- お役立ち記事
- 7 QC tools that new employees in the quality assurance department should know and the basics of quality improvement
7 QC tools that new employees in the quality assurance department should know and the basics of quality improvement
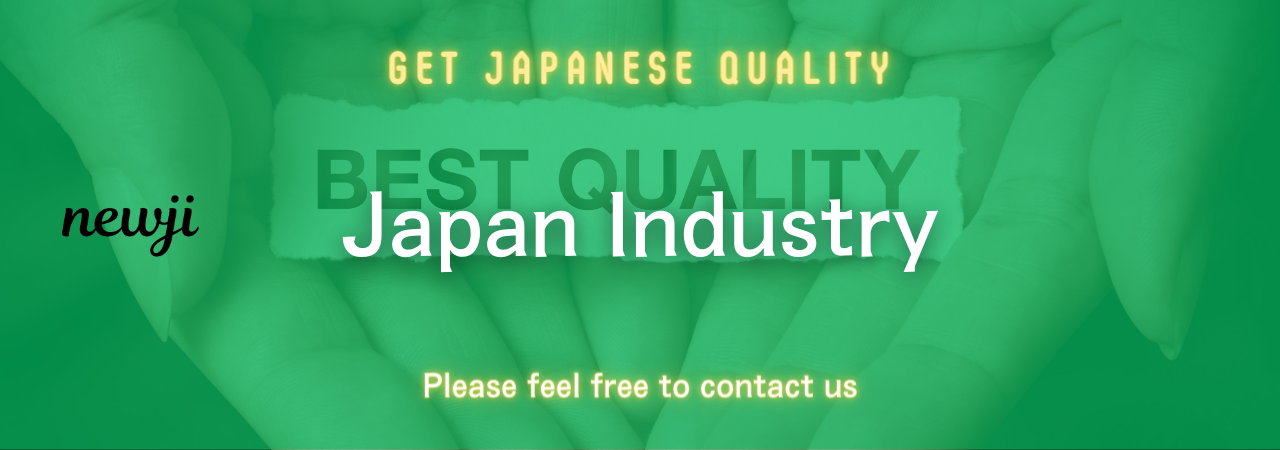
New employees in the quality assurance department are often tasked with maintaining and improving the quality of products or services.
To excel in this role, it’s essential to have a grasp of the fundamental quality control (QC) tools.
These tools are designed to help identify, analyze, and solve quality-related problems.
Here, we discuss the seven QC tools that every new quality assurance employee should be familiar with, along with the basics of quality improvement.
目次
1. Pareto Chart
A Pareto Chart is a simple yet powerful tool that displays the most significant factors in a dataset.
Named after Vilfredo Pareto, this tool emphasizes the “80/20 rule,” suggesting that 80% of problems are often due to 20% of causes.
New employees can use Pareto Charts to prioritize issues and decide which one to tackle first.
By focusing on the most pressing problems, significant improvements in quality can be achieved.
How to Create a Pareto Chart
– Identify and list problems or causes of defects.
– Collect data and determine the frequency of each problem.
– Order the problems from most to least frequent.
– Calculate the cumulative percentage of each problem.
– Draw the chart with bars representing the frequency of each problem and a line graph tracking the cumulative percentage.
2. Fishbone Diagram
Also known as the Ishikawa or Cause-and-Effect Diagram, the Fishbone Diagram helps in identifying potential causes of a quality issue.
It resembles a fish skeleton, with the problem at the head and causes depicted as bones branching out.
This tool facilitates brainstorming sessions and encourages team members to consider various factors that might contribute to a problem.
Steps to Develop a Fishbone Diagram
– Define the problem clearly at the “head” of the diagram.
– Identify major categories contributing to the problem, such as people, methods, machines, materials, measurements, and environments.
– Brainstorm possible causes and add them under the appropriate category.
– Analyze the completed diagram to isolate the most likely root causes.
3. Scatter Diagram
A Scatter Diagram, or Scatter Plot, is used to examine the relationship between two variables.
By plotting data points on a graph, employees can observe patterns or correlations, which can aid in understanding how changes in one variable might affect another.
Using a Scatter Diagram
– Determine the variables to analyze and gather data for both.
– Plot each pair of values on a graph, one variable on the x-axis and the other on the y-axis.
– Analyze the pattern or trend of the data points.
– Look for correlations, such as trends where variables increase together or move inversely.
4. Control Chart
Control Charts are essential for monitoring processes over time, helping determine if they operate consistently or if variations occur.
By visualizing variations, employees can quickly spot anomalies or unexpected trends.
Steps to Create a Control Chart
– Collect data points from the process over a period.
– Calculate the mean (average) of the data set.
– Determine the upper control limit (UCL) and lower control limit (LCL) using statistical methods.
– Plot the data points along with the mean, UCL, and LCL on a graph.
– Analyze the chart for any data points extending beyond the control limits or unusual patterns.
5. Flowchart
Flowcharts graphically represent a process by outlining each step in sequential order.
This tool is beneficial for visualizing complex processes, identifying inefficiencies, and ensuring consistent procedures.
Creating a Flowchart
– Define the process to be visualized.
– Identify each step along the process from start to end.
– Use standardized symbols to represent each type of action (e.g., ovals for start/end points, rectangles for steps, diamonds for decision points).
– Connect the steps using arrows indicating the flow of the process.
– Review the flowchart for completeness and accuracy.
6. Histogram
A Histogram is a type of bar graph used to visualize the distribution of numerical data.
It helps employees understand the frequency of a range of outcomes in a dataset, making it easier to identify patterns or outliers.
Steps to Create a Histogram
– Collect and organize the data for analysis.
– Decide on the intervals or “bins” for the data grouping.
– Count how many data points fall into each bin.
– Draw the histogram with bars representing the frequency of each interval.
– Analyze the shape and distribution of the histogram for insights.
7. Check Sheet
A Check Sheet is a structured, simple form used for collecting data in real-time at the location where it is generated.
This tool is useful for tracking how often certain events occur and can be customized to suit specific data collection needs.
Using a Check Sheet
– Define the purpose of the data collection and what information needs to be captured.
– Design a form that allows for easy recording of occurrences.
– Use tick marks or tally marks to record each event or defect as it is observed.
– Periodically review the collected data to spot trends or areas needing improvement.
Basics of Quality Improvement
Understanding and utilizing these QC tools is only part of the equation for quality improvement.
Quality improvement requires a proactive approach, a commitment to continuous learning, and a desire to meet or exceed customer expectations.
Essential Elements of Quality Improvement
– Set clear quality objectives: Define goals that align with business objectives and customer needs.
– Foster a culture of quality: Encourage all employees to prioritize quality in their roles and empower them to contribute to improvements.
– Analyze data regularly: Use the QC tools to assess processes and identify areas for enhancement.
– Implement corrective actions: Develop and apply solutions to address the root causes of problems.
– Monitor and evaluate changes: Track the effectiveness of implemented changes and adjust as necessary.
New employees in the quality assurance department can significantly contribute to their organizations by mastering these QC tools and embracing quality improvement principles.
Continuous learning and application of these tools will lead to better product quality, higher customer satisfaction, and a more efficient working environment.
資料ダウンロード
QCD調達購買管理クラウド「newji」は、調達購買部門で必要なQCD管理全てを備えた、現場特化型兼クラウド型の今世紀最高の購買管理システムとなります。
ユーザー登録
調達購買業務の効率化だけでなく、システムを導入することで、コスト削減や製品・資材のステータス可視化のほか、属人化していた購買情報の共有化による内部不正防止や統制にも役立ちます。
NEWJI DX
製造業に特化したデジタルトランスフォーメーション(DX)の実現を目指す請負開発型のコンサルティングサービスです。AI、iPaaS、および先端の技術を駆使して、製造プロセスの効率化、業務効率化、チームワーク強化、コスト削減、品質向上を実現します。このサービスは、製造業の課題を深く理解し、それに対する最適なデジタルソリューションを提供することで、企業が持続的な成長とイノベーションを達成できるようサポートします。
オンライン講座
製造業、主に購買・調達部門にお勤めの方々に向けた情報を配信しております。
新任の方やベテランの方、管理職を対象とした幅広いコンテンツをご用意しております。
お問い合わせ
コストダウンが利益に直結する術だと理解していても、なかなか前に進めることができない状況。そんな時は、newjiのコストダウン自動化機能で大きく利益貢献しよう!
(Β版非公開)