- お役立ち記事
- [For home appliance ODM] How to provide consistent support from prototyping, evaluation, and cost estimation
月間77,185名の
製造業ご担当者様が閲覧しています*
*2025年2月28日現在のGoogle Analyticsのデータより
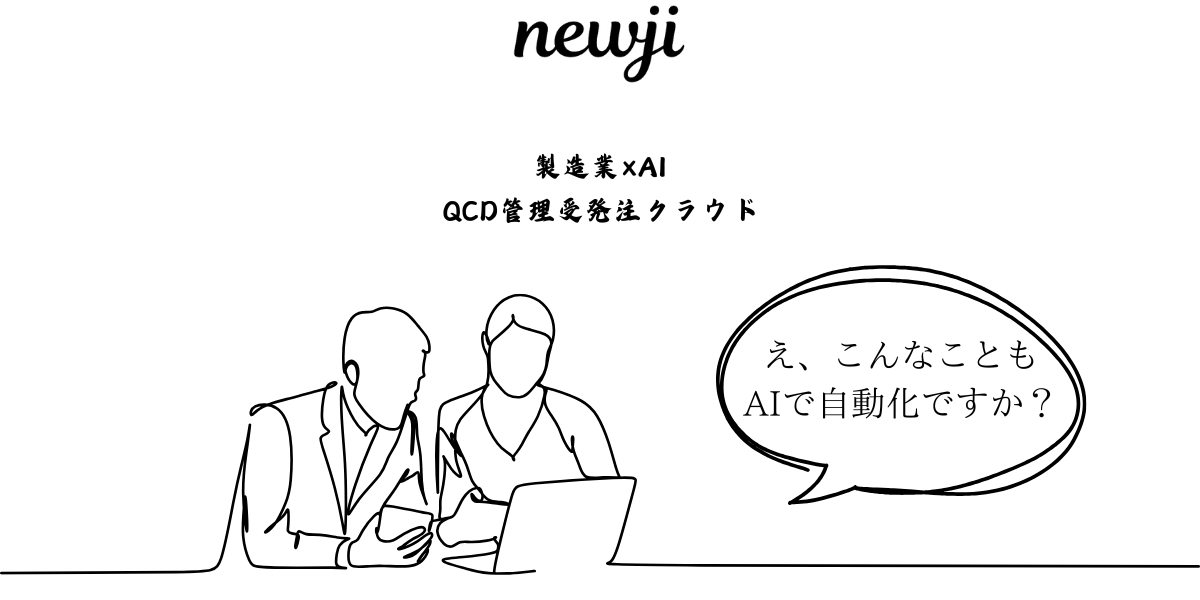
[For home appliance ODM] How to provide consistent support from prototyping, evaluation, and cost estimation
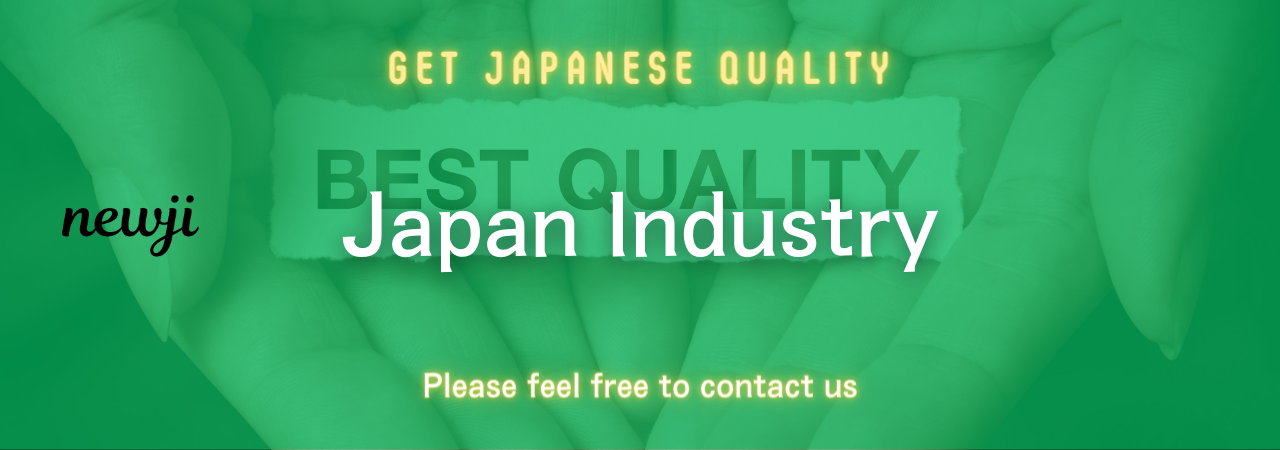
目次
Understanding ODM in Home Appliances
When it comes to home appliance manufacturing, the Original Design Manufacturer (ODM) model offers significant advantages.
An ODM is a company that designs and manufactures products as specified, which are then sold under another company’s brand.
This approach allows businesses to put their branding on high-quality products without the need to handle the engineering or manufacturing process themselves.
The scope of services provided by an ODM extends far beyond simple manufacturing.
A reputable ODM offers assistance at every stage of product development—from ideation to delivery.
This includes prototyping, evaluation, and cost estimation.
Each stage is crucial for ensuring the final product aligns with market demands and brand standards.
Prototyping: The First Step
Prototyping is an essential first step in any product development process.
In the context of home appliances, this stage involves creating a working model of the proposed product.
This prototype is used to validate design concepts, functionality, and overall performance.
For an ODM, offering prototyping services means working closely with clients to turn their ideas into tangible models.
This collaborative process often involves multiple rounds of iterations and adjustments.
The goal is to address any potential design flaws early and refine the features to meet customer needs.
During prototyping, an accomplished ODM will employ advanced technologies such as 3D printing or CNC machining.
These techniques help in producing accurate and functional prototypes quickly and efficiently.
By utilizing cutting-edge technology, an ODM can help ensure that the final product will be as close to the design intent as possible.
Evaluation: Testing and Enhancing
Following the successful creation of a prototype, the next stage is thorough evaluation.
This phase is critical as it involves testing the prototype under real-world conditions to assess its performance, safety, and reliability.
An ODM will conduct a range of tests tailored to the specific home appliance.
These may include electrical safety tests, performance evaluations, stress tests, and environmental impact assessments.
Each test aims to identify potential risks or areas for improvement.
Evaluation doesn’t end with testing.
An ODM will gather all relevant data and feedback from these tests to refine the product further.
This might involve making changes to design, materials, or components based on the findings.
This iterative process ensures that the final product not only meets compliance standards but also exceeds customer expectations in quality and functionality.
Cost Estimation: Planning for Success
Accurate cost estimation is a vital aspect of product development.
It involves forecasting the total expenses involved in producing a home appliance, from raw materials to final delivery.
A reliable cost estimation ensures the project stays within budget and aligns with financial goals.
An ODM with expertise in cost estimation can offer detailed insights into each component of the manufacturing process.
This includes analyzing material costs, labor expenses, product lifecycle costs, and even logistics.
By providing a comprehensive breakdown of these factors, an ODM helps clients make informed decisions about pricing, market positioning, and profitability.
Furthermore, ODMs often have established relationships with suppliers, which can result in cost savings on materials.
This advantage, combined with in-depth market knowledge, enables ODMs to provide competitive pricing without sacrificing quality.
Consistent Support Across All Stages
What sets a leading ODM apart is the ability to offer consistent support across all stages of the manufacturing process, from prototyping to delivery.
This holistic approach ensures coherence and alignment throughout the project.
A dedicated project manager will typically oversee every phase, acting as the main point of contact between the client and the ODM team.
This ensures clear communication, quick resolution of any issues, and keeping the project on track.
Supporting clients consistently means adapting to evolving needs and expectations.
A flexible ODM can adjust production timelines, accommodate design changes, and respond swiftly to market trends.
By maintaining open communication and a customer-centric focus, an ODM can tailor its services to match the specific objectives of each project.
The Benefits of Choosing the Right ODM
Partnering with the right ODM presents several advantages for home appliance brands.
First, it allows companies to focus on their core competencies, such as marketing and sales, while the ODM handles the complexities of production.
Additionally, collaborating with an experienced ODM provides access to a wealth of industry knowledge and expertise.
This can lead to innovative solutions and enhancements that may not have been possible otherwise.
Finally, by leveraging the ODM’s existing infrastructure and supplier networks, companies can significantly reduce time-to-market.
This competitive edge is crucial in the fast-paced home appliance industry, where quick adaptation to consumer demands can dictate market success.
Conclusion
Navigating the path from concept to completion in home appliance manufacturing requires expertise, precision, and reliable partnerships.
An ODM that provides consistent support through prototyping, evaluation, and cost estimation is invaluable in this journey.
By choosing the right ODM partner, home appliance brands can ensure their products are not only built to high standards but also effectively positioned in the market.
Ultimately, this collaboration leads to innovative, efficient, and successful product launches that resonate with consumers and drive brand success.
資料ダウンロード
QCD管理受発注クラウド「newji」は、受発注部門で必要なQCD管理全てを備えた、現場特化型兼クラウド型の今世紀最高の受発注管理システムとなります。
ユーザー登録
受発注業務の効率化だけでなく、システムを導入することで、コスト削減や製品・資材のステータス可視化のほか、属人化していた受発注情報の共有化による内部不正防止や統制にも役立ちます。
NEWJI DX
製造業に特化したデジタルトランスフォーメーション(DX)の実現を目指す請負開発型のコンサルティングサービスです。AI、iPaaS、および先端の技術を駆使して、製造プロセスの効率化、業務効率化、チームワーク強化、コスト削減、品質向上を実現します。このサービスは、製造業の課題を深く理解し、それに対する最適なデジタルソリューションを提供することで、企業が持続的な成長とイノベーションを達成できるようサポートします。
製造業ニュース解説
製造業、主に購買・調達部門にお勤めの方々に向けた情報を配信しております。
新任の方やベテランの方、管理職を対象とした幅広いコンテンツをご用意しております。
お問い合わせ
コストダウンが利益に直結する術だと理解していても、なかなか前に進めることができない状況。そんな時は、newjiのコストダウン自動化機能で大きく利益貢献しよう!
(β版非公開)