- お役立ち記事
- Example of cutting/grinding hybrid prototype of difficult-to-process material Inconel
月間77,185名の
製造業ご担当者様が閲覧しています*
*2025年2月28日現在のGoogle Analyticsのデータより
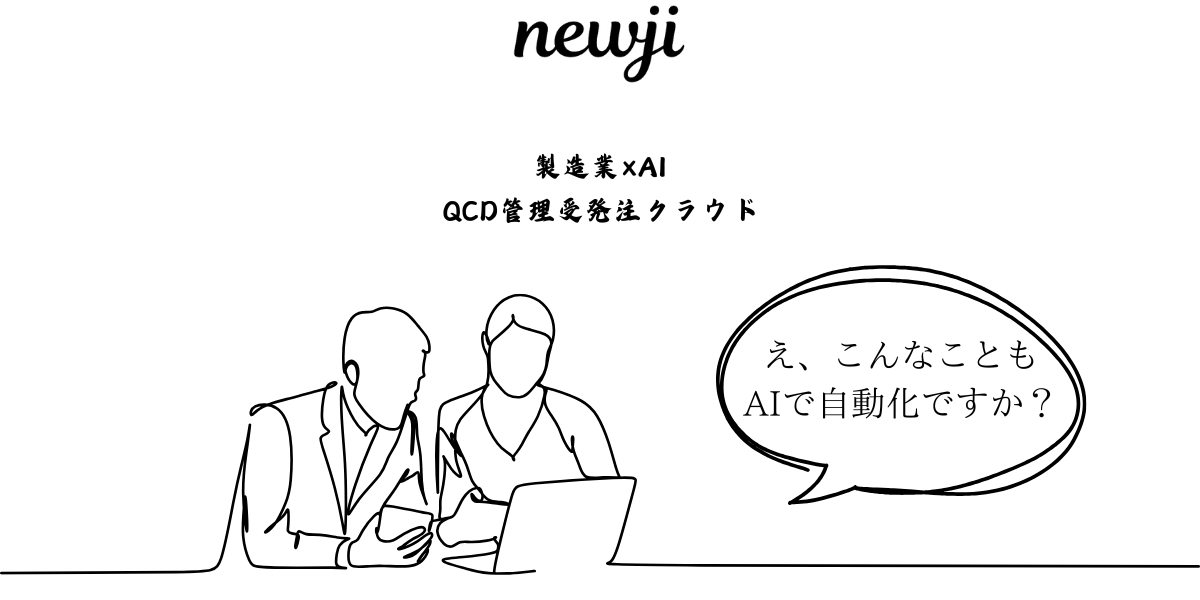
Example of cutting/grinding hybrid prototype of difficult-to-process material Inconel
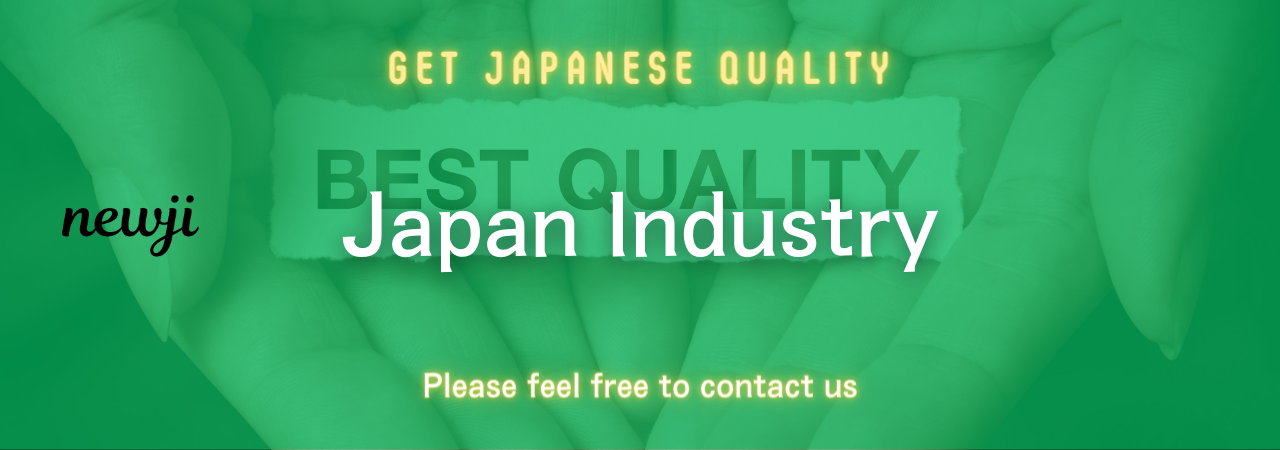
目次
Understanding Inconel: A Challenging Material
Inconel is a family of nickel-chromium-based superalloys known for their ability to withstand extreme environments.
They are highly resistant to oxidation and corrosion, making them ideal for use in harsh conditions.
This includes applications in the aerospace, automotive, and chemical industries.
However, one of the challenges with Inconel is its difficulty in processing due to its toughness and hardness.
The Need for Hybrid Processing Methods
Given the challenges Inconel presents, traditional machining methods often fall short.
Conventional cutting tools can wear out quickly, increasing costs and production time.
Thus, innovative methods like cutting/grinding hybrid techniques have been explored and developed.
These techniques blend the best aspects of cutting and grinding to enhance the efficiency and quality of machining this difficult material.
What is Cutting/Grinding Hybrid Technique?
The cutting/grinding hybrid technique integrates the strengths of cutting tools with the precision of grinding processes.
This method offers a more efficient way to process hard-to-machine materials like Inconel.
In cutting, material is removed using a tool with defined edges.
Grinding, on the other hand, utilizes an abrasive wheel to achieve fine finishes and tight tolerances.
Advantages of the Hybrid Method
Combining cutting and grinding has several benefits over using these methods separately.
Firstly, it extends tool life by reducing wear on both cutting and grinding tools.
This also lowers operational costs and minimizes downtime.
Secondly, the hybrid technique provides higher precision in machining, which is beneficial for applications demanding tight tolerances.
Prototype Development of Hybrid Techniques
To successfully implement the cutting/grinding hybrid technique, developing prototypes is an essential step.
This involves designing machines and processes that can handle the complexities of hybrid operations.
The development phase includes experimenting with different tools, abrasives, and operational parameters.
Optimal conditions must be established to achieve the desired balance between cutting and grinding.
Challenges in Prototype Development
Developing a prototype for a hybrid technique involves addressing several challenges.
One major hurdle is synchronization.
The cutting and grinding processes must work in harmony to attain the necessary material removal rate and surface finish.
Additionally, the equipment must be able to handle the thermal stresses without compromising the integrity of either process.
Case Studies: Implementing Hybrid Techniques with Inconel
Several industrial case studies have demonstrated the effectiveness of cutting/grinding hybrids in machining Inconel.
These real-world applications show improved production rates and surface finishes.
For instance, in aerospace, complicated components with stringent specifications have been successfully manufactured using hybrid techniques.
Companies report reduced tool wear and enhanced product quality, leading to significant cost savings.
Future Prospects of Hybrid Techniques
The success of hybrid techniques in processing Inconel suggests promising applications for other hard-to-machine materials.
Advancements in technology and material science continue to push the boundaries of what these hybrid methods can achieve.
As industries demand more intricate and durable components, the cutting/grinding hybrid approach will likely become even more essential.
Considerations for Adopting Hybrid Techniques
Adopting a cutting/grinding hybrid approach requires careful planning and investment.
Enterprises must evaluate whether the potential benefits outweigh the initial costs.
Also, there is a need for skilled labor capable of operating and maintaining these advanced systems.
Training personnel in both cutting and grinding disciplines is crucial for a successful implementation.
Conclusion: The Path Forward
Inconel’s resilience and durability make it indispensable across many high-stakes industries.
While machining this superalloy presents significant challenges, cutting/grinding hybrid techniques offer a viable solution.
As industries continue to evolve and demand innovative approaches, the development and refinement of these hybrid techniques will be key.
By striking a balance between cutting and grinding, manufacturers can fully harness Inconel’s unique properties while maintaining cost-efficiency and precision.
資料ダウンロード
QCD管理受発注クラウド「newji」は、受発注部門で必要なQCD管理全てを備えた、現場特化型兼クラウド型の今世紀最高の受発注管理システムとなります。
ユーザー登録
受発注業務の効率化だけでなく、システムを導入することで、コスト削減や製品・資材のステータス可視化のほか、属人化していた受発注情報の共有化による内部不正防止や統制にも役立ちます。
NEWJI DX
製造業に特化したデジタルトランスフォーメーション(DX)の実現を目指す請負開発型のコンサルティングサービスです。AI、iPaaS、および先端の技術を駆使して、製造プロセスの効率化、業務効率化、チームワーク強化、コスト削減、品質向上を実現します。このサービスは、製造業の課題を深く理解し、それに対する最適なデジタルソリューションを提供することで、企業が持続的な成長とイノベーションを達成できるようサポートします。
製造業ニュース解説
製造業、主に購買・調達部門にお勤めの方々に向けた情報を配信しております。
新任の方やベテランの方、管理職を対象とした幅広いコンテンツをご用意しております。
お問い合わせ
コストダウンが利益に直結する術だと理解していても、なかなか前に進めることができない状況。そんな時は、newjiのコストダウン自動化機能で大きく利益貢献しよう!
(β版非公開)