- お役立ち記事
- Monday.comで構築!製造業の生産スケジュール管理
Monday.comで構築!製造業の生産スケジュール管理
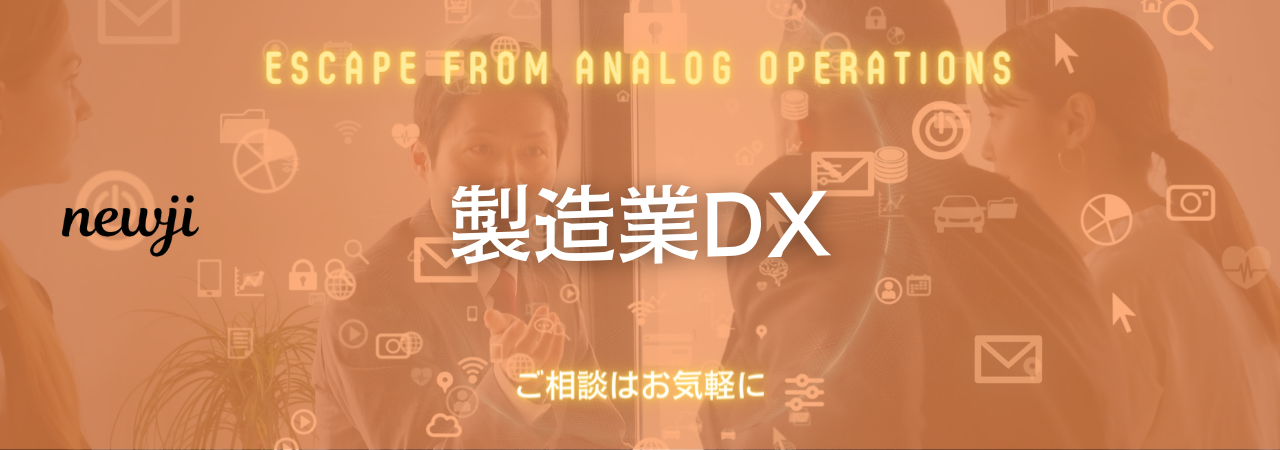
目次
Introduction to Monday.com in Manufacturing
In today’s fast-paced manufacturing environment, efficient and accurate production scheduling is key to maintaining competitiveness. The advent of digital tools and software can significantly streamline these processes, improving productivity and reducing errors. One such tool making a significant impact is Monday.com. This article explores how Monday.com can be leveraged to optimize production schedule management in the manufacturing sector.
What is Monday.com?
Monday.com is a Work Operating System (Work OS) that provides customizable workflows to manage teams and projects efficiently. Although it is commonly used in various industries, its capabilities are particularly beneficial for manufacturing. With features like task assignment, automated workflows, and real-time updates, Monday.com helps manufacturing managers keep track of production schedules, resource allocation, and project timelines.
Why Choose Monday.com for Production Scheduling?
1. Real-Time Collaboration
Manufacturing involves coordination between various departments—procurement, production, quality control, and logistics. Monday.com enables real-time collaboration among these departments, ensuring that everyone stays on the same page. Updates made by one department are immediately visible to others, reducing the likelihood of miscommunication and errors.
2. Customizable Dashboards
One of the standout features of Monday.com is its highly customizable dashboards. These can be configured to display key performance indicators (KPIs), production timelines, and resource allocation in real-time. Managers can quickly get an overview of the production status and make data-driven decisions to optimize operations.
3. Automation
Manual data entry and task allocation can be time-consuming and prone to errors. Monday.com offers automation capabilities that can take over these repetitive tasks. For instance, when a production order is completed, the system can automatically update inventory levels, notify the procurement team, and schedule the next production run.
How to Set Up Monday.com for Production Scheduling?
1. Identify Key Processes and Tasks
The first step in setting up Monday.com for production scheduling is identifying the key processes and tasks involved. This includes procurement of raw materials, production phases, quality control checks, and logistics. List these tasks down and categorize them based on priority and sequence.
2. Create Boards for Each Process
Monday.com uses ‘boards’ to organize tasks and projects. Create separate boards for each key process identified. For example, you might have one board for procurement, another for production, and a third for quality control. Within each board, tasks can be further broken down into individual steps.
3. Assign Roles and Responsibilities
Each task and process should have a designated owner responsible for its completion. Monday.com allows you to easily assign roles and responsibilities, ensuring accountability. Assign tasks to specific team members, and set deadlines to monitor progress.
4. Integrate with Existing Systems
Monday.com offers various integrations with other software systems commonly used in manufacturing, such as ERP systems, inventory management software, and communication tools like Slack. Integrating these systems can provide a seamless flow of information, further enhancing efficiency.
Optimizing Production Schedules with Monday.com
1. Gantt Charts for Visual Planning
Gantt charts are a powerful visual tool for planning and tracking production schedules. Monday.com features an excellent Gantt chart view that allows managers to see the entire production process at a glance. By dragging and dropping tasks within the Gantt chart, managers can easily adjust schedules in response to changes in production needs or unexpected delays.
2. Resource Management
Efficient resource management is crucial for maintaining productivity. Monday.com provides features for tracking and allocating resources, including machinery, labor, and materials. By monitoring resource availability in real-time, managers can avoid bottlenecks and ensure optimal utilization of resources.
3. Real-Time Updates and Notifications
Staying informed of changes and updates is critical in manufacturing. Monday.com allows real-time updates and notifications, ensuring that all stakeholders are immediately aware of any changes in the production schedule. For example, if a machinery breakdown occurs, a notification can be sent to the maintenance team to address the issue promptly.
4. Use Data for Continuous Improvement
One of Monday.com’s strengths lies in its comprehensive data collection and reporting capabilities. By analyzing this data, manufacturers can identify trends, monitor performance, and find areas for improvement. This data-driven approach supports continuous improvement, enhancing overall efficiency and productivity.
Case Study: Successful Implementation of Monday.com
To illustrate the potential of Monday.com in manufacturing, let’s consider a real-life case study of a mid-sized manufacturing company implementing this tool.
The company, specializing in electronic component manufacturing, faced significant challenges in managing its production schedules, leading to frequent delays and increased operational costs. The firm decided to implement Monday.com to solve these issues.
Step 1: Initial Setup
The company began by identifying its core processes and creating specific boards for each, including procurement, production, quality control, and logistics. Tasks were clearly defined and assigned to appropriate team members, ensuring accountability.
Step 2: Training and Integration
Training sessions were conducted for all employees to familiarize them with the new system. Furthermore, Monday.com was integrated with the company’s existing ERP system, allowing seamless data flow and reducing manual entry tasks.
Step 3: Monitoring and Adjustment
Using the customizable dashboards and automation features, managers monitored the production schedules and made necessary adjustments in real time. The Gantt chart view was particularly useful for visualizing the entire production process, ensuring that tasks flowed smoothly from one stage to the next.
Step 4: Continuous Improvement
The company leveraged Monday.com’s data reporting tools to analyze performance metrics. This data-driven approach led to continuous process improvements, resulting in a 20% reduction in production time and a 15% decrease in operational costs within the first six months.
Conclusion
In the ever-evolving manufacturing landscape, efficient production schedule management is vital for maintaining competitiveness and achieving operational excellence. Monday.com offers a comprehensive, customizable, and user-friendly platform capable of addressing these needs. By leveraging its robust features, manufacturers can enhance collaboration, optimize resource utilization, and drive continuous improvement. Investing time and resources into implementing such digital tools can yield significant long-term benefits, propelling companies towards greater productivity and success.
資料ダウンロード
QCD調達購買管理クラウド「newji」は、調達購買部門で必要なQCD管理全てを備えた、現場特化型兼クラウド型の今世紀最高の購買管理システムとなります。
ユーザー登録
調達購買業務の効率化だけでなく、システムを導入することで、コスト削減や製品・資材のステータス可視化のほか、属人化していた購買情報の共有化による内部不正防止や統制にも役立ちます。
NEWJI DX
製造業に特化したデジタルトランスフォーメーション(DX)の実現を目指す請負開発型のコンサルティングサービスです。AI、iPaaS、および先端の技術を駆使して、製造プロセスの効率化、業務効率化、チームワーク強化、コスト削減、品質向上を実現します。このサービスは、製造業の課題を深く理解し、それに対する最適なデジタルソリューションを提供することで、企業が持続的な成長とイノベーションを達成できるようサポートします。
オンライン講座
製造業、主に購買・調達部門にお勤めの方々に向けた情報を配信しております。
新任の方やベテランの方、管理職を対象とした幅広いコンテンツをご用意しております。
お問い合わせ
コストダウンが利益に直結する術だと理解していても、なかなか前に進めることができない状況。そんな時は、newjiのコストダウン自動化機能で大きく利益貢献しよう!
(Β版非公開)