- お役立ち記事
- 11. How to use CAE simulation at the prototyping stage
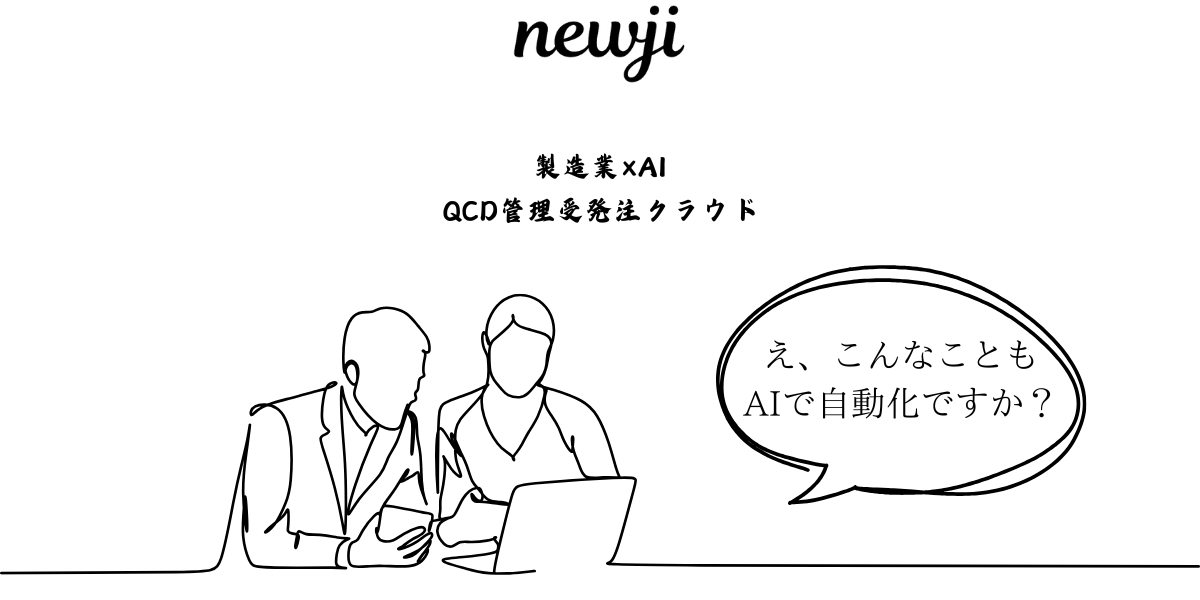
11. How to use CAE simulation at the prototyping stage
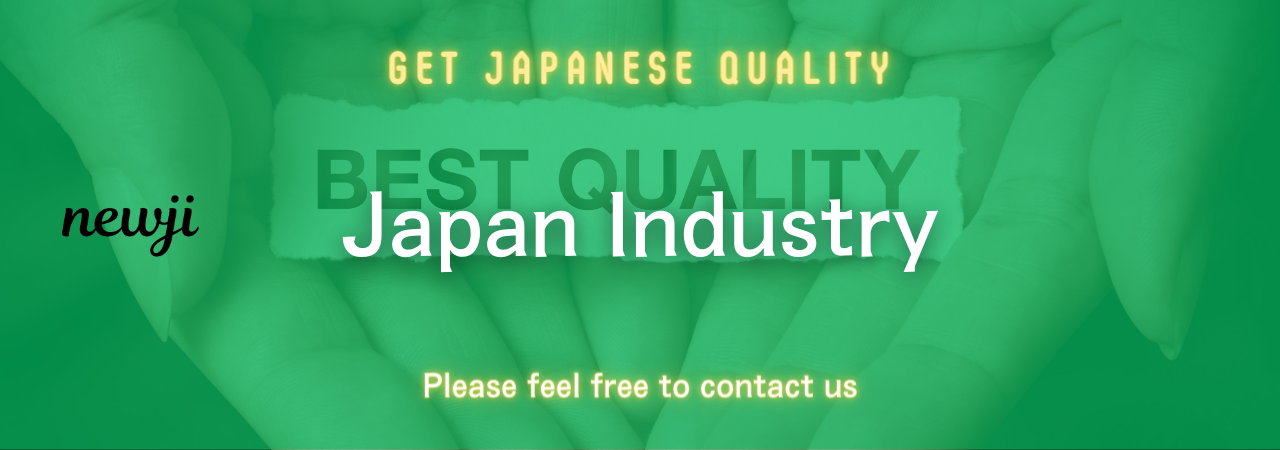
Understanding CAE Simulation
Computer-Aided Engineering (CAE) simulation plays a crucial role in modern product development, especially during the prototyping stage.
It involves the use of computer software to simulate performance and analyze engineering designs, processes, and systems.
It helps engineers to evaluate and optimize design performance before the creation of physical prototypes.
This is particularly beneficial in reducing both time and costs associated with product development.
CAE simulation can cover a broad range of analyses, including structural, thermal, fluid dynamics, and more.
These simulations allow engineers to visualize how a design will perform in real-world conditions, assess functionality, and identify potential issues early.
The Role of CAE in the Prototyping Stage
The prototyping stage is a critical phase in product development where ideas are transformed into tangible models.
CAE simulation enhances this process by enabling virtual testing and validation of designs, thereby improving accuracy and efficiency.
By using CAE tools, engineers can gain insights into product behavior under different conditions and make informed decisions.
This simulation aids in identifying structural weaknesses, optimizing materials, and validating performance requirements.
It presents opportunities to refine the design before any physical prototype is constructed, ensuring that resources are used effectively.
Key Benefits of CAE Simulation in Prototyping
Incorporating CAE simulation during the prototyping stage offers several advantages:
– **Cost Reduction**: By simulating a product’s design virtually, companies can reduce the number of physical prototypes they need to build, which cuts down material costs and labor.
– **Reduced Time to Market**: Faster iterations of design improvements mean that products can be developed swiftly, getting them to market sooner.
– **Improved Quality**: Engineers can explore a wide array of design alternatives and select the optimal configurations, leading to higher-quality products.
– **Risk Mitigation**: Virtual simulations enable the identification of potential design failures and safety issues, which reduces the risk of product recalls or redesigns later.
Implementing CAE Simulation Effectively
When integrating CAE simulation into the prototyping process, certain practices can enhance its effectiveness:
1. **Define Clear Objectives**: Begin by establishing what you aim to achieve with the simulation.
Whether it’s stress analysis, heat dissipation, or fluid flow, having clear goals will guide your simulation studies effectively.
2. **Comprehensive Modeling**: Ensure that the digital model accurately represents the physical prototype.
High-quality models with well-defined parameters and boundary conditions lead to more reliable simulation results.
3. **Iterative Testing**: Use simulation results to make incremental improvements and run multiple iterations.
This approach fine-tunes the design gradually and ensures that each iteration is better than the last.
4. **Integration with Other Tools**: Coordinate CAE simulation efforts with other engineering tools and processes, like CAD (Computer-Aided Design) systems.
This integration creates a seamless workflow, aligning design and analysis efficiently.
5. **Training and Expertise**: Qualified professionals should conduct simulations to maximize their benefits.
Thoroughly trained personnel understand the complexities involved and can interpret results accurately, leading to better decision-making.
Examples of CAE Simulation Applications
CAE simulation finds applications across various industries, influencing how products are designed and tested:
– **Automotive Industry**: Simulating crash tests and aerodynamics reduces the need for numerous physical crash tests, saving time and resources.
– **Aerospace Sector**: Engineers use CAE for aerodynamic analysis, structural testing under pressure, and assessing durability, ensuring safety and performance.
– **Consumer Electronics**: Electronics benefit from thermal simulations to ensure components do not overheat, assisting in the design of efficient cooling systems.
– **Construction and Civil Engineering**: Finite element analysis (FEA) predicts structural responses to loads and environmental factors, maintaining safety and performance.
Challenges and Considerations
While CAE simulation offers significant advantages, there are challenges to consider:
– **Computational Costs**: Simulations require powerful hardware and software, which can be expensive.
However, with advances in cloud computing, these costs are becoming more manageable.
– **Accuracy of Results**: The accuracy often hinges on the quality of input data and the precision of the model.
It’s imperative to validate simulation results with experimental data whenever possible.
– **Complexity**: The complexity of setting up simulations can be daunting, demanding careful planning and expertise.
Conclusion
CAE simulation is transforming the prototyping phase, enabling engineers to create optimized designs with greater confidence and efficiency.
By providing virtual testing capabilities, it reduces the need for extensive physical prototyping, cutting down on costs and accelerating product development cycles.
When implemented effectively, CAE simulation ensures robust product designs and paves the way for innovation across various industries.
資料ダウンロード
QCD調達購買管理クラウド「newji」は、調達購買部門で必要なQCD管理全てを備えた、現場特化型兼クラウド型の今世紀最高の購買管理システムとなります。
ユーザー登録
調達購買業務の効率化だけでなく、システムを導入することで、コスト削減や製品・資材のステータス可視化のほか、属人化していた購買情報の共有化による内部不正防止や統制にも役立ちます。
NEWJI DX
製造業に特化したデジタルトランスフォーメーション(DX)の実現を目指す請負開発型のコンサルティングサービスです。AI、iPaaS、および先端の技術を駆使して、製造プロセスの効率化、業務効率化、チームワーク強化、コスト削減、品質向上を実現します。このサービスは、製造業の課題を深く理解し、それに対する最適なデジタルソリューションを提供することで、企業が持続的な成長とイノベーションを達成できるようサポートします。
オンライン講座
製造業、主に購買・調達部門にお勤めの方々に向けた情報を配信しております。
新任の方やベテランの方、管理職を対象とした幅広いコンテンツをご用意しております。
お問い合わせ
コストダウンが利益に直結する術だと理解していても、なかなか前に進めることができない状況。そんな時は、newjiのコストダウン自動化機能で大きく利益貢献しよう!
(Β版非公開)