- お役立ち記事
- Differences in processing technology between polypropylene and polyethylene and appropriate selection method [For industry engineers]
月間77,185名の
製造業ご担当者様が閲覧しています*
*2025年2月28日現在のGoogle Analyticsのデータより
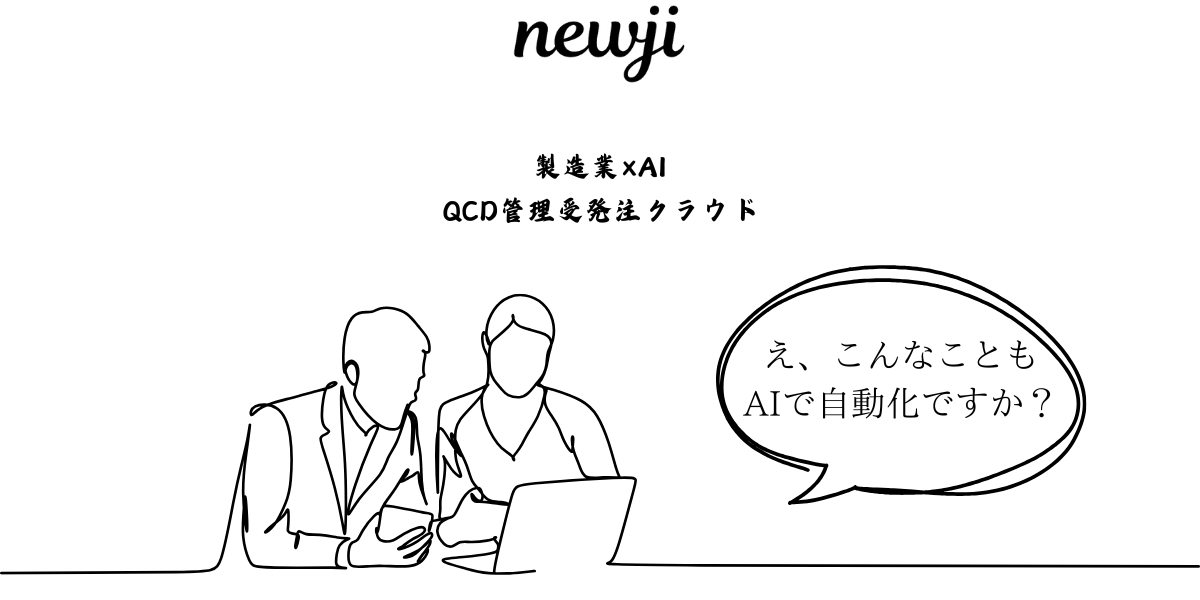
Differences in processing technology between polypropylene and polyethylene and appropriate selection method [For industry engineers]
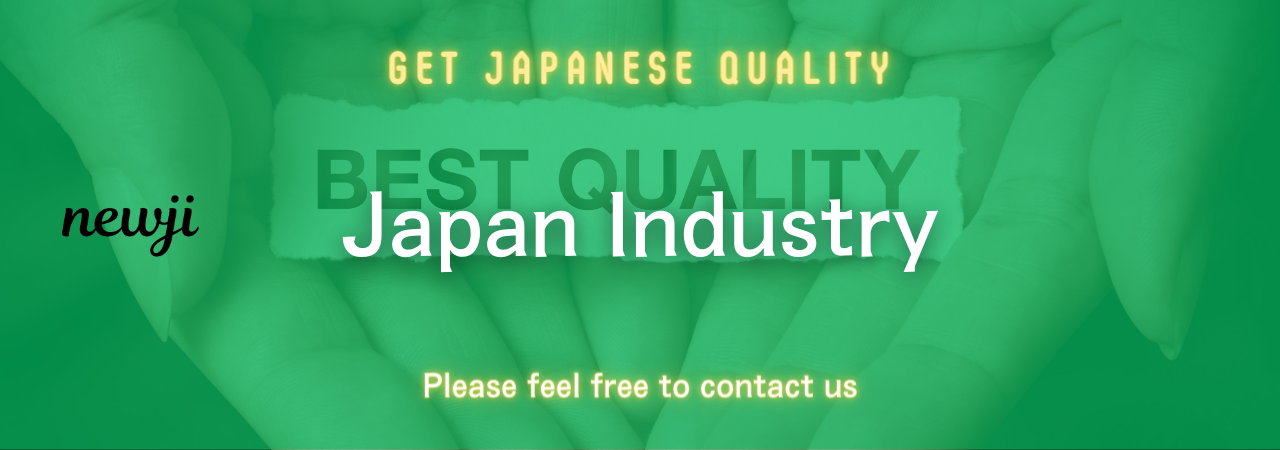
目次
Introduction to Polypropylene and Polyethylene
Polypropylene (PP) and polyethylene (PE) are among the most widely used thermoplastics in the world.
Their popularity stems from their versatility, durability, and cost-effectiveness, making them staples in various industries including packaging, automotive, textiles, and construction.
Despite their similarities, these materials have distinctive properties which necessitate different processing technologies.
Understanding these differences is crucial for industry engineers in determining the appropriate material selection for specific applications.
Basic Properties of Polypropylene
Polypropylene is a semi-crystalline polymer characterized by its high strength-to-weight ratio and excellent chemical resistance.
Its melting point ranges between 130°C and 170°C, which makes it suitable for applications requiring sterilization.
PP is less dense than polyethylene and exhibits high resistance to fatigue, making it perfect for living hinges, packaging, and automotive parts.
Additionally, it possesses good impact strength and has a low water absorption rate, which are important for products exposed to moisture.
Basic Properties of Polyethylene
Polyethylene, another widely used thermoplastic, exists in various densities: low-density polyethylene (LDPE), medium-density polyethylene (MDPE), and high-density polyethylene (HDPE).
This variability provides a range of mechanical properties fitting different applications.
PE typically has a lower melting point than PP, ranging between 115°C and 135°C for LDPE, slightly higher for HDPE.
It is known for being highly pliable and resistant to stress-cracking.
The inherent flexibility of PE, especially LDPE, makes it ideal for film applications, bags, and flexible tubing.
HDPE, being more rigid, is often employed in applications requiring structural integrity, like containers and pipes.
Processing Techniques for Polypropylene
Polypropylene is commonly processed using extrusion, injection molding, and blow molding due to its ability to be melted and reshaped.
In injection molding, precise control over polypropylene’s cooling process is critical, as this determines the final product’s strength and appearance.
Extrusion is widely used for making films and fibers.
During this process, PP is melted and forced through a die to form continuous shapes such as pipes and sheets.
Blow molding is used when creating hollow objects such as bottles and containers; the PP is extruded into a parison, then captured in a mold where air inflates it into shape.
Processing Techniques for Polyethylene
Polyethylene can also be processed using extrusion, blow molding, and injection molding, with some variations in techniques suited to its different grades.
In extrusion, LDPE and HDPE can both be used to produce films, pipes, and sheets, but they require different processing conditions due to their distinct melt indices and viscosities.
Blow molding is predominantly used with HDPE to produce containers and bottles due to its superior rigidity compared to LDPE.
In injection molding, polyethylene’s lower melting point and flexibility can sometimes result in longer cycle times compared to PP, but it is advantageous for creating complex shapes with high impact resistance.
Rotational molding is another notable technique for PE, often used for large, hollow products like tanks, leveraging its excellent flow characteristics.
Key Differences in Processing Technologies
While both PP and PE share common processing techniques, the differences in their thermal and mechanical properties necessitate specific adaptations.
Polypropylene typically offers better resistance to environmental stress cracking than polyethylene, which must be accounted for during design and processing.
Since PP has a higher melting point, it can sustain higher temperature processes which can be advantageous for applications where thermal stability is crucial.
Conversely, polyethylenes, especially HDPE, generally exhibit better impact resistance at lower temperatures compared to PP.
These thermal properties significantly influence the choice of additives and stabilizers during manufacturing to enhance performance.
Selection Method for Engineers
Selecting the right material between polypropylene and polyethylene depends on the application’s specific requirements.
Industry engineers should consider factors such as environmental exposure, physical stress, chemical interaction, and regulatory compliance.
For instance, in applications requiring heat resistance or exposure to chemicals, PP would typically be more suitable due to its higher melting point and chemical resistance.
Where flexibility and impact resistance are essential—such as in packaging films or toys—PE, particularly LDPE, would be favorable.
Cost, while generally comparable, can also be a deciding factor depending on the required volumes and material waste during the manufacturing process.
Furthermore, sustainability considerations might play a role, as both PP and PE are recyclable, but facilities and technologies for recycling differ regionally.
Conclusion
For industry engineers, understanding the differences in processing technologies between polypropylene and polyethylene is pivotal.
Choosing the appropriate material requires a thorough evaluation of the application’s specific needs, balancing cost, environmental considerations, and the mechanical and thermal properties required.
Through strategic selection and skillful application of processing techniques, engineers can harness the strengths of both materials to produce superior products suited to a wide array of industrial demands.
資料ダウンロード
QCD管理受発注クラウド「newji」は、受発注部門で必要なQCD管理全てを備えた、現場特化型兼クラウド型の今世紀最高の受発注管理システムとなります。
ユーザー登録
受発注業務の効率化だけでなく、システムを導入することで、コスト削減や製品・資材のステータス可視化のほか、属人化していた受発注情報の共有化による内部不正防止や統制にも役立ちます。
NEWJI DX
製造業に特化したデジタルトランスフォーメーション(DX)の実現を目指す請負開発型のコンサルティングサービスです。AI、iPaaS、および先端の技術を駆使して、製造プロセスの効率化、業務効率化、チームワーク強化、コスト削減、品質向上を実現します。このサービスは、製造業の課題を深く理解し、それに対する最適なデジタルソリューションを提供することで、企業が持続的な成長とイノベーションを達成できるようサポートします。
製造業ニュース解説
製造業、主に購買・調達部門にお勤めの方々に向けた情報を配信しております。
新任の方やベテランの方、管理職を対象とした幅広いコンテンツをご用意しております。
お問い合わせ
コストダウンが利益に直結する術だと理解していても、なかなか前に進めることができない状況。そんな時は、newjiのコストダウン自動化機能で大きく利益貢献しよう!
(β版非公開)