- お役立ち記事
- Fundamentals of fracture mechanics and finite element method and application to fatigue life estimation
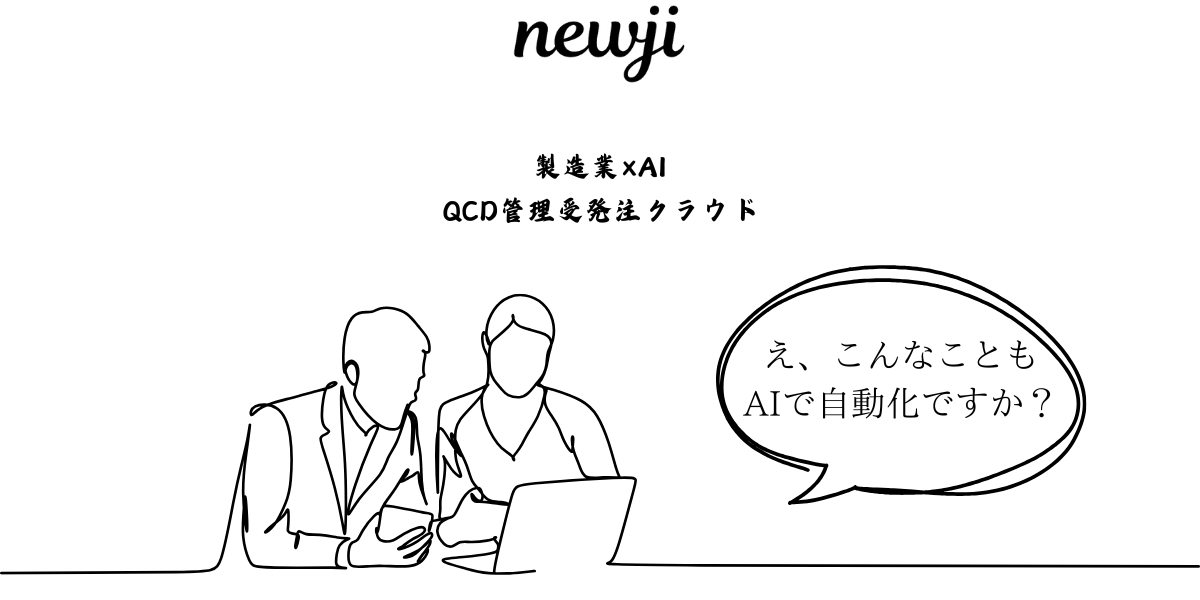
Fundamentals of fracture mechanics and finite element method and application to fatigue life estimation
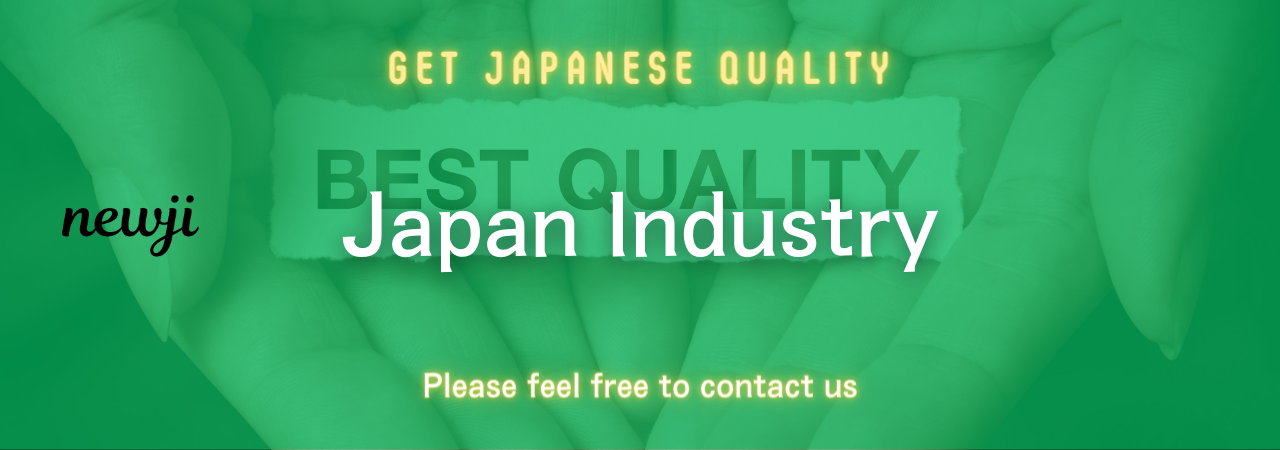
目次
Understanding Fracture Mechanics
Fracture mechanics is a critical field of study focused on understanding the propagation of cracks in materials.
Its importance lies in predicting and preventing catastrophic failures in structures, ranging from buildings and bridges to aerospace components and automotive parts.
The study of fracture mechanics can be traced back to the early 20th century, with pioneering work done by scientists like A.A. Griffith.
Their research laid the foundations for modern fracture mechanics, which combines principles of materials science, physics, and engineering.
At its core, fracture mechanics seeks to understand how and why materials fail under various types of stress.
This understanding is crucial for ensuring the reliability and safety of structures in countless industries.
Types of Fractures
Fractures can be categorized based on the type of stress that causes them.
There are generally three types of fractures: Mode I (opening mode), Mode II (sliding mode), and Mode III (tearing mode).
Each type corresponds to different stress conditions, and understanding these modes is essential for experts seeking to predict and mitigate material failure.
Mode I fractures occur when a material is subjected to tensile stress, causing it to open like a book.
Mode II fractures are driven by in-plane shear stress that causes sliding, while Mode III fractures occur due to out-of-plane shear stress, leading to tearing.
By analyzing the stressors and material responses, engineers can develop solutions to prevent these types of fractures.
Linear Elastic Fracture Mechanics (LEFM)
Linear Elastic Fracture Mechanics (LEFM) is an approach used when a material is considered to be linearly elastic, even in the presence of a crack.
LEFM assumes that the stress-strain state remains linear elastic and that the plastic deformation in the material is limited to the region immediately surrounding the crack tip.
This approach is widely used when dealing with brittle materials or when stress conditions lead to minimal plastic deformation.
Key concepts in LEFM include stress intensity factors, strain energy release rates, and fracture toughness.
These metrics help quantify how close a material is to failure and aid in designing safer structures.
Elastic-Plastic Fracture Mechanics (EPFM)
Elastic-Plastic Fracture Mechanics (EPFM) extends beyond the assumptions of LEFM by considering plastic deformation around the crack tip.
This makes EPFM suitable for materials that exhibit significant plasticity before fracture, such as ductile metals.
EPFM uses parameters such as the J-integral and crack tip opening displacement (CTOD) to describe fracture behavior.
These metrics provide a more comprehensive understanding of how stress distribution and material properties influence crack propagation.
EPFM is particularly valuable in industries where materials are subjected to high loads and temperatures, requiring rigorous safety standards.
The Finite Element Method (FEM)
The Finite Element Method (FEM) is a numerical approach used to solve complex engineering problems involving stress and deformation in structures.
FEM subdivides a large system into smaller, simpler components called elements, simplifying the analysis of stresses and strains.
This method allows engineers to build a comprehensive understanding of how forces distribute throughout a structure.
How FEM Works
FEM involves creating a mesh of elements that represent the structure under analysis.
Each element is defined by its shape, size, and the material properties assigned to it.
Once the mesh is established, boundary conditions and external forces are applied as inputs.
Through mathematical equations, FEM calculates the behavior of each element under the given conditions, providing results like displacement, strain, and stress distribution.
This provides a visual simulation of how a structure will react to specific stresses and loads.
Applications of FEM
FEM is used in numerous industries, including aerospace, automotive, and civil engineering.
Engineers utilize FEM to design and analyze components such as aircraft wings, car bodies, and bridges, optimizing these structures for performance and safety.
By using FEM simulations, engineers can predict potential failure points, improving designs before production.
Additionally, FEM is invaluable for failure analysis post-incident, as it allows engineers to understand why a structure failed and how to prevent future occurrences.
Fatigue Life Estimation
Fatigue life estimation is a critical process that predicts the number of cycles a material can endure before failure due to repeated loading.
This type of failure is known as fatigue and is a common issue in components that experience cyclical stress, such as aircraft wings and automotive suspension systems.
Factors Affecting Fatigue Life
Several factors influence a material’s fatigue life, including stress range, material properties, surface finish, and environmental conditions.
The stress range refers to the variation in stress experienced by the material during a load cycle.
The larger the stress range, the shorter the fatigue life.
Material properties such as hardness, ductility, and toughness also play significant roles in determining how susceptible a material is to fatigue.
Surface finish and environmental conditions, like corrosion and temperature, can further influence fatigue life by affecting crack initiation and propagation.
Methods for Estimating Fatigue Life
One common method for estimating fatigue life is the strain-life approach, which considers the strain-energy relationships in a material under cyclic loading.
Another method is the stress-life approach, which uses S-N curves to represent the stress level versus the number of cycles to failure.
FEM can be integrated with these methods to simulate stress-strain conditions accurately, aiding in more precise fatigue life predictions.
For engineers and designers, accurately estimating fatigue life is essential for ensuring product reliability and preventing premature failure.
Conclusion
Understanding fracture mechanics, the Finite Element Method, and fatigue life estimation are vital components in the field of engineering.
They provide the tools necessary to design and evaluate structures capable of withstanding the forces and conditions they encounter over their lifetimes.
By mastering these fundamentals, engineers can prevent failures that might lead to catastrophic consequences, ultimately ensuring the safety and longevity of critical structural components.
資料ダウンロード
QCD調達購買管理クラウド「newji」は、調達購買部門で必要なQCD管理全てを備えた、現場特化型兼クラウド型の今世紀最高の購買管理システムとなります。
ユーザー登録
調達購買業務の効率化だけでなく、システムを導入することで、コスト削減や製品・資材のステータス可視化のほか、属人化していた購買情報の共有化による内部不正防止や統制にも役立ちます。
NEWJI DX
製造業に特化したデジタルトランスフォーメーション(DX)の実現を目指す請負開発型のコンサルティングサービスです。AI、iPaaS、および先端の技術を駆使して、製造プロセスの効率化、業務効率化、チームワーク強化、コスト削減、品質向上を実現します。このサービスは、製造業の課題を深く理解し、それに対する最適なデジタルソリューションを提供することで、企業が持続的な成長とイノベーションを達成できるようサポートします。
オンライン講座
製造業、主に購買・調達部門にお勤めの方々に向けた情報を配信しております。
新任の方やベテランの方、管理職を対象とした幅広いコンテンツをご用意しております。
お問い合わせ
コストダウンが利益に直結する術だと理解していても、なかなか前に進めることができない状況。そんな時は、newjiのコストダウン自動化機能で大きく利益貢献しよう!
(Β版非公開)