- お役立ち記事
- 製造業DX革命: 故障解析で生産効率とコスト削減を実現する方法
月間76,176名の
製造業ご担当者様が閲覧しています*
*2025年3月31日現在のGoogle Analyticsのデータより
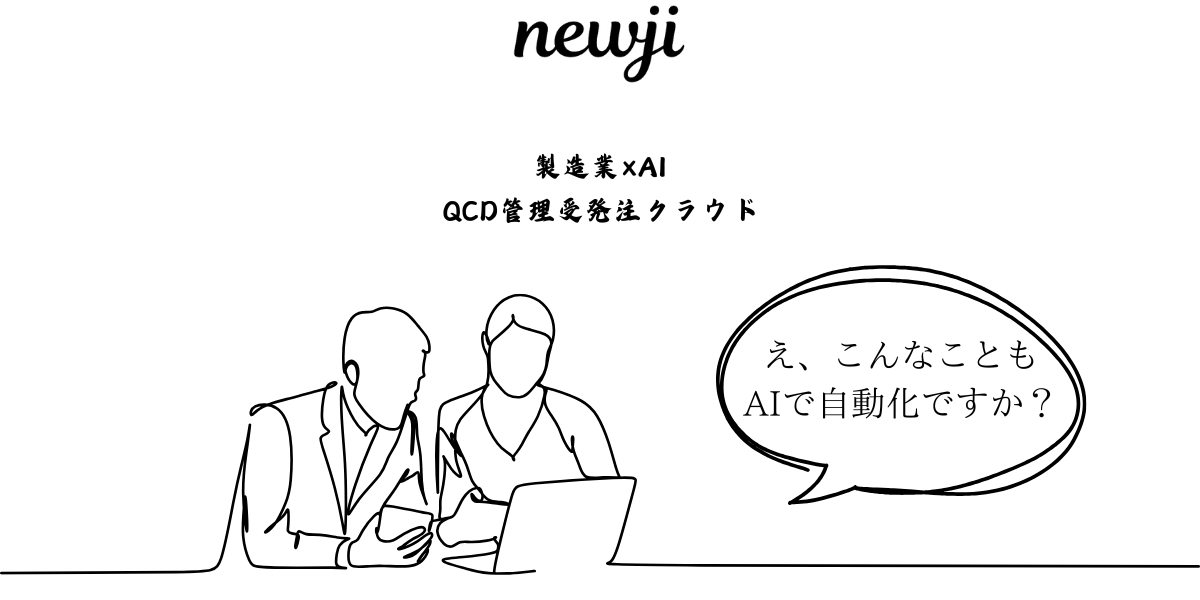
製造業DX革命: 故障解析で生産効率とコスト削減を実現する方法
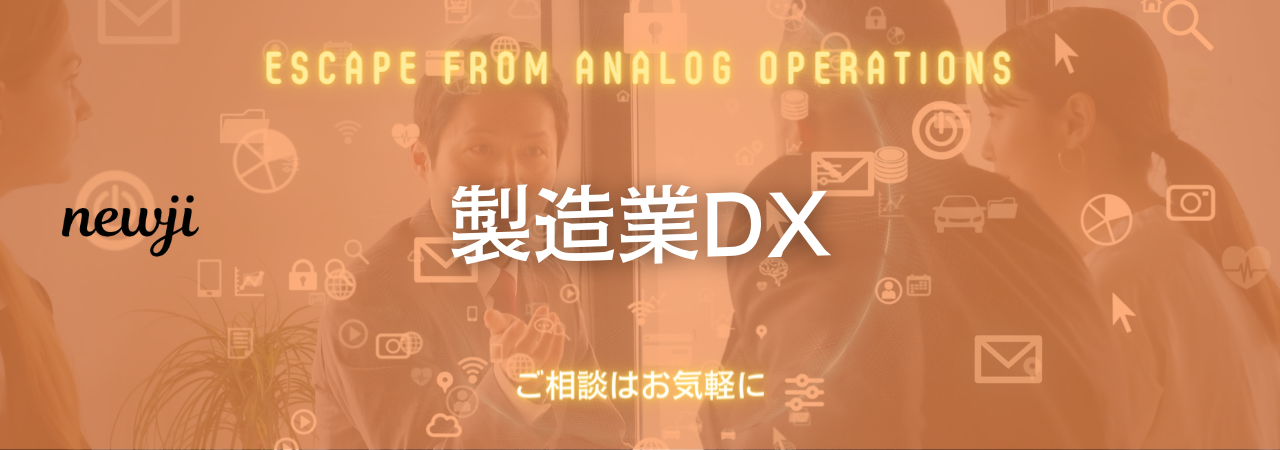
目次
製造業DX革命: 故障解析で生産効率とコスト削減を実現する方法
製造業が直面する多くの課題の一つに、機械の故障があります。これによって生産が停止し、それに伴うコスト増加や生産遅延といった問題が発生します。製造業のデジタルトランスフォーメーション(DX)は、そのような課題を解決するための強力なツールです。本記事では、製造業の現場で培った知識や経験を基に、DXを活用した故障解析による生産効率の向上とコスト削減の方法について解説します。
故障解析の重要性
生産停止の影響
製造業では、設備や機械の故障が生産ラインの停止を引き起こす要因の一つです。このような停止は、製品の納期遅延や追加の労務費用、部品交換費用など、さまざまなコストを引き起こします。生産ラインが停止した場合、預かりのある注文は遅れ、顧客満足度に影響を与えます。
予防保全と事後対応の違い
故障解析は予防保全と事後対応の両面で重要な役割を果たします。予防保全では、故障の兆候を事前に察知し、計画的なメンテナンスを行うことで故障を未然に防ぐことが目的です。一方、事後対応では、故障が発生した原因を迅速に特定し、再発防止策を講じることが求められます。
DXによる故障解析のアプローチ
IoTセンサーによるデータ収集
IoT(Internet of Things)センサーは、機械や設備の状態をリアルタイムで監視するための強力なツールです。温度、振動、圧力などのデータを収集するセンサーを設備に取り付けることで、異常が発生する前兆を察知することが可能です。また、定期的なデータ収集により、傾向を把握し、予防保全の計画を立てることができます。
ビッグデータ分析
IoTセンサーから収集したデータは膨大な量になります。これを効率的に解析するためには、ビッグデータ分析が不可欠です。機械学習アルゴリズムを活用することで、過去のデータから故障のパターンを発見し、異常検知の精度を向上させることができます。例えば、同じタイプの故障が多発する機械や部品があれば、それを重点的に監視することで予防保全の効果が高まります。
クラウドコンピューティングの活用
収集したデータを効率的に管理・解析するためには、クラウドコンピューティングの活用が有効です。クラウド上でデータを一元管理することで、必要な情報に迅速にアクセスできるほか、解析結果を関係者と容易に共有することができます。これにより、異常が検知された際の迅速な対応が可能となります。
具体的な導入事例
自動車部品メーカーの事例
ある自動車部品メーカーでは、生産ラインにIoTセンサーを導入し、クラウド上でデータを分析する体制を整えました。これにより、機械の振動データが異常値を示した際にアラートが発信され、故障が発生する前に適切なメンテナンスが行われるようになりました。この結果、予期せぬ生産停止が大幅に減少し、生産効率が向上しました。
電子機器製造業の事例
電子機器製造業では、機械学習を活用した故障予測モデルを構築しました。このモデルは過去の故障データを基にしており、新たなデータが入力されるたびに精度が向上します。具体的には、製造ラインで使用するロボットアームの動作データから異常を検出し、故障の予兆を事前に察知するためのシステムが導入されました。これにより、計画外のダウンタイムが減少し、メンテナンス費用の削減にも成功しました。
メリットとデメリット
メリット
1. **生産効率の向上**: 故障を未然に防ぐことで生産ラインの停止が減少し、効率的な生産が可能になります。
2. **コスト削減**: 故障による緊急対応や部品交換などのコストが削減されます。また、計画的なメンテナンスが可能になるため、長期的にもコスト削減に繋がります。
3. **迅速な対応**: 異常が検知された際に迅速に対応することができ、被害を最小限に抑えることができます。
4. **データに基づく意思決定**: データを活用した解析により、根拠のある意思決定が可能になります。
デメリット
1. **初期投資の高さ**: IoTセンサーの設置やシステム構築にかかるコストが高いため、初期投資が必要です。
2. **データ管理の複雑さ**: 膨大なデータを効率的に管理・解析するためには、専門知識が必要です。
3. **サイバーセキュリティリスク**: データをクラウド上で管理するため、サイバーセキュリティリスクが増加します。
最新技術動向
AIと機械学習の進化
AIと機械学習の進化により、故障解析の精度はさらに向上しています。最新のアルゴリズムは、異常検知の速度と精度を大幅に改善しており、故障の予測には欠かせないツールとなっています。また、深層学習を導入することで、より複雑な解析が可能となり、異常の早期発見が期待されています。
デジタルツインの活用
デジタルツインは、物理的な製品やシステムをデジタル上で再現する技術です。これにより、実際の設備や機械の動作をシミュレーションし、故障の予兆を事前に把握することができます。例えば、製造ライン全体のデジタルツインを構築することで、どの部分でトラブルが発生する可能性が高いかを予測し、適切な対策を講じることができます。
導入のためのステップ
基本計画の策定
故障解析の導入を検討する際には、まず基本計画を策定することが重要です。対象となる設備や機械の現状を把握し、どのようなデータを収集すべきかを明確にしましょう。
必要な技術の選定
IoTセンサー、クラウドコンピューティング、機械学習アルゴリズムなど、必要な技術を選定します。導入にあたっては、専門知識を持つパートナー企業と協力することが推奨されます。
パイロットプロジェクトの実施
全体的な導入前に、まずは限られた範囲でパイロットプロジェクトを実施しましょう。これにより、システムの性能や効果を実際に確認することができます。また、改善点を洗い出し、全体導入の際に反映させることが可能です。
本格導入とフィードバック
パイロットプロジェクトで得られた知見を基に、本格的な導入を進めます。また、導入後も定期的なフィードバックを行い、システムの最適化を図ることが重要です。
まとめ
製造業におけるDXの故障解析は、生産効率の向上とコスト削減に大きく貢献します。IoTセンサーやクラウドコンピューティング、機械学習などの最新技術を活用することで、予期せぬ生産停止を未然に防ぎ、効率的な生産が可能になります。ただし、初期投資やデータ管理、セキュリティ面の課題についても十分に考慮する必要があります。
これらのステップを踏み、故障解析の導入を進めることで、より競争力のある製造業が実現できるでしょう。未来の製造業をリードするために、今回ご紹介した技術と方法をぜひ参考にしてください。
資料ダウンロード
QCD管理受発注クラウド「newji」は、受発注部門で必要なQCD管理全てを備えた、現場特化型兼クラウド型の今世紀最高の受発注管理システムとなります。
ユーザー登録
受発注業務の効率化だけでなく、システムを導入することで、コスト削減や製品・資材のステータス可視化のほか、属人化していた受発注情報の共有化による内部不正防止や統制にも役立ちます。
NEWJI DX
製造業に特化したデジタルトランスフォーメーション(DX)の実現を目指す請負開発型のコンサルティングサービスです。AI、iPaaS、および先端の技術を駆使して、製造プロセスの効率化、業務効率化、チームワーク強化、コスト削減、品質向上を実現します。このサービスは、製造業の課題を深く理解し、それに対する最適なデジタルソリューションを提供することで、企業が持続的な成長とイノベーションを達成できるようサポートします。
製造業ニュース解説
製造業、主に購買・調達部門にお勤めの方々に向けた情報を配信しております。
新任の方やベテランの方、管理職を対象とした幅広いコンテンツをご用意しております。
お問い合わせ
コストダウンが利益に直結する術だと理解していても、なかなか前に進めることができない状況。そんな時は、newjiのコストダウン自動化機能で大きく利益貢献しよう!
(β版非公開)