- お役立ち記事
- Fundamentals of drawing processing and know-how to improve workability
月間77,185名の
製造業ご担当者様が閲覧しています*
*2025年2月28日現在のGoogle Analyticsのデータより
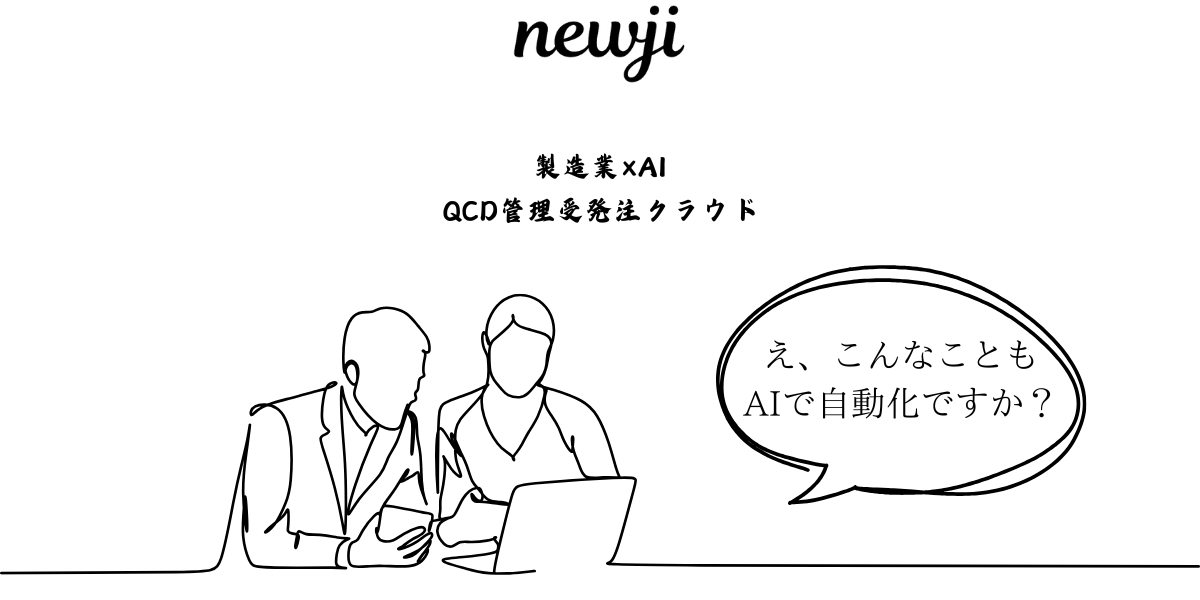
Fundamentals of drawing processing and know-how to improve workability
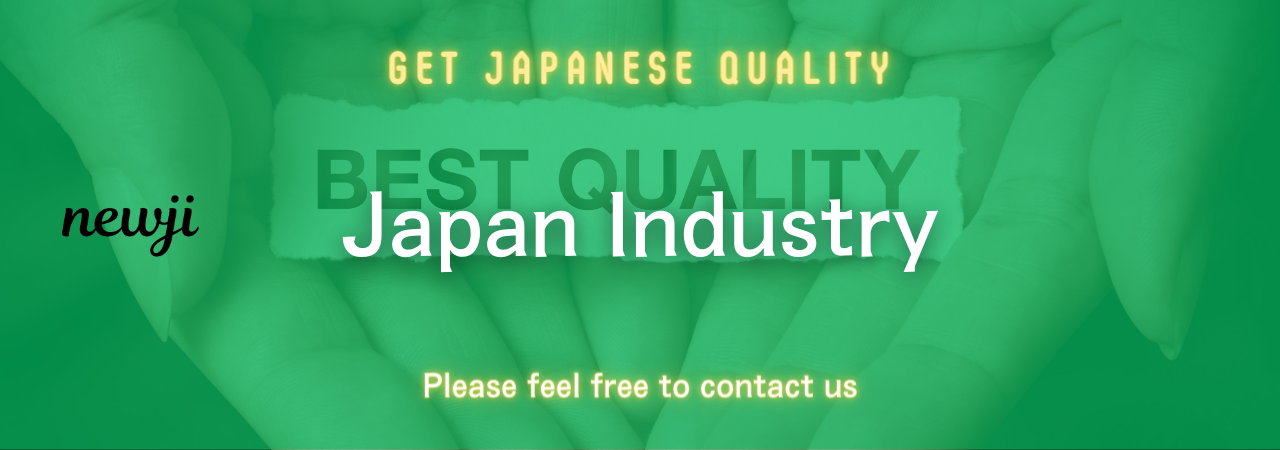
目次
Understanding the Basics of Drawing Processing
Drawing processing is a fundamental technique used in manufacturing and engineering that involves reshaping metal by pulling it through a die.
It is a process applied to produce a variety of items such as wires, tubes, and rods.
To get a better grasp of how drawing processing works, let’s delve into its core concepts and procedures.
At its core, drawing processing serves to reduce the diameter of a metal piece while increasing its length.
This transformation is achieved by forcing the metal into progressively smaller dies, which shift it into the desired shape and size.
The process can be conducted at room temperature or with the application of heat, depending on the material and the specific requirements of the final product.
Different metals behave differently under the drawing process.
For instance, ductile metals like copper and aluminum are more amenable to cold drawing, where the operation occurs at room temperature.
On the other hand, harder metals such as steel may require heat to make them pliable during hot drawing.
Types of Drawing Processes
There are several types of drawing processes, each catering to different materials and desired outcomes.
Wire Drawing
Wire drawing is a widely used technique for creating thin and flexible metal wires.
Start by feeding a thick metal rod through progressively smaller dies to eventually achieve the thin wires seen in products like electrical cables and springs.
Tubular Drawing
This process is utilized to produce hollow tubes and pipes.
By using a mandrel along with the dies, manufacturers can ensure that the inner diameter of the tube is as precise as the outer.
This technique is essential for industries that require uniform wall thickness for pipelines and structural tubes.
Rod Drawing
Rod drawing is used to produce metallic rods with a consistent diameter along their entire length.
These rods are often further processed into products like bolts, screws, or even used as components in manufacturing machinery.
Enhancing Workability in Drawing Processing
Improving workability in drawing processing essentially revolves around ensuring high efficiency with minimal defects, while also maintaining the quality of the finished product.
Here are some key strategies to enhance workability.
Material Selection
Choosing the right material is crucial for achieving optimal results.
Each metal has its own characteristics, which determine its compatibility with drawing processing.
Factors like ductility, tensile strength, and heat treatment properties must be considered before initiating the process.
Lubrication
Adequate lubrication reduces friction and wear on the metal and drawing dies.
It minimizes force required for drawing and improves the surface finish of the final product.
Selecting the right lubricant based on the metal type and drawing speed is essential for maintaining quality and preventing tool wear.
Die Design and Maintenance
The design and condition of the dies play a pivotal role in the success of drawing processing.
Ensuring that dies are designed with smooth, even contours helps in reducing surface defects.
Regular maintenance and timely replacement of worn-out dies are critical to sustaining production quality and efficiency.
Temperature Control
Material properties change with temperature variations.
In hot drawing processes, maintaining precise temperature control is crucial to prevent overheating of the metal and to achieve uniform material properties.
In cold drawing, controlling room temperature and material preheating can also impact the process positively.
Quality Control and Testing
Implementing stringent quality control measures is fundamental to maintaining high standards in drawing processing.
Regular testing of feedstock materials, as well as finished products, guarantees consistency and reliability.
Incorporating non-destructive testing techniques helps in identifying imperfections without damaging the product.
Common Challenges and Solutions
Drawing processing, although efficient, poses its own challenges that need to be addressed for smooth operations.
Surface Defects
Surface defects like scratches or irregularities occur due to worn dies or insufficient lubrication.
Regularly inspecting and maintaining equipment, along with proper lubrication management, can mitigate such issues.
Material Breakage
Breakage typically results from excessive drawing speed or incorrect material selection.
Adjusting the speed settings and ensuring the choice of material aligns with the drawing requirements can prevent breakage.
Inconsistent Dimensions
Variations in dimensions can arise from die misalignment or improper material feeding.
Meticulous calibration of the drawing setup and consistent monitoring of the process help in achieving dimensional accuracy.
Conclusion
Drawing processing is a vital procedure in the manufacturing world, essential for creating various metal products.
Understanding its fundamentals and implementing strategies to improve workability can significantly enhance operational efficiency and product quality.
By focusing on the aspects of material selection, lubrication, die maintenance, temperature control, and quality testing, manufacturers can overcome the challenges associated with drawing processing.
Equipped with this know-how, industries can optimize their processes to meet the demands of modern engineering and manufacturing.
資料ダウンロード
QCD管理受発注クラウド「newji」は、受発注部門で必要なQCD管理全てを備えた、現場特化型兼クラウド型の今世紀最高の受発注管理システムとなります。
ユーザー登録
受発注業務の効率化だけでなく、システムを導入することで、コスト削減や製品・資材のステータス可視化のほか、属人化していた受発注情報の共有化による内部不正防止や統制にも役立ちます。
NEWJI DX
製造業に特化したデジタルトランスフォーメーション(DX)の実現を目指す請負開発型のコンサルティングサービスです。AI、iPaaS、および先端の技術を駆使して、製造プロセスの効率化、業務効率化、チームワーク強化、コスト削減、品質向上を実現します。このサービスは、製造業の課題を深く理解し、それに対する最適なデジタルソリューションを提供することで、企業が持続的な成長とイノベーションを達成できるようサポートします。
製造業ニュース解説
製造業、主に購買・調達部門にお勤めの方々に向けた情報を配信しております。
新任の方やベテランの方、管理職を対象とした幅広いコンテンツをご用意しております。
お問い合わせ
コストダウンが利益に直結する術だと理解していても、なかなか前に進めることができない状況。そんな時は、newjiのコストダウン自動化機能で大きく利益貢献しよう!
(β版非公開)