- お役立ち記事
- QC7つ道具の基礎をマスターして効果的な提案を実現
月間76,176名の
製造業ご担当者様が閲覧しています*
*2025年3月31日現在のGoogle Analyticsのデータより
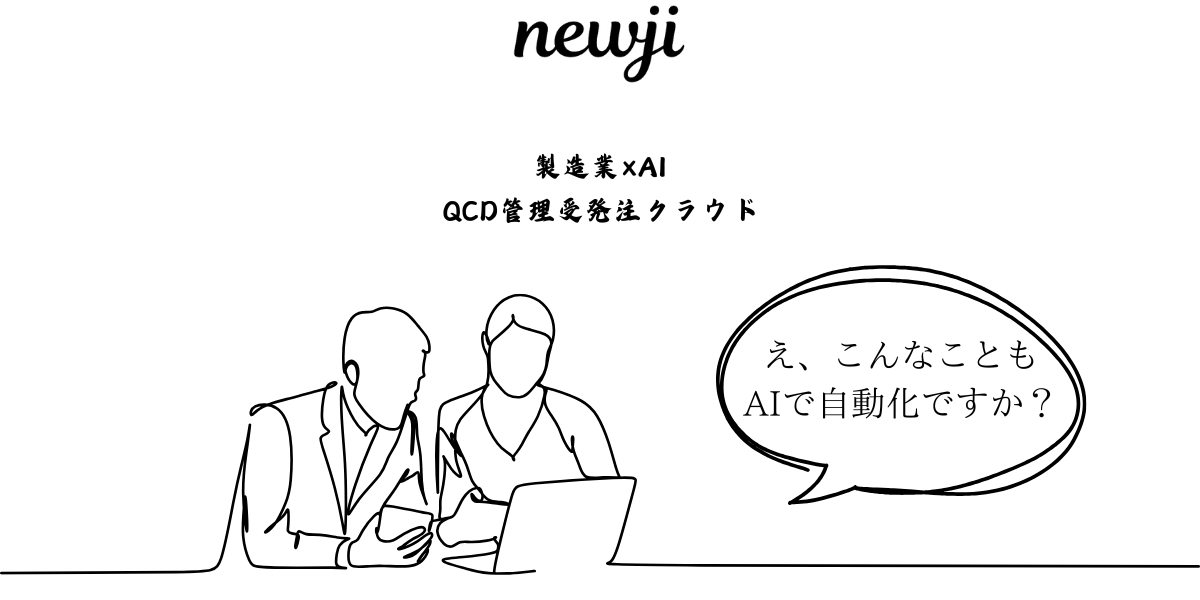
QC7つ道具の基礎をマスターして効果的な提案を実現
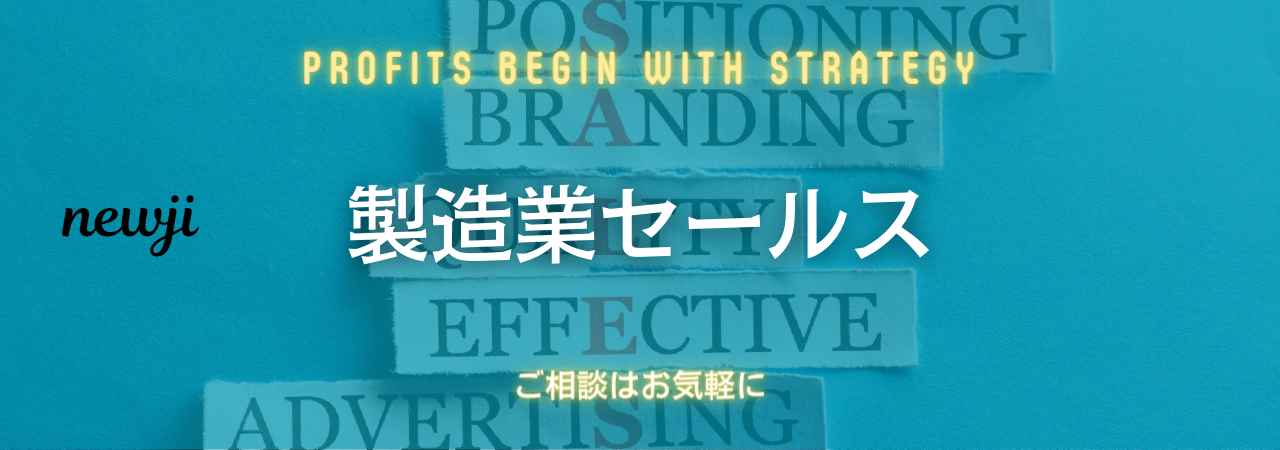
目次
QC7つ道具とは?
製造業の現場では、品質管理が非常に重要な役割を担っています。
QC7つ道具は、その品質管理を効果的に行うための基本的な手法として広く利用されています。
具体的には、1) パレート図、2) 特性要因図(フィッシュボーンダイアグラム)、3) ヒストグラム、4) 散布図、5) 管理図、6) チェックシート、7) 層別の7つです。
これらのツールを使うことによって、問題の根本原因を特定し、効果的な改善提案を行うことが可能です。
パレート図で重要な問題を特定
パレート図は、問題の発生頻度や影響度を視覚的に把握するためのグラフです。
この図を用いることで、全体の中でどの要因が最も大きな問題であるかを容易に特定できます。
80対20の法則としても知られるパレートの法則に基づき、少数の重要な要因が多数の問題を引き起こしていることが多いため、パレート図は優先順位を決める際に非常に有効です。
実際のデータを元にパレート図を作成し、リソースを最も影響の大きい問題の解決に集中させることが重要です。
パレート図の作成手順
1. 解決する問題のカテゴリをリスト化します。
2. 各カテゴリの発生頻度や問題の影響度を集計します。
3. 発生頻度や影響度の大きい順に並べ替えます。
4. 累積度数を計算し、百分率に変換します。
5. 横軸にカテゴリ、縦軸の一方に発生頻度や影響度、もう一方に累積百分率を配置してグラフを描きます。
特性要因図で根本原因を洗い出す
特性要因図(フィッシュボーンダイアグラム)は、問題の根本原因を探るために用いられます。
骨の形をした図に問題の特性(結果)とその要因を整理することで、どの因子が結果にどのように影響を与えているかを視覚的に把握できます。
これにより、問題を解決するための具体的なアクションプランを策定することができます。
特性要因図の作成手順
1. 解決したい問題を特性としてチャートの右側に記入します。
2. 特性に影響を与えると考えられる主要な要因を分岐線上に記入します。
(一般的に「人」「機械」「材料」「方法」といったカテゴリで分類します)
3. 各主要因に対して、更なる要素を分岐して記入します。
4. 可能な限り細かく要素を分解し、影響を与えるすべての要素を特定します。
ヒストグラムでデータの分布を分析
ヒストグラムは、データの分布状況を視覚的に表現するためのグラフです。
品質管理においては、製品の仕上がりや寸法などが所定の規格内に収まっているかを確認する際に用います。
この図を用いることで、データがどのように広がっているか、偏りがないか、異常値が含まれていないかを確認することができます。
ヒストグラムの作成手順
1. 測定したデータを並べ替えます。
2. データ範囲を数区間に分割します。
3. 各区間に属するデータの数をカウントします。
4. 横軸に区間、縦軸に度数を設定し、長方形の棒を描きます。
散布図で変数間の関係を把握
散布図は、二つの変数間の関係性を視覚的に示すためのグラフです。
製造業では品質に影響を及ぼす要因が多様に存在するため、各要因の間にどのような関連性があるかを把握するのに役立ちます。
例えば、製品の重量と製造ラインの速度との関係などを評価することが可能です。
散布図の作成手順
1. 二つの関連する変数の値を取得します。
2. 横軸に一つの変数、縦軸にもう一つの変数を設定します。
3. 各データポイントをプロットし、変数間の関係性を視覚的に確認します。
管理図でプロセスの安定性を確認
管理図は、製造プロセスの安定性や異常を検出するためのツールです。
一定期間のデータを集計し、平均値や管理限界線を計算してグラフにプロットします。
これにより、プロセスが安定しているか、何らかの問題により正常な範囲を超えていないかを検査できます。
管理図の作成手順
1. プロセスから定期的にデータを収集します。
2. データの平均値を計算します。
3. 管理限界線を設定します(通常、±3σを用います)。
4. 平均値と管理限界線を含むグラフにデータをプロットします。
チェックシートでデータ収集の効率化
チェックシートは、現場でのデータ収集を簡単かつ効率的に行うための方法です。
特定の問題の発生頻度や時間的なパターンを把握するのに役立ちます。
直接的なデータ収集が難しい場合も、チェックシートを利用することで精確な記録が可能となります。
チェックシートの作成手順
1. データ収集の目的を明確にします。
2. 収集するデータ項目をリスト化します。
3. データ収集のプロセスや時間、担当者を明記したチェックシートを作成します。
4. 現場で日常的にデータを記録します。
層別でデータの背景を理解する
層別は、データを異なるカテゴリーに分け、その中での違いを分析する手法です。
問題の原因を特定のカテゴリに絞り込むことができるため、より詳細な原因分析が可能です。
製造業では、例えば装置ごとの仕上がりのばらつきや操業員ごとの作業品質を分析するなどに使用されます。
層別の実施手順
1. 分析対象のデータを取得します。
2. 分析の目的に応じて適切な層(カテゴリ)を設定します。
3. 各層ごとにデータを整理し、分析します。
4. 得られた結果をもとに改善策を検討します。
QC7つ道具は、製造業における品質管理の基礎として非常に有益なツールです。
これらのツールを適切に使用することで、問題の特定から改善策の提案に至るプロセスがスムーズに進み、効果的な品質改善を実現することが可能です。
各道具の特性を理解し、現場での実践を通じて効果的に活用しましょう。
資料ダウンロード
QCD管理受発注クラウド「newji」は、受発注部門で必要なQCD管理全てを備えた、現場特化型兼クラウド型の今世紀最高の受発注管理システムとなります。
ユーザー登録
受発注業務の効率化だけでなく、システムを導入することで、コスト削減や製品・資材のステータス可視化のほか、属人化していた受発注情報の共有化による内部不正防止や統制にも役立ちます。
NEWJI DX
製造業に特化したデジタルトランスフォーメーション(DX)の実現を目指す請負開発型のコンサルティングサービスです。AI、iPaaS、および先端の技術を駆使して、製造プロセスの効率化、業務効率化、チームワーク強化、コスト削減、品質向上を実現します。このサービスは、製造業の課題を深く理解し、それに対する最適なデジタルソリューションを提供することで、企業が持続的な成長とイノベーションを達成できるようサポートします。
製造業ニュース解説
製造業、主に購買・調達部門にお勤めの方々に向けた情報を配信しております。
新任の方やベテランの方、管理職を対象とした幅広いコンテンツをご用意しております。
お問い合わせ
コストダウンが利益に直結する術だと理解していても、なかなか前に進めることができない状況。そんな時は、newjiのコストダウン自動化機能で大きく利益貢献しよう!
(β版非公開)