- お役立ち記事
- Importance of manufacturing process monitoring and effective implementation methods
Importance of manufacturing process monitoring and effective implementation methods
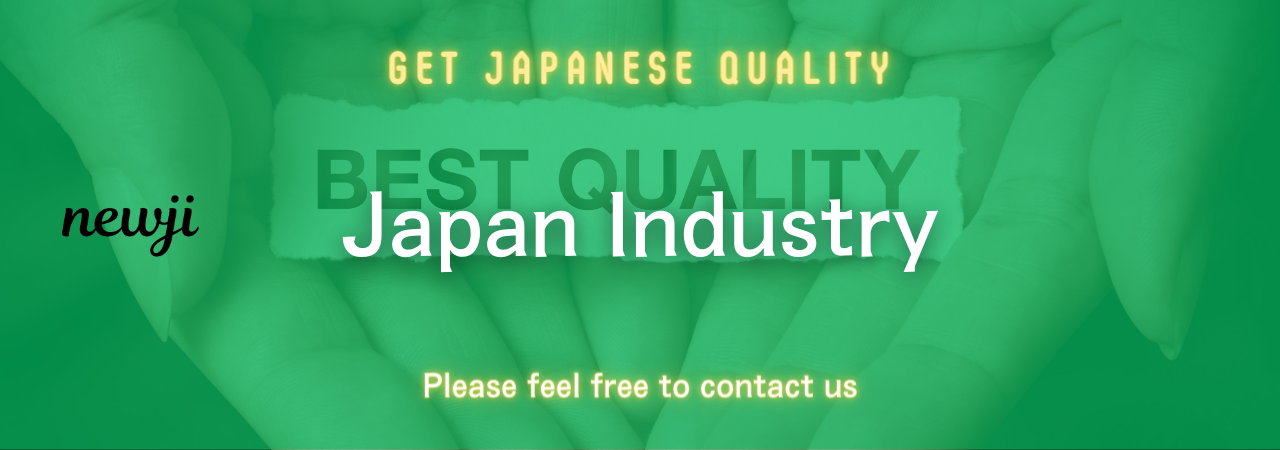
In today’s rapidly evolving industrial landscape, the importance of manufacturing process monitoring cannot be overstated. Keeping an eye on the entire production process ensures that products meet quality standards, helps in maintaining machinery efficiency, reduces waste, and optimizes the use of resources. Effective monitoring also aids in timely identification and rectification of issues, preventing costly downtime and fostering continuous improvement in manufacturing operations.
Understanding what manufacturing process monitoring entails is crucial. It involves the systematic tracking, analyzing, and documenting of various stages in the production process. From the initial sourcing of raw materials to the final production phase, each step is scrutinized to ensure that every component meets predefined specifications and standards.
Quality control is one significant area where process monitoring plays a critical role. By continually observing the production process, manufacturers can detect deviations from the set standards early on. For instance, if a component does not meet the required criteria, corrective measures can be implemented immediately before the issue affects the entire batch. This early intervention not only saves time and resources but also helps in maintaining high-quality standards for the finished product.
Another crucial aspect of manufacturing process monitoring is equipment and machinery upkeep. Continuous tracking of machine performance ensures they operate at optimal levels, reducing the likelihood of unforeseen breakdowns that can halt production. By monitoring variables such as temperature, pressure, and operational speed, manufacturers can schedule timely maintenance, thereby extending the lifespan of the machinery and enhancing overall plant efficiency.
The role of data in manufacturing process monitoring cannot be ignored. Advanced technologies, such as the Internet of Things (IoT) and machine learning, empower manufacturers to collect vast amounts of data from their machinery and production lines. This data can then be analyzed to gain insights into operational efficiencies, production bottlenecks, and potential areas of improvement. Through the effective use of data analytics, manufacturers can make informed decisions that drive productivity and profitability.
Implementing an effective manufacturing process monitoring system involves several steps. Firstly, it is crucial to identify key performance indicators (KPIs) that align with the organizational goals. These KPIs might include metrics such as production volume, defect rate, machine downtime, and overall equipment effectiveness (OEE). Once identified, these KPIs serve as a benchmark for evaluating the performance of the manufacturing process.
Next, selecting the right monitoring tools and technologies is vital. Various software solutions exist that cater to different aspects of manufacturing monitoring. For example, Manufacturing Execution Systems (MES) offer comprehensive functionalities, such as real-time monitoring, production scheduling, and quality management. Implementing such technologies provides factories with a centralized platform to oversee their entire production process seamlessly.
In addition, sensors and automation technologies have revolutionized manufacturing process monitoring. Through the integration of smart sensors, manufacturers can capture real-time data on various parameters, such as temperature, humidity, pressure, and chemical compositions. This data can then be relayed to a central system for analysis, providing immediate feedback on the production status. Automation further enhances monitoring by allowing for processes to be controlled with minimal human intervention, thus reducing the scope of errors and inefficiencies.
Employee training and involvement are also critical in the successful implementation of process monitoring systems. Workers who are well-versed in the technology and methodology behind process monitoring are more likely to embrace and efficiently utilize these systems. Regular training sessions and workshops can help employees stay updated on the latest tools and techniques, fostering a culture of continuous improvement within the organization.
The benefits of effective manufacturing process monitoring are manifold. Enhanced product quality, improved operational efficiency, reduced downtime, and cost savings are just a few advantages. Moreover, by maintaining a consistent and high-quality production line, manufacturers can strengthen their brand reputation and customer trust, leading to increased market competitiveness.
In conclusion, manufacturing process monitoring is an indispensable aspect of modern industrial operations. By implementing robust monitoring systems and effectively utilizing the data derived from these systems, manufacturers can significantly enhance their production processes. This leads to higher quality products, greater efficiency, and ultimately, a stronger bottom line. Continuous advancement in monitoring technologies promises to further empower manufacturers, paving the way for smarter, more efficient, and more resilient manufacturing operations.
資料ダウンロード
QCD調達購買管理クラウド「newji」は、調達購買部門で必要なQCD管理全てを備えた、現場特化型兼クラウド型の今世紀最高の購買管理システムとなります。
ユーザー登録
調達購買業務の効率化だけでなく、システムを導入することで、コスト削減や製品・資材のステータス可視化のほか、属人化していた購買情報の共有化による内部不正防止や統制にも役立ちます。
NEWJI DX
製造業に特化したデジタルトランスフォーメーション(DX)の実現を目指す請負開発型のコンサルティングサービスです。AI、iPaaS、および先端の技術を駆使して、製造プロセスの効率化、業務効率化、チームワーク強化、コスト削減、品質向上を実現します。このサービスは、製造業の課題を深く理解し、それに対する最適なデジタルソリューションを提供することで、企業が持続的な成長とイノベーションを達成できるようサポートします。
オンライン講座
製造業、主に購買・調達部門にお勤めの方々に向けた情報を配信しております。
新任の方やベテランの方、管理職を対象とした幅広いコンテンツをご用意しております。
お問い合わせ
コストダウンが利益に直結する術だと理解していても、なかなか前に進めることができない状況。そんな時は、newjiのコストダウン自動化機能で大きく利益貢献しよう!
(Β版非公開)