- お役立ち記事
- 100. Measures to strengthen cooperation between the manufacturing site and the design department during the prototyping stage
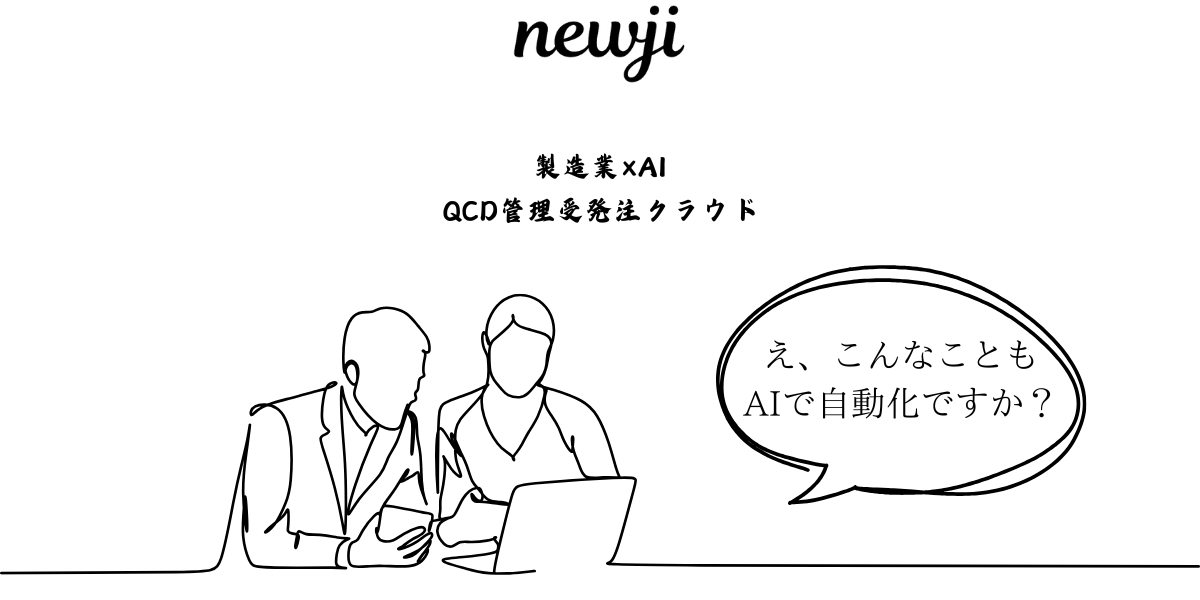
100. Measures to strengthen cooperation between the manufacturing site and the design department during the prototyping stage
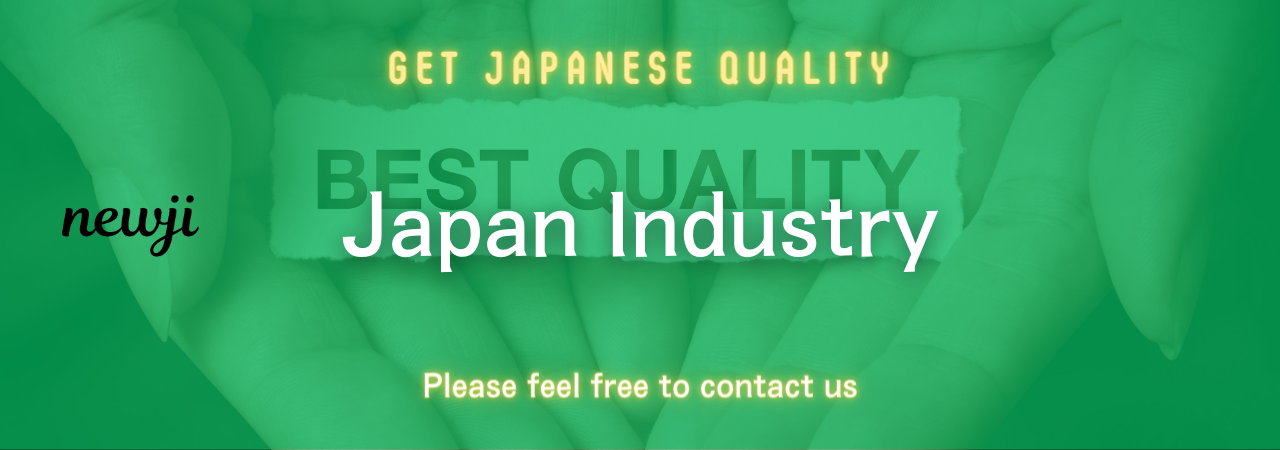
目次
Understanding the Importance of Cooperation
In the realm of manufacturing and design, collaboration is not just beneficial; it’s essential.
The development of a prototype marks a critical intersection where the design department’s vision meets the manufacturing site’s reality.
Without strategic cooperation, even the most brilliant designs can face roadblocks or inefficiencies during production.
Thus, strengthening the synergy between these two departments during the prototyping stage is crucial to the success of a product.
Establishing Clear Communication Channels
At the heart of successful cooperation is clear and open communication.
Manufacturers and designers must establish effective communication channels to ensure that everyone is on the same page.
This can be achieved through regular meetings, shared digital communication platforms, and integrated project management tools.
By facilitating ongoing discussions, departments can quickly resolve issues, brainstorm solutions, and develop a shared understanding of the project goals.
Additionally, fostering a culture of openness encourages team members to voice their concerns and suggestions without hesitation, ultimately leading to more creative and effective solutions.
Implementing Collaborative Technologies
The use of collaborative technologies can greatly enhance the cooperation between manufacturing and design teams.
Software tools that enable real-time updates, virtual simulations, and shared document access can streamline workflows significantly.
These technologies allow design iterations to be reviewed instantly by both sides, with feedback promptly integrated into revisions.
Moreover, virtual simulations enable teams to foresee potential manufacturing issues and address them before they appear in actual production.
Choosing the Right Tools
Selecting the appropriate tools is paramount for effective collaboration.
Look for software that supports both design file formats and production process data.
Platforms that offer features like 3D modeling and virtual prototyping can bridge the gap between theoretical design and practical manufacturing needs.
Training the team to use these tools efficiently will ensure they add value to the prototyping process rather than complicating it.
Developing Cross-Functional Teams
To enhance cooperation during the prototyping phase, forming cross-functional teams can be highly effective.
By embedding members of the design team within the manufacturing team, and vice versa, businesses can cultivate a deeper understanding and appreciation of each other’s roles and challenges.
These teams encourage members to work closely together, allowing them to share insights instantly and consider different perspectives when addressing problems.
This integrated approach minimizes miscommunication and helps maintain a streamlined process from design conception through to prototype production.
Regular Joint Workshops
Conducting regular workshops can also foster unity and improve collaborative efforts.
These workshops can serve as a platform for team members to interact informally, exchange ideas, and learn new skills.
They provide an excellent opportunity for teams to evaluate completed projects and identify areas for improvement, setting the stage for further collaboration and innovation.
Establishing Clear Roles and Responsibilities
A clear delineation of roles and responsibilities prevents confusion and ensures accountability at every step of the prototyping process.
Both departments must have a thorough understanding of their individual and collective responsibilities.
Clearly defined roles ensure that team members know whom to approach for specific issues or approvals, which streamlines decision-making and reduces delays.
Key Responsibility Areas
Before starting a project, outline the key responsibility areas and match them with team members who have the required expertise.
This structured approach allows team members to focus on their strengths while also promoting collaboration where roles overlap.
Setting Tangible, Shared Goals
For successful cooperation, it is important that both the manufacturing site and the design department work towards common objectives.
These shared goals should be realistic and measurable, providing a clear vision for the entire team.
During the prototyping stage, setting milestones can keep the project on track and motivate teams to push towards achievement.
Aligning on these goals fosters a sense of unity and purpose, encouraging team members to collaborate more effectively.
Regular Progress Assessments
Frequent evaluations of the progress towards these goals are essential to ensure that both teams remain aligned and can adjust strategies as needed.
Utilizing project management tools to track progress, identify potential bottlenecks, and facilitate prompt interventions can lead to significant improvements in productivity and morale.
Encouraging a Culture of Continuous Improvement
Finally, developing a culture of continuous improvement can further reinforce cooperation between the manufacturing site and the design department.
Encourage team members to review each project upon completion to understand what worked and what did not.
This feedback loop can lead to incremental improvements in processes, collaboration, and outcomes over time.
Celebrating Successes and Learning from Failures
It’s important to acknowledge successes and learn from failures.
Celebrating achievements fosters a positive working environment, while analyzing setbacks ensures such issues are not repeated in future projects.
Create an atmosphere where team members feel empowered to experiment and innovate, knowing that they are a part of a learning organization that values growth and improvement.
By implementing these measures, the manufacturing site and the design department can enhance their cooperation during the prototyping stage, leading to more successful products and a more efficient production pipeline.
Ultimately, such collaboration not only benefits the teams involved but also helps the company achieve its broader objectives, from innovation to profitability.
資料ダウンロード
QCD調達購買管理クラウド「newji」は、調達購買部門で必要なQCD管理全てを備えた、現場特化型兼クラウド型の今世紀最高の購買管理システムとなります。
ユーザー登録
調達購買業務の効率化だけでなく、システムを導入することで、コスト削減や製品・資材のステータス可視化のほか、属人化していた購買情報の共有化による内部不正防止や統制にも役立ちます。
NEWJI DX
製造業に特化したデジタルトランスフォーメーション(DX)の実現を目指す請負開発型のコンサルティングサービスです。AI、iPaaS、および先端の技術を駆使して、製造プロセスの効率化、業務効率化、チームワーク強化、コスト削減、品質向上を実現します。このサービスは、製造業の課題を深く理解し、それに対する最適なデジタルソリューションを提供することで、企業が持続的な成長とイノベーションを達成できるようサポートします。
オンライン講座
製造業、主に購買・調達部門にお勤めの方々に向けた情報を配信しております。
新任の方やベテランの方、管理職を対象とした幅広いコンテンツをご用意しております。
お問い合わせ
コストダウンが利益に直結する術だと理解していても、なかなか前に進めることができない状況。そんな時は、newjiのコストダウン自動化機能で大きく利益貢献しよう!
(Β版非公開)