- お役立ち記事
- Fundamentals of finite element method (FEM) and points for effective use of CAE in removal machining
月間76,176名の
製造業ご担当者様が閲覧しています*
*2025年3月31日現在のGoogle Analyticsのデータより
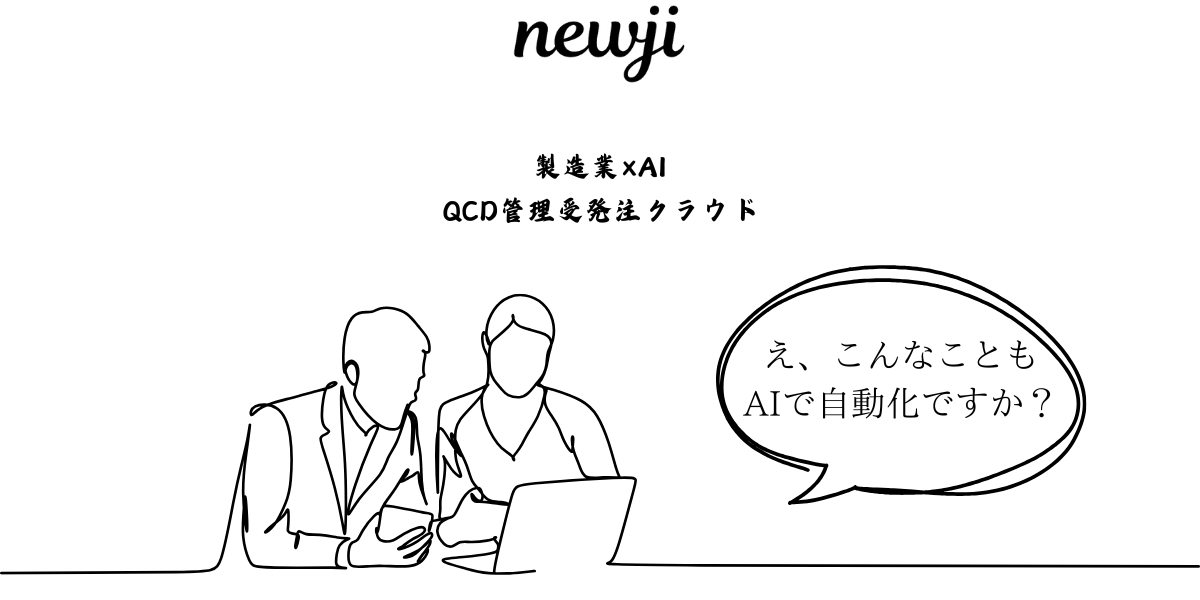
Fundamentals of finite element method (FEM) and points for effective use of CAE in removal machining
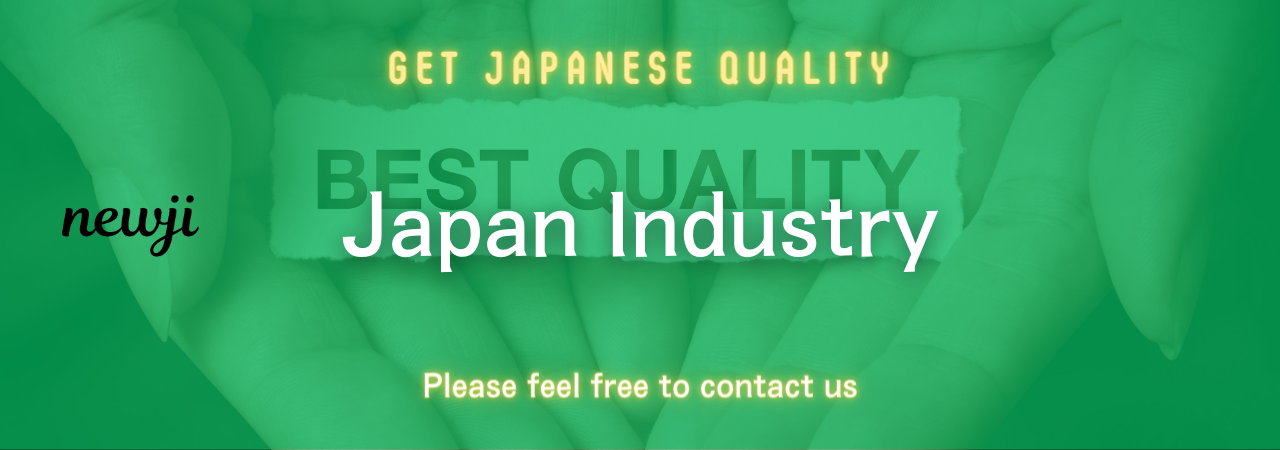
目次
Understanding the Basics of Finite Element Method (FEM)
The Finite Element Method (FEM) is a powerful computational technique used to solve complex problems in engineering and mathematical physics.
It subdivides a large system into smaller, simpler parts called finite elements.
These elements are then analyzed individually and reassembled to simulate the whole system.
With its application broadly spanning various disciplines, understanding FEM is crucial for those engaged in engineering and design tasks.
At the core of FEM is the concept of breaking down a complex structure into manageable elements.
Each element has distinct properties but is considered part of the whole framework.
When these elements are connected at nodes, they form a mesh that represents the entire structure.
By applying known forces and constraints, engineers can predict how these structures will behave under different conditions.
How FEM Works
The operation of FEM involves several key steps.
First, the structure or material domain is divided into small finite elements.
These elements can be triangles, quadrilaterals, tetrahedra, or hexahedra, depending on the complexity and the type of analysis required.
Next, a mathematical representation, usually in the form of differential equations, is set up based on the physics of the problem.
These equations relate to the element’s behavior, such as stress, strain, or heat transfer.
To solve these equations, boundary conditions and load conditions are applied.
Boundary conditions define the limitations within which the solution is applicable, while load conditions specify the forces acting on the structure.
The final step involves solving the equations numerically to provide a solution.
This solution may include the displacement of points, the distribution of stresses, or the temperature field within the material.
Applications of FEM in Removal Machining
Finite Element Method is particularly useful in removal machining processes such as milling, drilling, and turning.
These processes involve the removal of material from a workpiece to shape it into a desired form.
FEM helps in understanding the dynamics of cutting tools and the workpiece, thereby optimizing the machining process.
One of the key applications of FEM in removal machining is tool life prediction.
By simulating the cutting process, engineers can predict the wear and tear of tools, allowing for better planning and tool selection.
Additionally, FEM aids in optimizing cutting parameters, such as speed and feed rate, to enhance efficiency and reduce tool wear.
FEM also offers insights into the thermal effects of machining.
Understanding the distribution of heat generated during cutting helps prevent overheating, which can degrade material properties and increase wear.
Moreover, FEM allows for the analysis of chip formation, stress distribution, and residual stresses, crucial for ensuring high-quality machining finishes.
The Role of CAE in Enhanced Machining
Computer-Aided Engineering (CAE) encompasses software tools that support the simulation and analysis of engineering tasks.
CAE is integral in removal machining, as it enhances the implementation of FEM by providing a comprehensive platform for simulation.
With CAE tools, engineers can build detailed models of machining processes and evaluate various scenarios.
These tools make it easier to visualize the effects of different machining parameters, aiding in the decision-making process.
Through simulation, engineers can experiment virtually, testing various strategies without the cost implications of physical trials.
CAE also supports the integration of FEM with Computer-Aided Design (CAD) to ensure that the machining process aligns with design intents.
By coordinating CAD and FEM, engineers can achieve a smoother transition from design to manufacturing, reducing errors and improving product quality.
Key Considerations for Effective FEM Use in Machining
When applying FEM and CAE in removal machining, several factors should be taken into account to ensure accuracy and efficiency.
Mesh Quality and Density
The mesh is a crucial element of FEM.
A finer mesh, with smaller elements, generally leads to more accurate results.
However, this comes at the cost of increased computational resources and time.
It is important to strike a balance, using a mesh that is fine enough for accurate results but not so fine that it becomes computationally prohibitive.
Material Properties
Accurate representation of material properties is vital for reliable simulations.
These properties should be input carefully into CAE software and may include elasticity, thermal conductivity, and density.
Inaccurate data can lead to misleading simulation results, rendering them unreliable for decision-making.
Boundary Conditions
Properly defining boundary conditions is crucial for realistic simulations.
These conditions should replicate the actual environment and constraints under which the machining process occurs.
Failure to simulate realistic boundary conditions may result in impractical or overly optimistic outcomes.
Handling Non-Linearities
Machining often involves non-linear behaviors, such as plastic deformation or complex contact conditions.
These require sophisticated modeling techniques and considerations within FEM analysis.
Engineers need to be mindful of non-linearities and utilize advanced FEM tools that can accommodate these challenges.
Conclusion
The Finite Element Method (FEM) is an essential tool in modern engineering, especially in removal machining applications.
By combining FEM with CAE software, engineers can simulate and optimize complex machining processes, improving efficiency and product quality.
Understanding the fundamentals of FEM, its applications, and the considerations for effective use can significantly enhance machining operations.
Proper implementation of FEM and CAE helps in making informed decisions and achieving best-in-class manufacturing outcomes.
資料ダウンロード
QCD管理受発注クラウド「newji」は、受発注部門で必要なQCD管理全てを備えた、現場特化型兼クラウド型の今世紀最高の受発注管理システムとなります。
ユーザー登録
受発注業務の効率化だけでなく、システムを導入することで、コスト削減や製品・資材のステータス可視化のほか、属人化していた受発注情報の共有化による内部不正防止や統制にも役立ちます。
NEWJI DX
製造業に特化したデジタルトランスフォーメーション(DX)の実現を目指す請負開発型のコンサルティングサービスです。AI、iPaaS、および先端の技術を駆使して、製造プロセスの効率化、業務効率化、チームワーク強化、コスト削減、品質向上を実現します。このサービスは、製造業の課題を深く理解し、それに対する最適なデジタルソリューションを提供することで、企業が持続的な成長とイノベーションを達成できるようサポートします。
製造業ニュース解説
製造業、主に購買・調達部門にお勤めの方々に向けた情報を配信しております。
新任の方やベテランの方、管理職を対象とした幅広いコンテンツをご用意しております。
お問い合わせ
コストダウンが利益に直結する術だと理解していても、なかなか前に進めることができない状況。そんな時は、newjiのコストダウン自動化機能で大きく利益貢献しよう!
(β版非公開)