- お役立ち記事
- Revolutionizing Japanese Manufacturing: The Impact of High-Frequency High-Current Inductors
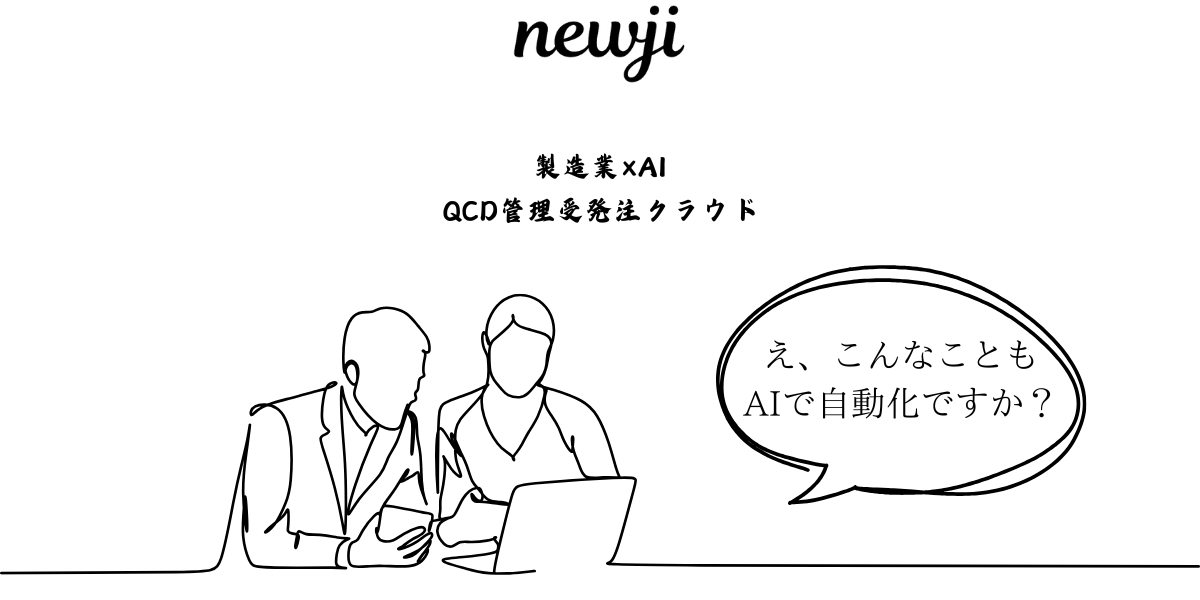
Revolutionizing Japanese Manufacturing: The Impact of High-Frequency High-Current Inductors
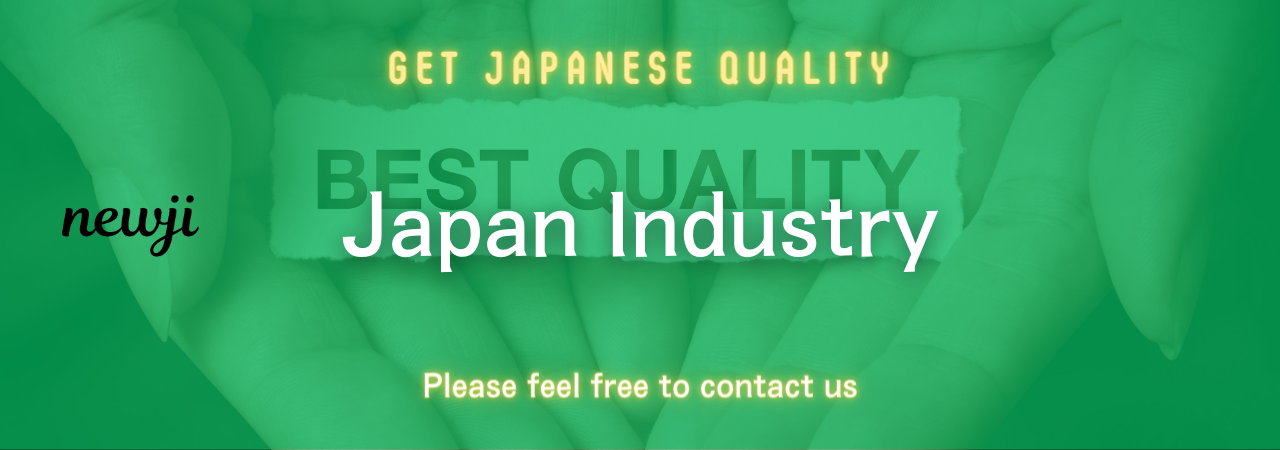
目次
Introduction
Japanese manufacturing has long been synonymous with precision, reliability, and innovation. In recent years, one of the pivotal advancements driving this reputation forward is the integration of high-frequency high-current inductors. These components are revolutionizing various aspects of manufacturing processes, contributing to enhanced efficiency, superior product quality, and competitive advantages in the global market. This article delves into the impact of high-frequency high-current inductors on Japanese manufacturing, exploring their benefits, challenges, supplier negotiation techniques, market conditions, and best practices from a procurement and purchasing perspective.
Understanding High-Frequency High-Current Inductors
High-frequency high-current inductors are essential components in electronic circuits, particularly in power supply systems. They store energy in a magnetic field when electrical current passes through them, playing a crucial role in managing energy flow and ensuring the stability of electronic devices. In the context of manufacturing, these inductors are vital for various applications, including switching power supplies, motor drives, and energy-efficient lighting systems.
Technical Specifications and Innovations
Japanese manufacturers have been at the forefront of developing inductors with enhanced specifications to meet the demanding requirements of modern electronics. Innovations include:
– **Increased Efficiency:** Advanced materials and design techniques have led to inductors with higher efficiency, reducing energy losses and improving overall system performance.
– **Compact Design:** Miniaturization of inductors allows for more compact electronic devices, supporting the trend towards smaller and more portable products.
– **Thermal Management:** Improved heat dissipation technologies ensure that inductors operate reliably under high-current conditions, extending their lifespan and maintaining performance.
The Role of Inductors in Japanese Manufacturing
Inductors play a multifaceted role in the manufacturing processes of Japanese companies, impacting various sectors including automotive, consumer electronics, industrial machinery, and renewable energy.
Automotive Industry
In the automotive sector, high-frequency high-current inductors are integral to electric vehicles (EVs) and hybrid systems. They are used in power electronics for motor control, energy storage systems, and charging infrastructure. The precision and reliability of these inductors contribute to the efficiency and performance of EVs, supporting Japan’s leadership in sustainable transportation solutions.
Consumer Electronics
Japanese consumer electronics are renowned for their quality and innovation. High-frequency inductors are crucial in devices such as smartphones, laptops, and home appliances, where they ensure stable power delivery and efficient energy management. The miniaturization and efficiency of these components enable the development of sleek, high-performance products that meet consumer demands.
Industrial Machinery
In industrial applications, high-frequency inductors enhance the performance of machinery by improving power regulation and reducing energy consumption. They are used in motor drives, automation systems, and power distribution units, contributing to the overall efficiency and reliability of manufacturing operations.
Renewable Energy Systems
The integration of high-frequency inductors in renewable energy systems, such as solar inverters and wind turbines, enhances energy conversion efficiency and grid compatibility. Japanese manufacturers are leveraging these components to develop advanced renewable energy technologies, supporting global sustainability initiatives.
Advantages of High-Frequency High-Current Inductors
The adoption of high-frequency high-current inductors in Japanese manufacturing offers numerous advantages that drive operational excellence and competitive differentiation.
Enhanced Efficiency
High-frequency inductors operate with minimal energy loss, improving the overall efficiency of electronic systems. This efficiency translates to lower energy consumption, reduced operational costs, and a smaller environmental footprint, aligning with global sustainability goals.
Improved Performance
The ability to handle high currents and operate at high frequencies ensures that electronic devices perform reliably under demanding conditions. This reliability is critical in applications such as automotive systems and industrial machinery, where performance consistency is paramount.
Space and Weight Reduction
Advanced inductor designs enable significant reductions in size and weight, facilitating the development of compact and lightweight products. This is particularly beneficial in consumer electronics and automotive applications, where space constraints are a common challenge.
Thermal Stability
Innovative thermal management solutions in high-frequency inductors ensure stable operation even under high-current loads. This stability prevents overheating, extends component lifespan, and maintains product performance over time.
Challenges and Disadvantages
While high-frequency high-current inductors offer substantial benefits, they also present certain challenges that manufacturers must address to maximize their potential.
Cost Considerations
Advanced inductors with high-frequency and high-current capabilities are often more expensive than standard components. The initial investment in these components can impact overall manufacturing costs, necessitating careful cost-benefit analysis and strategic procurement planning.
Complexity in Design and Integration
Incorporating high-frequency inductors into electronic systems requires specialized design expertise. Manufacturers must ensure seamless integration with other components, which can increase the complexity of the design and development process.
Reliability Issues
Operating at high frequencies and currents can introduce reliability challenges, such as electromagnetic interference (EMI) and thermal stress. Ensuring the long-term reliability of inductors under these conditions requires robust design practices and thorough testing.
Supply Chain Constraints
The specialized nature of high-frequency high-current inductors can lead to supply chain bottlenecks, particularly if demand exceeds the production capacity of key suppliers. Diversifying the supplier base and establishing strong relationships with reliable partners are essential strategies to mitigate supply risks.
Supplier Negotiation Techniques
Effective supplier negotiation is crucial for securing high-frequency high-current inductors that meet quality, performance, and cost requirements. Japanese manufacturing companies employ several strategies to optimize their procurement processes.
Establishing Strong Relationships
Building long-term relationships with suppliers fosters trust and collaboration. Japanese companies often engage in continuous communication and partnership-building activities, ensuring that suppliers understand their specific needs and are committed to delivering high-quality components.
Leveraging Bulk Purchasing
By consolidating orders and committing to large purchase volumes, companies can negotiate better pricing and favorable terms. Bulk purchasing agreements can also enhance supply chain stability, ensuring consistent component availability.
Implementing Collaborative Development
Collaborating with suppliers during the product development phase ensures that inductors are tailored to specific application requirements. Joint development initiatives can lead to innovative solutions and optimized component performance, benefiting both parties.
Negotiating Flexible Contracts
Flexible contracts that allow for scalability and adaptability can accommodate changing demand and technological advancements. Negotiating terms that include options for future adjustments helps manufacturers stay agile in a dynamic market environment.
Ensuring Quality Assurance
Establishing clear quality standards and expectations is essential. Companies negotiate quality assurance measures, including rigorous testing protocols and compliance with industry standards, to ensure that suppliers deliver reliable and high-performance inductors.
Market Conditions and Trends
The market for high-frequency high-current inductors is influenced by various factors, including technological advancements, economic conditions, and industry-specific demands.
Technological Advancements
Continuous innovations in materials science and manufacturing technologies drive the development of more efficient and compact inductors. Trends such as the Internet of Things (IoT), electric vehicles, and renewable energy systems are increasing demand for advanced inductive components.
Economic Factors
Global economic conditions, including fluctuations in currency exchange rates and trade policies, impact the procurement costs and supply chain dynamics for inductors. Japanese manufacturers must stay abreast of economic trends to make informed purchasing decisions.
Industry-Specific Demands
Different industries have unique requirements for inductors. For example, the automotive sector prioritizes reliability and efficiency, while consumer electronics focus on miniaturization and performance. Understanding these specific demands allows manufacturers to tailor their procurement strategies accordingly.
Supply Chain Dynamics
Global supply chain disruptions, such as those caused by geopolitical tensions or natural disasters, can affect the availability and cost of high-frequency high-current inductors. Diversifying the supplier base and establishing contingency plans are essential strategies to mitigate these risks.
Sustainability and Regulatory Compliance
Increasing emphasis on sustainability and regulatory compliance is shaping the market. Manufacturers are seeking inductors that not only perform well but also adhere to environmental standards and reduce the overall carbon footprint of their operations.
Best Practices in Procurement and Purchasing
To effectively leverage high-frequency high-current inductors, Japanese manufacturing companies adopt best practices in procurement and purchasing, ensuring optimal performance and cost-efficiency.
Comprehensive Supplier Evaluation
Conducting thorough evaluations of potential suppliers is fundamental. This includes assessing their technical capabilities, financial stability, quality management systems, and compliance with industry standards. A robust evaluation process ensures the selection of reliable partners.
Strategic Sourcing
Strategic sourcing involves identifying and engaging suppliers that provide the best value in terms of quality, cost, and delivery reliability. By aligning sourcing strategies with overall business objectives, companies can enhance their competitive advantage.
Demand Forecasting and Inventory Management
Accurate demand forecasting allows for better inventory management, reducing the risks of stockouts or excess inventory. Implementing advanced forecasting techniques and inventory optimization tools helps maintain the right balance between supply and demand.
Continuous Improvement and Feedback Loops
Establishing feedback mechanisms with suppliers fosters continuous improvement. Regular performance reviews and collaborative problem-solving initiatives help identify areas for enhancement and drive mutual growth.
Embracing Technology and Digital Tools
Leveraging digital procurement tools and technologies, such as e-procurement platforms and supply chain management software, streamlines the purchasing process. These tools enhance visibility, improve decision-making, and increase overall efficiency.
Risk Management and Mitigation
Proactive risk management strategies are essential to address potential disruptions in the supply chain. This includes identifying critical suppliers, assessing risk exposure, and developing contingency plans to ensure continuity of supply.
Training and Development
Investing in the training and development of procurement and purchasing teams ensures that they are equipped with the latest knowledge and skills. Continuous education on industry trends, negotiation techniques, and technology advancements enhances the effectiveness of the procurement function.
Case Studies: Success Stories in Japanese Manufacturing
Examining real-world examples of Japanese manufacturers successfully integrating high-frequency high-current inductors provides valuable insights into best practices and effective strategies.
Toyota Motor Corporation
Toyota has incorporated high-frequency inductors into its hybrid and electric vehicle power systems. By collaborating closely with inductors suppliers, Toyota has optimized energy efficiency and performance, reinforcing its position as a leader in sustainable automotive technologies.
Panasonic Corporation
Panasonic utilizes high-frequency inductors in its consumer electronics range, including smartphones and laptops. Their focus on miniaturization and energy efficiency has been achieved through strategic partnerships with inductors manufacturers, ensuring high-quality components that meet stringent performance standards.
Hitachi Ltd.
Hitachi employs high-frequency high-current inductors in its industrial machinery and automation systems. By implementing rigorous quality assurance processes and fostering collaborative relationships with suppliers, Hitachi has enhanced the reliability and efficiency of its products.
Kyocera Corporation
Kyocera integrates high-frequency inductors into its renewable energy solutions, such as solar inverters. Their commitment to innovation and sustainability is supported by the use of advanced inductors, contributing to the efficiency and effectiveness of their energy systems.
Future Outlook
The future of high-frequency high-current inductors in Japanese manufacturing looks promising, driven by continuous technological advancements and evolving industry needs.
Advancements in Material Science
Ongoing research in material science is expected to lead to the development of inductors with even higher efficiency, better thermal management, and greater durability. These advancements will further enhance the performance of electronic systems across various industries.
Integration with Smart Manufacturing
As Japanese manufacturers embrace Industry 4.0 and smart manufacturing practices, high-frequency inductors will play a crucial role in enabling intelligent power management and energy-efficient operations. Their integration with IoT devices and automation systems will drive further innovations in manufacturing processes.
Expansion into Emerging Markets
The growing demand for high-frequency inductors in emerging markets, particularly in electric vehicles and renewable energy sectors, presents significant growth opportunities. Japanese manufacturers are well-positioned to capitalize on these trends through their expertise and technological prowess.
Focus on Sustainability
Sustainability will continue to be a key driver in the development and procurement of high-frequency inductors. Manufacturers will prioritize components that contribute to energy efficiency and reduce environmental impact, aligning with global sustainability initiatives.
Customization and Flexibility
The demand for customized inductors tailored to specific application requirements will increase. Manufacturers will need to provide flexible solutions and bespoke designs to meet the diverse needs of their clients, fostering innovation and collaboration.
Conclusion
High-frequency high-current inductors are playing a transformative role in revolutionizing Japanese manufacturing. Their integration into various sectors, from automotive to consumer electronics and renewable energy, underscores their importance in enhancing efficiency, performance, and competitiveness. While challenges such as cost and supply chain complexities exist, effective procurement and purchasing strategies, coupled with strong supplier relationships and best practices, enable manufacturers to harness the full potential of these advanced components. As technology continues to evolve, high-frequency high-current inductors will remain a cornerstone of innovation, driving the future of Japanese manufacturing towards greater heights of excellence and sustainability.
資料ダウンロード
QCD調達購買管理クラウド「newji」は、調達購買部門で必要なQCD管理全てを備えた、現場特化型兼クラウド型の今世紀最高の購買管理システムとなります。
ユーザー登録
調達購買業務の効率化だけでなく、システムを導入することで、コスト削減や製品・資材のステータス可視化のほか、属人化していた購買情報の共有化による内部不正防止や統制にも役立ちます。
NEWJI DX
製造業に特化したデジタルトランスフォーメーション(DX)の実現を目指す請負開発型のコンサルティングサービスです。AI、iPaaS、および先端の技術を駆使して、製造プロセスの効率化、業務効率化、チームワーク強化、コスト削減、品質向上を実現します。このサービスは、製造業の課題を深く理解し、それに対する最適なデジタルソリューションを提供することで、企業が持続的な成長とイノベーションを達成できるようサポートします。
オンライン講座
製造業、主に購買・調達部門にお勤めの方々に向けた情報を配信しております。
新任の方やベテランの方、管理職を対象とした幅広いコンテンツをご用意しております。
お問い合わせ
コストダウンが利益に直結する術だと理解していても、なかなか前に進めることができない状況。そんな時は、newjiのコストダウン自動化機能で大きく利益貢献しよう!
(Β版非公開)