- お役立ち記事
- A manufacturing efficiency method that integrates safety management and maintenance planning
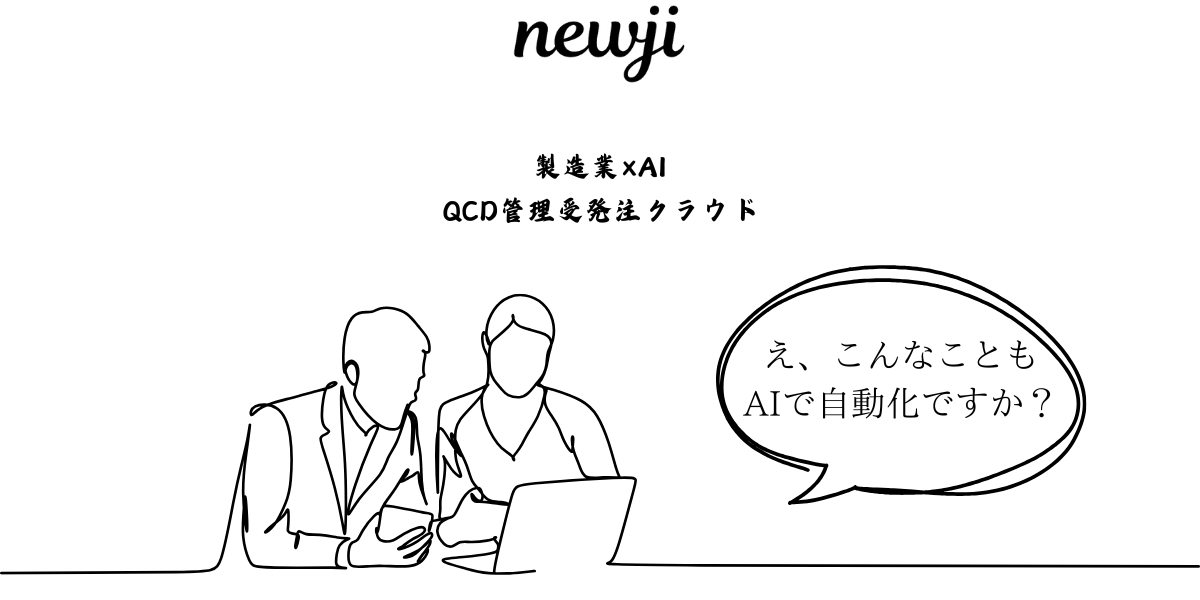
A manufacturing efficiency method that integrates safety management and maintenance planning
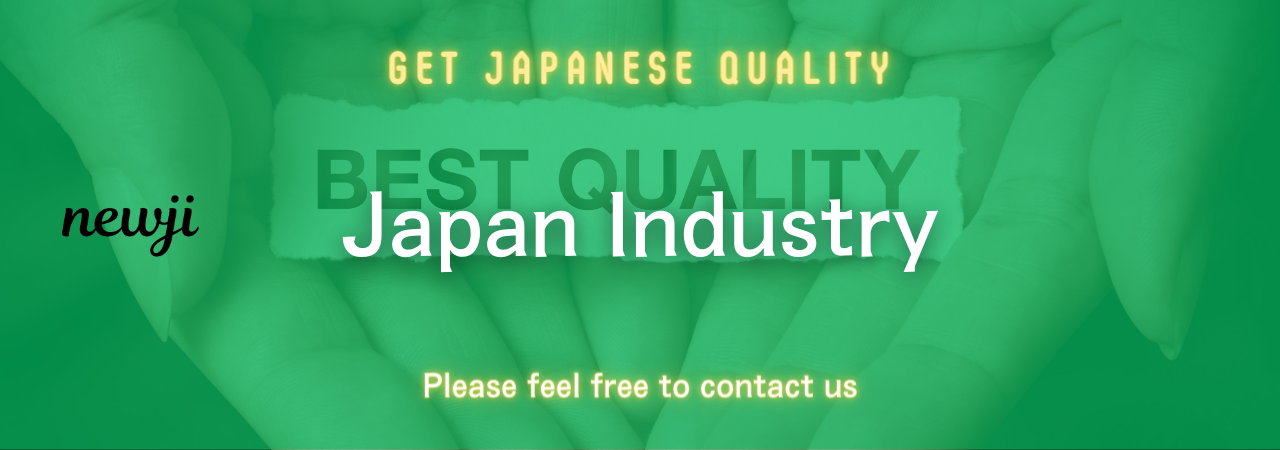
目次
Understanding the Importance of Manufacturing Efficiency
In today’s fast-paced industrial landscape, manufacturing efficiency is more important than ever.
It’s not just about producing goods at a rapid rate but doing so cost-effectively while maintaining high-quality standards.
Efficiency in manufacturing equates to optimized use of resources, reduced waste, and increased profitability.
Yet, achieving this level of efficiency isn’t solely about mechanics and technology.
It involves a seamless integration of safety management and maintenance planning, ensuring smooth operations without compromising on worker safety or product quality.
The Role of Safety Management in Manufacturing
Safety management plays a critical role in manufacturing efficiency.
An unsafe work environment can lead to accidents, which not only disrupt production but also incur significant costs.
Implementing a robust safety management system helps in identifying potential risks and mitigating them before they can cause harm.
When workers feel safe, they are more likely to operate machines smoothly and with confidence, enhancing overall productivity.
Furthermore, a culture of safety ensures compliance with industry regulations, avoiding legal issues that can further disrupt manufacturing processes.
The Significance of Maintenance Planning
Effective maintenance planning is another pillar of efficient manufacturing.
Equipment downtime is one of the biggest culprits of production delays and inefficiencies.
A thorough maintenance plan includes regular checks, timely repairs, and routine updates to keep machinery in optimal working condition.
This proactivity reduces the likelihood of unexpected breakdowns, which can disrupt the entire production line.
Moreover, well-maintained equipment operates more efficiently, ensuring consistent product quality and reducing waste.
Integrating Safety Management and Maintenance Planning
For maximum manufacturing efficiency, it’s essential to integrate safety management with maintenance planning.
Traditionally, these two aspects might have been handled separately, but their synergy can lead to remarkable improvements in productivity.
When safety protocols are aligned with maintenance schedules, potential hazards can be identified during routine checks.
This not only safeguards employees but also helps in recognizing mechanical issues that might otherwise go unnoticed.
Career development opportunities arise for employees who are trained in both safety and maintenance, creating a more versatile workforce.
Creating a Comprehensive Integration Framework
Developing a framework that amalgamates safety management and maintenance planning requires thorough analysis and strategic planning.
Begin by assessing your current safety and maintenance strategies to identify areas of overlap.
For instance, regular maintenance checks can incorporate safety inspections as a dual-purpose activity.
An integrated framework should also align with the company’s overall goals, including compliance with safety regulations and production targets.
Employee training programs play a vital role in this integration, enhancing awareness and understanding of the dual aspects of their roles.
Leveraging Technology for Integration
Advancements in technology can significantly aid the integration of safety management and maintenance planning.
Use of data analytics allows for predictive maintenance, alerting teams to potential equipment failures before they occur.
Similarly, safety management systems equipped with real-time monitoring can proactively address potential hazards.
Digital platforms can facilitate the coordination between safety and maintenance teams, ensuring seamless communication and workflow management.
IoT devices offer valuable insights into machine performance and worker safety, presenting an opportunity for immediate problem resolution.
Embracing these technologies not only smoothens the integration process but also provides a competitive edge in a constantly evolving industry.
Measuring the Impact of Integrated Approaches
Once implemented, it’s crucial to measure the impact of integrated safety management and maintenance planning on manufacturing efficiency.
Key performance indicators (KPIs) should be established to assess improvements in productivity, safety compliance, and machinery uptime.
Regular audits and feedback loops ensure that the integration remains effective and can evolve with changing manufacturing dynamics.
Reviews should also consider employee satisfaction, as a well-integrated system can alleviate stress and enhance job performance.
The findings from these assessments can guide further refinement and adjustment of both safety and maintenance strategies.
Challenges in Integration and How to Overcome Them
Despite the clear benefits, integrating safety management and maintenance planning may present challenges.
Resistance to change is a common hurdle, especially if employees are accustomed to traditional methods.
To overcome this, it’s essential to foster a culture of openness and provide comprehensive training to ease the transition.
Communication is key; ensure that all team members understand the purpose and benefits of integration.
Sometimes, budget constraints might limit the extent of technological enhancements, but prioritizing critical areas can mitigate these limitations.
Finally, continuous improvement and adaptability are crucial, ensuring the integrated approach remains relevant in a modern manufacturing setting.
Conclusion: A Future-Ready Manufacturing Approach
Integrating safety management with maintenance planning is not just a trend, but a necessary evolution for manufacturing efficiency.
By combining these two critical components, manufacturers can ensure a safer work environment, extend equipment life, and maintain high productivity levels.
Investing in training, adopting suitable technologies, and fostering an adaptable culture will pave the way for a future-ready manufacturing approach.
This holistic strategy not only meets current demands but also prepares businesses for the challenges and opportunities of the future industry landscape.
資料ダウンロード
QCD調達購買管理クラウド「newji」は、調達購買部門で必要なQCD管理全てを備えた、現場特化型兼クラウド型の今世紀最高の購買管理システムとなります。
ユーザー登録
調達購買業務の効率化だけでなく、システムを導入することで、コスト削減や製品・資材のステータス可視化のほか、属人化していた購買情報の共有化による内部不正防止や統制にも役立ちます。
NEWJI DX
製造業に特化したデジタルトランスフォーメーション(DX)の実現を目指す請負開発型のコンサルティングサービスです。AI、iPaaS、および先端の技術を駆使して、製造プロセスの効率化、業務効率化、チームワーク強化、コスト削減、品質向上を実現します。このサービスは、製造業の課題を深く理解し、それに対する最適なデジタルソリューションを提供することで、企業が持続的な成長とイノベーションを達成できるようサポートします。
オンライン講座
製造業、主に購買・調達部門にお勤めの方々に向けた情報を配信しております。
新任の方やベテランの方、管理職を対象とした幅広いコンテンツをご用意しております。
お問い合わせ
コストダウンが利益に直結する術だと理解していても、なかなか前に進めることができない状況。そんな時は、newjiのコストダウン自動化機能で大きく利益貢献しよう!
(Β版非公開)