- お役立ち記事
- A Case Study of Efforts by a Quality Assurance Department in a Manufacturing Company to Prevent Outflow of Defective Products
A Case Study of Efforts by a Quality Assurance Department in a Manufacturing Company to Prevent Outflow of Defective Products
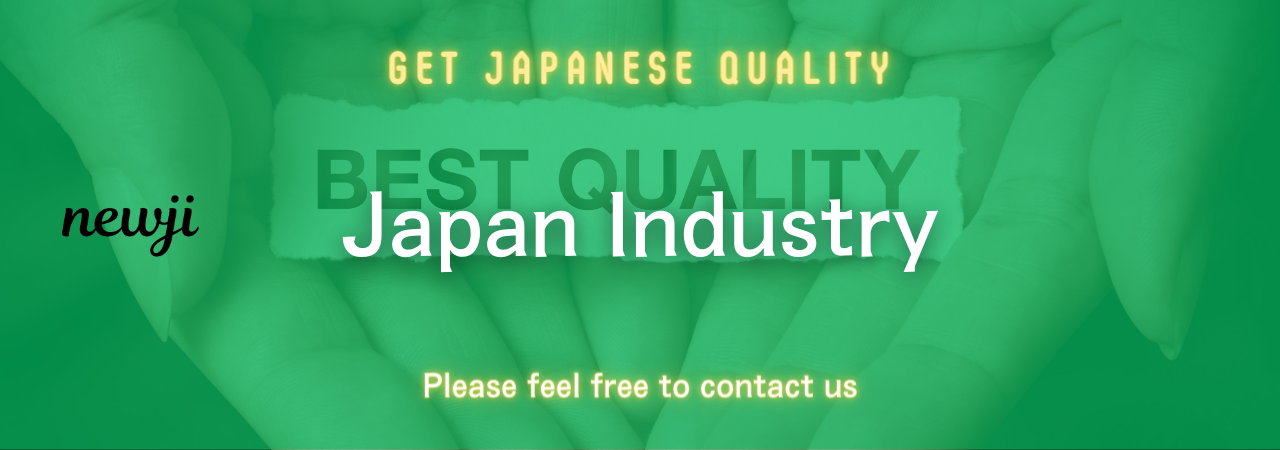
In today’s competitive market, ensuring product quality is paramount for manufacturing companies. One of the critical departments tasked with this responsibility is the Quality Assurance (QA) department. This article delves into a case study of a QA department’s efforts to prevent the outflow of defective products. By examining their strategies, processes, and tools, we can glean valuable insights into how other manufacturing companies can improve their quality control measures.
目次
The Importance of QA in Manufacturing
Before diving into the specifics of the case study, it’s essential to understand the role of the QA department in manufacturing companies. The primary responsibility of the QA department is to ensure that the products meet or exceed customer expectations and regulatory requirements. They achieve this by implementing comprehensive inspection procedures, establishing quality standards, and continuously monitoring production processes.
Case Study Overview
The manufacturing company in focus specializes in producing electronic components. Over the past few years, they faced significant challenges related to defective products reaching the market, which led to increased customer complaints and a decline in brand reputation. Recognizing the urgency of the situation, the company’s management decided to revamp its QA processes entirely.
Initial Assessment
The first step taken by the QA department was to conduct a thorough assessment of the existing processes. This included:
1. Reviewing Historical Data: Analyzing past defect data to identify common issues and patterns.
2. Engaging Stakeholders: Discussing with production managers, line workers, and customers to gain a comprehensive understanding of the problem areas.
3. Auditing Current Procedures: Evaluating the effectiveness of current inspection methods and the adequacy of QA resources.
Identified Issues
From the initial assessment, several issues were identified:
– Inconsistent Inspection Procedures: There was a lack of standardization, leading to variability in quality checks.
– Insufficient Training: QA personnel and production workers were not adequately trained on the latest inspection techniques and quality standards.
– Outdated Equipment: The inspection tools and equipment were outdated, leading to inaccurate results.
– Limited Use of Data Analytics: The company was not leveraging data analytics to predict and prevent defects.
Strategic Improvements
Armed with this knowledge, the QA department set out to implement a series of strategic improvements:
1. Standardization of Procedures
The first step was to create a comprehensive quality manual that standardized all inspection procedures. This manual served as a definitive guide for QA personnel, ensuring consistency across the board. Procedures were broken down into easy-to-follow steps, and checklists were introduced to ensure no aspect of the inspection was overlooked.
2. Enhanced Training Programs
Recognizing the importance of skilled personnel, the company invested in extensive training programs. These programs covered:
– Advanced Inspection Techniques: Training on the latest inspection methods and tools.
– Quality Standards: Education on both company-specific and industry-wide quality standards.
– Problem-Solving Skills: Teaching employees how to identify root causes of defects and implement corrective actions.
3. Upgraded Equipment
To ensure accurate inspections, the QA department pushed for the acquisition of state-of-the-art inspection equipment. This included:
– Advanced Microscopes: For detailed examination of electronic components.
– Automated Optical Inspection (AOI) Systems: To detect defects at various stages of production.
– Software Tools: For real-time monitoring and data analysis.
4. Data-Driven Quality Control
A significant shift was made towards data-driven quality control. The QA department collaborated with the IT team to develop a robust data analytics platform. This platform allowed for:
– Real-Time Monitoring: Continuous tracking of production processes to quickly identify and address deviations.
– Predictive Analysis: Using historical data to predict potential defects and take preventive measures.
– Reporting and Dashboards: Generating comprehensive reports and visual dashboards for easy monitoring and decision-making.
Results and Benefits
The implementation of these strategic improvements led to several positive outcomes:
– Reduction in Defect Rates: The most notable achievement was the significant reduction in the rate of defective products. Over a six-month period, defects decreased by over 50%.
– Improved Customer Satisfaction: With fewer defective products reaching the market, customer complaints dropped, leading to higher satisfaction and brand loyalty.
– Enhanced Employee Morale: The investment in training and upgraded equipment boosted employee morale and confidence in their work.
– Better Compliance: The standardized procedures and data-driven approach ensured compliance with industry regulations and standards.
– Cost Savings: By preventing defects, the company saved substantial costs associated with rework, returns, and lost sales.
Continuous Improvement
The company understood that quality assurance is not a one-time effort but an ongoing journey. To sustain and further improve these gains, the QA department implemented a culture of continuous improvement. This involved:
– Regular Audits: Conducting regular audits to ensure adherence to quality standards and identifying areas for enhancement.
– Feedback Loops: Establishing feedback mechanisms from customers and production line workers to continually refine processes.
– Benchmarking: Comparing their quality metrics with industry benchmarks to stay competitive.
The case study of this manufacturing company’s QA department highlights the critical role that quality assurance plays in preventing the outflow of defective products. By standardizing procedures, enhancing training, upgrading equipment, and leveraging data analytics, the company was able to achieve substantial improvements in product quality and customer satisfaction. This comprehensive approach serves as a valuable blueprint for other manufacturing companies facing similar challenges.
Continuous improvement, driven by regular audits, feedback loops, and benchmarking, ensures that these gains are not only maintained but also built upon, paving the way for long-term success and a stellar market reputation.
資料ダウンロード
QCD調達購買管理クラウド「newji」は、調達購買部門で必要なQCD管理全てを備えた、現場特化型兼クラウド型の今世紀最高の購買管理システムとなります。
ユーザー登録
調達購買業務の効率化だけでなく、システムを導入することで、コスト削減や製品・資材のステータス可視化のほか、属人化していた購買情報の共有化による内部不正防止や統制にも役立ちます。
NEWJI DX
製造業に特化したデジタルトランスフォーメーション(DX)の実現を目指す請負開発型のコンサルティングサービスです。AI、iPaaS、および先端の技術を駆使して、製造プロセスの効率化、業務効率化、チームワーク強化、コスト削減、品質向上を実現します。このサービスは、製造業の課題を深く理解し、それに対する最適なデジタルソリューションを提供することで、企業が持続的な成長とイノベーションを達成できるようサポートします。
オンライン講座
製造業、主に購買・調達部門にお勤めの方々に向けた情報を配信しております。
新任の方やベテランの方、管理職を対象とした幅広いコンテンツをご用意しております。
お問い合わせ
コストダウンが利益に直結する術だと理解していても、なかなか前に進めることができない状況。そんな時は、newjiのコストダウン自動化機能で大きく利益貢献しよう!
(Β版非公開)