- お役立ち記事
- Basics of surface hardening heat treatment technology and countermeasures against defects and troubles
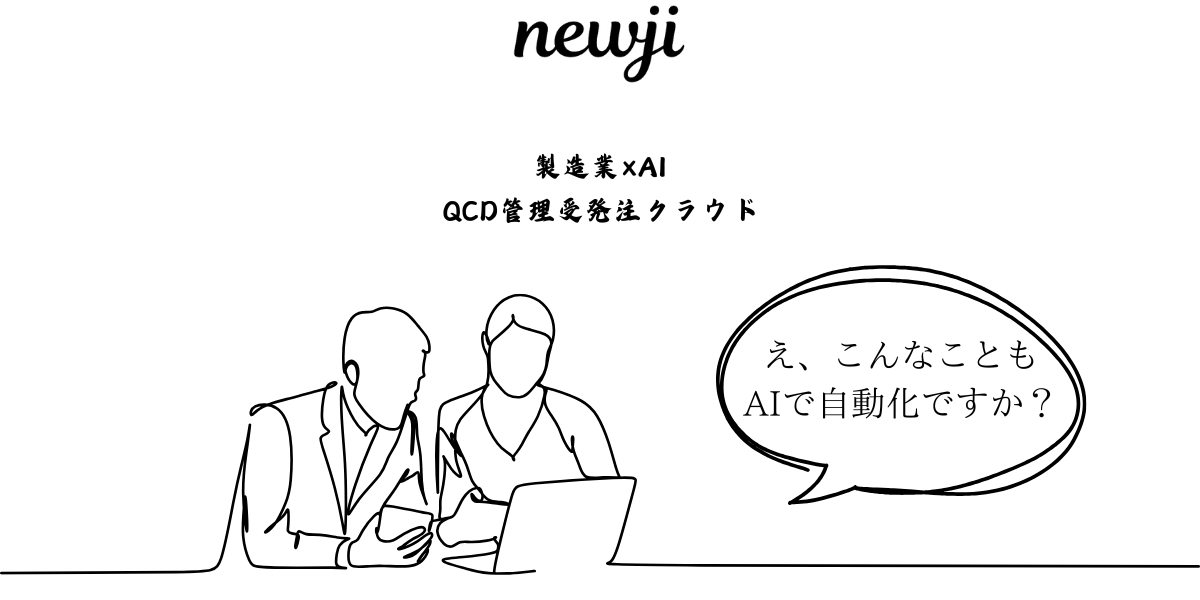
Basics of surface hardening heat treatment technology and countermeasures against defects and troubles
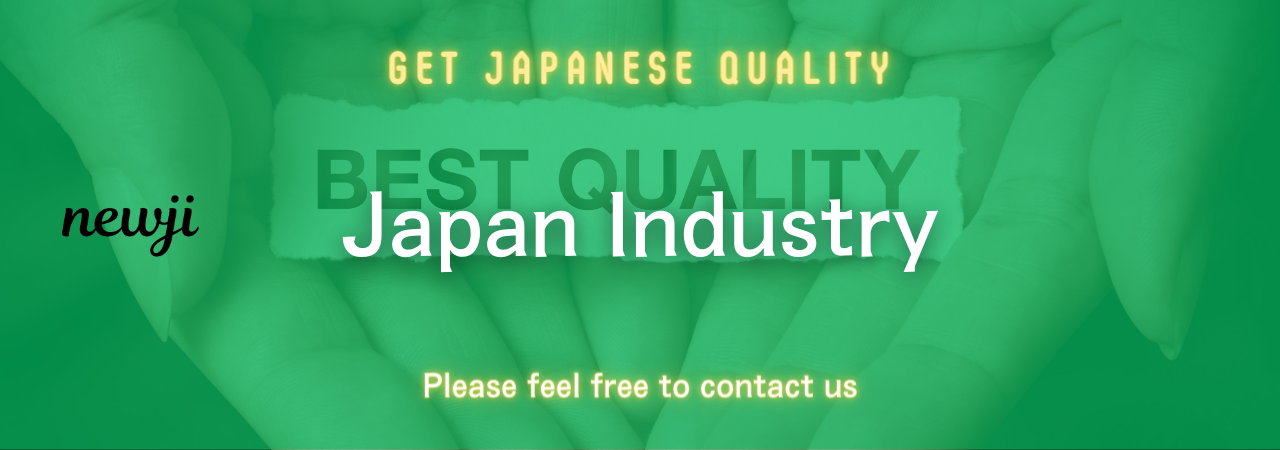
目次
Understanding Surface Hardening Heat Treatment
Surface hardening heat treatment is an essential process in the field of metallurgy and manufacturing.
It’s used to increase the hardness of the outer surface of a material while maintaining a softer, ductile interior, thus enhancing both wear resistance and impact strength.
This process is crucial in industries where components endure significant stress and wear, such as automotive, aerospace, and heavy machinery manufacturing.
The Basics of Surface Hardening Techniques
Several methods are utilized for surface hardening, each with its specific applications and advantages.
Some of the most common techniques include:
Carburizing
Carburizing involves introducing carbon into a steel component’s surface layer.
This is typically done by heating the component in a carbon-rich environment.
The process results in a hard, carbon-enriched surface once the component is quenched.
Nitriding
Through nitriding, nitrogen is diffused into the surface of the metal.
This is often preferred for alloy steels.
Nitriding provides high surface hardness and wear resistance without the need for quenching.
Induction Hardening
Induction hardening uses electromagnetic induction to heat the component’s surface rapidly followed by immediate quenching.
This method is advantageous due to its precision and the ability to select specific hardening areas.
Flame Hardening
Flame hardening employs an oxy-gas flame to heat the material surface.
Immediately after heating, the surface is quenched.
It’s suitable for complex shapes and larger components.
Countermeasures Against Defects in Surface Hardening
While surface hardening significantly enhances material properties, it’s not without challenges.
Understanding potential defects and implementing countermeasures is vital for ensuring product integrity.
Common Defects and Remedies
Cracking
Cracking can occur due to excessive thermal stress during the hardening process.
To mitigate this risk, it’s essential to control heating and cooling rates.
Preheating the component before hardening and using tempering after the process can also help reduce cracking.
Warping
Warping is a distortion in the shape of the component caused by uneven heat application or rapid cooling.
To counteract warping, uniform heating should be ensured, and gradual cooling methods should be employed.
Decarburization
Decarburization involves the loss of carbon from the metal surface, leading to reduced hardness.
This can be avoided by maintaining a controlled atmosphere with adequate carbon potential during heat treatment.
Oxidation
Oxidation happens when metals are heated in the presence of oxygen, leading to the formation of an oxide layer.
Using inert gas atmospheres like nitrogen or argon during the treatment can prevent oxidation.
Successful Implementation of Surface Hardening
To ensure successful surface hardening, certain factors must be considered:
Material Selection
Different materials react differently to surface hardening methods, so choose a compatible material for the desired hardening technique.
For example, stainless steel responds well to carburizing, while certain low-alloy steels may be better suited for nitriding.
Proper Equipment
Employing the right equipment is crucial for achieving the desired results.
Surface hardening requires precision, so ensure the equipment is capable of controlling temperature and atmosphere accurately.
Process Control
Meticulously controlling process parameters such as time, temperature, and atmosphere composition is essential.
Automated systems can assist in maintaining consistent control over these variables.
Post-Treatment Procedures
Sometimes post-treatment processes are necessary to optimize the mechanical properties and relieve internal stresses.
Tempering or stress-relief annealing can enhance the toughness of the treated material.
Advantages of Surface Hardening
Surface hardening provides several benefits that improve the performance and longevity of components.
These advantages include:
Enhanced Wear Resistance
The hard surface layer is more resistant to abrasion and wear, extending the life of components in high-stress environments.
Improved Fatigue Strength
The process increases the fatigue strength of metals, reducing the likelihood of failure under cyclic loads.
Cost Efficiency
By improving the durability of parts, surface hardening reduces the need for frequent replacements, leading to cost savings in the long run.
Lightweight Solutions
By allowing components to have a strong, hard surface layer with a tough core, lightweight materials can be used without compromising strength.
Conclusion
Understanding and mastering the basics of surface hardening heat treatment is crucial for anyone involved in fields that demand high-performance materials.
By selecting the appropriate technique, mitigating potential defects, and controlling the process parameters, manufacturers can significantly enhance the properties and lifespan of their products.
The technology continues to evolve, offering more efficient and precise methods, thus promising an exciting future for industries reliant on high-strength materials.
資料ダウンロード
QCD調達購買管理クラウド「newji」は、調達購買部門で必要なQCD管理全てを備えた、現場特化型兼クラウド型の今世紀最高の購買管理システムとなります。
ユーザー登録
調達購買業務の効率化だけでなく、システムを導入することで、コスト削減や製品・資材のステータス可視化のほか、属人化していた購買情報の共有化による内部不正防止や統制にも役立ちます。
NEWJI DX
製造業に特化したデジタルトランスフォーメーション(DX)の実現を目指す請負開発型のコンサルティングサービスです。AI、iPaaS、および先端の技術を駆使して、製造プロセスの効率化、業務効率化、チームワーク強化、コスト削減、品質向上を実現します。このサービスは、製造業の課題を深く理解し、それに対する最適なデジタルソリューションを提供することで、企業が持続的な成長とイノベーションを達成できるようサポートします。
オンライン講座
製造業、主に購買・調達部門にお勤めの方々に向けた情報を配信しております。
新任の方やベテランの方、管理職を対象とした幅広いコンテンツをご用意しております。
お問い合わせ
コストダウンが利益に直結する術だと理解していても、なかなか前に進めることができない状況。そんな時は、newjiのコストダウン自動化機能で大きく利益貢献しよう!
(Β版非公開)