- お役立ち記事
- 製造業DXを加速する!PDCAサイクル活用法で現場革新を実現する方法
製造業DXを加速する!PDCAサイクル活用法で現場革新を実現する方法
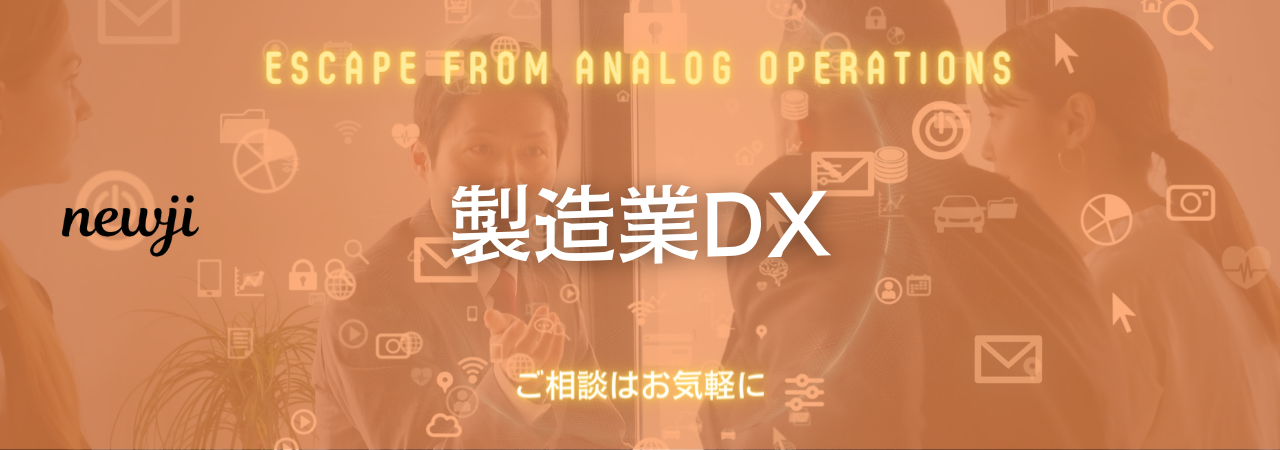
目次
はじめに
製造業におけるデジタルトランスフォーメーション(DX)は、今や企業の競争力を左右する重要な要素となっています。特に、PDCAサイクル(Plan-Do-Check-Act)を活用することで、現場の業務改善や効率化を効果的に推進できます。本記事では、製造業DXを加速させるためのPDCAサイクル活用法について、現場目線の実践的な内容やメリット・デメリット、最新の技術動向や事例を交えて解説します。
PDCAサイクルとは
PDCAサイクルは、業務改善やプロジェクト管理において広く用いられるフレームワークです。以下の4つのステップから構成されます。
Plan(計画)
目標を設定し、達成するための計画を立てます。現状分析を行い、改善点を特定します。
Do(実行)
計画に基づいて実行します。具体的な行動を起こし、計画通りに進めます。
Check(確認)
実行結果を評価し、計画とのギャップを確認します。データを収集し、効果を分析します。
Act(改善)
評価結果を基に、次のサイクルに向けて改善策を立案します。成功点を標準化し、失敗点を修正します。
製造業におけるPDCAサイクルの活用方法
製造業の現場では、PDCAサイクルを効果的に活用することで、生産性の向上や品質の改善が期待できます。以下に具体的な活用方法を紹介します。
1. 生産プロセスの最適化
Plan段階で生産ラインのボトルネックを特定し、Do段階で改善策を実施します。Check段階で生産効率を評価し、Act段階でさらなる最適化を図ります。これにより、無駄な工程の削減や生産速度の向上が実現します。
2. 品質管理の強化
品質問題を計画的に解決するためにPDCAサイクルを導入します。Planで品質基準を設定し、Doで検査やテストを実施します。Checkで不良品率を分析し、Actで品質向上策を講じます。これにより、製品の安定した品質を維持できます。
3. 設備の保全とメンテナンス
設備の故障を未然に防ぐため、計画的なメンテナンスをPDCAサイクルで管理します。Planでメンテナンススケジュールを作成し、Doで定期点検を行います。Checkで設備の状態を評価し、Actで改善点を反映させます。これにより、設備の稼働率を高め、生産停止を防止します。
PDCAサイクル導入のメリットとデメリット
PDCAサイクルを製造業に導入する際には、以下のようなメリットとデメリットがあります。
メリット
– **継続的な改善が可能**:PDCAサイクルを繰り返すことで、持続的な業務改善が実現できます。
– **問題の早期発見と対応**:定期的な評価により、問題点を早期に発見し迅速に対応できます。
– **組織全体の統一感**:全社員が同じフレームワークを使用することで、組織全体の統一感が生まれます。
デメリット
– **時間とリソースの消費**:PDCAサイクルの各ステップを丁寧に実施するには、時間とリソースが必要です。
– **柔軟性の欠如**:計画に固執しすぎると、急な変更や柔軟な対応が難しくなる場合があります。
– **効果の測定が困難な場合も**:特に品質改善などの分野では、効果を定量的に測定することが難しい場合があります。
最新の技術動向とPDCAサイクルの融合
製造業におけるDX推進において、最新の技術とPDCAサイクルの融合は非常に重要です。以下に、注目すべき技術動向とその活用方法を紹介します。
IoT(モノのインターネット)の活用
IoT技術を活用することで、生産ラインの各設備からリアルタイムなデータを収集できます。これにより、Plan段階での現状分析が精緻になり、Do段階での改善策の実行が効果的になります。Check段階では、収集したデータを基に詳細な評価が可能となり、Act段階での迅速な改善が実現します。
ビッグデータとAIの活用
ビッグデータとAIを活用することで、膨大なデータの中から有益な情報を抽出し、意思決定の精度を高めることができます。特に、品質管理や需要予測においてAIは強力なツールとなります。PDCAサイクルの各ステップにおいて、データドリブンなアプローチを採用することで、改善の効果を最大化できます。
成功事例:PDCAサイクルでDXを実現した企業
実際にPDCAサイクルを活用してDXを成功させた企業の事例を紹介します。
事例1:自動車メーカーの生産ライン改善
某大手自動車メーカーでは、PDCAサイクルを導入して生産ラインの効率化を図りました。Plan段階で生産ボトルネックを特定し、Do段階で自動化設備を導入しました。Check段階で生産速度と不良品率を詳細に分析し、Act段階でさらに自動化範囲を拡大しました。その結果、生産効率が20%向上し、不良品率が15%減少しました。
事例2:電子部品メーカーの品質管理強化
ある電子部品メーカーでは、品質問題を減少させるためにPDCAサイクルを活用しました。Plan段階で品質基準を見直し、Do段階で検査プロセスを強化しました。Check段階で不良品データを分析し、Act段階で改善策を実施しました。これにより、顧客クレームが大幅に減少し、顧客満足度が向上しました。
PDCAサイクル導入のポイント
PDCAサイクルを効果的に導入するためには、以下のポイントに留意することが重要です。
1. 目標の明確化
具体的で測定可能な目標を設定することが重要です。曖昧な目標では、改善の方向性が定まりません。
2. データの活用
正確なデータを収集・分析することで、現状の課題を正確に把握し、適切な改善策を立案できます。
3. 継続的なフィードバック
PDCAサイクルを一度実施するだけでなく、継続的に繰り返すことで、持続的な改善が可能となります。
4. 組織全体の協力
PDCAサイクルの効果を最大化するためには、組織全体の協力とコミットメントが必要です。現場の意見を積極的に取り入れ、全員が改善に参加する文化を醸成しましょう。
まとめ
製造業におけるDX推進において、PDCAサイクルは強力なツールとなります。計画的な業務改善を繰り返すことで、生産性の向上や品質の安定が実現できます。最新技術との融合や成功事例を参考にしながら、効果的なPDCAサイクルの運用を目指しましょう。組織全体で取り組むことで、持続的な成長と競争力の向上が期待できます。
資料ダウンロード
QCD調達購買管理クラウド「newji」は、調達購買部門で必要なQCD管理全てを備えた、現場特化型兼クラウド型の今世紀最高の購買管理システムとなります。
ユーザー登録
調達購買業務の効率化だけでなく、システムを導入することで、コスト削減や製品・資材のステータス可視化のほか、属人化していた購買情報の共有化による内部不正防止や統制にも役立ちます。
NEWJI DX
製造業に特化したデジタルトランスフォーメーション(DX)の実現を目指す請負開発型のコンサルティングサービスです。AI、iPaaS、および先端の技術を駆使して、製造プロセスの効率化、業務効率化、チームワーク強化、コスト削減、品質向上を実現します。このサービスは、製造業の課題を深く理解し、それに対する最適なデジタルソリューションを提供することで、企業が持続的な成長とイノベーションを達成できるようサポートします。
オンライン講座
製造業、主に購買・調達部門にお勤めの方々に向けた情報を配信しております。
新任の方やベテランの方、管理職を対象とした幅広いコンテンツをご用意しております。
お問い合わせ
コストダウンが利益に直結する術だと理解していても、なかなか前に進めることができない状況。そんな時は、newjiのコストダウン自動化機能で大きく利益貢献しよう!
(Β版非公開)