- お役立ち記事
- A framework adopted by purchasing departments to minimize procurement risks
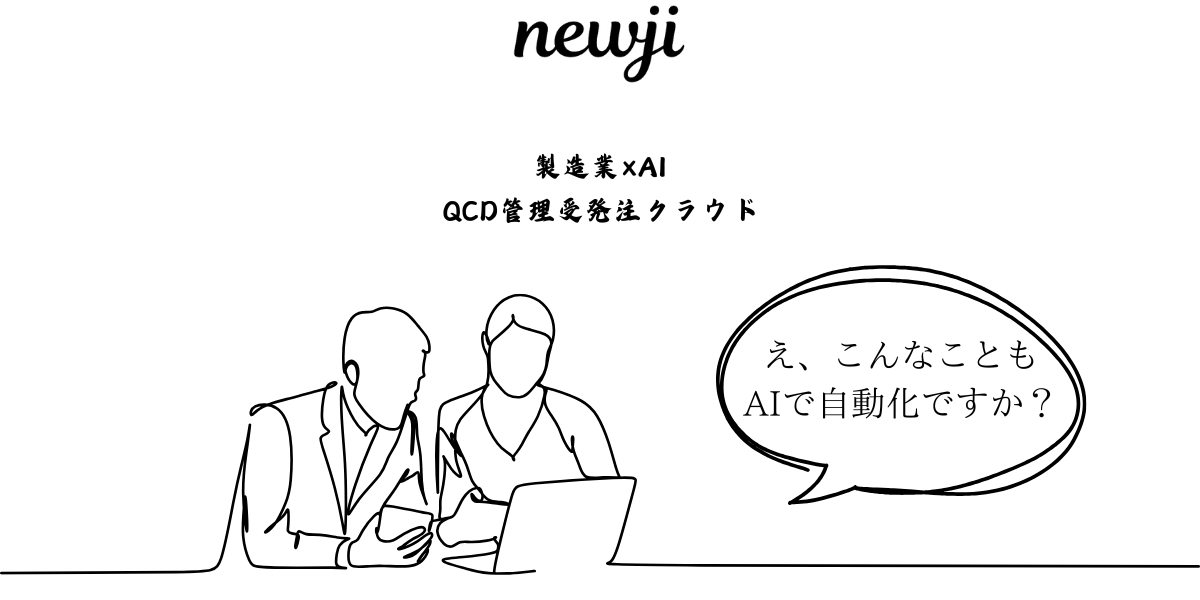
A framework adopted by purchasing departments to minimize procurement risks
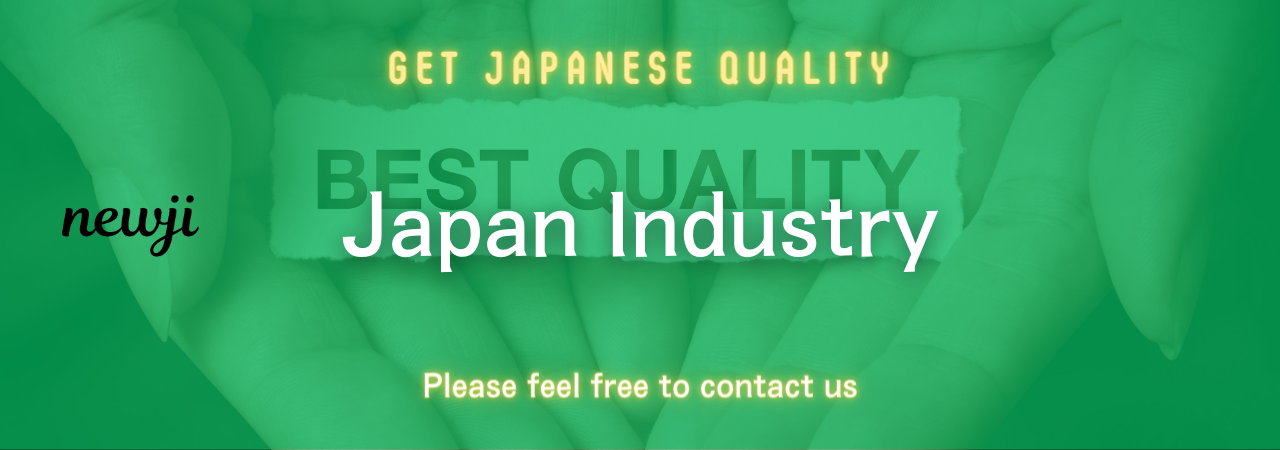
目次
Understanding Procurement Risks
Procurement risks are uncertainties or potential negative outcomes that can affect the purchasing processes of organizations.
These risks can arise from various sources, including supplier issues, market dynamics, and internal inefficiencies.
Managing these risks is crucial for the success of any purchasing department as it ensures that the flow of goods and services continues smoothly and that costs are kept under control.
Effectively managing procurement risks can prevent costly disruptions, protect the organization’s reputation, and ensure compliance with regulations.
Procurement departments adopt frameworks that provide structured approaches to identify, assess, and mitigate these risks.
Identifying Procurement Risks
The first step in minimizing procurement risks is to identify them.
This involves a comprehensive assessment of the entire procurement cycle from planning and ordering to receipt and payment.
Common sources of procurement risks include:
Supplier Risk
This refers to potential issues with the suppliers, such as financial instability, failure to deliver on time, or supplying substandard goods.
To mitigate supplier risks, organizations need to conduct thorough evaluations of potential suppliers and also continually assess existing ones.
Market Risk
Market risks include fluctuations in prices and availability of goods and services.
These fluctuations can be due to changes in demand and supply, geopolitical factors, or economic conditions.
Purchasing departments need to stay informed about market trends to effectively manage these risks.
Operational Risk
This involves risks arising from the procurement process itself, such as inefficient processes, inadequate technology, or lack of clear communication.
Implementing standardized and streamlined procedures can help in minimizing operational risks.
Assessing Procurement Risks
Once identified, procurement risks need to be assessed to understand their potential impact and likelihood.
This helps to prioritize which risks should be mitigated first.
Risk assessment usually involves two key steps:
Risk Analysis
Risk analysis involves determining how each potential risk can affect the organization.
This might involve estimating potential financial losses, impacts on supply chains, or reputational damage.
Risk Evaluation
Following the analysis, risks are evaluated to prioritize those that need the most attention.
This is generally based on a combination of the likelihood of the risk occurring and its potential impact.
Developing a Risk Mitigation Plan
Once procurement risks have been identified and assessed, the next step is to develop a risk mitigation plan.
This plan outlines the specific actions that will be taken to reduce or eliminate risks.
Supplier Management
A robust supplier management strategy is essential.
This may include diversifying the supplier base to reduce dependency on single suppliers, incorporating rigorous contract terms, and maintaining good supplier relationships.
Market Analysis
Regular market analysis helps procurement teams anticipate price changes and supply shortages.
This can involve setting up frameworks for continuous monitoring of market trends and building strategic partnerships with suppliers to ensure priority access to resources.
Process Improvements
Optimizing procurement processes is critical to minimizing operational risks.
Implementing technology solutions like procurement software can help automate and streamline procurement tasks, reducing the chances of errors and inefficiencies.
The Role of Technology in Minimizing Procurement Risks
Technology plays a critical role in risk management strategies for procurement departments.
With modern technological solutions, procurement processes can be more efficient, transparent, and controlled.
Procurement Software
Procurement software can automate routine purchasing processes, provide insights through data analytics, and improve communications.
It helps organizations maintain better control over purchasing activities and promptly respond to risks.
Data Analytics
Data analytics can provide invaluable insights into supplier performance, market trends, and internal processes.
Analytics tools can identify patterns and anomalies that signal potential risks, allowing organizations to respond proactively.
Blockchain
Blockchain technology offers enhanced transparency and traceability in supply chains.
By maintaining an immutable record of transactions, organizations can verify the authenticity of suppliers and track the provenance of goods.
The Importance of Continuous Improvement
The landscape of procurement is dynamic, with new risks continually emerging.
As such, continuous improvement is essential in procurement risk management.
Regular Reviews
Procurement departments must regularly review and update their risk management strategies to address new challenges.
This involves continuous monitoring of supplier performance, market conditions, and internal processes.
Training and Development
Investing in training and development for the procurement team ensures they are well-equipped to recognize and manage risks.
Training programs can cover new technologies, risk management techniques, and industry trends.
Collaboration Across Departments
Effective procurement risk management often requires collaboration with other departments such as finance, legal, and logistics.
By working together, departments can align their strategies and ensure a comprehensive approach to risk management.
By adopting a structured framework for managing procurement risks, purchasing departments can minimize disruptions, control costs, and maintain a competitive edge. As organizations continue to evolve, so too should their approaches to procurement, ensuring they are prepared to handle any challenges that may arise in the future.
資料ダウンロード
QCD調達購買管理クラウド「newji」は、調達購買部門で必要なQCD管理全てを備えた、現場特化型兼クラウド型の今世紀最高の購買管理システムとなります。
ユーザー登録
調達購買業務の効率化だけでなく、システムを導入することで、コスト削減や製品・資材のステータス可視化のほか、属人化していた購買情報の共有化による内部不正防止や統制にも役立ちます。
NEWJI DX
製造業に特化したデジタルトランスフォーメーション(DX)の実現を目指す請負開発型のコンサルティングサービスです。AI、iPaaS、および先端の技術を駆使して、製造プロセスの効率化、業務効率化、チームワーク強化、コスト削減、品質向上を実現します。このサービスは、製造業の課題を深く理解し、それに対する最適なデジタルソリューションを提供することで、企業が持続的な成長とイノベーションを達成できるようサポートします。
オンライン講座
製造業、主に購買・調達部門にお勤めの方々に向けた情報を配信しております。
新任の方やベテランの方、管理職を対象とした幅広いコンテンツをご用意しております。
お問い合わせ
コストダウンが利益に直結する術だと理解していても、なかなか前に進めることができない状況。そんな時は、newjiのコストダウン自動化機能で大きく利益貢献しよう!
(Β版非公開)