and scalable processes contribute to overall flexibility.
Lean Integration
Integrating lean manufacturing principles with agile practices ensures that resources are used efficiently and waste is minimized. This combination enhances both flexibility and efficiency, supporting sustainable operations.
Collaborative Supply Chain
Building a collaborative supply chain involves working closely with suppliers and partners to ensure alignment with agile objectives. Sharing information, coordinating planning, and fostering partnerships enhance the overall responsiveness of the supply chain.
Continuous Feedback Mechanisms
Implementing continuous feedback mechanisms, such as regular performance reviews and customer feedback loops, allows for ongoing adjustments and improvements. This responsiveness ensures that the manufacturing process remains aligned with market demands and quality standards.
Risk Management
Proactively identifying and managing risks associated with agile manufacturing is essential. Developing contingency plans, diversifying suppliers, and maintaining flexibility in operations help mitigate potential disruptions and maintain continuity.
Case Studies: Success Stories of Agile Manufacturing in Japan
Several Japanese companies have successfully implemented agile manufacturing, serving as models for others seeking to adopt similar practices.
Toyota Motor Corporation
Toyota is renowned for its production system, which integrates lean manufacturing with agile principles. The company’s ability to rapidly adapt to market changes, introduce new models, and maintain high-quality standards exemplifies the effectiveness of agile manufacturing.
Canon Inc.
Canon has leveraged agile manufacturing to enhance its product development and production processes. By fostering a culture of continuous improvement and investing in advanced technologies, Canon has maintained its position as a leading manufacturer of imaging and optical products.
Panasonic Corporation
Panasonic has adopted agile practices to streamline its supply chain and improve product flexibility. The company’s focus on collaborative partnerships with suppliers and investment in digital technologies has enabled it to respond swiftly to market demands and innovate continuously.
The Role of Technology in Agile Manufacturing
Technology plays a pivotal role in enabling agile manufacturing, providing the tools and infrastructure necessary for flexibility and responsiveness.
Automation and Robotics
Automation and robotics enhance production efficiency and flexibility by allowing for rapid reconfiguration of manufacturing lines. Automated systems can quickly switch between different product lines, reducing downtime and increasing responsiveness to market changes.
Internet of Things (IoT)
IoT technology facilitates real-time monitoring and data collection across the manufacturing process. This connectivity enables better decision-making, predictive maintenance, and enhanced supply chain visibility, all of which support agile operations.
Data Analytics
Advanced data analytics provide insights into production processes, customer behavior, and market trends. By leveraging data, manufacturers can make informed decisions, optimize processes, and anticipate changes in demand, enhancing agility.
Digital Twin Technology
Digital twin technology involves creating virtual replicas of physical manufacturing systems. These digital models enable simulation, testing, and optimization of processes without disrupting actual operations, facilitating rapid adjustments and improvements.
Cloud Computing
Cloud computing offers scalable and flexible IT infrastructure, supporting agile manufacturing by enabling remote collaboration, data sharing, and real-time communication across global supply chains.
Artificial Intelligence and Machine Learning
AI and machine learning algorithms enhance predictive capabilities, optimize production schedules, and improve quality control. These technologies enable proactive adjustments and continuous improvements, essential for maintaining agility.
Sustainability and Agile Manufacturing
Sustainability is increasingly becoming a focal point in manufacturing, and agile practices contribute significantly to environmental responsibility.
Resource Optimization
Agile manufacturing emphasizes the efficient use of resources, reducing waste and minimizing environmental impact. By optimizing production processes, companies can conserve energy, reduce material usage, and lower emissions.
Flexible Production for Sustainable Products
The flexibility of agile manufacturing allows companies to adapt production lines to produce more sustainable products, such as those made from recycled materials or designed for energy efficiency. This adaptability supports the development of environmentally friendly products in response to market demands.
Reduced Inventory and Waste
Agile manufacturing practices, such as Just-In-Time (JIT) production, minimize excess inventory and reduce waste. Lower inventory levels decrease the need for storage space and reduce the likelihood of obsolete or unsold products, contributing to sustainability.
Collaborative Supply Chains
Collaborative supply chains inherent in agile manufacturing promote sustainable practices among all partners. Shared goals and transparent communication encourage suppliers to adopt environmentally friendly practices, enhancing the overall sustainability of the manufacturing ecosystem.
Long-Term Environmental Planning
Agile manufacturing supports long-term environmental planning by enabling continuous improvement and the integration of sustainable practices into the production process. This ongoing commitment to sustainability helps companies adapt to evolving regulations and societal expectations.
Future Trends in Agile Manufacturing
The landscape of agile manufacturing is continuously evolving, driven by technological advancements and changing market dynamics. Several trends are shaping the future of agile manufacturing in Japan and globally.
Integration of Artificial Intelligence
AI will play an increasingly significant role in agile manufacturing, enhancing predictive maintenance, quality control, and supply chain optimization. Advanced AI algorithms will enable more precise and proactive adjustments to manufacturing processes, further increasing agility.
Expansion of Smart Manufacturing
Smart manufacturing, characterized by interconnected and intelligent systems, will expand the capabilities of agile manufacturing. The integration of IoT, AI, and automation will create more responsive and efficient manufacturing environments.
Increased Emphasis on Sustainability
Sustainability will continue to drive agile manufacturing practices, with companies striving to balance flexibility and environmental responsibility. Innovations in green technologies and sustainable materials will become integral to agile manufacturing strategies.
Customization and Personalization
The demand for customized and personalized products will increase, pushing manufacturers to adopt more agile and flexible production systems. Advanced technologies, such as 3D printing and modular production, will support this trend by enabling rapid customization without sacrificing efficiency.
Global Supply Chain Agility
As global supply chains become more complex and interconnected, the need for greater agility will intensify. Companies will invest in technologies and strategies that enhance supply chain visibility, resilience, and responsiveness to manage global disruptions effectively.
Workforce Transformation
The workforce will undergo significant transformation, with a greater emphasis on digital skills, adaptability, and continuous learning. Training programs and educational initiatives will focus on equipping employees with the capabilities needed to thrive in agile manufacturing environments.
Resilience and Risk Management
Building resilience into manufacturing systems will become a priority, ensuring that companies can withstand and recover from disruptions. Agile manufacturing practices will incorporate robust risk management strategies to enhance overall resilience and maintain operational continuity.
Conclusion
Agile manufacturing represents a significant shift in the production landscape, offering Japanese manufacturers the flexibility, responsiveness, and innovation needed to thrive in a dynamic global market. By embracing agile principles, investing in advanced technologies, and fostering collaborative relationships with suppliers, Japanese companies can enhance their competitiveness and achieve sustainable growth. While challenges exist, the advantages of agile manufacturing—ranging from improved quality and reduced lead times to enhanced supply chain management and sustainability—make it a game changer in the manufacturing sector. As the landscape continues to evolve, agile manufacturing will remain a critical strategy for companies seeking to adapt to changing market conditions and maintain their leadership in the global marketplace.
資料ダウンロード
QCD調達購買管理クラウド「newji」は、調達購買部門で必要なQCD管理全てを備えた、現場特化型兼クラウド型の今世紀最高の購買管理システムとなります。
ユーザー登録
調達購買業務の効率化だけでなく、システムを導入することで、コスト削減や製品・資材のステータス可視化のほか、属人化していた購買情報の共有化による内部不正防止や統制にも役立ちます。
NEWJI DX
製造業に特化したデジタルトランスフォーメーション(DX)の実現を目指す請負開発型のコンサルティングサービスです。AI、iPaaS、および先端の技術を駆使して、製造プロセスの効率化、業務効率化、チームワーク強化、コスト削減、品質向上を実現します。このサービスは、製造業の課題を深く理解し、それに対する最適なデジタルソリューションを提供することで、企業が持続的な成長とイノベーションを達成できるようサポートします。
オンライン講座
製造業、主に購買・調達部門にお勤めの方々に向けた情報を配信しております。
新任の方やベテランの方、管理職を対象とした幅広いコンテンツをご用意しております。
お問い合わせ
コストダウンが利益に直結する術だと理解していても、なかなか前に進めることができない状況。そんな時は、newjiのコストダウン自動化機能で大きく利益貢献しよう!
(Β版非公開)