- お役立ち記事
- Application of AI Predictive Maintenance: The Future of Maintenance in Manufacturing
Application of AI Predictive Maintenance: The Future of Maintenance in Manufacturing
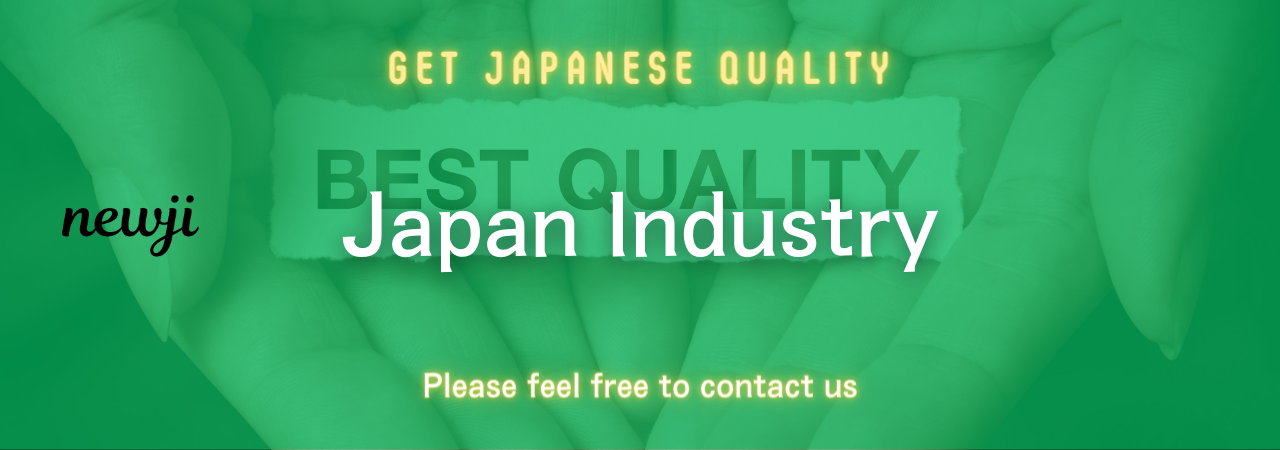
Predictive maintenance, driven by Artificial Intelligence (AI), is revolutionizing the manufacturing industry.
This innovative approach anticipates equipment failures before they occur, helping companies maintain optimal production levels and avoid costly downtime.
By integrating AI into maintenance strategies, manufacturers can enhance efficiency, reduce costs, and extend the lifespan of their machinery.
目次
Understanding Predictive Maintenance
Predictive maintenance involves monitoring the condition of equipment in real-time using advanced technologies like AI and the Internet of Things (IoT).
Traditional maintenance practices typically follow a reactive or preventive approach.
Reactive maintenance happens after a failure has occurred, leading to unplanned downtime and high repair costs.
Preventive maintenance schedules regular maintenance activities, regardless of the equipment’s actual condition, which can be inefficient and costly.
AI predictive maintenance offers a smarter, data-driven alternative.
AI algorithms analyze data from sensors and other monitoring devices, identifying patterns and predicting potential failures.
This information allows maintenance teams to address issues before they escalate, ensuring consistent and reliable operation.
How AI Predictive Maintenance Works
AI predictive maintenance utilizes several key elements to function effectively.
Data Collection
The process begins with collecting data from various sources within the manufacturing environment.
Sensors attached to equipment gather information on temperature, vibration, pressure, and other critical parameters.
This data is then transmitted to a centralized system for analysis.
Data Analysis
AI algorithms process the collected data, identifying trends and anomalies that could indicate potential failures.
Machine learning models are trained on historical data, enabling them to recognize patterns associated with specific types of equipment malfunctions.
As new data comes in, these models continuously improve their predictive accuracy.
Predictive Insights
The AI system generates insights and alerts based on the analyzed data.
These insights inform maintenance teams when a piece of equipment is likely to fail or require servicing.
By acting on these predictions, manufacturers can perform maintenance at the most opportune times, minimizing disruptions.
Benefits of AI Predictive Maintenance
Implementing AI predictive maintenance brings a multitude of benefits to the manufacturing sector.
Reduced Downtime
One of the most significant advantages is reduced downtime.
Unexpected equipment failures can bring production lines to a halt, resulting in lost revenue and delayed deliveries.
Predictive maintenance helps prevent such incidents by catching potential problems early, allowing for scheduled maintenance during non-peak times.
Cost Savings
Maintenance costs can be a substantial burden for manufacturers, especially when dealing with emergency repairs.
Predictive maintenance reduces the need for unplanned repairs and replacement of components, lowering overall maintenance costs.
Additionally, by optimizing maintenance schedules, companies can reduce labor costs and extend the life of their equipment.
Improved Safety
Equipment failures can pose serious safety risks to workers.
By addressing issues before they result in breakdowns, predictive maintenance enhances workplace safety.
Employees can work in a more secure environment, knowing that machinery is being monitored and maintained proactively.
Enhanced Efficiency
Predictive maintenance helps maintain a smooth and efficient production process.
With fewer unexpected interruptions, manufacturers can achieve higher productivity and better meet customer demands.
The improved reliability of equipment also leads to consistent product quality, boosting customer satisfaction.
Implementing AI Predictive Maintenance in Manufacturing
Transitioning to an AI predictive maintenance strategy requires careful planning and execution.
Choosing the Right Technology
Selecting the appropriate AI and IoT technologies is crucial.
Manufacturers need to invest in robust sensors and monitoring devices that can capture accurate data.
Additionally, choosing a reliable AI platform that can handle the data analysis and provide actionable insights is vital for success.
Integrating Systems
Effective predictive maintenance relies on seamless integration between various systems within the manufacturing environment.
Data from sensors, production management systems, and maintenance software must be synchronized to ensure accurate predictions.
Establishing a centralized data repository can facilitate this integration, making it easier to analyze and utilize the information collected.
Training and Skill Development
Introducing AI predictive maintenance requires upskilling the workforce.
Maintenance teams need to understand how to interpret AI-generated insights and take appropriate actions.
Providing training on the new technologies and systems will help employees adapt to the changes and leverage the full potential of predictive maintenance.
Continuous Improvement
Predictive maintenance is not a one-time implementation but an ongoing process.
Manufacturers should continuously monitor and refine their predictive models to improve accuracy.
Regularly updating the AI algorithms with new data ensures that the system remains effective in identifying potential failures.
The Future of Predictive Maintenance
As AI technology continues to advance, the capabilities of predictive maintenance will only improve.
Future developments may include more sophisticated AI models that can predict complex failure scenarios with even greater accuracy.
The integration of AI with other emerging technologies like augmented reality (AR) and digital twins could further enhance maintenance processes, providing real-time visualizations and virtual simulations of equipment conditions.
Moreover, the increasing adoption of Industry 4.0 principles will drive more widespread implementation of predictive maintenance.
By embracing these innovations, manufacturers can stay competitive in a rapidly evolving industry landscape.
In conclusion, AI predictive maintenance represents the future of maintenance in manufacturing.
Its ability to reduce downtime, lower costs, improve safety, and enhance efficiency makes it an invaluable tool for modern manufacturers.
By investing in the right technologies and strategies, companies can reap the benefits of this innovative approach and secure a more reliable and productive future.
資料ダウンロード
QCD調達購買管理クラウド「newji」は、調達購買部門で必要なQCD管理全てを備えた、現場特化型兼クラウド型の今世紀最高の購買管理システムとなります。
ユーザー登録
調達購買業務の効率化だけでなく、システムを導入することで、コスト削減や製品・資材のステータス可視化のほか、属人化していた購買情報の共有化による内部不正防止や統制にも役立ちます。
NEWJI DX
製造業に特化したデジタルトランスフォーメーション(DX)の実現を目指す請負開発型のコンサルティングサービスです。AI、iPaaS、および先端の技術を駆使して、製造プロセスの効率化、業務効率化、チームワーク強化、コスト削減、品質向上を実現します。このサービスは、製造業の課題を深く理解し、それに対する最適なデジタルソリューションを提供することで、企業が持続的な成長とイノベーションを達成できるようサポートします。
オンライン講座
製造業、主に購買・調達部門にお勤めの方々に向けた情報を配信しております。
新任の方やベテランの方、管理職を対象とした幅広いコンテンツをご用意しております。
お問い合わせ
コストダウンが利益に直結する術だと理解していても、なかなか前に進めることができない状況。そんな時は、newjiのコストダウン自動化機能で大きく利益貢献しよう!
(Β版非公開)