- お役立ち記事
- 2. Basics and practice of quality control at the prototype stage
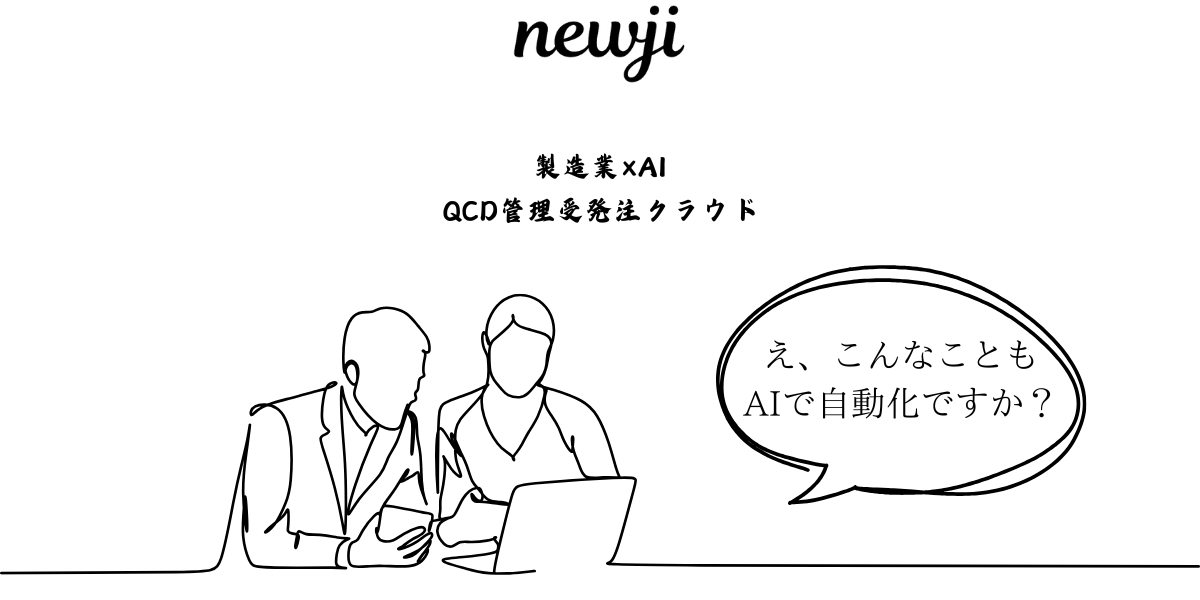
2. Basics and practice of quality control at the prototype stage
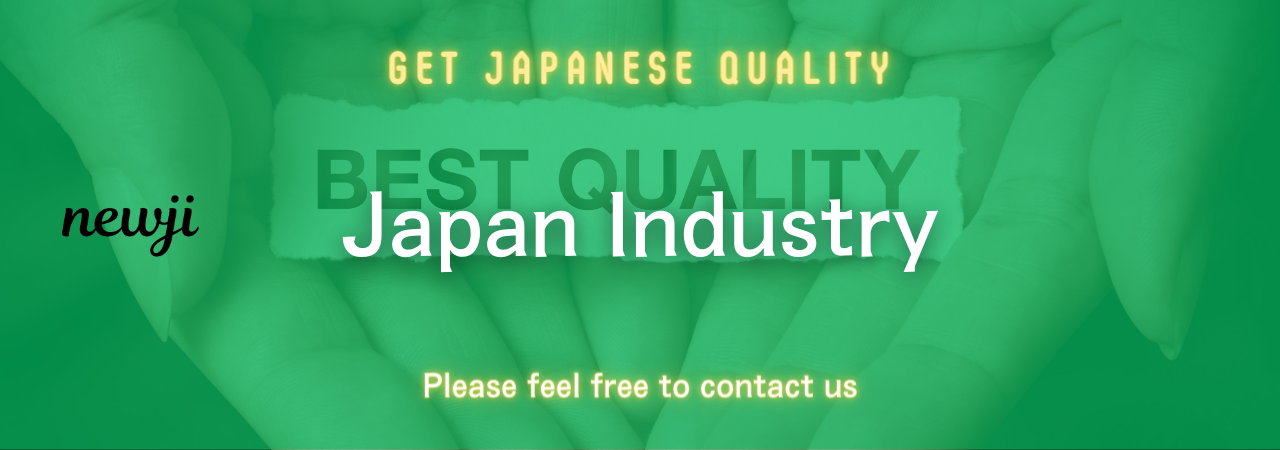
目次
Understanding Quality Control in the Prototype Stage
Quality control is an essential practice in manufacturing and product development.
At its core, quality control ensures that the products meet specific standards and function as intended.
When dealing with prototypes, quality control is even more crucial, as it sets the stage for subsequent production phases.
Understanding the basics and practices involved in quality control during the prototype stage can significantly impact the overall success of the product.
The Importance of Quality Control for Prototypes
In the early stages of product development, prototypes serve as preliminary versions of the final product.
They are designed to test concepts, functionality, and design before full-scale production begins.
Quality control at this stage is vital because it identifies potential flaws that could lead to costly problems down the line.
Addressing quality issues during the prototype stage helps save time, resources, and money in the long run.
By ensuring that the prototype meets desired standards, companies can avoid the risks of releasing a defective product to market.
Moreover, maintaining high quality in prototypes cultivates trust and confidence among stakeholders, investors, and potential customers.
A well-executed prototype signifies the reliability and potential of the final product.
Key Elements of Quality Control in Prototype Development
Effective quality control during the prototype stage revolves around several key elements.
These components help create a thorough and efficient process that guarantees optimal results.
Material and Component Selection
One of the first steps in quality control is selecting appropriate materials and components.
The materials chosen should align with the desired specifications and performance requirements.
Working with substandard materials can lead to issues such as malfunction or poor product performance.
Therefore, thorough evaluation and testing of materials are critical in the prototype phase.
Design Validation
Design validation is another crucial aspect, ensuring that the prototype will function as intended.
This process involves comparing the design specifications with the actual performance of the prototype.
Any discrepancies are addressed through redesign and further testing.
Working closely with engineers and designers can ensure that the designs meet both functional and aesthetic expectations.
Performance Testing
Performance testing is an integral part of quality control for prototypes.
It involves rigorous evaluations to determine if the prototype meets defined performance standards.
Tests may include stress tests, endurance tests, and environmental tests to simulate real-world conditions.
The data gathered from these tests is invaluable in refining the prototype and preventing potential issues in the production phase.
Documentation and Standards
Proper documentation is essential for maintaining quality control throughout the prototype development.
This includes keeping detailed records of tests, changes, and evaluations.
Adhering to industry standards and regulations also plays a vital role in ensuring the prototype’s quality.
Compliance with standards not only ensures safety but also enhances the product’s credibility and marketability.
Practical Steps to Implementing Quality Control
Having a theoretical understanding of quality control is essential, but practical implementation is what drives results.
Here are some actionable steps to ensure effective quality control during the prototype stage.
Define Clear Objectives
Before beginning the prototype development, it is crucial to define clear objectives and quality standards.
Understanding what the prototype should achieve allows for focused efforts in testing and improving it.
Providing all team members with these objectives ensures everyone is aligned toward achieving high-quality results.
Set Measurable Quality Metrics
Establishing measurable quality metrics provides a concrete way to assess whether the prototype meets the desired standards.
These metrics can include dimensions, weight, performance output, and safety features.
Regularly comparing the prototype against these metrics ensures it is on track to meet the quality objectives.
Conduct Regular Reviews
Frequent reviews and evaluations are necessary to maintain the quality trajectory of the prototype.
Organizing regular meetings with cross-functional teams enables the identification of any emerging issues or areas for improvement.
These reviews ensure that all aspects of the prototype are scrutinized, enabling timely corrections and enhancements.
Encourage Collaboration and Communication
Quality control is a collaborative effort.
Ensuring open communication channels among designers, engineers, and quality assurance teams fosters a culture of quality.
Problems are more easily identified and solved when all stakeholders contribute their expertise and insights.
The Role of Feedback in Quality Control
Feedback is an invaluable component of quality control, especially during the prototype stage.
Gathering feedback from stakeholders, users, and experts provides diverse perspectives on the prototype’s functionality and appeal.
User feedback is particularly useful, as it reflects the actual experience of potential consumers.
Incorporating this feedback can lead to design improvements and enhancements that align with user expectations.
Furthermore, feedback from internal teams and expert evaluators provides technical insights that might not be immediately evident.
This feedback can guide necessary adjustments, contributing to a more robust and market-ready product.
Conclusion
Quality control during the prototype stage is a pivotal element of product development.
It ensures that the prototype meets defined standards, preventing future complications, and enhancing final product success.
By focusing on material selection, design validation, performance testing, and following practical implementation steps, quality control becomes a guiding force for innovation.
Ultimately, integrating feedback and maintaining a collaborative culture can propel the prototype toward excellence and market readiness.
資料ダウンロード
QCD調達購買管理クラウド「newji」は、調達購買部門で必要なQCD管理全てを備えた、現場特化型兼クラウド型の今世紀最高の購買管理システムとなります。
ユーザー登録
調達購買業務の効率化だけでなく、システムを導入することで、コスト削減や製品・資材のステータス可視化のほか、属人化していた購買情報の共有化による内部不正防止や統制にも役立ちます。
NEWJI DX
製造業に特化したデジタルトランスフォーメーション(DX)の実現を目指す請負開発型のコンサルティングサービスです。AI、iPaaS、および先端の技術を駆使して、製造プロセスの効率化、業務効率化、チームワーク強化、コスト削減、品質向上を実現します。このサービスは、製造業の課題を深く理解し、それに対する最適なデジタルソリューションを提供することで、企業が持続的な成長とイノベーションを達成できるようサポートします。
オンライン講座
製造業、主に購買・調達部門にお勤めの方々に向けた情報を配信しております。
新任の方やベテランの方、管理職を対象とした幅広いコンテンツをご用意しております。
お問い合わせ
コストダウンが利益に直結する術だと理解していても、なかなか前に進めることができない状況。そんな時は、newjiのコストダウン自動化機能で大きく利益貢献しよう!
(Β版非公開)