- お役立ち記事
- Unlocking Efficiency: The Rise of Batch Processing in Japanese Manufacturing
月間77,185名の
製造業ご担当者様が閲覧しています*
*2025年2月28日現在のGoogle Analyticsのデータより
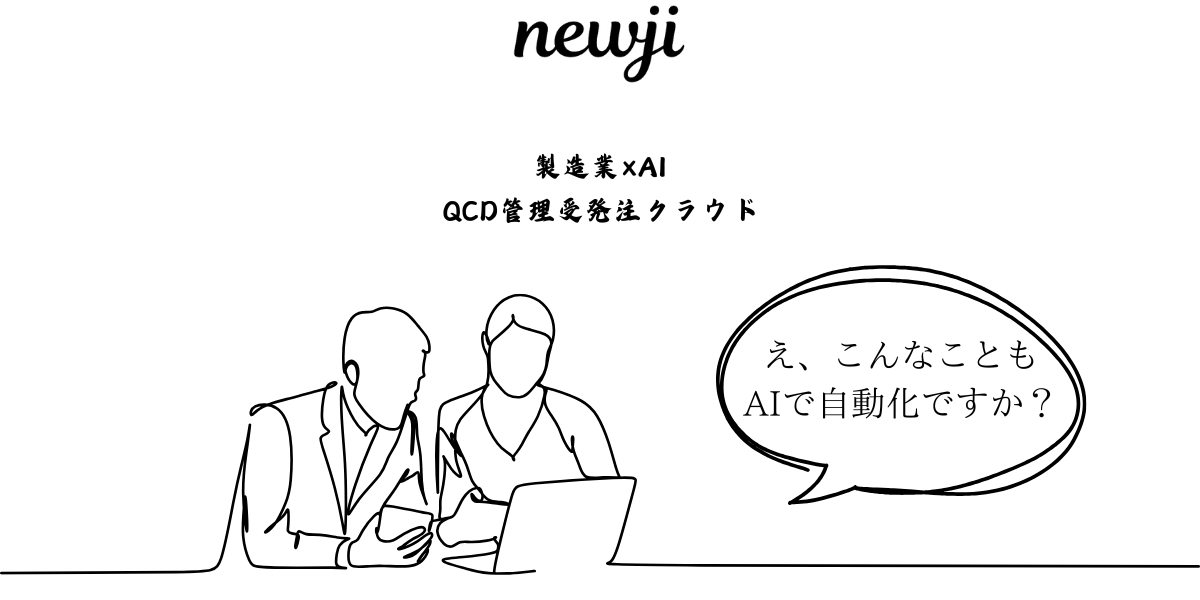
Unlocking Efficiency: The Rise of Batch Processing in Japanese Manufacturing
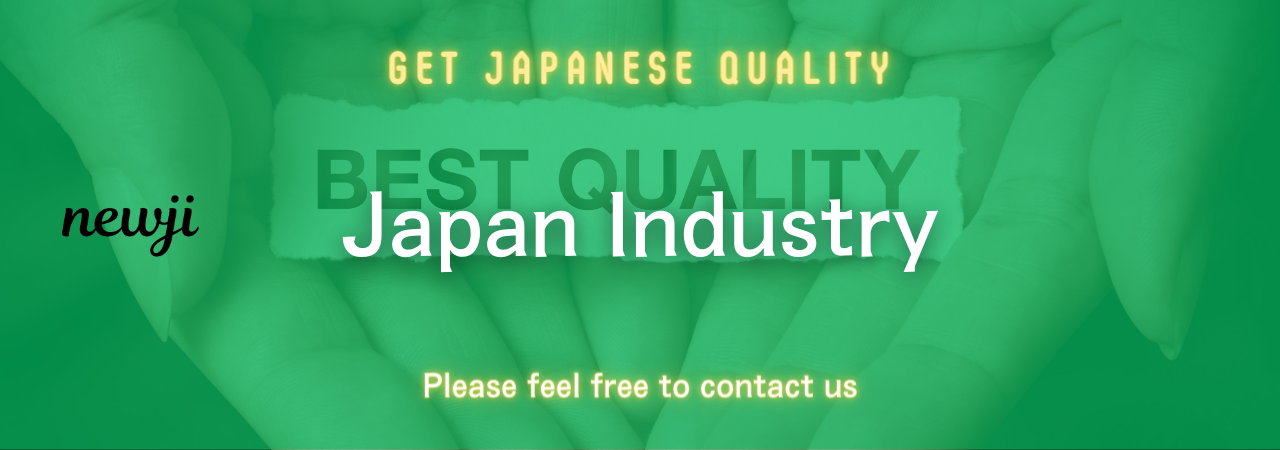
目次
Introduction to Batch Processing in Japanese Manufacturing
Batch processing has become a cornerstone of modern Japanese manufacturing, driving efficiency and excellence across various industries. This method involves producing goods in large quantities within specific timeframes, allowing manufacturers to optimize production schedules and resource allocation. The rise of batch processing in Japan is a testament to the country’s commitment to innovation, quality, and continuous improvement. This article delves into the intricacies of batch processing, exploring its advantages and disadvantages, the role of procurement and purchasing, supplier negotiation techniques, market conditions, and best practices from the perspective of experienced procurement and purchasing professionals.
The Evolution of Batch Processing in Japan
Japanese manufacturing has long been synonymous with quality and reliability. The evolution of batch processing in Japan can be traced back to post-war industrialization, where the need for efficient production methods became paramount. Over the decades, Japanese manufacturers have refined batch processing techniques, integrating advanced technologies and lean manufacturing principles to enhance productivity and reduce waste.
Historical Context
In the aftermath of World War II, Japan faced significant economic challenges. The government and industry leaders focused on rebuilding the economy through manufacturing, leading to the adoption of efficient production methods. Batch processing emerged as a viable solution, allowing manufacturers to meet growing demand while maintaining high standards of quality.
Integration with Lean Manufacturing
The integration of batch processing with lean manufacturing practices has been pivotal in Japanese manufacturing success. Lean principles emphasize waste reduction, continuous improvement, and value creation, all of which align seamlessly with the objectives of batch processing. This synergy has enabled Japanese manufacturers to achieve remarkable levels of efficiency and competitiveness in the global market.
Advantages of Batch Processing
Batch processing offers numerous benefits that contribute to the overall efficiency and effectiveness of manufacturing operations. Understanding these advantages is crucial for procurement and purchasing professionals aiming to optimize their supply chains and production processes.
Operational Efficiency
One of the primary advantages of batch processing is enhanced operational efficiency. By producing goods in large batches, manufacturers can streamline production schedules, reduce setup times, and minimize downtime. This leads to increased output and faster turnaround times, allowing companies to meet market demand more effectively.
Cost Reduction
Batch processing can significantly reduce manufacturing costs. Producing in bulk allows for economies of scale, where the cost per unit decreases as production volume increases. Additionally, bulk purchasing of raw materials and components often leads to discounts, further lowering overall production costs.
Quality Control
Maintaining consistent quality is essential in manufacturing, and batch processing facilitates this. By producing goods in controlled batches, manufacturers can implement rigorous quality checks at each stage of production. This ensures that defects are identified and addressed promptly, resulting in high-quality products that meet or exceed customer expectations.
Inventory Management
Effective inventory management is another advantage of batch processing. Producing in batches allows for better forecasting and planning, reducing the likelihood of overproduction or stockouts. This balance between supply and demand minimizes holding costs and enhances cash flow management.
Disadvantages of Batch Processing
While batch processing offers significant benefits, it also presents certain challenges that manufacturers must address to ensure optimal performance.
Flexibility Limitations
Batch processing can limit flexibility in production. Switching between different product batches may require changes in setup and configuration, leading to potential delays. This can be particularly challenging in industries where demand fluctuates or where customization is essential.
Higher Initial Investment
Implementing batch processing systems often requires substantial initial investment in equipment, technology, and training. Smaller manufacturers or those with limited resources may find it challenging to bear these upfront costs, potentially hindering their ability to adopt batch processing methods.
Storage Requirements
Producing large batches necessitates adequate storage facilities for raw materials, in-process inventory, and finished goods. Ensuring sufficient storage space can be a logistical challenge, especially in environments with limited physical infrastructure.
Impact on Lead Times
Batch processing can sometimes lead to longer lead times, particularly if production cycles are not well-coordinated. Delays in one stage of the batch process can cascade, affecting the overall production timeline and potentially impacting customer delivery schedules.
Procurement and Purchasing in Batch Processing
Effective procurement and purchasing strategies are critical to the success of batch processing in Japanese manufacturing. These functions ensure the timely acquisition of high-quality materials and components, supporting seamless production operations.
Supplier Selection and Management
Selecting the right suppliers is foundational to successful batch processing. Procurement professionals must evaluate suppliers based on their ability to deliver consistent quality, reliability, and scalability. Building strong relationships with suppliers fosters collaboration and ensures that materials meet the stringent standards required for batch production.
Bulk Purchasing Advantages
Bulk purchasing is inherent to batch processing, offering several benefits. By buying large quantities, manufacturers can negotiate better pricing, secure timely deliveries, and reduce the frequency of ordering. This not only lowers costs but also enhances supply chain stability, mitigating risks associated with material shortages.
Inventory Optimization
Optimizing inventory levels is essential in batch processing to prevent excess stock or shortages. Procurement and purchasing teams must work closely with production planners to align material orders with production schedules. Advanced inventory management systems and demand forecasting tools can aid in maintaining the right balance between supply and demand.
Quality Assurance
Ensuring the quality of procured materials is paramount in batch processing. Procurement professionals must implement stringent quality assurance protocols, including supplier audits, material testing, and compliance checks. High-quality inputs are crucial for maintaining the integrity of the batch process and producing superior end products.
Supplier Negotiation Techniques
Negotiating effectively with suppliers is a vital skill for procurement and purchasing professionals in Japanese manufacturing. Successful negotiations can lead to favorable terms, cost savings, and long-term partnerships.
Building Strong Relationships
In Japanese business culture, relationships are highly valued. Establishing trust and mutual respect with suppliers is fundamental to successful negotiations. Building strong relationships fosters collaboration, facilitates open communication, and paves the way for more favorable negotiation outcomes.
Leveraging Volume for Better Terms
Batch processing involves large order volumes, providing significant leverage during negotiations. Procurement professionals can use their purchasing power to negotiate better pricing, extended payment terms, and additional services. Emphasizing the long-term partnership potential can also encourage suppliers to offer more competitive terms.
Understanding Supplier Constraints
Effective negotiators understand the constraints and challenges faced by their suppliers. By gaining insights into suppliers’ cost structures, production capabilities, and market conditions, procurement professionals can propose solutions that address mutual interests, leading to win-win agreements.
Utilizing Data and Analytics
Data-driven negotiations are more effective and strategic. Using analytics to assess supplier performance, market trends, and cost structures empowers procurement teams to make informed decisions. Presenting data-backed arguments during negotiations enhances credibility and strengthens bargaining positions.
Market Conditions Affecting Batch Processing
The success of batch processing in Japanese manufacturing is influenced by various market conditions. Understanding these factors is crucial for procurement and purchasing professionals to navigate challenges and capitalize on opportunities.
Global Supply Chain Dynamics
Global supply chains are subject to fluctuations due to geopolitical events, trade policies, and economic shifts. Japanese manufacturers must stay abreast of these dynamics to anticipate disruptions and adjust their batch processing strategies accordingly. Diversifying supplier bases and building resilient supply chains can mitigate risks associated with global uncertainties.
Technological Advancements
Rapid technological advancements continuously reshape manufacturing landscapes. The integration of automation, AI, and IoT in batch processing enhances efficiency and data visibility. Procurement and purchasing teams must stay informed about emerging technologies to leverage their benefits and maintain competitive advantage.
Environmental Regulations
Environmental sustainability is increasingly important in manufacturing. Compliance with environmental regulations requires manufacturers to adopt eco-friendly practices within batch processing. Procurement professionals play a role in sourcing sustainable materials and ensuring that suppliers adhere to environmental standards, thereby supporting the company’s sustainability goals.
Consumer Demand Trends
Shifting consumer preferences and demand trends impact batch processing strategies. Manufacturers must align their production batches with market demand to avoid overproduction or shortages. Agile procurement and purchasing practices that respond swiftly to changing consumer needs are essential for maintaining market relevance.
Best Practices in Batch Processing
Implementing best practices in batch processing enhances efficiency, quality, and overall manufacturing performance. Drawing from extensive field experience, the following best practices are recommended for Japanese manufacturers.
Lean Batch Production
Integrating lean principles with batch processing minimizes waste and optimizes resource utilization. Practices such as just-in-time (JIT) inventory, continuous improvement (Kaizen), and value stream mapping streamline production processes, reducing costs and enhancing productivity.
Advanced Planning and Scheduling
Effective planning and scheduling are critical for successful batch processing. Utilizing advanced planning systems and software enables manufacturers to coordinate production batches, manage resource allocation, and optimize production timelines. This leads to improved efficiency and timely delivery of products.
Automation and Technology Integration
Incorporating automation and advanced technologies into batch processing systems boosts efficiency and accuracy. Automated machinery, robotics, and AI-driven analytics enhance production capabilities, reduce human error, and facilitate real-time monitoring and control of manufacturing processes.
Quality Management Systems
Robust quality management systems (QMS) are essential for maintaining high standards in batch processing. Implementing comprehensive QMS protocols ensures consistent quality control, defect tracking, and continuous improvement. This results in reliable and superior products that meet customer expectations.
Training and Development
Investing in the training and development of staff is crucial for the successful implementation of batch processing. Skilled and knowledgeable employees can operate advanced machinery, adhere to quality standards, and contribute to continuous improvement initiatives. Ongoing training programs foster a culture of excellence and innovation.
Case Studies: Success Stories in Japanese Batch Processing
Examining real-world examples of successful batch processing implementation in Japanese manufacturing provides valuable insights and practical lessons for procurement and purchasing professionals.
Automotive Industry
Japanese automotive manufacturers excel in batch processing, producing vehicles in large quantities while maintaining high quality standards. By integrating advanced robotics, automation, and lean manufacturing principles, companies like Toyota and Honda achieve remarkable efficiency and reliability, meeting global demand effectively.
Electronics Manufacturing
In the electronics sector, Japanese manufacturers leverage batch processing to produce components and devices at scale. Companies such as Sony and Panasonic utilize sophisticated supply chain management and quality control systems to ensure consistency and innovation in their product lines.
Pharmaceutical Production
Japanese pharmaceutical companies implement batch processing to produce medications and medical devices. Strict regulatory compliance, rigorous quality assurance protocols, and efficient production scheduling enable these companies to meet healthcare demands while ensuring product safety and efficacy.
Challenges and Solutions in Batch Processing
Despite its advantages, batch processing presents challenges that manufacturers must address to maintain efficiency and competitiveness. Identifying and implementing effective solutions is essential for overcoming these obstacles.
Managing Production Variability
Batch processing can be susceptible to variability in production processes, leading to inconsistencies in output quality. Implementing standardized procedures, continuous monitoring, and real-time adjustments can mitigate variability and enhance reliability.
Balancing Batch Size and Flexibility
Determining the optimal batch size requires balancing efficiency with flexibility. Large batches optimize costs but reduce responsiveness to market changes. Adopting mixed-model batch processing or flexible manufacturing systems can provide the necessary adaptability without compromising efficiency.
Mitigating Supplier Risks
Reliance on suppliers poses inherent risks, including delays, quality issues, and supply interruptions. Diversifying the supplier base, establishing contingency plans, and fostering strong supplier relationships can minimize these risks and ensure a stable supply chain.
Addressing Environmental and Regulatory Compliance
Compliance with environmental and regulatory standards is non-negotiable in manufacturing. Implementing sustainable practices, investing in eco-friendly technologies, and staying informed about regulatory changes ensure that batch processing operations remain compliant and environmentally responsible.
The Future of Batch Processing in Japanese Manufacturing
The future of batch processing in Japanese manufacturing is poised for continued growth and evolution, driven by technological advancements and changing market dynamics. Embracing innovation and adaptability will be key to sustaining efficiency and competitiveness.
Integration of Industry 4.0
Industry 4.0 technologies, including the Internet of Things (IoT), artificial intelligence (AI), and big data analytics, are set to revolutionize batch processing. These technologies enable real-time monitoring, predictive maintenance, and data-driven decision-making, enhancing overall production efficiency and flexibility.
Sustainable Manufacturing Practices
Sustainability will remain a critical focus, influencing batch processing strategies. Japanese manufacturers will increasingly adopt green manufacturing practices, such as energy-efficient processes, waste reduction, and the use of renewable materials, aligning with global sustainability goals and consumer expectations.
Customization and Personalization
The trend towards customization and personalization poses new challenges for batch processing. Manufacturers will need to develop flexible batch processing systems that can accommodate varying product specifications without compromising efficiency, meeting the diverse needs of modern consumers.
Global Collaboration and Innovation
Global collaboration and innovation will drive the future of batch processing in Japan. Partnerships with international suppliers, research institutions, and technology providers will foster the exchange of knowledge and advancements, enhancing the capability to innovate and adapt to emerging trends.
Conclusion
Batch processing has emerged as a vital strategy in Japanese manufacturing, underpinning the country’s reputation for efficiency, quality, and innovation. By leveraging the advantages of batch processing—such as operational efficiency, cost reduction, and quality control—while addressing its challenges through effective procurement, supplier management, and technological integration, Japanese manufacturers continue to excel in the global marketplace. As the industry evolves, embracing advanced technologies, sustainable practices, and flexible production methods will be essential for maintaining competitiveness and meeting the dynamic demands of the future. Procurement and purchasing professionals play a crucial role in this ecosystem, ensuring the seamless acquisition of quality materials, fostering strong supplier relationships, and implementing best practices that drive continuous improvement and excellence in batch processing.
資料ダウンロード
QCD管理受発注クラウド「newji」は、受発注部門で必要なQCD管理全てを備えた、現場特化型兼クラウド型の今世紀最高の受発注管理システムとなります。
ユーザー登録
受発注業務の効率化だけでなく、システムを導入することで、コスト削減や製品・資材のステータス可視化のほか、属人化していた受発注情報の共有化による内部不正防止や統制にも役立ちます。
NEWJI DX
製造業に特化したデジタルトランスフォーメーション(DX)の実現を目指す請負開発型のコンサルティングサービスです。AI、iPaaS、および先端の技術を駆使して、製造プロセスの効率化、業務効率化、チームワーク強化、コスト削減、品質向上を実現します。このサービスは、製造業の課題を深く理解し、それに対する最適なデジタルソリューションを提供することで、企業が持続的な成長とイノベーションを達成できるようサポートします。
製造業ニュース解説
製造業、主に購買・調達部門にお勤めの方々に向けた情報を配信しております。
新任の方やベテランの方、管理職を対象とした幅広いコンテンツをご用意しております。
お問い合わせ
コストダウンが利益に直結する術だと理解していても、なかなか前に進めることができない状況。そんな時は、newjiのコストダウン自動化機能で大きく利益貢献しよう!
(β版非公開)