- お役立ち記事
- A Look at Semiconductor Factory Workflows from an Employee’s Perspective
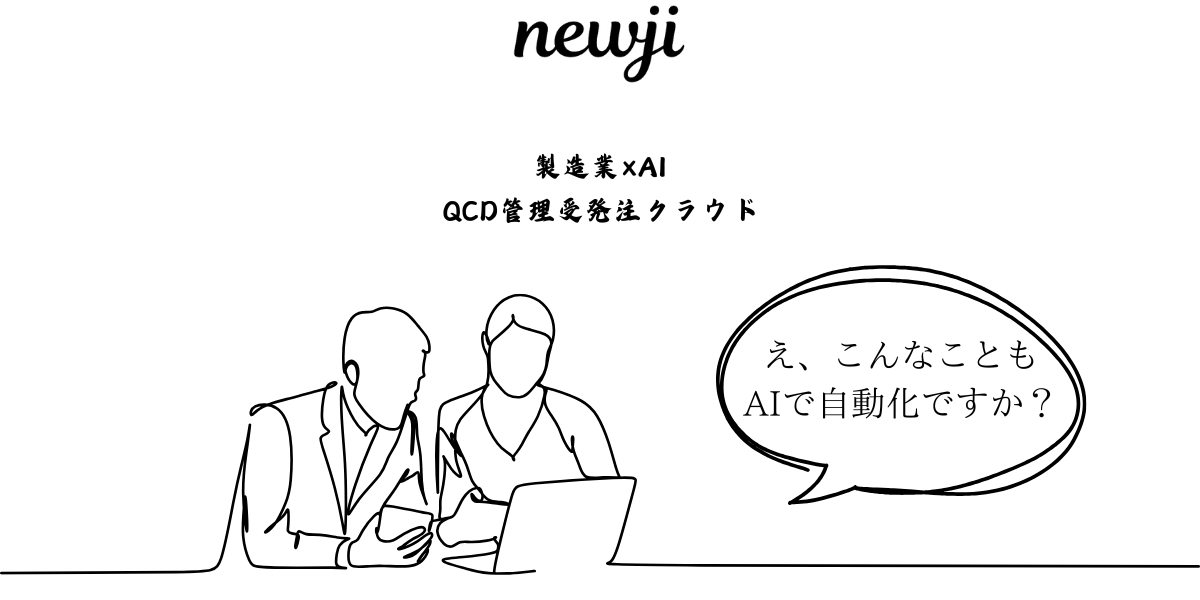
A Look at Semiconductor Factory Workflows from an Employee’s Perspective
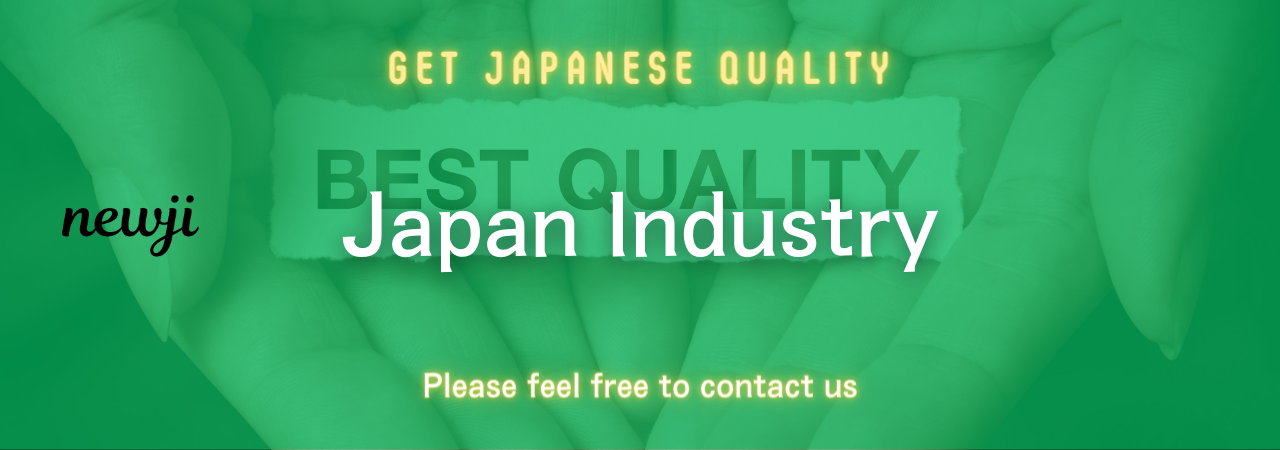
目次
Introduction to Semiconductor Factories
In the modern tech-driven world, semiconductor factories play a crucial role.
These factories produce the chips that power our everyday electronics, from smartphones to laptops and even cars.
Understanding the workflows within these factories offers insight into how these essential components make their way from raw materials to finished products.
By exploring semiconductor factory processes from an employee’s perspective, we can appreciate the complexity and precision involved in their production.
The Start of the Process: Wafer Production
The journey of a semiconductor begins with the creation of wafers, which are thin slices of semiconductor material, typically silicon, used as the base for chip fabrication.
Employees in this stage are responsible for purification and crystal growth, creating cylinders known as ingots.
The wafers are then sliced from these ingots and polished to an ultra-smooth finish.
Factory workers must handle these wafers with extreme care to prevent contamination or damage.
The process demands high precision and attention to detail, as any imperfections can affect the entire chip production process.
Cleanroom Operations
A significant part of semiconductor manufacturing occurs in cleanrooms, highly controlled environments that maintain low levels of pollutants such as dust, airborne microbes, and chemical vapors.
This is crucial because even the tiniest speck of dust can ruin an entire wafer.
Employees wear specialized suits known as “bunny suits” to prevent contamination.
These suits cover the entire body and are made from materials that do not shed particles.
Working in a cleanroom requires adherence to strict hygiene protocols and routines, ensuring equipment and materials remain uncontaminated.
Importance of the Cleanroom
The cleanroom environment is essential for achieving the high precision needed in semiconductor manufacturing.
Employees perform tasks ranging from photolithography to etching and ion implantation here.
Each step must be executed with exacting precision to ensure that the complex circuits on a chip function correctly.
Photolithography and Circuit Printing
Once the wafers are prepared, they move to the crucial step of photolithography, where circuit patterns are transferred onto the wafer.
This process involves coating the wafer with a light-sensitive material called photoresist.
Employees use photomasks to shine ultraviolet light onto the wafer, thereby imprinting the intricate circuit design.
Any deviation in this step can affect the performance of the final chip.
Regular checks and calibrations are performed by employees to ensure every layer of the circuit aligns perfectly.
Etching and Layering
After photolithography, the wafers undergo etching, where the exposed areas are chemically removed.
This step is crucial for creating the microscopic pathways that electricity will flow through.
Employees oversee this process to ensure precision and correct dimensions of the etched sections.
The wafers go through multiple etching phases, depending on how complex the chip design is.
Moreover, the layering process involves adding successive layers of materials that contribute to the chip’s functionality.
Critical Role of Precision
At this stage, every atom-sized feature counts.
The employees’ ability to maintain precision affects the overall product quality and yield.
Continuous training and experience are essential, as employees strive to optimize the processes to reduce defects and enhance efficiency.
Testing and Quality Assurance
Before reaching the final packaging stage, chips undergo rigorous testing to ensure they meet quality and performance standards.
Employees conduct a series of electrical tests on the completed wafers to check for any faults.
Those that pass these tests are cut into individual chips, while defective ones are discarded or reworked if possible.
Quality assurance teams play a vital role, ensuring that only products meeting stringent standards move forward.
This attention to detail is what makes semiconductor components reliable and efficient.
Packaging and Final Steps
The final stage of the manufacturing process involves packaging the chips.
This not only protects them but also prepares them for integration into electronic devices.
Employees in this department design and assemble chip packages, ensuring proper thermal and electrical performance.
Communication between teams is crucial, as they must ensure that every chip fits its intended specifications.
Employee Insights
Employees often describe their roles as challenging yet rewarding.
The precision and intricate nature of the work demand a high level of skill and concentration.
Attention to detail and a willingness to adapt to new technologies are common themes in their experiences.
Conclusion
The journey of a semiconductor from raw silicon to a functioning chip is a complex one.
By examining the workflows from an employee’s perspective, we gain a deeper understanding of the skill and precision required in this industry.
From wafer production to final packaging, each step is meticulously planned and executed.
This process supports the functioning of countless devices that define modern life, highlighting the importance of semiconductor factory workflows.
資料ダウンロード
QCD調達購買管理クラウド「newji」は、調達購買部門で必要なQCD管理全てを備えた、現場特化型兼クラウド型の今世紀最高の購買管理システムとなります。
ユーザー登録
調達購買業務の効率化だけでなく、システムを導入することで、コスト削減や製品・資材のステータス可視化のほか、属人化していた購買情報の共有化による内部不正防止や統制にも役立ちます。
NEWJI DX
製造業に特化したデジタルトランスフォーメーション(DX)の実現を目指す請負開発型のコンサルティングサービスです。AI、iPaaS、および先端の技術を駆使して、製造プロセスの効率化、業務効率化、チームワーク強化、コスト削減、品質向上を実現します。このサービスは、製造業の課題を深く理解し、それに対する最適なデジタルソリューションを提供することで、企業が持続的な成長とイノベーションを達成できるようサポートします。
オンライン講座
製造業、主に購買・調達部門にお勤めの方々に向けた情報を配信しております。
新任の方やベテランの方、管理職を対象とした幅広いコンテンツをご用意しております。
お問い合わせ
コストダウンが利益に直結する術だと理解していても、なかなか前に進めることができない状況。そんな時は、newjiのコストダウン自動化機能で大きく利益貢献しよう!
(Β版非公開)