- お役立ち記事
- Practical course on the basics of DRBFM and effective prevention
月間77,185名の
製造業ご担当者様が閲覧しています*
*2025年2月28日現在のGoogle Analyticsのデータより
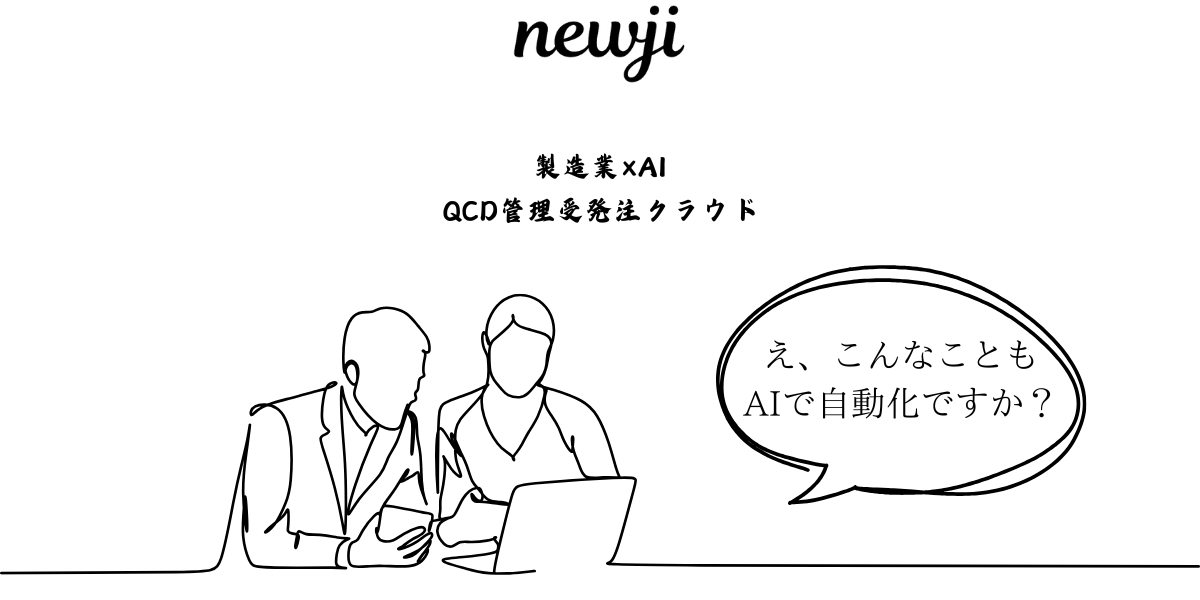
Practical course on the basics of DRBFM and effective prevention
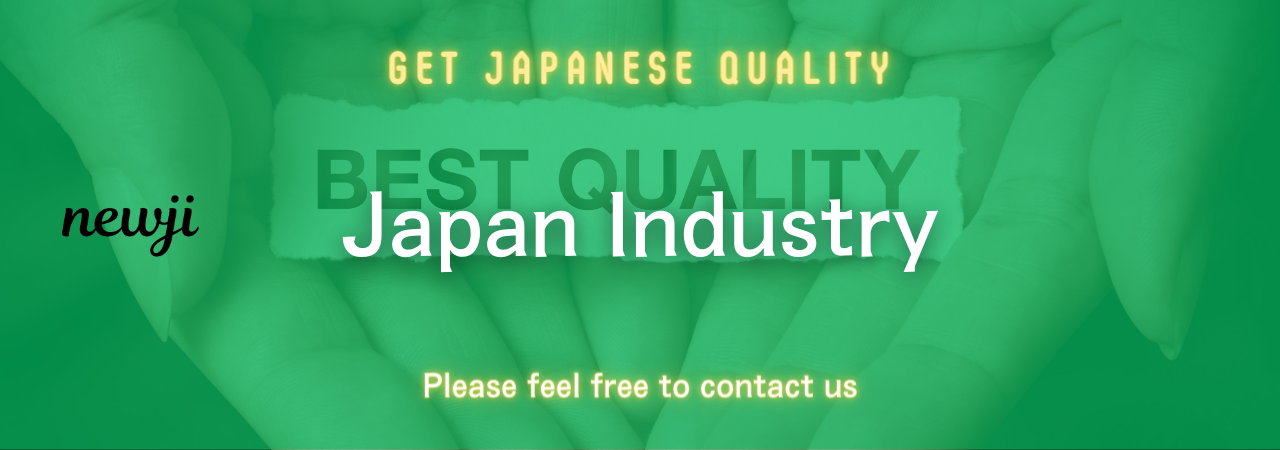
目次
Understanding DRBFM: An Overview
Design Review Based on Failure Modes (DRBFM) is an analytical methodology used to improve the reliability and quality of products.
Originally developed in the automotive industry, this approach helps teams identify potential design flaws and mitigate them before they become significant problems.
But what exactly is DRBFM and why is it important?
The core objective of DRBFM is to foresee potential failures in a product’s design.
By doing so, teams can make informed decisions on necessary modifications to prevent issues from reaching consumers.
This not only enhances product quality but also safeguards a company’s reputation while minimizing costly recalls.
Steps of DRBFM Process
Implementing DRBFM involves a structured process, typically comprising several stages:
1. Planning and Preparation
Before diving into the analysis, it is essential to set clear objectives and gather a multidisciplinary team.
Preparation includes collecting all relevant design documents and establishing the scope of the review.
This groundwork maximizes the efficiency of the subsequent steps.
2. Change Point Identification
DRBFM places significant emphasis on changes between the current design and any modifications.
These change points are potential sources of failure since they introduce new variables into the established system.
Identifying change points is crucial because it directs the focus of risk analysis.
3. Conducting Detailed Design Analysis
Once change points are identified, the design team conducts a thorough analysis of these areas.
This includes brainstorming possible failure modes and their effects.
Potential causes are considered, and the team evaluates the severity, occurrence, and detection of each failure mode.
This step is vital to understanding the possible impacts on the overall design.
4. Developing Preventative Actions
With a clear understanding of potential failure modes, the next step is to determine actions to counteract them.
This may involve design modifications, additional testing, or process changes.
Preventative actions aim to eliminate or mitigate the risks associated with identified failure modes.
5. Documentation and Follow-up
Documentation is essential in DRBFM to keep a detailed record of the process, decisions made, and actions taken.
Follow-up involves monitoring the outcomes of the implemented changes to ensure that they have effectively addressed the identified risks.
This step also includes a review to confirm the effectiveness of the implemented preventative actions.
Benefits of DRBFM in Product Development
Implementing DRBFM holds numerous benefits for organizations across various industries:
Improved Product Quality
By proactively identifying and addressing potential design flaws, DRBFM enhances the quality of the final product.
This approach reduces the likelihood of defects and leads to greater customer satisfaction.
Cost-Effectiveness
Investing time in detailed analysis during the design phase can prevent costly corrections later in the production process.
By anticipating potential failures, DRBFM minimizes the need for expensive redesigns or recalls.
Enhanced Team Collaboration
DRBFM requires input from multiple departments and stakeholders, fostering a culture of collaboration.
Teams that work together gain a deeper understanding of the product, leading to more innovative solutions.
Best Practices for Effective DRBFM Implementation
For DRBFM to be effective, organizations should adhere to best practices:
Engage a Multidisciplinary Team
Involving team members from diverse backgrounds brings varied perspectives to the table, enriching the analysis process.
Encouraging open communication among team members can lead to more thorough and creative solutions.
Focus on Change Points
Concentrating specifically on areas of change allows teams to pinpoint elements that might introduce failure modes.
This focus makes the analysis more manageable and targeted without overwhelming the team.
Regular Training and Updates
Keeping the team informed with up-to-date DRBFM training ensures that everyone is aware of the latest methodologies and techniques.
Regular updates and training sessions help maintain a high level of analysis quality.
Comprehensive Documentation
Thorough documentation throughout the DRBFM process is crucial for tracking progress and for future reference.
Well-maintained records enable a smoother review process and can expedite the implementation of improvements.
Conclusion
DRBFM is a valuable tool in the arsenal of any organization aiming to elevate product quality and reliability.
By focusing on potential failure modes from the outset, teams can prevent many common design issues that lead to recalls or customer dissatisfaction.
Through a structured process involving clear communication and strategic planning, DRBFM addresses risks at the design phase.
This results in cost savings and stronger collaboration, improving the overall product development lifecycle.
By adopting DRBFM, organizations are effectively safeguarding their products and ensuring customer trust and loyalty.
Implementing this methodology is an investment in a product’s success and in a company’s reputation.
資料ダウンロード
QCD管理受発注クラウド「newji」は、受発注部門で必要なQCD管理全てを備えた、現場特化型兼クラウド型の今世紀最高の受発注管理システムとなります。
ユーザー登録
受発注業務の効率化だけでなく、システムを導入することで、コスト削減や製品・資材のステータス可視化のほか、属人化していた受発注情報の共有化による内部不正防止や統制にも役立ちます。
NEWJI DX
製造業に特化したデジタルトランスフォーメーション(DX)の実現を目指す請負開発型のコンサルティングサービスです。AI、iPaaS、および先端の技術を駆使して、製造プロセスの効率化、業務効率化、チームワーク強化、コスト削減、品質向上を実現します。このサービスは、製造業の課題を深く理解し、それに対する最適なデジタルソリューションを提供することで、企業が持続的な成長とイノベーションを達成できるようサポートします。
製造業ニュース解説
製造業、主に購買・調達部門にお勤めの方々に向けた情報を配信しております。
新任の方やベテランの方、管理職を対象とした幅広いコンテンツをご用意しております。
お問い合わせ
コストダウンが利益に直結する術だと理解していても、なかなか前に進めることができない状況。そんな時は、newjiのコストダウン自動化機能で大きく利益貢献しよう!
(β版非公開)