- お役立ち記事
- Fundamentals of welding technology, causes of cracking and deformation, and countermeasure points
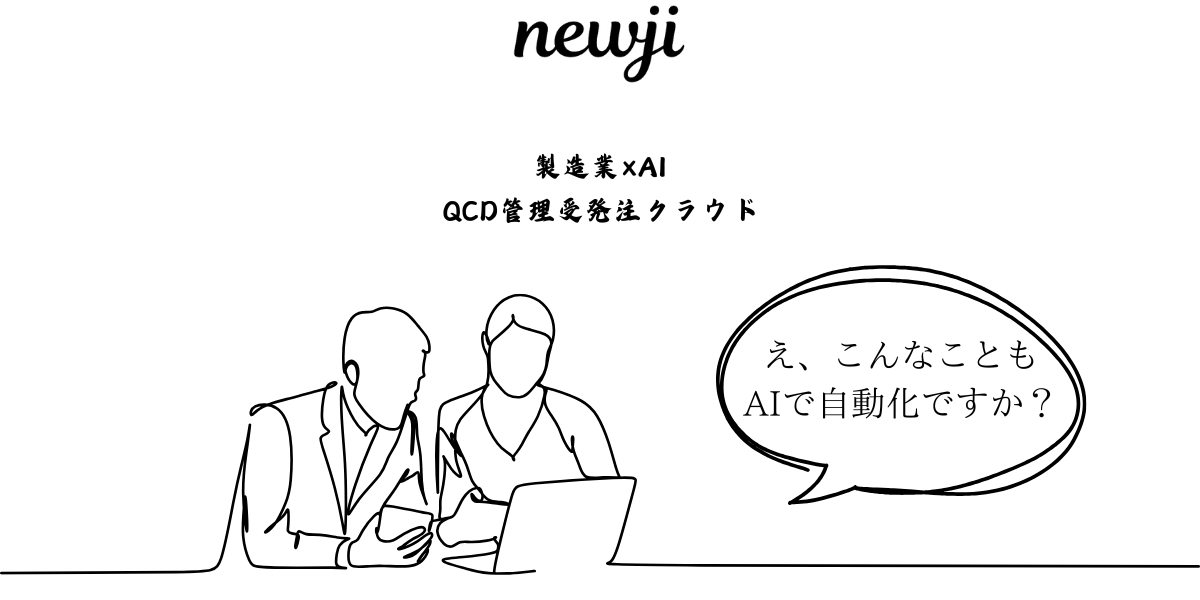
Fundamentals of welding technology, causes of cracking and deformation, and countermeasure points
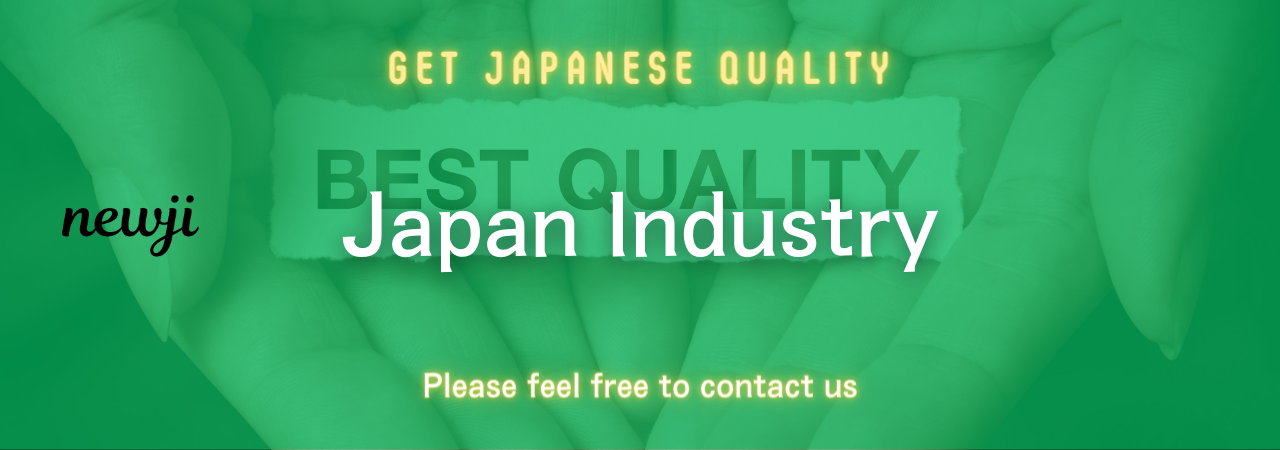
目次
Understanding the Basics of Welding Technology
Welding is a widely used technique in various industries to join metals and thermoplastics together.
The process involves the application of heat, pressure, or both, to create a durable joint between materials.
Understanding the fundamentals of welding technology is critical for ensuring strong and reliable welds.
There are several welding techniques, such as arc welding, MIG welding, TIG welding, and more.
Each technique has its unique benefits, making it suitable for different applications and materials.
In arc welding, an electric arc is used to generate heat for melting and fusing materials.
MIG welding, or Metal Inert Gas welding, employs a continuous feeding wire as an electrode and requires a shielding gas to protect the weld from contamination.
TIG welding, or Tungsten Inert Gas welding, uses a non-consumable tungsten electrode and a separate filler material.
The choice of welding process depends on factors like material type, thickness, and the required strength of the joint.
Common Causes of Welding Cracks and Deformations
Welding cracks and deformations are potential defects that can compromise the strength and durability of welded joints.
Cracks can occur during the welding process or after the weld has cooled and hardened.
Deformations, on the other hand, result from unwanted changes in the shape or dimensions of the welded components.
Understanding their causes is crucial to prevent defects and ensure high-quality welds.
Causes of Cracking in Welds
1. **Thermal Stresses:** Rapid heating and cooling can induce thermal stresses in materials, leading to cracks.
Differential cooling rates between the weld metal and the base metal can cause tensile stresses, promoting crack formation.
2. **Poor Fit-Up and Joint Design:** Mismatches in fit-up or improper joint designs can create stress concentrations, making the welded joint more susceptible to cracking.
3. **Contamination:** The presence of impurities like oil, grease, or moisture on the surface of materials can lead to porosity, increasing the likelihood of cracks.
4. **Improper Filler Material:** Using the wrong type or composition of filler material can affect the integrity of the weld, leading to cracking.
Causes of Deformation in Welds
1. **Uneven Heating and Cooling:** Non-uniform temperature distribution during welding can cause uneven expansion and contraction, resulting in warping or distortion.
2. **Excessive Heat Input:** Applying too much heat can lead to excessive melting and flow of the base material, causing deformation.
3. **Residual Stresses:** Welding can introduce residual stresses within materials, manifesting as deformations during cooling.
Effective Countermeasures for Welding Defects
Implementing strategies to minimize cracking and deformations is essential for producing reliable welded joints.
By following best practices and employing preventive measures, you can significantly reduce the risk of defects.
Preventing Cracks in Welds
1. **Preheat and Post-Heat Treatments:** Controlling the temperature of materials before and after welding can help reduce thermal stresses and prevent cracking.
2. **Proper Joint Design:** Optimizing joint design and fit-up can distribute stresses more evenly, minimizing the likelihood of cracks.
3. **Surface Preparation:** Thoroughly cleaning the surfaces of materials to remove impurities can prevent contamination and reduce crack risk.
4. **Suitable Filler Material:** Choosing the right filler material that matches the composition and properties of the base metal can enhance weld integrity.
Minimizing Deformations in Welds
1. **Controlled Heat Application:** Using appropriate heat input and welding techniques can reduce the risk of excessive melting and deformation.
2. **Symmetrical Welding:** Applying welds symmetrically and sequentially can help balance heat distribution, minimizing distortion.
3. **Clamping and Fixturing:** Securing the components during welding with clamps or fixtures can prevent movement and distortion.
4. **Post-Weld Treatment:** Stress-relief treatments such as annealing can help alleviate residual stresses and prevent deformations.
Importance of Monitoring and Quality Control
To ensure high-quality welds, regular monitoring and quality control measures must be in place throughout the welding process.
Inspection techniques like visual examination, ultrasonic testing, and radiographic testing can help identify defects early and take corrective actions.
Implementing a robust quality assurance program can improve weld reliability and extend the service life of welded components.
A well-trained workforce is a crucial component of successful welding operations.
Providing adequate training for welders ensures they have the technical knowledge to perform at a high level and understand the importance of quality practices.
Continual education and certification programs can keep welders updated on the latest welding technologies and safety standards.
Conclusion
Grasping the fundamentals of welding technology and understanding the causes of defects like cracking and deformation is essential for any industry utilizing welding processes.
By taking preventive measures and employing effective strategies, you can minimize defects and boost the quality of welded joints.
Regular monitoring, quality control, and skilled welders can further enhance the reliability and performance of welding operations.
With a solid foundation in welding technology, you can ensure that welded structures are safe, durable, and capable of withstanding their intended loads.
資料ダウンロード
QCD調達購買管理クラウド「newji」は、調達購買部門で必要なQCD管理全てを備えた、現場特化型兼クラウド型の今世紀最高の購買管理システムとなります。
ユーザー登録
調達購買業務の効率化だけでなく、システムを導入することで、コスト削減や製品・資材のステータス可視化のほか、属人化していた購買情報の共有化による内部不正防止や統制にも役立ちます。
NEWJI DX
製造業に特化したデジタルトランスフォーメーション(DX)の実現を目指す請負開発型のコンサルティングサービスです。AI、iPaaS、および先端の技術を駆使して、製造プロセスの効率化、業務効率化、チームワーク強化、コスト削減、品質向上を実現します。このサービスは、製造業の課題を深く理解し、それに対する最適なデジタルソリューションを提供することで、企業が持続的な成長とイノベーションを達成できるようサポートします。
オンライン講座
製造業、主に購買・調達部門にお勤めの方々に向けた情報を配信しております。
新任の方やベテランの方、管理職を対象とした幅広いコンテンツをご用意しております。
お問い合わせ
コストダウンが利益に直結する術だと理解していても、なかなか前に進めることができない状況。そんな時は、newjiのコストダウン自動化機能で大きく利益貢献しよう!
(Β版非公開)