- お役立ち記事
- Enhancing Manufacturing DX: Innovations in Tear Strength Measurement Techniques
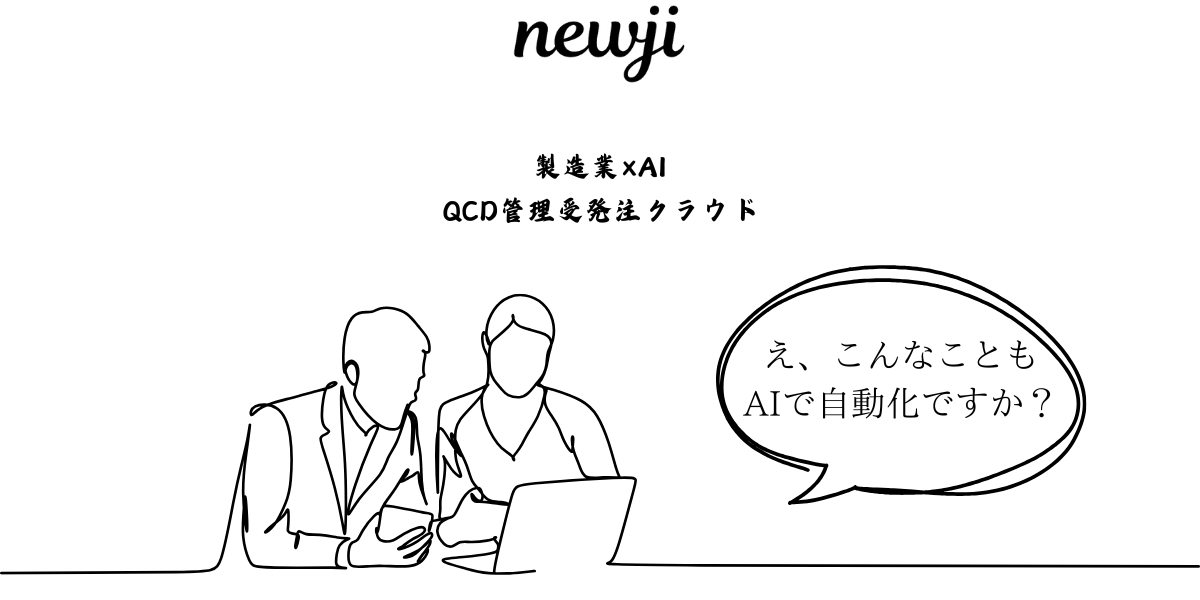
Enhancing Manufacturing DX: Innovations in Tear Strength Measurement Techniques
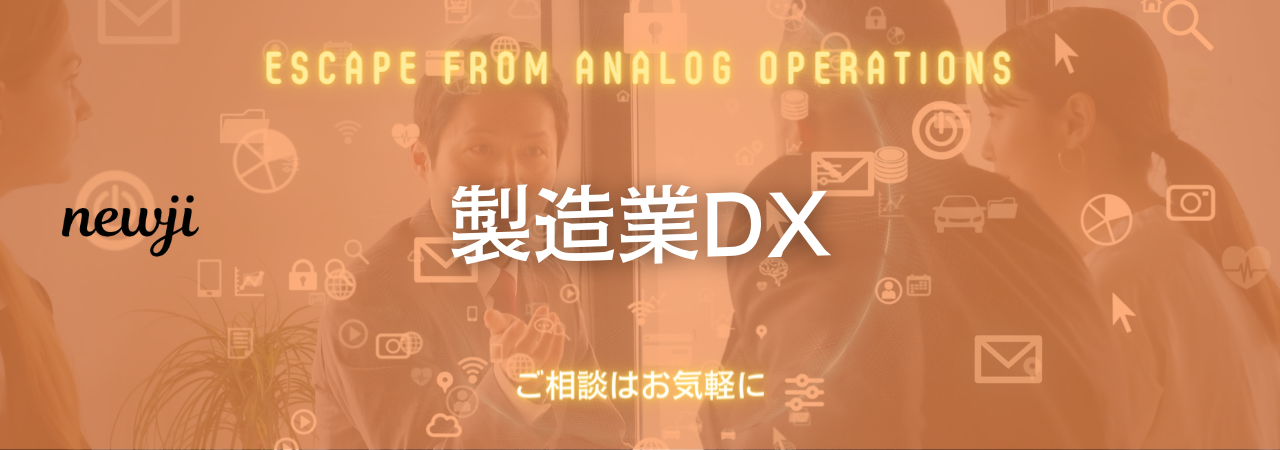
目次
はじめに
製造業におけるデジタルトランスフォーメーション(DX)は、企業の競争力を維持・向上させるための不可欠な戦略となっています。DXの推進により、生産プロセスの効率化、品質管理の高度化、コスト削減など多岐にわたるメリットが享受できるようになります。その中でも、品質管理の一環として重要な役割を果たすのが「テア強度測定」です。テア強度測定技術の革新は、製造DXを更に進化させる鍵となっています。本記事では、「Enhancing Manufacturing DX: Innovations in Tear Strength Measurement Techniques」というテーマに基づき、テア強度測定技術の最新動向、メリット・デメリット、具体的な事例などを現場目線で詳しく解説します。
製造DX(デジタルトランスフォーメーション)とは
製造DXとは、デジタル技術を活用して製造業のプロセスやビジネスモデルを根本的に変革し、競争力を高める取り組みを指します。具体的には、IoT(モノのインターネット)、ビッグデータ解析、AI(人工知能)、クラウドコンピューティングなどの先端技術を導入し、生産現場から経営層に至るまでの全ての業務をデジタル化・最適化することを目指します。
- スマートファクトリーの構築: IoTデバイスやセンサーを活用し、リアルタイムで生産データを収集・分析。これにより、生産ラインの稼働状況を常時監視し、効率的な運用を実現します。
- ビッグデータとAIの活用: 大量の生産データを解析し、異常検知や予知保全、需要予測などに活用。AIが分析結果を基に最適な意思決定を支援します。
- サプライチェーンのデジタル化: 調達から製造、配送までのサプライチェーン全体をデジタルで管理し、効率化と透明性の向上を図ります。
- 新製品開発の迅速化: デジタルツールを活用して迅速にプロトタイプを作成・テストし、市場投入までのリードタイムを短縮します。
製造DXは、単に技術を導入するだけでなく、組織全体の文化や業務プロセスの見直しを伴い、継続的なイノベーションを促進します。これにより、競争が激化する市場環境においても柔軟に対応し、持続的な成長を実現することが可能となります。
テア強度測定の重要性
テア強度測定は、材料や製品が裂ける際の抵抗力を評価する試験であり、製造業において極めて重要な役割を果たします。以下に、テア強度測定の重要性について詳しく説明します。
製品の信頼性向上
テア強度が高い製品は、使用中に裂けにくく、長期間にわたって性能を維持します。これは特に包装材、フィルム、繊維製品などにおいて重要です。例えば、食品包装材のテア強度が高いほど、輸送や保管中の破損リスクが低減し、製品の品質を守ることができます。
安全性の確保
自動車部品や航空機部品など、製品の安全性が直接関わる分野では、テア強度測定が欠かせません。例えば、自動車のシートベルトやエアバッグの素材は、高いテア強度が求められます。これにより、事故発生時に確実に機能し、乗員の安全を確保します。
コスト削減と品質向上
テア強度測定を適切に行うことで、不良品の発生を抑制し、材料の無駄を減少させることができます。これにより、再加工や廃棄に伴うコスト削減と同時に、製品の品質向上を図ることが可能です。また、製品の信頼性が向上することで、顧客満足度の向上にも寄与します。
規制遵守と市場要求への対応
多くの産業分野では、製品の強度や耐久性に関する規制が存在します。これらの規制を満たすためには、正確なテア強度測定が必須です。また、消費者や市場からの要求も日々高まっており、製品の品質管理の重要性が増しています。テア強度測定技術の進化により、これらの要求に迅速かつ的確に対応することが可能となります。
テア強度測定技術の最新動向
テア強度測定技術は、製造DXの進展とともに大きく進化しています。以下に、現在注目されている最新の技術動向を紹介します。
従来の測定技術
従来のテア強度測定は、主に物理的な試験機を用いて行われます。代表的な方法には、ASTM(アメリカ材料試験協会)やJIS(日本工業規格)で定められた標準試験方法があります。これらの方法では、材料試片に一定の引張力を加え、裂けるまでの力を測定します。手動での操作や半自動的な測定が一般的であり、測定速度が遅く、人為的な誤差が発生しやすいという課題がありました。
最新の非破壊検査技術
近年では、非破壊検査技術(Non-Destructive Testing: NDT)が注目されています。これにより、製品を破壊することなく内部の特性を評価し、品質を確保することが可能となります。具体的な技術としては、以下のものが挙げられます。
- 画像解析技術: 高解像度カメラや光学センサーを用いて、材料表面や内部の微細な欠陥を検出します。画像解析ソフトウェアが自動で裂け目や亀裂を識別し、テア強度の予測に活用されます。
- 超音波検査: 超音波を使用して材料内部の欠陥を検出します。超音波の反射特性を解析することで、内部の応力状態や欠陥の有無を評価します。
- レーザー測定技術: レーザーを用いた非接触測定により、材料表面や内部の形状変化を高精度に捉えます。これにより、裂ける前の微小な変形を検出し、テア強度の評価に役立てます。
これらの非破壊検査技術の導入により、製品の品質を高精度かつ迅速に評価することが可能となり、製造プロセス全体の効率化と品質向上が実現します。
AIと機械学習の活用
AI(人工知能)と機械学習の進展により、テア強度測定技術も大きな変革を遂げています。これらの技術を活用することで、測定データの解析や異常検知の精度が飛躍的に向上します。具体的には以下のような応用が行われています。
- データの自動解析: AIが大量の測定データを自動で解析し、テア強度の分布や傾向をリアルタイムで把握します。これにより、人手によるデータ整理や分析の手間が省かれます。
- 異常検知と予測: 機械学習アルゴリズムを用いて製造プロセスにおける異常なパターンを検出します。これにより、不良品の早期発見や予防が可能となり、製品品質の安定化に寄与します。
- 予知保全: 測定データや設備の運用データを基に、機械や設備の故障を予知します。これにより、計画的なメンテナンスが可能となり、生産ラインのダウンタイムを最小限に抑えることができます。
AIと機械学習の導入により、テア強度測定は単なる品質確認の手段から、製造プロセス全体の最適化を支援する戦略的なツールへと進化しています。
製造DXにおけるテア強度測定のメリット
最新のテア強度測定技術を製造DXに取り入れることで、企業は多くのメリットを享受できます。以下では、その主な利点について詳しく解説します。
生産性の向上
自動化されたテア強度測定システムは、従来の手動測定に比べて測定速度が大幅に向上します。これにより、リアルタイムでの品質検査が可能となり、生産ラインのボトルネックが解消されます。さらに、測定プロセスの自動化により人的ミスが減少し、一貫した測定結果が得られます。その結果、全体的な生産性が向上し、製品の市場投入までのリードタイムが短縮されます。
品質の安定化
AIや機械学習を活用したテア強度測定技術により、測定データのばらつきが抑えられ、品質管理の一貫性が向上します。これにより、製品の品質が安定し、顧客からの信頼を獲得することができます。また、異常検知の精度が向上することで、不良品の早期発見・対応が可能となり、全体的な品質向上に寄与します。
コスト削減
最新のテア強度測定技術の導入により、測定プロセスの効率化が図られます。これにより、人的コストや時間の削減が可能となります。また、測定精度の向上により、不良品の発生率が低減され、再加工や廃棄に伴うコストも削減されます。さらに、予知保全の導入により、設備の故障を未然に防ぎ、メンテナンスコストの最適化が実現します。
データ活用による意思決定の最適化
テア強度測定から得られる大量のデータは、製造プロセスの改善や新製品開発において貴重な情報源となります。ビッグデータ解析やAIを活用することで、データから有用な洞察を抽出し、経営層や現場の意思決定を支援します。これにより、製造プロセスの継続的な改善や市場ニーズへの迅速な対応が可能となります。
持続可能な製造プロセスの実現
高精度なテア強度測定により、材料の最適な使用量や製造プロセスの効率化が促進されます。これにより、資源の無駄遣いやエネルギー消費を削減し、環境負荷の低減に寄与します。また、品質の安定化により製品寿命が延びることで、持続可能な製造プロセスの構築が可能となります。
テア強度測定技術の課題とデメリット
最新のテア強度測定技術を導入する際には、多くのメリットがある一方で、いくつかの課題やデメリットも存在します。これらを理解し、適切に対処することが成功への鍵となります。
初期導入コスト
最新のテア強度測定システムは、高度な技術を搭載しているため、初期導入コストが高額になることが一般的です。特に中小企業にとっては、資金調達や投資対効果の見極めが重要な課題となります。初期投資の回収には、長期的な視点でのコスト削減効果や生産性向上を見据える必要があります。
技術習得と人材の確保
新しいテア強度測定技術を効果的に活用するためには、専門的な知識やスキルが必要となります。従業員の教育や研修が不可欠であり、そのための時間とコストがかかります。また、最新技術に精通した人材の確保も容易ではない場合があります。企業は、継続的な教育プログラムや外部専門家との連携を通じて、技術の習得と人材の育成を図る必要があります。
データ管理とプライバシーの課題
大量の測定データを効率的に管理・分析するためには、適切なデータ管理システムが必要です。特にクラウドベースのシステムを導入する場合、データのセキュリティやプライバシー保護が重要な課題となります。企業は、データガバナンスポリシーを策定し、適切なセキュリティ対策を講じることで、データの安全性を確保する必要があります。
技術の急速な進化と適応
テア強度測定技術は急速に進化しており、新しい技術やツールが次々と登場しています。これに迅速に適応し、最新技術を導入し続けることは容易ではありません。技術の選定においては、企業のニーズや既存システムとの互換性、将来的な拡張性を考慮する必要があります。また、技術の陳腐化リスクを見越した長期的な技術戦略を策定することが求められます。
テア強度測定技術の導入事例
実際に最新のテア強度測定技術を導入し、製造DXを推進している企業の事例を紹介します。これにより、具体的な導入効果や成功要因を理解することができます。
事例1: 自動車部品メーカーの成功例
ある大手自動車部品メーカーでは、従来の手動測定に依存していたテア強度測定を、最新のAI搭載自動測定システムに刷新しました。このシステムは、製造ラインに設置されたセンサーとカメラを通じて、製品のテア強度をリアルタイムで測定・分析します。導入後、以下のような成果を得ることができました。
- 測定速度の向上: 従来の手動測定に比べ、測定時間が70%短縮され、ラインのスループットが向上しました。
- 品質の安定化: AIアルゴリズムによる異常検知により、製品のばらつきが減少し、品質が安定しました。
- コスト削減: 不良品の削減により、再加工費用や廃棄コストが年間で約15%削減されました。
- 生産ラインの柔軟性向上: リアルタイムデータの活用により、生産ラインの調整が迅速に行えるようになり、多様な製品ニーズに対応可能となりました。
この成功により、同社は生産効率の向上とコスト削減を実現し、競争力を大幅に強化することができました。また、AIの導入によりデータドリブンな意思決定が可能となり、継続的なプロセス改善が容易になりました。
事例2: 繊維業界におけるDX活用
繊維業界のある企業では、製品のテア強度に対する厳しい品質要求を満たすため、最新の非破壊検査技術とクラウドベースのデータ管理システムを導入しました。具体的な取り組みと成果は以下の通りです。
- 非破壊検査技術の導入: レーザー測定技術を導入し、製品の表面変形を高精度で測定。これにより、製品の損傷リスクを最小限に抑えることができました。
- クラウドデータ管理の採用: 測定データをリアルタイムでクラウドに保存・共有する仕組みを構築。生産現場と品質管理部門間での情報共有が円滑になり、迅速な意思決定が可能となりました。
- データ分析による品質向上: クラウド上のデータをビッグデータ分析ツールで解析し、製造プロセスのボトルネックや改善点を特定。これにより、製造工程の最適化と製品品質の向上を達成しました。
- 市場対応力の強化: データに基づく迅速な生産調整により、市場の需要変動に柔軟に対応できるようになりました。これにより、顧客満足度の向上と市場での競争力強化が実現しました。
この導入により、同社は製品の品質向上と生産効率の最適化を同時に達成し、市場での競争優位性を確固たるものとしました。また、クラウドベースのデータ管理により、グローバルな製造拠点間での情報共有が容易となり、国際的な競争環境にも適応できるようになりました。
今後の展望と結論
テア強度測定技術の革新は、製造DXの推進において極めて重要な要素となっています。最新技術の導入により、製品の品質向上や生産効率の改善が可能となり、企業の競争力強化に直結します。しかし、一方で初期導入コストや技術習得といった課題も存在します。これらの課題を克服し、最新技術を効果的に活用するためには、企業全体での戦略的なアプローチが必要です。
今後、テア強度測定技術はさらに進化し、より高精度で迅速な測定が可能となるでしょう。AIやIoTのさらなる発展により、測定データのリアルタイム解析や予測モデルの精度向上が期待されます。また、クラウド技術の普及により、製造現場と経営層との連携が強化され、データドリブンな意思決定が一層推進されるでしょう。
製造業においては、テア強度測定技術を積極的に導入・活用することで、品質管理の高度化と生産効率の向上を図ることができます。これにより、競争が激化する市場環境においても持続可能な成長を実現することが可能となります。企業は、最新技術の動向を常に把握し、柔軟かつ戦略的にDXを推進することで、未来に向けた強固な基盤を築いていく必要があります。
製造DXの成功は、単に技術を導入するだけではなく、組織全体での文化変革や継続的な改善活動の継続が不可欠です。テア強度測定技術の革新を活用し、製品の品質を保証するとともに、効率的な生産プロセスを構築することで、企業は持続的な成長と市場での優位性を確立することができるでしょう。
資料ダウンロード
QCD調達購買管理クラウド「newji」は、調達購買部門で必要なQCD管理全てを備えた、現場特化型兼クラウド型の今世紀最高の購買管理システムとなります。
ユーザー登録
調達購買業務の効率化だけでなく、システムを導入することで、コスト削減や製品・資材のステータス可視化のほか、属人化していた購買情報の共有化による内部不正防止や統制にも役立ちます。
NEWJI DX
製造業に特化したデジタルトランスフォーメーション(DX)の実現を目指す請負開発型のコンサルティングサービスです。AI、iPaaS、および先端の技術を駆使して、製造プロセスの効率化、業務効率化、チームワーク強化、コスト削減、品質向上を実現します。このサービスは、製造業の課題を深く理解し、それに対する最適なデジタルソリューションを提供することで、企業が持続的な成長とイノベーションを達成できるようサポートします。
オンライン講座
製造業、主に購買・調達部門にお勤めの方々に向けた情報を配信しております。
新任の方やベテランの方、管理職を対象とした幅広いコンテンツをご用意しております。
お問い合わせ
コストダウンが利益に直結する術だと理解していても、なかなか前に進めることができない状況。そんな時は、newjiのコストダウン自動化機能で大きく利益貢献しよう!
(Β版非公開)