- お役立ち記事
- A Day in the Life of a Cardboard Factory: The Process of Fluting
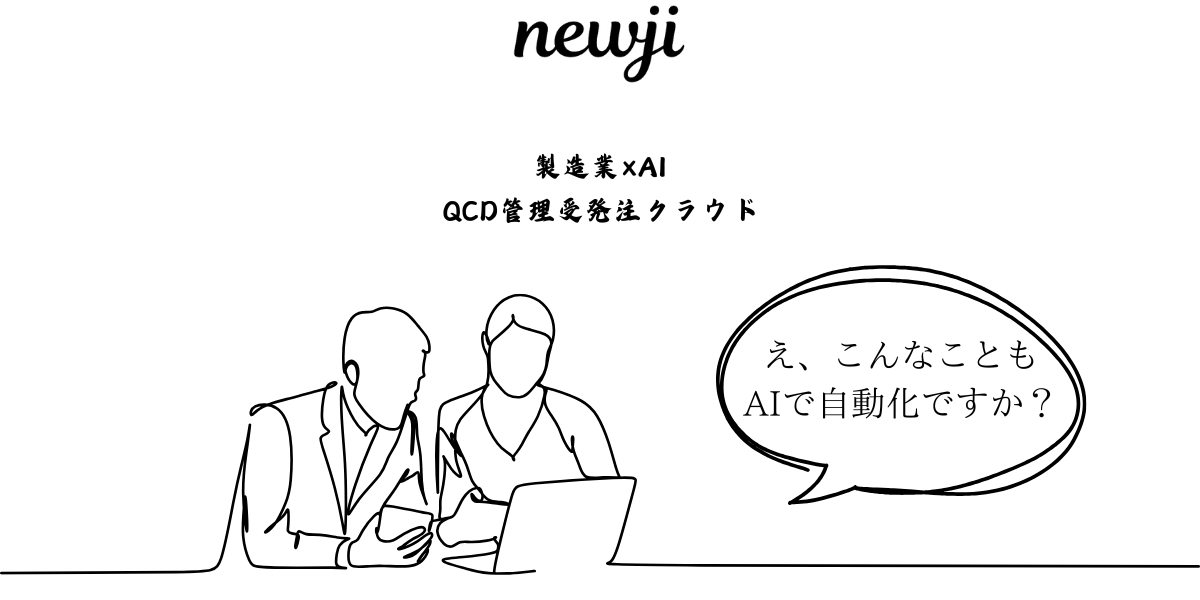
A Day in the Life of a Cardboard Factory: The Process of Fluting
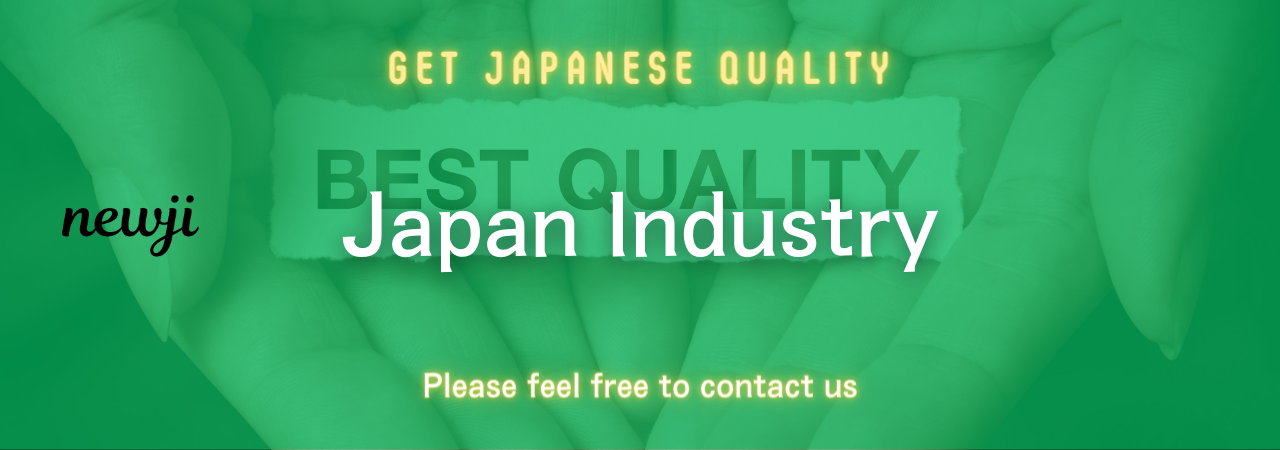
目次
Introduction: What is Fluting in Cardboard Production?
Cardboard is a ubiquitous material, used for packaging everything from cereal boxes to large shipping containers.
One of the most crucial processes that give cardboard its strength and durability is known as fluting.
This technique involves creating a wave-like pattern that is sandwiched between two flat layers of paper.
Fluting plays a significant role in making the cardboard sturdy, lightweight, and shock absorbent.
Understanding the process of fluting helps us appreciate how everyday packaging is designed to protect the contents within.
The Beginning: Raw Materials
A day in a cardboard factory begins with sourcing the raw materials essential for production.
The main components for creating fluted cardboard are paper and adhesives.
Typically, recycled paper or wood pulp is used, contributing to the eco-friendliness of cardboard production.
These materials arrive at the factory in large rolls, which are then prepared for processing through rigorous inspections to ensure quality.
The Importance of Quality Checks
Before production begins, these materials undergo numerous quality checks.
Inspectors assess the weight, thickness, and moisture content of the paper.
These factors are vital as they impact the final product’s strength and flexibility.
Quality paper forms the backbone of the sturdy cardboard, ensuring it meets the necessary standards for various packaging needs.
The Production Process: Corrugating the Paper
The heart of the cardboard production process is the corrugator machine, responsible for giving cardboard its unique wave-like fluting.
This intricate machine consists of various heated rolls that bend and shape the paper into the trademark ridges.
Here is how the process unfolds:
Step 1: Heating the Paper
The journey begins by passing the paper through preheaters.
These large heated rolls soften the paper, making it pliable enough to be molded without tearing.
This step is crucial as it ensures the paper can be formed into waves without compromising integrity.
Step 2: Forming the Flute
Softened paper is then fed into the corrugating rolls, where the magic happens.
These rolls mold the paper into a series of ridges and grooves, akin to a wave pattern.
This fluting process not only strengthens the paper but also provides cushioning.
It’s the flutes that absorb shocks and resist compression, critical for protecting goods during transit.
Step 3: Applying Adhesives
Once fluted, the paper layers are glued together.
The outer layers are bonded to the fluted paper using strong adhesives.
This bonding ensures the stability and rigidity of the final product.
Precision and speed are key here, as improper gluing can result in weak points, affecting overall durability.
Finishing Touches: Cutting and Finishing
With the fluting complete and layers securely bonded, the cardboard is then directed toward the finishing stages.
In this phase, the continuous sheet of corrugated cardboard is cut into the desired lengths and widths.
Advanced computer systems guide high-precision cutters to achieve the required dimensions.
Customizing the Product
After cutting, customization options are available.
Clients often require specific branding to be printed on the cardboard.
Using high-quality inks, the cardboard passes through a printing press where logos, product details, or handling instructions are added.
This step ensures that companies can personalize their packaging while maintaining quality.
Quality Assurance and Packing
Before the final product leaves the factory, it undergoes another round of rigorous testing.
Several quality assurance checks are performed to ensure the cardboard meets industry standards and customer requirements.
Testing for Strength and Durability
The cardboard is tested for various properties, including:
1. **Burst strength** – Measures resistance to pressure.
2. **Edge crush strength** – Assesses how well the edges hold under stress.
3. **Moisture resistance** – Ensures performance under varying humidity levels.
These tests confirm that the cardboard can withstand the stresses of shipping and handling.
Packing and Dispatching
Once tests are completed, the cardboard sheets are stacked and packed.
They are then dispatched to various clients who turn them into boxes, partitions, or displays.
Some factories also produce ready-to-use cartons, shipped flat-packed to save space and cost during transit.
Conclusion: The Impact of Fluting
Fluting in cardboard production is an art and science combo that transforms simple paper into a versatile packaging solution.
This process ensures that cardboard remains an integral part of today’s logistics and retail sectors.
Understanding this journey—from raw materials to the final product—fosters a greater appreciation for the engineering and care that goes into everyday packaging solutions.
Next time you receive a parcel, take a moment to think about the journey it took through the cardboard factory and the fascinating process of fluting that made it all possible.
資料ダウンロード
QCD調達購買管理クラウド「newji」は、調達購買部門で必要なQCD管理全てを備えた、現場特化型兼クラウド型の今世紀最高の購買管理システムとなります。
ユーザー登録
調達購買業務の効率化だけでなく、システムを導入することで、コスト削減や製品・資材のステータス可視化のほか、属人化していた購買情報の共有化による内部不正防止や統制にも役立ちます。
NEWJI DX
製造業に特化したデジタルトランスフォーメーション(DX)の実現を目指す請負開発型のコンサルティングサービスです。AI、iPaaS、および先端の技術を駆使して、製造プロセスの効率化、業務効率化、チームワーク強化、コスト削減、品質向上を実現します。このサービスは、製造業の課題を深く理解し、それに対する最適なデジタルソリューションを提供することで、企業が持続的な成長とイノベーションを達成できるようサポートします。
オンライン講座
製造業、主に購買・調達部門にお勤めの方々に向けた情報を配信しております。
新任の方やベテランの方、管理職を対象とした幅広いコンテンツをご用意しております。
お問い合わせ
コストダウンが利益に直結する術だと理解していても、なかなか前に進めることができない状況。そんな時は、newjiのコストダウン自動化機能で大きく利益貢献しよう!
(Β版非公開)