- お役立ち記事
- QC7つ道具で製造業DXを加速:デジタル時代の品質管理戦略
月間76,176名の
製造業ご担当者様が閲覧しています*
*2025年3月31日現在のGoogle Analyticsのデータより
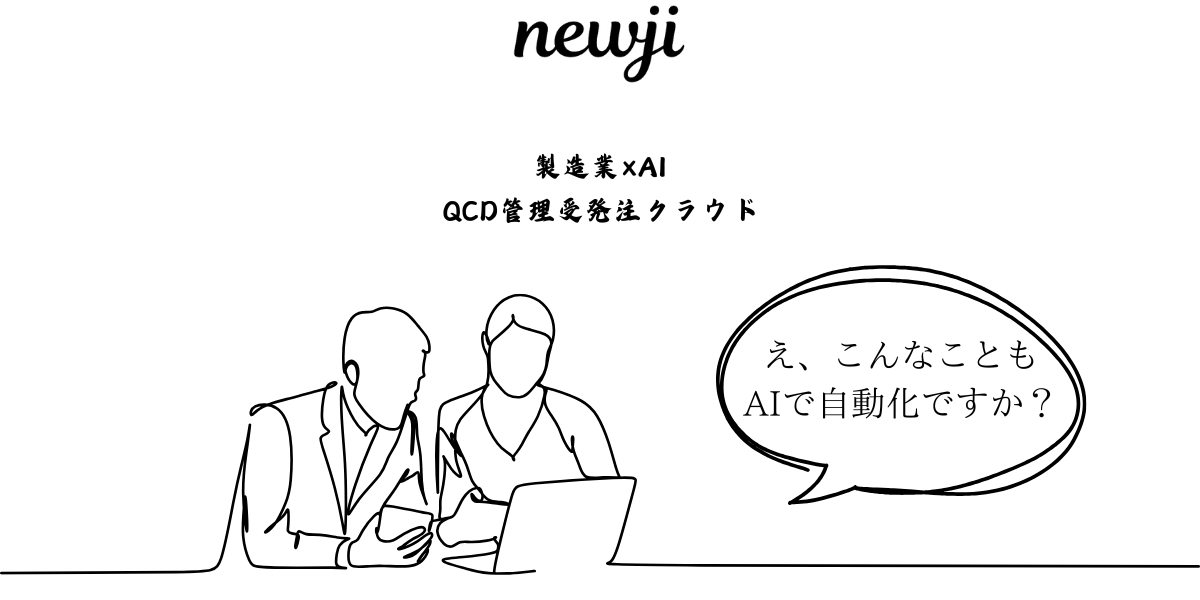
QC7つ道具で製造業DXを加速:デジタル時代の品質管理戦略
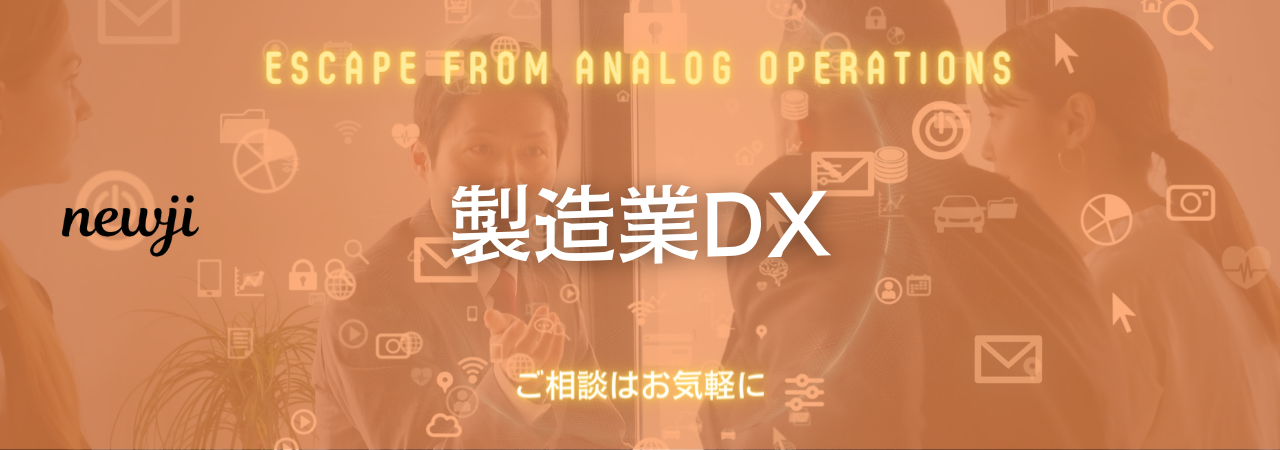
目次
はじめに
製造業において、品質管理は常に重要なテーマでした。
しかし、デジタル時代が到来し、品質管理の方法も大きく変わろうとしています。
特に、QC7つ道具はこれまでも現場の問題解決に活用されてきましたが、最新のデジタル技術と組み合わせることで、さらなる効果が期待されます。
本記事では、QC7つ道具を活用するためのデジタル戦略について詳しく解説します。
QC7つ道具とは
まず、QC7つ道具について簡単におさらいします。
これは品質管理の基本ツールであり、問題解決やデータ分析に有用です。
具体的には以下の7つが挙げられます。
1. パレート図
2. 特性要因図(魚の骨図)
3. 管理図
4. チェックシート
5. ヒストグラム
6. 散布図
7. 層別
これらのツールは、手作業でも利用できますが、デジタル技術を活用することで、より効率的にデータを収集・分析できます。
デジタル化がもたらすメリット
QC7つ道具をデジタル化することで、以下のメリットがあります。
1. データの自動収集と分析:センサーやIoTデバイスを活用することで、現場のデータをリアルタイムで収集し、自動的に分析できます。
2. フィードバックの迅速化:分析結果を瞬時にフィードバックし、問題点を早期に発見できます。
3. 作業の効率化:手作業でのデータ入力や分析が不要になり、作業効率が向上します。
4. 高い精度:デジタルツールを使用することで、ヒューマンエラーを減らし、分析結果の精度が向上します。
パレート図とデジタルツールの活用
パレート図は、問題の大きさを視覚的に示すためのツールです。
従来は手動でデータを集め、エクセルなどで図表化していましたが、デジタルツールを活用することで、この工程を大幅に省略できます。
具体例:IoTとパレート図
例えば、製造ラインの各箇所に設置したセンサーが不良品数や生産量をリアルタイムでモニタリングします。
これらのデータを自動で収集し、クラウド上でパレート図を生成することが可能です。
不良原因別に分類することで、最も改善が必要なポイントを迅速に特定できます。
メリットとデメリット
デジタルツールを活用する場合のメリットとしては、データの収集と分析が自動化されるため、迅速なフィードバックが得られる点が挙げられます。
一方、デメリットとしては初期導入コストや、実際の運用には一定のスキルが必要となることです。
特性要因図とAIの活用
特性要因図は、問題の原因を特定するためのツールです。
従来はチームでブレインストーミングし、原因を手作業で挙げていましたが、AIを活用することで、より精度の高い原因特定が可能です。
AIによる因果関係の特定
AIは膨大なデータを解析し、隠れた因果関係を見つけ出すことが得意です。
例えば、製品の不良品率が高い場合、製造プロセスのデータを解析し、その原因と考えられる要因を特定します。
これにより、以前見逃していた問題を発見することができます。
メリットとデメリット
AIの導入によるメリットとしては、高度なデータ解析が可能になり、より精度の高い原因特定ができる点が挙げられます。
デメリットとしては、AIのトレーニングと運用に時間とコストがかかることです。
管理図とリアルタイムモニタリング
管理図は、製品の安定性を監視するためのツールです。
従来は、一定期間のデータを手動で記録し、エクセルなどで管理図を作成していましたが、デジタルツールを活用することで、リアルタイムでの監視が可能になります。
具体例:SCADAシステム
SCADA(Supervisory Control and Data Acquisition)システムを導入することで、製造プロセスをリアルタイムで監視し、管理図を自動生成できます。
異常が検出された場合は、即座にアラートが発信されるため、早期に対策を講じることが可能です。
メリットとデメリット
リアルタイムモニタリングのメリットは、異常を早期に発見できる点です。
これにより、製品の不良率を低減し、品質を保つことができます。
デメリットとしては、初期導入コストやシステムのメンテナンスが必要となることです。
チェックシートとデジタル記録
チェックシートは、特定の項目を定期的にチェックし、記録するためのツールです。
従来は紙ベースでチェックシートを作成し、手動で記録していましたが、デジタルツールを活用することで、効率的なデータ管理が可能です。
具体例:モバイルアプリの活用
モバイルアプリを使用して、現場作業員がチェック項目をデジタルで記録することで、リアルタイムでデータを共有できます。
これにより、管理者もリアルタイムで状況を把握し、適切な判断を下すことができます。
メリットとデメリット
デジタルチェックシートのメリットは、定期的なデータが自動的に整理され、管理が簡単になる点です。
また、紙ベースのチェックシートと比べて、ヒューマンエラーも減少します。
デメリットとしては、システムの導入と運用が必要になることです。
ヒストグラムとビッグデータ解析
ヒストグラムは、データの分布を視覚的に表すツールです。
従来はデータを手動で集計し、エクセルなどで作成していましたが、ビッグデータ解析ツールを活用することで、より詳細な分析が可能です。
具体例:データ解析プラットフォームの活用
例えば、製造ラインの各ポイントのデータをクラウド上に集約し、そのデータを解析プラットフォームでヒストグラムとして表示します。
これにより、データの分布や異常値を迅速に把握できます。
メリットとデメリット
ビッグデータ解析を活用する場合のメリットは、大量のデータを効率的に解析できる点です。
また、異常値を早期に発見し、迅速に対策を講じることができます。
デメリットとしては、大量のデータを扱うため、解析ツールの導入と運用に時間とコストがかかることです。
散布図と機械学習の組み合わせ
散布図は、二つの変数の関係を視覚的に示すツールです。
従来は手動でデータを集計し、エクセルで作成していましたが、機械学習を利用することで、より高度な解析が可能です。
具体例:機械学習モデルの適用
例えば、製品の歩留まりと製造条件の関係を解析するために、機械学習モデルを用います。
これにより、二つの変数間の複雑な関係をより詳しく理解し、最適な製造条件を特定することができます。
メリットとデメリット
機械学習を組み合わせるメリットは、高度な解析が可能となり、潜在的な問題点を発見できる点です。
デメリットとしては、機械学習モデルのトレーニングや運用にスキルとリソースが必要となることです。
層別とデータの可視化
層別は、データを特定の条件で区分して分析するツールです。
従来は手動でデータを区分していましたが、デジタルツールを利用することで、簡単にデータを層別し、可視化できます。
具体例:BIツールの活用
BI(ビジネスインテリジェンス)ツールを導入することで、異なる条件でデータを自動的に層別し、視覚的に表示できます。
例えば、製造ラインの稼働状況を時間帯や作業員別に層別し、効率の高い時間帯や作業員を特定します。
メリットとデメリット
デジタル層別のメリットは、多様な条件でデータを簡単に区分し、詳細な分析が可能となる点です。
デメリットとしては、BIツールの導入と運用にコストがかかることです。
まとめ
デジタル時代の製造業において、QC7つ道具をデジタル化することは、品質管理の向上に大いに役立ちます。
データの自動収集と分析、リアルタイムモニタリング、AIと機械学習の活用など、最新の技術を取り入れることで、従来の方法では実現できなかった高度な品質管理が可能となります。
しかし、導入にあたっては初期コストや運用のためのスキルが必要となるため、慎重に検討することが大切です。
今後もデジタル技術の進化に伴い、さらに高度な品質管理手法が登場するでしょう。
製造業がこれらの技術を適切に活用することで、競争力を維持し、さらなる成長を遂げることが期待されます。
資料ダウンロード
QCD管理受発注クラウド「newji」は、受発注部門で必要なQCD管理全てを備えた、現場特化型兼クラウド型の今世紀最高の受発注管理システムとなります。
ユーザー登録
受発注業務の効率化だけでなく、システムを導入することで、コスト削減や製品・資材のステータス可視化のほか、属人化していた受発注情報の共有化による内部不正防止や統制にも役立ちます。
NEWJI DX
製造業に特化したデジタルトランスフォーメーション(DX)の実現を目指す請負開発型のコンサルティングサービスです。AI、iPaaS、および先端の技術を駆使して、製造プロセスの効率化、業務効率化、チームワーク強化、コスト削減、品質向上を実現します。このサービスは、製造業の課題を深く理解し、それに対する最適なデジタルソリューションを提供することで、企業が持続的な成長とイノベーションを達成できるようサポートします。
製造業ニュース解説
製造業、主に購買・調達部門にお勤めの方々に向けた情報を配信しております。
新任の方やベテランの方、管理職を対象とした幅広いコンテンツをご用意しております。
お問い合わせ
コストダウンが利益に直結する術だと理解していても、なかなか前に進めることができない状況。そんな時は、newjiのコストダウン自動化機能で大きく利益貢献しよう!
(β版非公開)