- お役立ち記事
- The Art of Accounting to Optimize Profits by Allocating Manufacturing Expenses Appropriately
The Art of Accounting to Optimize Profits by Allocating Manufacturing Expenses Appropriately
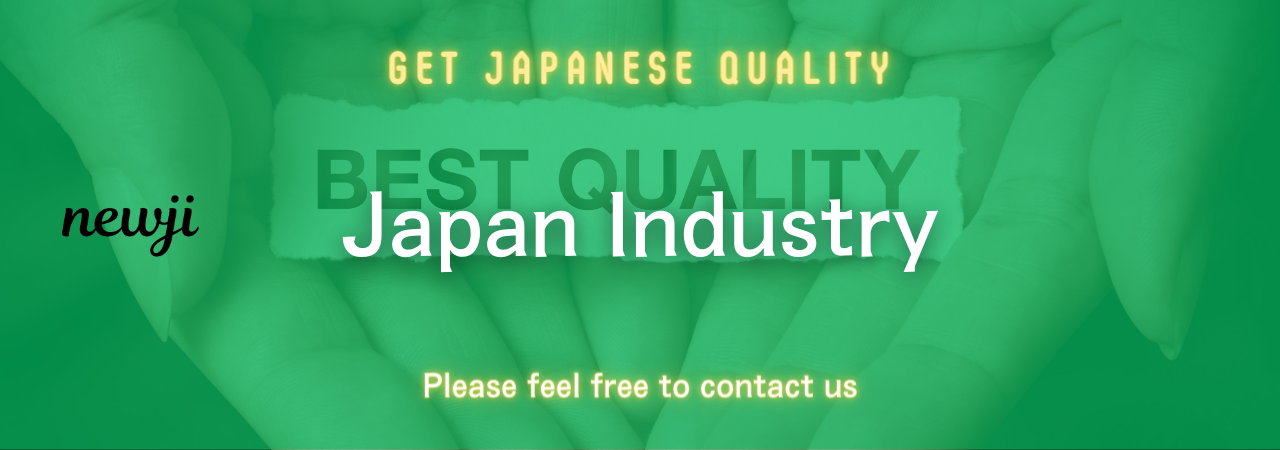
When it comes to running a business, especially one that involves manufacturing, understanding how to allocate manufacturing expenses appropriately can play a significant role in optimizing profits. Mastering the art of accounting isn’t just for accountants; it’s for anyone who wants to see their business flourish.
Many business owners focus heavily on revenue generation and marketing strategies, often overlooking the importance of meticulous expense allocation. However, without proper attention to how your manufacturing costs are allocated, it’s easy to encounter financial inefficiencies. These inefficiencies can lead to lower profit margins and potential mismanagement of resources.
目次
Understanding Manufacturing Expenses
Manufacturing expenses encompass all costs related to producing goods. These costs generally fall into three categories: direct materials, direct labor, and manufacturing overhead.
1. Direct Materials: These are the raw materials that are directly used in creating the product. For instance, if you manufacture chairs, wood and screws would be considered direct materials.
2. Direct Labor: This includes the wages of employees who are directly involved in the manufacturing process. The time spent by workers assembling a chair, for example, would be considered direct labor.
3. Manufacturing Overhead: This is a bit more complex and includes all other indirect costs. This can range from factory rent and utility bills to the depreciation of manufacturing equipment.
Importance of Appropriately Allocating Manufacturing Expenses
Proper allocation of manufacturing expenses is crucial for a variety of reasons:
– Accurate Costing: Knowing the exact cost of manufacturing each product helps in setting an appropriate selling price. Undervalued pricing can lead to losses, while overvalued pricing can drive away customers.
– Effective Budgeting: By accurately tracking where money is spent, businesses can create more precise budgets. This helps in forecasting expenses and avoiding unexpected financial pitfalls.
– Profit Optimization: Efficiently allocated expenses enhance profit margins. When resources are used wisely, more capital is conserved and utilized for growth opportunities or reinvestment into the business.
Steps for Effective Allocation of Manufacturing Expenses
1. Classify Your Costs Accurately
Begin by categorizing your manufacturing expenses into direct materials, direct labor, and manufacturing overhead. This clear demarcation is fundamental for precise accounting and budgeting. Use accounting software to automate this process, ensuring fewer errors and greater ease of access to financial data.
2. Measure Direct Costs in Real-Time
Utilize time-tracking software and inventory management systems to record direct labor hours and material usage as they occur. Real-time tracking allows for immediate adjustments, if necessary, and provides up-to-date cost data for decision-making.
3. Allocate Overhead Costs Wisely
Manufacturing overhead can be tricky to allocate since these costs are not linked directly to a specific product. One effective method involves using Activity-Based Costing (ABC). ABC assigns overhead costs to products based on their use of activities, such as machine hours or labor hours, providing a more accurate cost per product.
Leveraging Technology for Efficiency
Implementing advanced technologies can significantly aid in the proper allocation of manufacturing expenses. Below are some tools and methods:
– ERP Systems: Enterprise Resource Planning systems integrate all facets of your business, including manufacturing, supply chain, and financial management. ERP systems help in comprehensive tracking and allocation of expenses, improving your overall financial management.
– Accounting Software: Modern accounting software comes equipped with modules designed specifically for manufacturing. These tools often include features like cost tracking, financial reporting, and budget forecasting.
– AI-Driven Analytics: Artificial Intelligence can help predict trends and suggest cost-cutting measures. AI-driven analytics analyze patterns and provide insights into areas where you can reduce expenses or reallocate resources more efficiently.
Regular Financial Audits
Conducting regular financial audits helps ensure that your expense allocation remains accurate and up-to-date. Financial audits can uncover discrepancies, inefficiencies, and potential areas for cost savings. This systematic review allows you to adjust strategies promptly and maintain financial health.
Benefits of Proper Allocation in Decision Making
1. Product Pricing: By understanding the exact cost of manufacturing, businesses can set competitive yet profitable prices. This balance between affordability for the customer and profitability for the business is critical for long-term success.
2. Performance Evaluation: Proper cost allocation helps in evaluating the performance of different departments within the manufacturing process. Identifying which areas are underperforming allows for targeted improvements.
3. Investment and Growth: With clear visibility on manufacturing costs, businesses can make informed decisions about reinvestments, expansions, or pivots. Knowing your financial standing opens up avenues for growth and scaling.
Conclusion
Optimal profit isn’t just a result of high sales; it’s intricately tied to how well a business manages and allocates its manufacturing expenses. By understanding and implementing strategies for accurate expense allocation, business owners can significantly improve their profit margins and overall financial health.
From categorizing costs accurately to leveraging advanced technology and conducting regular audits, each step in the allocation process matters. Mastering this aspect of accounting ultimately helps in setting appropriate prices, budgeting effectively, and making well-informed decisions for growth.
In the competitive world of manufacturing, being diligent about your expenses isn’t just good practice—it’s essential for sustaining and optimizing profitability. Start refining your allocation practices today and witness the transformative impact on your bottom line.
資料ダウンロード
QCD調達購買管理クラウド「newji」は、調達購買部門で必要なQCD管理全てを備えた、現場特化型兼クラウド型の今世紀最高の購買管理システムとなります。
ユーザー登録
調達購買業務の効率化だけでなく、システムを導入することで、コスト削減や製品・資材のステータス可視化のほか、属人化していた購買情報の共有化による内部不正防止や統制にも役立ちます。
NEWJI DX
製造業に特化したデジタルトランスフォーメーション(DX)の実現を目指す請負開発型のコンサルティングサービスです。AI、iPaaS、および先端の技術を駆使して、製造プロセスの効率化、業務効率化、チームワーク強化、コスト削減、品質向上を実現します。このサービスは、製造業の課題を深く理解し、それに対する最適なデジタルソリューションを提供することで、企業が持続的な成長とイノベーションを達成できるようサポートします。
オンライン講座
製造業、主に購買・調達部門にお勤めの方々に向けた情報を配信しております。
新任の方やベテランの方、管理職を対象とした幅広いコンテンツをご用意しております。
お問い合わせ
コストダウンが利益に直結する術だと理解していても、なかなか前に進めることができない状況。そんな時は、newjiのコストダウン自動化機能で大きく利益貢献しよう!
(Β版非公開)