- お役立ち記事
- Application and Results of Six Sigma in Quality Assurance in Manufacturing
Application and Results of Six Sigma in Quality Assurance in Manufacturing
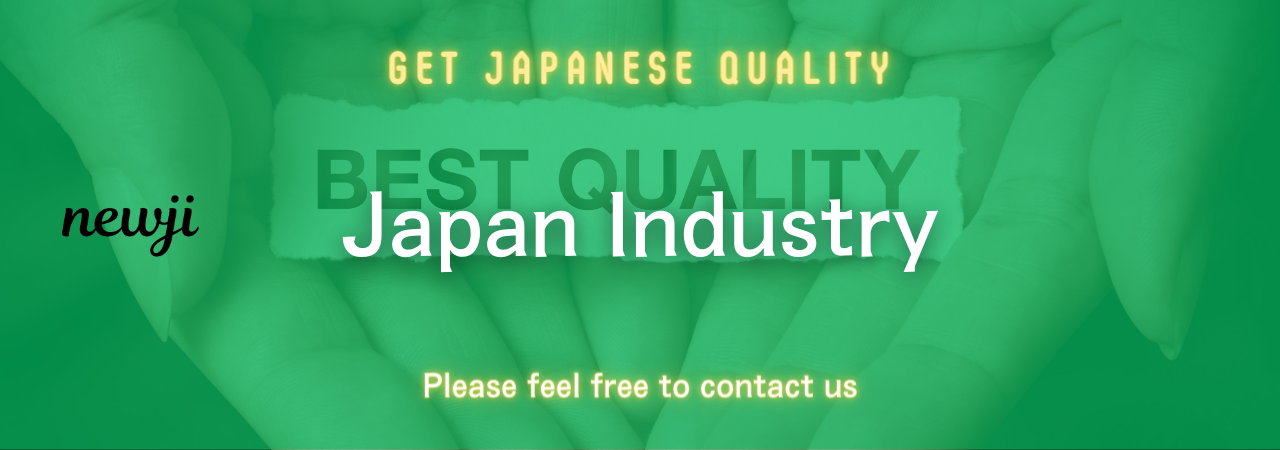
In the competitive landscape of manufacturing, ensuring top-notch quality is not just a requirement, but a crucial differentiator.
This is where Six Sigma comes into play.
Let’s dive into the application and results of Six Sigma in quality assurance in manufacturing.
目次
What is Six Sigma?
Six Sigma is a data-driven methodology aimed at improving processes and eliminating defects.
Developed by Motorola in 1986, Six Sigma focuses on reducing variability and enhancing consistency.
The main goal is to achieve near-perfection, or only 3.4 defects per one million opportunities.
Application of Six Sigma in Manufacturing
Implementing Six Sigma in manufacturing involves several steps.
Let’s explore these steps and see how they contribute to quality assurance.
Define Phase
In the Define phase, the problem that needs to be solved is clearly defined.
This phase sets the scope and objectives of the project.
For instance, if a car manufacturing plant faces issues with engine quality, the Define phase would identify the specific problems within the engine assembly.
Measure Phase
The Measure phase involves collecting data to understand the current performance.
In a manufacturing context, this could involve measuring the defect rates, cycle times, or production costs.
Accurate data collection is crucial for identifying gaps and areas for improvement.
Analyze Phase
During the Analyze phase, the collected data is scrutinized to identify root causes of defects and inefficiencies.
Advanced statistical tools are often used to pinpoint these root causes.
For example, in a factory producing electronics, the Analyze phase might reveal that a specific machine is responsible for a high number of defects.
Improve Phase
The Improve phase focuses on brainstorming and implementing solutions to the problems identified.
In manufacturing, this could mean redesigning a process, upgrading machinery, or introducing automation.
The goal is to reduce defect rates and enhance overall efficiency.
Control Phase
The Control phase ensures that the improvements are sustained over time.
Monitoring and control systems are put in place to consistently track performance.
For instance, regular quality inspections might be scheduled to ensure that defect rates remain low.
Results of Implementing Six Sigma in Manufacturing
The application of Six Sigma in manufacturing has yielded significant results for companies worldwide.
Here are some notable outcomes:
Enhanced Product Quality
Implementing Six Sigma methodologies can lead to substantial improvements in product quality.
By focusing on reducing variability, manufacturers can ensure that products meet or exceed customer expectations.
This leads to higher customer satisfaction and trust in the brand.
Cost Reduction
One of the primary benefits of Six Sigma is the reduction in costs.
By identifying and eliminating defects, manufacturers can reduce waste, rework, and returns.
This not only saves money but also boosts overall profitability.
Improved Efficiency
Six Sigma emphasizes streamlining processes, which enhances operational efficiency.
In a manufacturing setting, this could mean shorter cycle times, better utilization of resources, and higher throughput.
As a result, manufacturers can produce more in less time.
Employee Engagement
Engaging employees in Six Sigma projects fosters a culture of continuous improvement.
Employees are empowered to identify problems and contribute to solutions.
This not only improves the processes but also boosts employee morale and job satisfaction.
Better Decision Making
Six Sigma is rooted in data and statistical analysis.
This allows for better decision-making based on evidence rather than intuition.
Manufacturers can make informed decisions that drive continuous improvement and long-term success.
Real-World Examples
Many leading companies have successfully implemented Six Sigma in their manufacturing processes.
Here are a few examples:
General Electric (GE)
General Electric is one of the pioneers in adopting Six Sigma.
By implementing Six Sigma methodologies, GE achieved significant cost savings and operational improvements.
For instance, the company saved over $300 million in one year by reducing defects in its products.
Motorola
As the birthplace of Six Sigma, Motorola has reaped immense benefits from its application.
The company reported savings of $17 billion over a period of five years through Six Sigma projects.
Motorola’s commitment to quality revolutionized its production processes and set a benchmark for the industry.
Ford Motor Company
Ford leveraged Six Sigma to enhance the quality of its vehicles and streamline its manufacturing operations.
By focusing on reducing defects and improving processes, Ford was able to achieve higher customer satisfaction and reduce warranty claims.
Challenges and Solutions
While Six Sigma offers numerous benefits, it also comes with its own set of challenges.
Let’s look at some common challenges and how they can be addressed:
Resistance to Change
Employees might resist changes introduced by Six Sigma projects.
To overcome this, it’s crucial to communicate the benefits and provide proper training.
Encouraging employee involvement and showing quick wins can also help in winning their support.
Lack of Expertise
Implementing Six Sigma requires a deep understanding of its tools and techniques.
To address this, companies can invest in training and certifying employees as Six Sigma Green Belts or Black Belts.
Maintaining Momentum
Sustaining improvements over the long term can be challenging.
Regular monitoring and control mechanisms should be put in place to ensure that gains are not lost over time.
Continuous training and reinforcement of Six Sigma principles are also essential.
Conclusion
The application of Six Sigma in quality assurance in manufacturing has proven to be a game-changer.
By following a structured approach, companies can significantly improve product quality, reduce costs, and enhance efficiency.
While challenges exist, they can be effectively managed with proper planning and execution.
As more and more manufacturers embrace Six Sigma, the future looks promising for delivering high-quality, defect-free products to customers worldwide.
資料ダウンロード
QCD調達購買管理クラウド「newji」は、調達購買部門で必要なQCD管理全てを備えた、現場特化型兼クラウド型の今世紀最高の購買管理システムとなります。
ユーザー登録
調達購買業務の効率化だけでなく、システムを導入することで、コスト削減や製品・資材のステータス可視化のほか、属人化していた購買情報の共有化による内部不正防止や統制にも役立ちます。
NEWJI DX
製造業に特化したデジタルトランスフォーメーション(DX)の実現を目指す請負開発型のコンサルティングサービスです。AI、iPaaS、および先端の技術を駆使して、製造プロセスの効率化、業務効率化、チームワーク強化、コスト削減、品質向上を実現します。このサービスは、製造業の課題を深く理解し、それに対する最適なデジタルソリューションを提供することで、企業が持続的な成長とイノベーションを達成できるようサポートします。
オンライン講座
製造業、主に購買・調達部門にお勤めの方々に向けた情報を配信しております。
新任の方やベテランの方、管理職を対象とした幅広いコンテンツをご用意しております。
お問い合わせ
コストダウンが利益に直結する術だと理解していても、なかなか前に進めることができない状況。そんな時は、newjiのコストダウン自動化機能で大きく利益貢献しよう!
(Β版非公開)