- お役立ち記事
- Points for selecting appropriate materials and processing methods and using them in the development, design, and manufacturing of aluminum products
月間77,185名の
製造業ご担当者様が閲覧しています*
*2025年2月28日現在のGoogle Analyticsのデータより
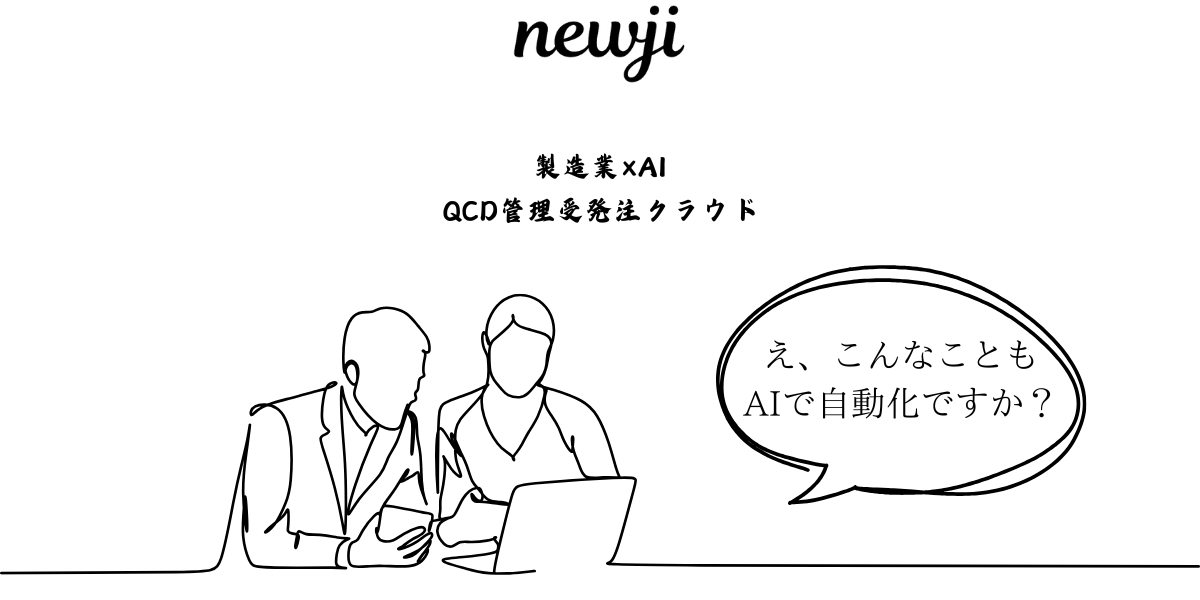
Points for selecting appropriate materials and processing methods and using them in the development, design, and manufacturing of aluminum products
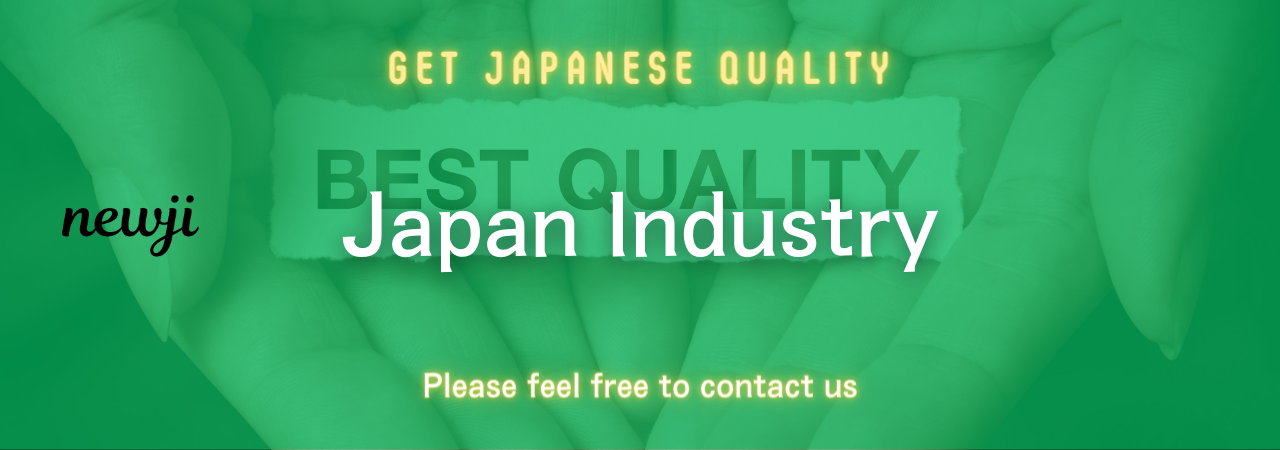
目次
Understanding Aluminum: An Essential Material
Aluminum is a versatile metal, widely used across various industries due to its unique properties.
It is lightweight, corrosion-resistant, and boasts excellent thermal and electrical conductivity.
These characteristics make it ideal for applications ranging from automotive and aerospace to consumer electronics and packaging.
Selecting the right aluminum alloy and processing method is crucial in the development, design, and manufacturing of aluminum products.
In this guide, we’ll explore the key points to consider when choosing materials and methods, ensuring your products meet the required standards and functionality.
Choosing the Right Aluminum Alloy
Aluminum comes in various alloys, each with different properties and suited to different applications.
The following considerations are essential when selecting the right aluminum alloy for your project:
1. Strength and Hardness
Different alloys offer varying levels of strength and hardness.
If your application requires a high-strength material, consider using a 7000-series aluminum alloy, known for its high tensile strength.
For applications where moderate strength and good machinability are important, 6000-series alloys could be the ideal choice.
2. Corrosion Resistance
Aluminum itself is naturally resistant to corrosion.
However, some applications, such as marine or outdoor environments, require enhanced resistance.
In such cases, alloys like 5000-series, which contain magnesium, provide greater corrosion resistance.
3. Formability
Formability refers to the ease with which the aluminum can be shaped into your desired configuration.
For applications requiring complex shapes or intricate designs, consider using 3000-series alloys, which offer good formability.
On the other hand, if you require precise, uniform parts, choose an alloy with excellent machinability, like those in the 6000-series.
4. Thermal and Electrical Requirements
The thermal and electrical conductivity of aluminum is also a vital consideration, especially in electronics or heat-exchanging apparatus.
Pure aluminum, classified under the 1000-series, provides excellent conductivity and might be suitable for your needs.
Selecting the Appropriate Processing Methods
Processing methods significantly affect the aluminum product’s properties, performance, and quality.
Here are some common processing techniques for aluminum and their considerations:
1. Extrusion
Extrusion is a preferred method for producing aluminum profiles and tubes.
It involves pushing aluminum billets through a shaped die to create long, uniform cross-sections.
When opting for extrusion, it’s important to consider the design limitations, surface finish requirements, and cost efficiency.
Extruded products are ideal for applications where strength-to-weight ratio is critical.
2. Casting
Casting involves pouring molten aluminum into a mold to produce a desired shape.
It’s ideal for complex or intricate designs that might be difficult to achieve through other methods.
When choosing casting, consider the final part’s dimensional accuracy, surface quality, and potential porosity issues.
Die-casting with aluminum alloys can produce high-quality, high-volume components efficiently.
3. Rolling
Rolling is essential for creating flat aluminum sheets, coils, and plates.
This process imparts the material with desired thickness and surface finish.
Consider the alloy type and intended application when choosing rolling as a processing method, as it affects the final product’s mechanical properties.
4. Forging
Forging is used to produce high-strength aluminum with excellent fatigue resistance.
It involves compressing aluminum between hard tools to form a desired shape.
Forging is suitable for components requiring high mechanical strength and precision, such as aerospace parts.
Design Considerations for Aluminum Products
Proper design plays a pivotal role in the performance and manufacturability of aluminum products.
Here are key aspects to consider during the design phase:
1. Weight Optimization
One of aluminum’s main advantages is its lightweight nature.
Incorporating design techniques like topology optimization can help reduce weight while maintaining structural integrity.
Such designs are particularly beneficial in weight-sensitive sectors like aerospace and automotive.
2. Stress and Load Analysis
Conduct thorough stress and load analysis to ensure the product can handle operational demands.
Finite Element Analysis (FEA) tools can simulate conditions to predict potential stress points and improve the design accordingly.
3. Surface Finishing
Surface finishing enhances the appearance, corrosion resistance, and durability of aluminum products.
Common finishing processes include anodizing, powder coating, and painting.
Consider the end-use environment and aesthetic requirements when selecting a suitable finish.
Quality Control and Testing
Quality assurance is crucial to ensure aluminum products meet safety standards and performance specifications.
Implement rigorous testing procedures such as tensile testing, hardness testing, and non-destructive testing methods to verify the quality of materials and processes used.
Establish a robust quality control system to identify defects promptly, reduce waste, and ensure consistent product performance.
Conclusion
Aluminum products offer unparalleled versatility and performance across various applications.
Choosing the right alloy, processing method, and design approach is key to optimizing product quality and functionality.
By understanding the properties and needs of your application, you can make informed decisions that lead to successful aluminum product development, design, and manufacturing.
By incorporating these essential points into your process, you can enhance your product’s quality, performance, and cost-effectiveness.
A thoughtful approach to material selection and processing will ultimately deliver superior aluminum solutions that meet industry demands and customer expectations.
資料ダウンロード
QCD管理受発注クラウド「newji」は、受発注部門で必要なQCD管理全てを備えた、現場特化型兼クラウド型の今世紀最高の受発注管理システムとなります。
ユーザー登録
受発注業務の効率化だけでなく、システムを導入することで、コスト削減や製品・資材のステータス可視化のほか、属人化していた受発注情報の共有化による内部不正防止や統制にも役立ちます。
NEWJI DX
製造業に特化したデジタルトランスフォーメーション(DX)の実現を目指す請負開発型のコンサルティングサービスです。AI、iPaaS、および先端の技術を駆使して、製造プロセスの効率化、業務効率化、チームワーク強化、コスト削減、品質向上を実現します。このサービスは、製造業の課題を深く理解し、それに対する最適なデジタルソリューションを提供することで、企業が持続的な成長とイノベーションを達成できるようサポートします。
製造業ニュース解説
製造業、主に購買・調達部門にお勤めの方々に向けた情報を配信しております。
新任の方やベテランの方、管理職を対象とした幅広いコンテンツをご用意しております。
お問い合わせ
コストダウンが利益に直結する術だと理解していても、なかなか前に進めることができない状況。そんな時は、newjiのコストダウン自動化機能で大きく利益貢献しよう!
(β版非公開)