- お役立ち記事
- FMEAを活用して製造業の営業力を飛躍的に高める方法
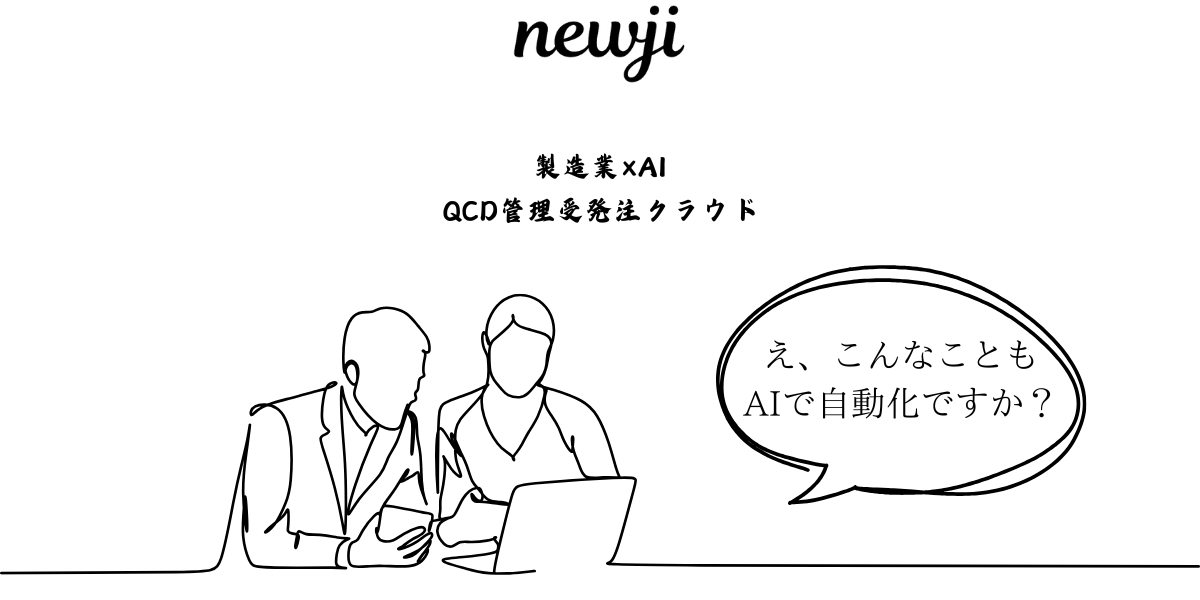
FMEAを活用して製造業の営業力を飛躍的に高める方法
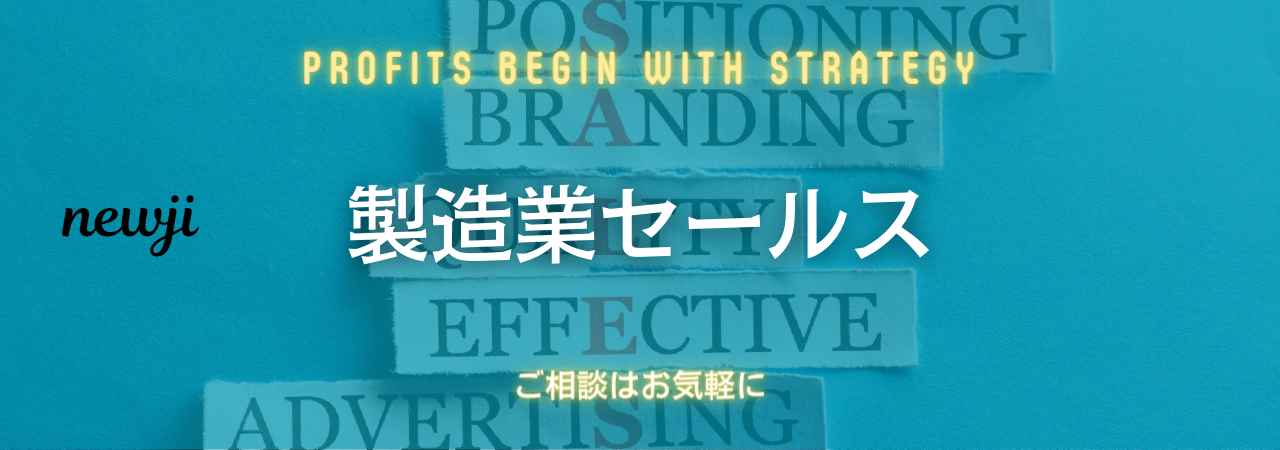
目次
FMEAとは何か?製造業における基礎知識
FMEA(Failure Mode and Effects Analysis)は、日本語で「故障モード影響解析」とも呼ばれ、設計や製造プロセスにおける潜在的な故障を事前に解析し、その影響やリスクを評価・軽減するための手法です。
多くの製造業者が品質向上、コスト削減、リスク管理を目指してFMEAを導入しています。
FMEAのメリット
1. リスクの早期発見と軽減
FMEAを活用することで、製造プロセスや製品の設計段階で潜在的な故障や問題を事前に特定できます。
これにより、問題が発生する前に適切な対策を講じることが可能になります。
2. 品質向上
品質管理の一環としてFMEAを取り入れることで、製品やプロセスの信頼性を向上させることができます。
これは顧客満足度の向上にもつながります。
3. コスト削減
問題が発生してからの修正には多大なコストと時間がかかります。
事前に問題を発見し対策を講じることで、コストを大幅に削減できます。
FMEAのデメリット
1. 導入コストと時間
FMEAの導入には初期投資が必要です。
専門知識を持つ人材の確保やトレーニング、ツールの購入にかかるコストと時間を見越す必要があります。
2. 適切な実行が難しい
FMEAは体系的な手法であるため、適切に実行するためには高い専門知識と経験が必要です。
誤った評価や対応が行われた場合、効果が薄れてしまう可能性があります。
FMEAの具体的な活用方法
1. チーム構成
FMEAを効果的に実施するためには、設計、製造、品質管理などの各部門から専門的な知識を持つメンバーを集めたクロスファンクショナルチームを構成することが重要です。
2. 潜在的な故障モードの特定
まず、製品やプロセスにおける故障の可能性がある箇所を洗い出します。
過去のデータや経験を基に、どのような故障が発生する可能性があるかをリストアップします。
3. 故障の影響評価
次に、それぞれの故障が発生した場合の影響を評価します。
評価には、故障の発生頻度、検出の可能性、影響の深刻度などを考慮します。
4. リスクの優先順位付け
評価が完了したら、各故障箇所のリスクを数値化し、優先順位を付けます。
これにより、最もリスクが高い箇所から優先的に対策を講じることができます。
5. 改善策の立案と実行
優先度の高いリスクに対して、具体的な改善策を立案し、実施します。
改善策の効果を定期的に評価し、必要に応じて見直しを行います。
FMEA活用の成功事例
製造業の現場でFMEAを活用した成功事例をいくつか紹介します。
自動車部品メーカーの事例
ある自動車部品メーカーでは、エンジンの設計段階でFMEAを活用しました。
エンジンの冷却システムに関する潜在的な故障を事前に特定し、対策を講じることで、エンジンの品質と信頼性を向上させました。
これにより、製品リコールのリスクを大幅に低減し、顧客からの信頼を確保しました。
電子機器メーカーの事例
ある電子機器メーカーでは、新製品の開発プロセスにFMEAを導入しました。
製造ラインでの潜在的な問題を事前に洗い出し、迅速に対応することで、製品の不良率を大幅に削減しました。
結果として、製造コストの削減と納期の短縮を実現し、競争力を強化しました。
最新技術を活用したFMEAの進化
近年では、デジタル技術の進化に伴い、FMEAも大きな進化を遂げています。
以下にその一部を紹介します。
1. AIとデータ分析の導入
人工知能(AI)やビッグデータを用いることで、より正確かつ迅速なリスク評価が可能になっています。
過去のデータを解析し、故障の発生確率や影響を高精度で予測することができます。
2. クラウドベースのFMEAツール
クラウドベースのFMEAツールを活用することで、チーム間の情報共有が容易になります。
リアルタイムでのデータ更新が可能となり、迅速な対応を実現できます。
3. IoTによるリアルタイムモニタリング
IoT技術を活用することで、製造ラインや機器の状態をリアルタイムで監視することができます。
異常を即座に検知し、迅速な対応が可能になります。
FMEAを活用するためのステップバイステップガイド
ステップ1: 目的と範囲の設定
最初に、FMEAの対象となる製品やプロセスの目標と範囲を明確に設定します。
これにより、リスク評価の焦点が定まります。
ステップ2: チームの構成
適切な専門知識を持つメンバーで構成されたクロスファンクショナルチームを結成します。
各メンバーの役割と責任を明確にします。
ステップ3: 故障モードの特定とリストアップ
製品やプロセスの各ステップにおける潜在的な故障モードを洗い出し、リストアップします。
過去の故障事例や設計仕様書を参考にします。
ステップ4: 故障の影響評価
次に、故障モードの影響を評価します。
影響の深刻度、発生頻度、検出の可能性を数値化し、リスク優先度数(RPN)を算出します。
ステップ5: 改善策の立案
優先度の高いリスクに対して具体的な対策を立案し、実施します。
これには設計変更、製造プロセスの見直し、監視体制の強化などが含まれます。
ステップ6: フィードバックと継続改善
改善策の効果を継続的にモニタリングし、必要に応じて追加対策を講じます。
フィードバックをもとにFMEAを更新し、継続的な改善を図ります。
まとめ
FMEAを活用することで、製造業におけるリスク管理、品質向上、コスト削減が可能になります。
導入には初期コストと専門知識が必要ですが、長期的な視点で見れば非常に有益な手法です。
最新の技術を活用しながら、適切に運用することで、更なる効果を発揮することができます。
製造業の営業力を飛躍的に高めるために、是非FMEAを積極的に活用してみてください。
資料ダウンロード
QCD調達購買管理クラウド「newji」は、調達購買部門で必要なQCD管理全てを備えた、現場特化型兼クラウド型の今世紀最高の購買管理システムとなります。
ユーザー登録
調達購買業務の効率化だけでなく、システムを導入することで、コスト削減や製品・資材のステータス可視化のほか、属人化していた購買情報の共有化による内部不正防止や統制にも役立ちます。
NEWJI DX
製造業に特化したデジタルトランスフォーメーション(DX)の実現を目指す請負開発型のコンサルティングサービスです。AI、iPaaS、および先端の技術を駆使して、製造プロセスの効率化、業務効率化、チームワーク強化、コスト削減、品質向上を実現します。このサービスは、製造業の課題を深く理解し、それに対する最適なデジタルソリューションを提供することで、企業が持続的な成長とイノベーションを達成できるようサポートします。
オンライン講座
製造業、主に購買・調達部門にお勤めの方々に向けた情報を配信しております。
新任の方やベテランの方、管理職を対象とした幅広いコンテンツをご用意しております。
お問い合わせ
コストダウンが利益に直結する術だと理解していても、なかなか前に進めることができない状況。そんな時は、newjiのコストダウン自動化機能で大きく利益貢献しよう!
(Β版非公開)