- お役立ち記事
- Unlocking Excellence: The Basics of QC Process Charts in Japanese Manufacturing
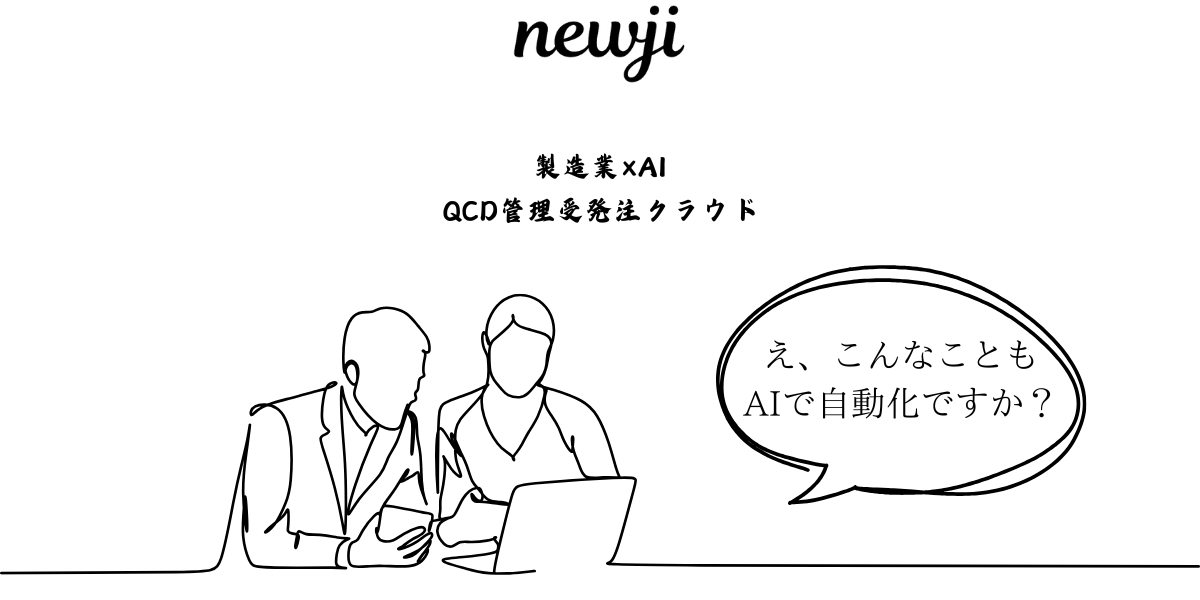
Unlocking Excellence: The Basics of QC Process Charts in Japanese Manufacturing
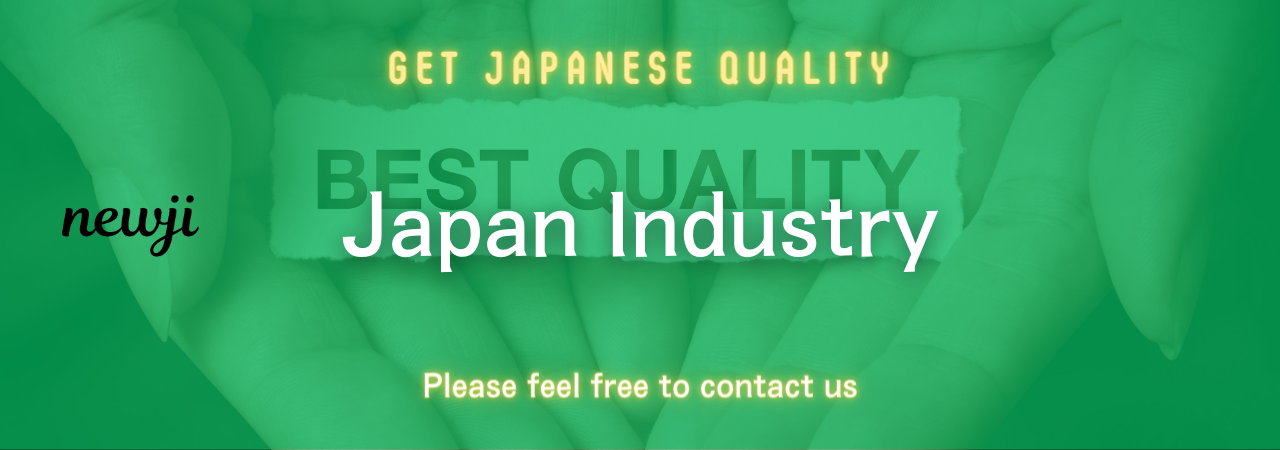
目次
Introduction to QC Process Charts in Japanese Manufacturing
Quality Control (QC) is a cornerstone of Japanese manufacturing excellence.
At the heart of this commitment lies the QC Process Chart, a tool that visually maps out the various stages of production to ensure consistent quality.
Understanding the basics of QC Process Charts is essential for procurement and purchasing professionals who engage with Japanese suppliers.
This article delves into the fundamentals of QC Process Charts, their advantages and disadvantages, and best practices for leveraging them in international procurement.
The Role of QC Process Charts in Quality Assurance
QC Process Charts serve as a blueprint for quality assurance in manufacturing.
They outline each step in the production process, allowing for meticulous monitoring and control.
In Japanese manufacturing, where precision and reliability are paramount, these charts enable companies to maintain high standards consistently.
Understanding the Components of QC Process Charts
A typical QC Process Chart includes several key components:
**Process Steps:** Detailed descriptions of each phase in production.
**Quality Metrics:** Specific criteria used to assess quality at each step.
**Inspection Points:** Designated stages where inspections occur to identify defects.
**Responsibility Assignments:** Clear delineation of roles and responsibilities for maintaining quality.
Benefits of Implementing QC Process Charts
The implementation of QC Process Charts offers numerous advantages:
1. **Enhanced Visibility:** Provides a clear overview of the entire production process, making it easier to identify potential bottlenecks.
2. **Improved Communication:** Facilitates better communication between departments by clearly defining each process step and responsibility.
3. **Consistent Quality:** Ensures that every product meets predetermined quality standards by standardizing processes.
4. **Efficient Problem Solving:** Aids in quickly pinpointing areas where quality issues arise, allowing for prompt corrective actions.
Advantages of QC Process Charts in Procurement and Purchasing
For procurement and purchasing professionals, QC Process Charts are invaluable tools.
They offer insights into a supplier’s production process, enabling informed decision-making and effective supplier management.
Informed Supplier Selection
By analyzing QC Process Charts, procurement teams can assess a supplier’s capability to maintain quality standards.
This reduces the risk of defects and ensures that the purchased components meet the necessary specifications.
Effective Contract Negotiation
Understanding the QC Process allows purchasers to negotiate more effectively.
They can address specific quality metrics and inspection points in contracts, ensuring that suppliers adhere to stringent quality requirements.
Enhanced Supplier Relationships
Transparency provided by QC Process Charts fosters trust between buyers and suppliers.
Collaborative efforts to maintain quality can lead to long-term, mutually beneficial relationships.
Disadvantages and Challenges of QC Process Charts
While QC Process Charts offer significant benefits, there are also challenges to consider.
Complexity in Implementation
Creating comprehensive QC Process Charts requires detailed knowledge of the manufacturing process.
This can be time-consuming and may necessitate specialized training for accurate development and interpretation.
Rigidity in Processes
Strict adherence to QC Process Charts may limit flexibility in production.
In rapidly changing markets, the inability to adapt processes quickly can be a disadvantage.
Dependency on Accurate Data
The effectiveness of QC Process Charts depends on the accuracy of the data input.
Inaccurate or outdated information can lead to flawed quality control and potential defects slipping through.
Supplier Negotiation Techniques Using QC Process Charts
Leveraging QC Process Charts in negotiations can significantly enhance procurement outcomes.
Here are effective techniques:
Data-Driven Discussions
Use specific data from QC Process Charts to discuss quality expectations and standards.
This ensures that both parties have a clear understanding of requirements.
Setting Clear Quality Expectations
Define explicit quality metrics and inspection points within the contract.
This minimizes ambiguities and sets a clear benchmark for performance.
Collaborative Problem Solving
Encourage joint review of QC Process Charts to identify and address potential quality issues together.
This collaborative approach fosters a sense of partnership and shared responsibility for quality.
Market Conditions Impacting QC Process Chart Utilization
Various market conditions can influence how QC Process Charts are utilized in procurement and purchasing.
Global Supply Chain Dynamics
Fluctuations in global supply chains, such as delays or disruptions, can affect the implementation of QC Process Charts.
Procurement professionals must remain adaptable and work closely with suppliers to maintain quality standards despite challenges.
Technological Advancements
Advancements in manufacturing technology can lead to updates in QC Process Charts.
Staying abreast of technological changes ensures that quality control measures remain effective and relevant.
Regulatory Changes
Changes in international standards and regulations may necessitate revisions to QC Process Charts.
Procurement teams must ensure that their quality control processes comply with evolving legal requirements.
Best Practices for Utilizing QC Process Charts in Procurement
Implementing QC Process Charts effectively requires adherence to best practices tailored to procurement and purchasing functions.
Comprehensive Training
Provide thorough training for procurement teams on how to interpret and utilize QC Process Charts.
This ensures that they can accurately assess supplier capabilities and quality control measures.
Regular Updates and Reviews
Maintain and regularly update QC Process Charts to reflect changes in production processes or quality standards.
Periodic reviews help identify areas for improvement and ensure ongoing relevance.
Integration with Procurement Systems
Integrate QC Process Charts with existing procurement and supply chain management systems.
This facilitates seamless information flow and enhances decision-making efficiency.
Collaborative Engagement with Suppliers
Engage suppliers in the creation and maintenance of QC Process Charts.
Collaborative efforts ensure that both parties are aligned in their quality objectives and processes.
Case Studies: Success Stories in Japanese Manufacturing
Examining real-world examples can illustrate the effectiveness of QC Process Charts in procurement and purchasing.
Automotive Industry Leader
A leading Japanese automotive manufacturer utilized QC Process Charts to streamline its supply chain.
By collaborating with suppliers to implement standardized quality control measures, the company significantly reduced defect rates and improved overall product reliability.
Electronics Manufacturer’s Approach
A prominent electronics company adopted QC Process Charts to enhance its supplier evaluation process.
This approach enabled more accurate assessments of supplier capabilities, leading to better quality components and increased customer satisfaction.
Overcoming Challenges in Implementing QC Process Charts
Despite their benefits, implementing QC Process Charts can present challenges.
However, strategic approaches can mitigate these issues.
Addressing Complexity
Simplify QC Process Charts by focusing on critical process steps and key quality metrics.
This reduces complexity and makes the charts more manageable and easier to use.
Maintaining Flexibility
Design QC Process Charts with some degree of flexibility to accommodate changes in production processes or market demands.
This balance ensures that quality control remains robust without stifling innovation.
Ensuring Data Accuracy
Implement robust data management practices to maintain the accuracy and reliability of QC Process Charts.
Regular audits and updates can help preserve data integrity and effectiveness.
The Future of QC Process Charts in Japanese Procurement
The evolution of manufacturing and procurement practices will shape the future use of QC Process Charts.
Integration with Digital Technologies
Emerging technologies like artificial intelligence and machine learning can enhance QC Process Charts by providing predictive analytics and real-time quality monitoring.
This integration can lead to more proactive quality control measures and increased efficiency.
Sustainability and Quality Control
As sustainability becomes a priority, QC Process Charts will likely incorporate environmental and social quality metrics.
This aligns quality control with broader corporate responsibility goals and regulatory requirements.
Global Standardization Efforts
Efforts to standardize quality control processes across global supply chains will influence the design and implementation of QC Process Charts.
Standardization facilitates better collaboration and consistency in quality across different regions and suppliers.
Conclusion
QC Process Charts are integral to maintaining high-quality standards in Japanese manufacturing.
For procurement and purchasing professionals, understanding and effectively utilizing these charts is crucial for successful supplier management and product quality assurance.
Despite challenges, the benefits of QC Process Charts, including enhanced visibility, improved communication, and consistent quality, make them invaluable tools in international procurement.
By adhering to best practices and embracing technological advancements, organizations can unlock excellence in their procurement processes and foster strong, quality-driven supplier relationships.
資料ダウンロード
QCD調達購買管理クラウド「newji」は、調達購買部門で必要なQCD管理全てを備えた、現場特化型兼クラウド型の今世紀最高の購買管理システムとなります。
ユーザー登録
調達購買業務の効率化だけでなく、システムを導入することで、コスト削減や製品・資材のステータス可視化のほか、属人化していた購買情報の共有化による内部不正防止や統制にも役立ちます。
NEWJI DX
製造業に特化したデジタルトランスフォーメーション(DX)の実現を目指す請負開発型のコンサルティングサービスです。AI、iPaaS、および先端の技術を駆使して、製造プロセスの効率化、業務効率化、チームワーク強化、コスト削減、品質向上を実現します。このサービスは、製造業の課題を深く理解し、それに対する最適なデジタルソリューションを提供することで、企業が持続的な成長とイノベーションを達成できるようサポートします。
オンライン講座
製造業、主に購買・調達部門にお勤めの方々に向けた情報を配信しております。
新任の方やベテランの方、管理職を対象とした幅広いコンテンツをご用意しております。
お問い合わせ
コストダウンが利益に直結する術だと理解していても、なかなか前に進めることができない状況。そんな時は、newjiのコストダウン自動化機能で大きく利益貢献しよう!
(Β版非公開)