- お役立ち記事
- | Precision, Reliability, and Innovation: The Pillars of Japanese Manufacturing
| Precision, Reliability, and Innovation: The Pillars of Japanese Manufacturing
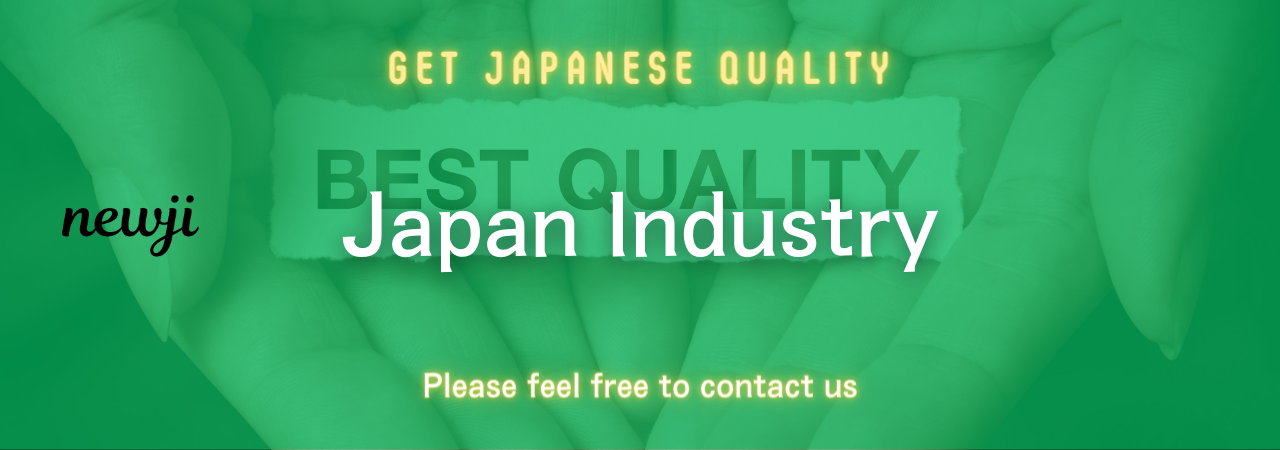
Japanese manufacturing has a long-standing reputation for excellence, driven by the three fundamental principles of precision, reliability, and innovation. These principles have shaped the industry, allowing Japanese companies to consistently deliver cutting-edge products and maintain a competitive edge in the global market. From automobiles to electronics, the meticulous attention to detail and commitment to quality exemplified by Japanese manufacturers have set a high standard that others strive to emulate.
目次
Precision: The Foundation of Excellence
Precision is at the heart of Japanese manufacturing. This focus on exactness ensures that every component, no matter how small, is meticulously crafted to meet stringent specifications. Companies like Toyota and Sony have become synonymous with precision manufacturing, incorporating advanced techniques such as Lean Manufacturing and Six Sigma to minimize variability and enhance product quality.
Lean Manufacturing, a methodology pioneered by Toyota, emphasizes the elimination of waste and the continuous improvement of processes. By streamlining production and eliminating inefficiencies, Japanese manufacturers can produce high-quality products with remarkable consistency. Similarly, Six Sigma, a data-driven approach aimed at reducing defects and improving process capability, has become integral to maintaining the precision of Japanese manufacturing.
The commitment to precision extends beyond processes to the workforce. Japanese companies invest heavily in training and workforce development, ensuring that employees possess the skills necessary to maintain high standards. This focus on human capital further reinforces the culture of precision that defines Japanese manufacturing.
Reliability: Building Trust and Reputation
Reliability is another cornerstone of Japanese manufacturing, rooted in the nation’s dedication to producing long-lasting and dependable products. This principle is evident in the automotive industry, where brands like Honda and Subaru are celebrated for their vehicles’ longevity and performance. The emphasis on reliability is not just about meeting consumer expectations but also about building trust and maintaining a strong reputation.
Japanese manufacturers achieve reliability through rigorous quality control measures and robust testing protocols. Before reaching the market, products undergo extensive testing to ensure they meet the highest standards of durability and performance. This proactive approach to quality management helps identify and address potential issues before they impact the customer, leading to fewer recalls and greater customer satisfaction.
Additionally, the concept of Kaizen, or continuous improvement, plays a vital role in maintaining reliability. By fostering a culture of ongoing enhancement, Japanese companies are able to innovate and refine their processes continually. This commitment to improvement helps ensure that the reliability of their products remains unparalleled.
Innovation: Driving Progress and Industry Leadership
Innovation is the driving force behind the continued success and evolution of Japanese manufacturing. The ability to develop and implement new technologies, processes, and products has enabled Japanese companies to stay at the forefront of various industries. Whether it’s advancements in robotics, automotive engineering, or consumer electronics, Japanese manufacturers are consistently pushing the boundaries of what is possible.
The pursuit of innovation is deeply embedded in the corporate culture of many Japanese companies. Research and development (R&D) are prioritized, with significant investments made to explore new ideas and technologies. This dedication to R&D has resulted in groundbreaking products like the hybrid car, pioneered by Toyota with the introduction of the Prius, and Sony’s development of revolutionary consumer electronics, such as the Walkman and PlayStation.
Collaborative efforts between companies and academic institutions also fuel innovation. By partnering with universities and research organizations, Japanese manufacturers can access a broader pool of knowledge and expertise, enabling them to pioneer new advancements. This collaborative approach fosters an environment where innovative ideas can flourish and be brought to market more effectively.
Embracing Sustainability: A New Focus for Japanese Manufacturing
In recent years, sustainability has become an increasingly important aspect of Japanese manufacturing. Recognizing the need to address environmental concerns, Japanese companies are integrating sustainable practices into their operations. This shift not only helps reduce the environmental impact but also aligns with global consumer preferences for eco-friendly products.
For example, Toyota’s commitment to sustainability is reflected in its development of hydrogen fuel cell vehicles and its efforts to achieve zero carbon emissions at its manufacturing plants. Similarly, Panasonic is focused on creating energy-efficient products and incorporating renewable energy sources into its manufacturing processes.
Moreover, the Japanese manufacturing industry is embracing the concept of the circular economy, which aims to minimize waste and make the most of resources. Companies are designing products with recyclability in mind and implementing programs to reclaim and repurpose materials. These efforts highlight the industry’s dedication to sustainability and its proactive approach to addressing environmental challenges.
The Future of Japanese Manufacturing
As we look to the future, Japanese manufacturing is poised to continue its legacy of precision, reliability, and innovation. The industry is adapting to the challenges and opportunities presented by the digital age, leveraging technologies such as artificial intelligence (AI), the Internet of Things (IoT), and Industry 4.0 to enhance production capabilities and efficiency.
AI-powered systems are being used to optimize supply chains, improve quality control, and enable predictive maintenance, ensuring that production runs smoothly and efficiently. IoT devices are providing manufacturers with real-time data and insights, allowing for greater control and visibility over the production process. These advancements are helping Japanese manufacturers maintain their competitive edge and meet the evolving demands of the global market.
Furthermore, the industry is likely to see increased collaboration between traditional manufacturers and tech startups. This synergy can drive further innovation and help bring cutting-edge technologies to the forefront of manufacturing. By staying at the intersection of tradition and innovation, Japanese manufacturing will continue to thrive and set new benchmarks for excellence in the years to come.
In conclusion, precision, reliability, and innovation are the pillars that have defined Japanese manufacturing and propelled it to global prominence. These principles guide the industry’s approach to quality, trust, and progress, ensuring that Japanese products remain synonymous with excellence. As the landscape evolves, the commitment to these foundational elements, combined with a focus on sustainability and technological advancement, will ensure that Japanese manufacturing continues to lead the way.
資料ダウンロード
QCD調達購買管理クラウド「newji」は、調達購買部門で必要なQCD管理全てを備えた、現場特化型兼クラウド型の今世紀最高の購買管理システムとなります。
ユーザー登録
調達購買業務の効率化だけでなく、システムを導入することで、コスト削減や製品・資材のステータス可視化のほか、属人化していた購買情報の共有化による内部不正防止や統制にも役立ちます。
NEWJI DX
製造業に特化したデジタルトランスフォーメーション(DX)の実現を目指す請負開発型のコンサルティングサービスです。AI、iPaaS、および先端の技術を駆使して、製造プロセスの効率化、業務効率化、チームワーク強化、コスト削減、品質向上を実現します。このサービスは、製造業の課題を深く理解し、それに対する最適なデジタルソリューションを提供することで、企業が持続的な成長とイノベーションを達成できるようサポートします。
オンライン講座
製造業、主に購買・調達部門にお勤めの方々に向けた情報を配信しております。
新任の方やベテランの方、管理職を対象とした幅広いコンテンツをご用意しております。
お問い合わせ
コストダウンが利益に直結する術だと理解していても、なかなか前に進めることができない状況。そんな時は、newjiのコストダウン自動化機能で大きく利益貢献しよう!
(Β版非公開)