- お役立ち記事
- A method for achieving both logistics optimization and quality assurance for the purchasing department
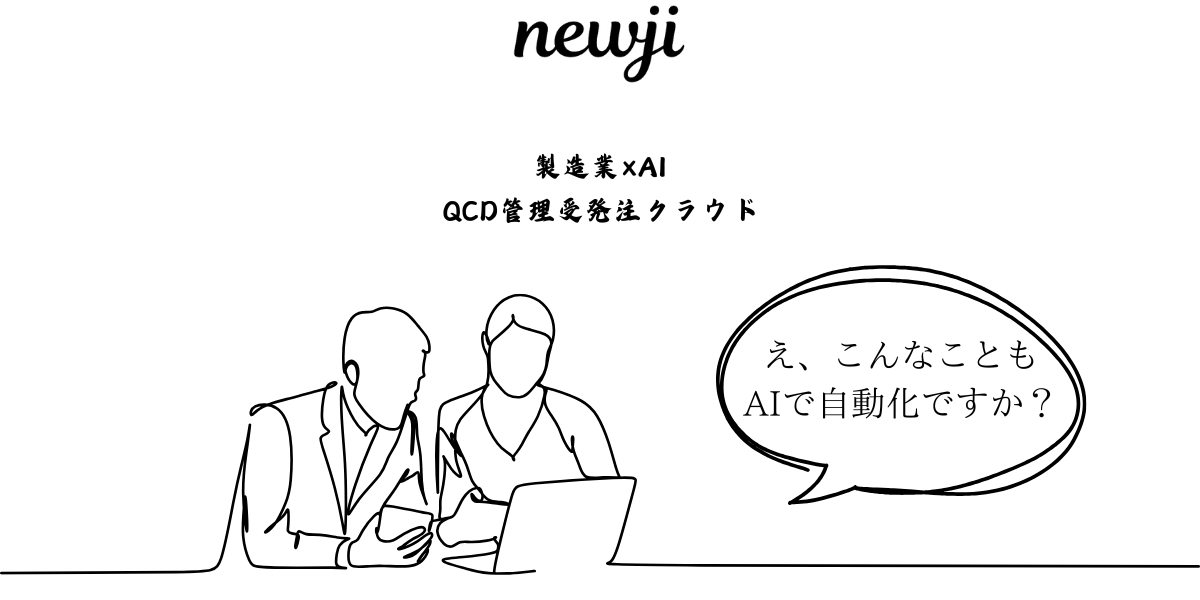
A method for achieving both logistics optimization and quality assurance for the purchasing department
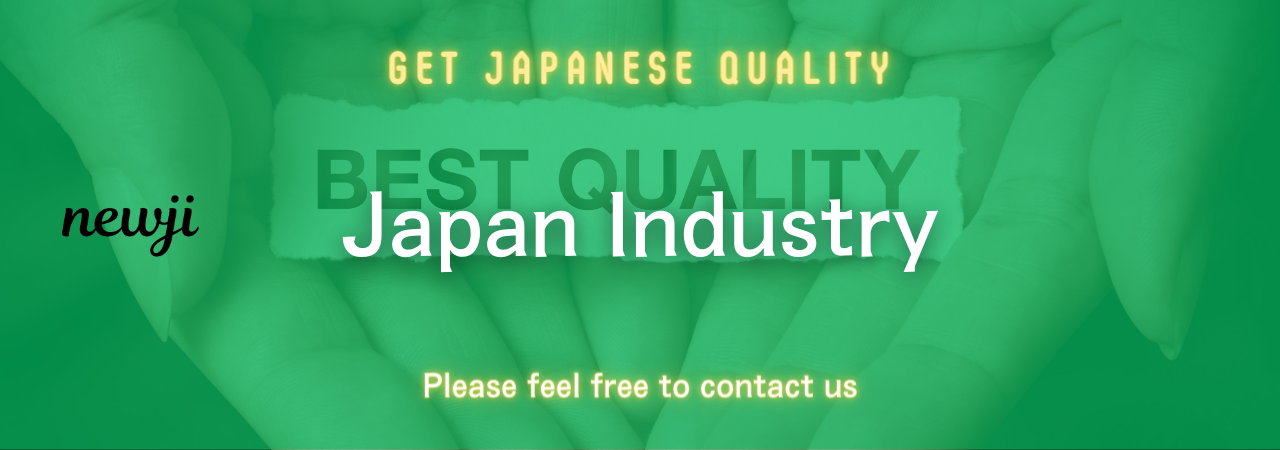
目次
Understanding the Importance of Logistics and Quality in Purchasing
When it comes to the purchasing department, achieving a balance between logistics optimization and quality assurance is crucial for the success of any organization.
The purchasing department is responsible for acquiring goods and services, which means they play a critical role in ensuring that operations run smoothly.
This function affects not only the cost but also the efficiency of the supply chain.
Logistics optimization ensures that the right products are delivered at the right time and in the most cost-effective way.
On the other hand, quality assurance focuses on maintaining standards to meet customer expectations and regulatory requirements.
Achieving both goals can seem daunting, but with the right approach, it can lead to improved performance and better customer satisfaction.
Strategies for Logistics Optimization
To achieve logistics optimization, the purchasing department must implement strategies that streamline processes and reduce waste without compromising on service quality.
Supplier Selection and Relationship Management
Choosing the right suppliers is the foundation of effective logistics.
The purchasing team should thoroughly assess potential suppliers based on their reliability, delivery speed, and cost-effectiveness.
Building strong relationships with suppliers can lead to better terms, more flexible services, and a reliable supply of products.
Inventory Management
Efficient inventory management is critical for optimizing logistics.
By using data analytics and forecasting techniques, the purchasing department can maintain optimal inventory levels.
This balances the need to avoid stockouts with minimizing excess inventory costs.
Just-in-time (JIT) inventory systems can significantly enhance efficiency by aligning inventory levels closely with actual demand.
Adopting Technology
Leveraging technology, such as automated procurement systems and advanced tracking tools, can vastly improve logistics processes.
These tools provide real-time visibility into supply chain activities, allowing the purchasing team to make informed decisions quickly.
Implementing an electronic data interchange (EDI) system can further streamline communication between suppliers and buyers.
Ensuring Quality Assurance
Quality assurance is equally vital, and the purchasing department must develop a rigorous approach to maintaining high standards.
Comprehensive Supplier Audits
Conducting regular supplier audits helps ensure compliance with quality standards.
These audits can identify potential issues early on, preventing defective products from entering the supply chain.
Criteria for audits should include the supplier’s adherence to industry standards and their ability to meet specifications consistently.
Setting Clear Quality Standards
The purchasing department should establish clear quality criteria and communicate these to all suppliers.
Standards should be part of the negotiation and contract process, ensuring that suppliers know the expectations upfront.
Regular evaluations and feedback help maintain these standards over time.
Sample Testing and Inspection
Implementing a systematic approach to sample testing and product inspection ensures that any deviations from quality standards are detected before products reach customers.
This step is essential for protecting the organization’s reputation and ensuring customer satisfaction.
Integrating Logistics and Quality for Optimal Results
Achieving both logistics optimization and quality assurance simultaneously requires an integrated approach.
Collaborative Planning
Frequent collaboration between the logistics and quality assurance teams is key.
By sharing information and planning together, teams can anticipate issues and develop solutions that address both logistics efficiency and quality assurance.
Continuous Improvement
The purchasing department should adopt a culture of continuous improvement.
Regular reviews of processes and performance metrics allow for ongoing adjustments and enhancements.
Encouraging feedback from suppliers and internal stakeholders can also identify areas for improvement.
Balancing Cost and Quality
While optimizing for cost, it is critical not to overlook quality.
Cost savings achieved at the expense of quality can lead to dissatisfied customers and additional expenses in the long-term.
A balanced approach that considers total cost of ownership, including quality, delivery, and service, ultimately drives better results.
Conclusion
The purchasing department holds the key to balancing logistics optimization and quality assurance.
With strategic supplier relationships, efficient inventory management, robust technology adoption, and a strong focus on quality standards, it can achieve this balance effectively.
Harnessing collaboration and fostering a culture of continuous improvement further enhances the department’s ability to meet organizational goals.
By carefully integrating logistics and quality efforts, companies can improve operational efficiency, reduce costs, and maintain high-quality standards, leading to increased customer satisfaction and long-term success.
資料ダウンロード
QCD調達購買管理クラウド「newji」は、調達購買部門で必要なQCD管理全てを備えた、現場特化型兼クラウド型の今世紀最高の購買管理システムとなります。
ユーザー登録
調達購買業務の効率化だけでなく、システムを導入することで、コスト削減や製品・資材のステータス可視化のほか、属人化していた購買情報の共有化による内部不正防止や統制にも役立ちます。
NEWJI DX
製造業に特化したデジタルトランスフォーメーション(DX)の実現を目指す請負開発型のコンサルティングサービスです。AI、iPaaS、および先端の技術を駆使して、製造プロセスの効率化、業務効率化、チームワーク強化、コスト削減、品質向上を実現します。このサービスは、製造業の課題を深く理解し、それに対する最適なデジタルソリューションを提供することで、企業が持続的な成長とイノベーションを達成できるようサポートします。
オンライン講座
製造業、主に購買・調達部門にお勤めの方々に向けた情報を配信しております。
新任の方やベテランの方、管理職を対象とした幅広いコンテンツをご用意しております。
お問い合わせ
コストダウンが利益に直結する術だと理解していても、なかなか前に進めることができない状況。そんな時は、newjiのコストダウン自動化機能で大きく利益貢献しよう!
(Β版非公開)