- お役立ち記事
- Basics and effective application of sliding mode control
月間77,185名の
製造業ご担当者様が閲覧しています*
*2025年2月28日現在のGoogle Analyticsのデータより
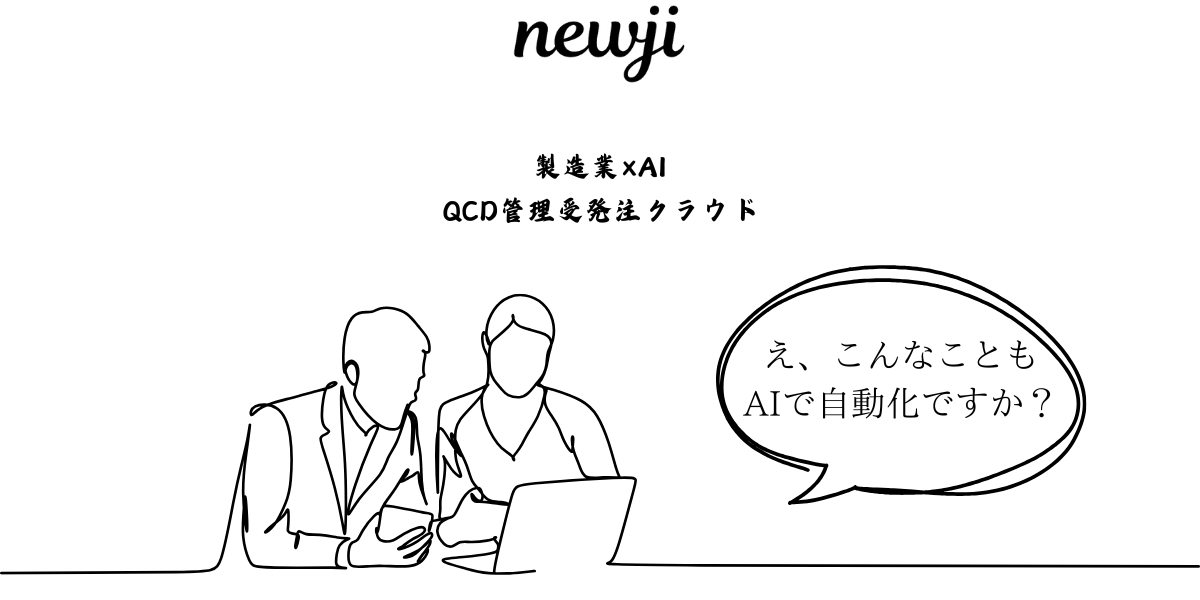
Basics and effective application of sliding mode control
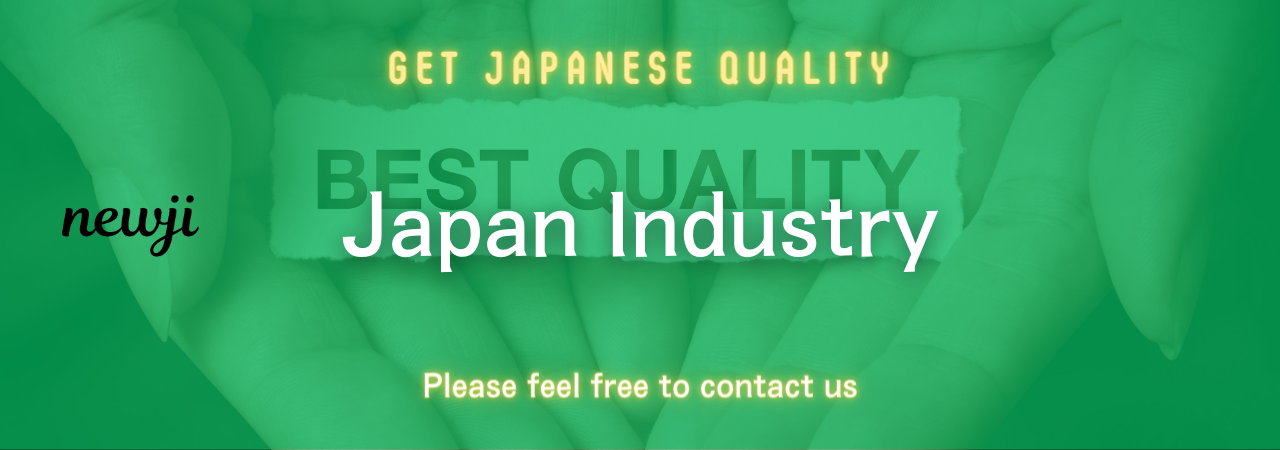
目次
Understanding Sliding Mode Control
Sliding mode control (SMC) is an advanced control technique that’s used in a variety of fields, including robotics, automotive systems, and electrical engineering.
At its core, SMC is a type of variable structure control system, aiming to enforce a desired behavior in systems subjected to changes or disturbances.
How Sliding Mode Control Works
The principle behind SMC is relatively straightforward.
It works by driving the system state toward a predefined surface, known as the sliding surface.
This sliding surface is carefully designed to ensure desired system dynamics.
When the system state reaches this surface, a discontinuous control action keeps the state on the surface, despite disturbances or changes.
This is what makes SMC robust; it effectively handles parameter variations and external disturbances.
Designing the Sliding Surface
The effectiveness of SMC largely depends on the design of the sliding surface.
This surface is a function of the system states, and it’s defined such that when the system state is on this surface, the system exhibits the desired dynamics.
The design process usually involves creating a model of the system and determining the appropriate dynamics.
This might involve choosing parameters that define the surface to ensure a swift response and minimal oscillations.
Advantages of Sliding Mode Control
One of the most appealing aspects of sliding mode control is its robustness.
Even in the face of significant disturbances or parameter changes within the system, SMC can maintain desired performance.
Another advantage is its simplicity in implementation compared to other robust control techniques.
It doesn’t require a highly accurate model of the system.
Additionally, SMC is known for its ability to quickly drive the system state to the sliding surface, ensuring rapid response to changes.
Challenges in Sliding Mode Control
Despite its advantages, SMC is not without challenges.
The most notable is the phenomenon known as “chattering.”
Chattering occurs due to the high-frequency switching of the control signal, which can induce wear and tear in mechanical systems.
To address chattering, several solutions have been proposed.
These include using boundary layers around the sliding surface, or higher-order sliding mode control strategies that smooth out the control action.
Applications of Sliding Mode Control
The robustness and efficiency of SMC make it suitable for a wide range of applications.
Robotics
In robotics, SMC is often used for motion control and stabilization.
Its ability to deal with model uncertainties and external disturbances makes it ideal for controlling robot arms and mobile robots.
Automotive Systems
Slipping and skidding can be controlled effectively in automotive applications using SMC.
It’s employed in areas like traction control, braking systems, and vehicle dynamics stabilization.
Electrical and Power Systems
SMC is widely used in electrical engineering for controlling power converters and managing energy distribution.
Its robustness ensures reliability in the presence of load variations and network disturbances.
Aerospace
In aerospace, the ability of SMC to handle aerodynamic disturbances makes it suitable for controlling the flight dynamics of aircraft and spacecraft.
Manufacturing
In the manufacturing sector, SMC is used for processes requiring precision and stability, such as CNC machining.
Conclusion
Sliding mode control offers a robust and reliable solution for systems where uncertainties and disturbances are prevalent.
Its simplicity and effectiveness in harsh conditions make it a preferred choice for various industries, including robotics, automotive, and aerospace.
However, the challenge of chattering must be addressed for successful implementation.
With ongoing research and development, SMC continues to evolve, offering even greater performance and applicability.
Understanding the basics and effective application of sliding mode control can provide engineers and researchers with a powerful tool in their control systems toolkit.
資料ダウンロード
QCD管理受発注クラウド「newji」は、受発注部門で必要なQCD管理全てを備えた、現場特化型兼クラウド型の今世紀最高の受発注管理システムとなります。
ユーザー登録
受発注業務の効率化だけでなく、システムを導入することで、コスト削減や製品・資材のステータス可視化のほか、属人化していた受発注情報の共有化による内部不正防止や統制にも役立ちます。
NEWJI DX
製造業に特化したデジタルトランスフォーメーション(DX)の実現を目指す請負開発型のコンサルティングサービスです。AI、iPaaS、および先端の技術を駆使して、製造プロセスの効率化、業務効率化、チームワーク強化、コスト削減、品質向上を実現します。このサービスは、製造業の課題を深く理解し、それに対する最適なデジタルソリューションを提供することで、企業が持続的な成長とイノベーションを達成できるようサポートします。
製造業ニュース解説
製造業、主に購買・調達部門にお勤めの方々に向けた情報を配信しております。
新任の方やベテランの方、管理職を対象とした幅広いコンテンツをご用意しております。
お問い合わせ
コストダウンが利益に直結する術だと理解していても、なかなか前に進めることができない状況。そんな時は、newjiのコストダウン自動化機能で大きく利益貢献しよう!
(β版非公開)