- お役立ち記事
- A Guide to Implementing and Choosing Print Inspection Systems for SMEs
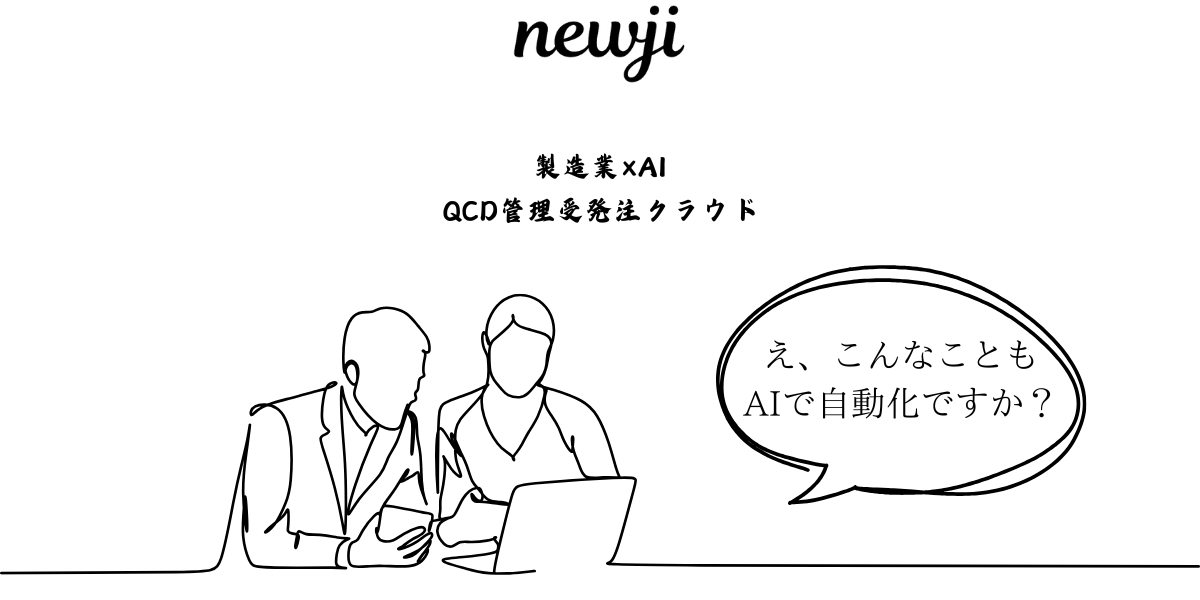
A Guide to Implementing and Choosing Print Inspection Systems for SMEs
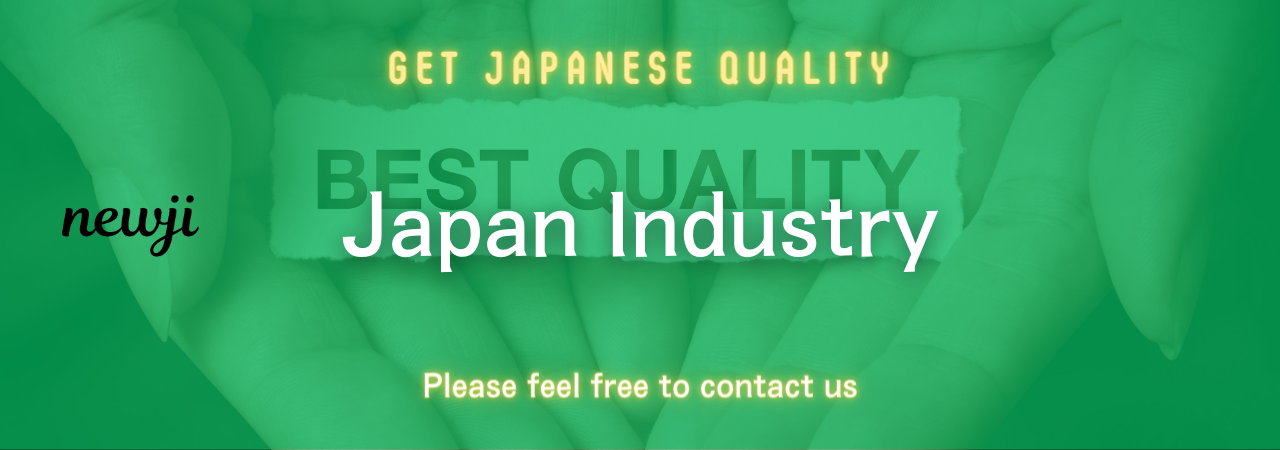
目次
Understanding Print Inspection Systems
In today’s dynamic business environment, quality control is paramount, especially among Small and Medium Enterprises (SMEs) looking to maintain competitiveness in the market.
One crucial aspect of quality assurance is the implementation of print inspection systems.
These systems ensure that print materials such as labels, packaging, and documents meet specific quality criteria.
By doing so, they help prevent costly errors, reduce waste, and improve overall customer satisfaction.
These systems rely on advanced imaging technologies and software algorithms to examine materials for any defects or deviations from the desired print specifications.
While traditionally used in large-scale operations, print inspection systems are now becoming increasingly accessible and beneficial for SMEs.
Benefits of Print Inspection Systems
One of the primary advantages of implementing a print inspection system in an SME is the enhancement of product quality.
By automatically identifying print defects like smudges, misalignments, or color inaccuracies, businesses can ensure that only flawless products reach customers.
This significantly lowers the risk of returns and increases brand reputation in the eyes of consumers.
Another benefit is the reduction in production costs related to material wastage.
Identifying and addressing defects early in the production process means less scrap and rework, thereby conserving resources and ultimately saving money.
Furthermore, by implementing print inspection systems, companies can speed up their production line without compromising on quality.
This enhances overall efficiency and output, allowing SMEs to meet larger orders and tighten delivery timelines.
Choosing the Right Print Inspection System
Selecting an appropriate print inspection system tailored to the needs of an SME is critical.
This decision can substantially impact the effectiveness and efficiency of the quality control process.
Evaluate Your Business Needs
Start by assessing your specific business requirements.
Consider factors such as the type of printing you do, the volume of materials, and the kind of defects that commonly occur in your processes.
Understanding these will inform what features and capabilities are necessary for your system, such as high-resolution imaging or quick defect recognition.
Consider the Technology
Different print inspection systems utilize varying technologies.
Some use vision systems with high-quality cameras, while others rely on more complex sensors and software.
For SMEs, it would be wise to choose a system that is user-friendly and easy to integrate into existing operations without requiring extensive training or expertise.
Furthermore, ensure that the system can handle the types of materials and colors you frequently use.
Budget and Cost-Effectiveness
Cost is a significant consideration for any SME.
Analyze the potential return on investment (ROI) of the inspection system.
While high-end systems might promise many features, ensure that they bring tangible improvements to your processes and justify the expenditure.
Take into account not only the initial purchase price but also long-term running costs, including maintenance and updates.
Implementing Print Inspection Systems
Once you’ve chosen the right system, successfully implementing it is the next challenge.
Effective implementation ensures that you receive the full benefits of your investment.
Integration Into Existing Workflows
The inspection system should seamlessly integrate with your current production processes.
Work with the supplier to understand installation requirements and necessary adjustments to your workflow.
A system that’s compatible with your existing equipment reduces downtime during the transition and helps in quick ramp-up.
Training Your Team
While many systems are designed to be intuitive, effective training is crucial.
Ensure your team receives thorough training on how to operate the system efficiently.
Understanding both the hardware and software components is vital for swift troubleshooting and optimizing system performance.
Monitoring and Feedback
Regular monitoring of the system’s performance is integral to its success.
Set up feedback loops to continually assess the performance and make necessary adjustments.
Review inspection data to identify patterns and areas for improvement, helping you refine the system settings and achieve higher accuracy.
The Future of Print Inspection for SMEs
The future of print inspection systems for SMEs looks promising, with continuous technological advancements lowering costs and improving capabilities.
Machine learning and AI are increasingly being incorporated into these systems, offering even greater improvements in defect detection and prediction.
As more SMEs adopt these systems, we will likely see an industry-wide enhancement in print quality standards.
Print inspection systems promise a host of efficiencies and quality improvements for SMEs.
By carefully selecting and implementing these systems, businesses can not only protect their brand reputation but also leverage this technology to gain a competitive edge in the marketplace.
Investing in such technology today can pave the way for increased profitability and market share tomorrow.
資料ダウンロード
QCD調達購買管理クラウド「newji」は、調達購買部門で必要なQCD管理全てを備えた、現場特化型兼クラウド型の今世紀最高の購買管理システムとなります。
ユーザー登録
調達購買業務の効率化だけでなく、システムを導入することで、コスト削減や製品・資材のステータス可視化のほか、属人化していた購買情報の共有化による内部不正防止や統制にも役立ちます。
NEWJI DX
製造業に特化したデジタルトランスフォーメーション(DX)の実現を目指す請負開発型のコンサルティングサービスです。AI、iPaaS、および先端の技術を駆使して、製造プロセスの効率化、業務効率化、チームワーク強化、コスト削減、品質向上を実現します。このサービスは、製造業の課題を深く理解し、それに対する最適なデジタルソリューションを提供することで、企業が持続的な成長とイノベーションを達成できるようサポートします。
オンライン講座
製造業、主に購買・調達部門にお勤めの方々に向けた情報を配信しております。
新任の方やベテランの方、管理職を対象とした幅広いコンテンツをご用意しております。
お問い合わせ
コストダウンが利益に直結する術だと理解していても、なかなか前に進めることができない状況。そんな時は、newjiのコストダウン自動化機能で大きく利益貢献しよう!
(Β版非公開)