- お役立ち記事
- A method for simultaneously achieving lead time reduction and quality assurance promoted by the purchasing department
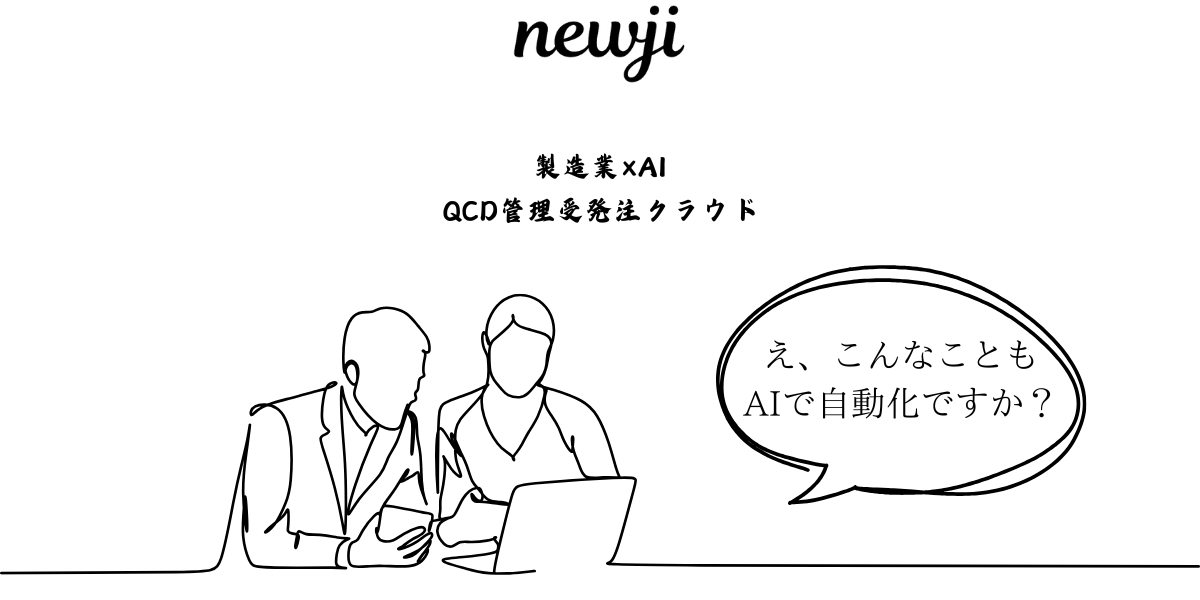
A method for simultaneously achieving lead time reduction and quality assurance promoted by the purchasing department
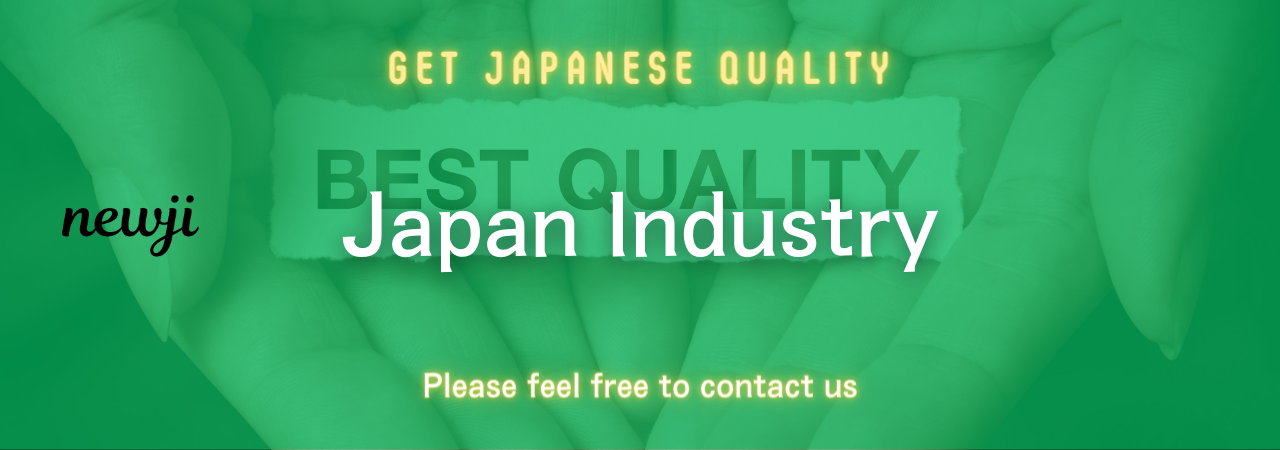
目次
Introduction
Every organization seeks to enhance its operational efficiency while maintaining high-quality standards.
A key player in achieving this balance is the purchasing department.
This crucial department has the potential to reduce lead times and ensure quality assurance simultaneously by adopting strategic methods and processes.
Importance of Lead Time Reduction
Lead time is the duration between a customer’s order placement and its fulfillment.
Reducing this time can significantly enhance a company’s competitiveness.
Quicker lead times mean faster delivery, which can improve customer satisfaction and increase market share.
From a company’s perspective, minimizing lead times can also decrease inventory costs.
Less inventory means less capital tied up in storing goods, freeing up resources for other business pursuits.
Challenges in Reducing Lead Time
Despite its advantages, reducing lead time is not without challenges.
Shorter cycles require faster supplier responses and streamlined internal processes.
Fluctuating demand, complex supply chains, and supplier delays can hinder the speed at which orders are processed.
Hence, the purchasing department must adopt innovative methods to address these challenges effectively.
Quality Assurance: A Non-Negotiable Factor
Maintaining quality assurance is paramount in any procurement process.
Quality refers to the consistency and reliability of products or services that meet established standards.
A decrease in product quality can lead to increased returns and dissatisfied customers.
Therefore, achieving quality assurance should not be compromised even when the focus is on reducing lead time.
Balancing Quality and Speed
The challenge for the purchasing department is balancing reduced lead times with consistent quality.
Often, attempts to accelerate processes may lead to overlooked errors, affecting the final product quality.
It is essential to integrate comprehensive quality checks with swift processes.
This ensures that quality assurance remains a priority even as lead times decrease.
Strategies for Achieving Both Goals
To simultaneously reduce lead times and maintain quality assurance, the purchasing department can adopt several strategies.
Building Strong Supplier Relationships
Constructing reliable relationships with suppliers is a fundamental step.
Having reliable suppliers ensures consistent quality and timely deliveries.
Engage suppliers in regular communication to discuss expectations, potential challenges, and improvement areas.
This open dialogue fosters a collaborative environment, making it easier to navigate any potential disruptions.
Implementing Technology Solutions
Technological advancements can significantly streamline procurement processes.
Investing in procurement software can enhance tracking capabilities, ensuring real-time updates for order statuses.
Automation tools can reduce manual errors and free up time for staff to focus on strategic tasks.
Additionally, data analytics can provide insights into supplier performance, enabling better decision-making.
Enhancing Supplier Evaluations
Regularly assessing suppliers is crucial for ensuring quality and dependability.
Evaluate suppliers based on their delivery timeliness, product quality, and responsiveness.
Use these evaluations to identify which suppliers consistently meet standards and where improvements or changes are necessary.
This continual assessment can help in prioritizing suppliers who align with the company’s goals.
Streamlining Internal Processes
Efficiency within the organization is just as crucial as external supplier management.
Analyze internal workflows to identify bottlenecks or redundant procedures.
Implement changes that optimize these processes, such as reducing unnecessary paperwork or approvals.
A lean internal process will contribute to reducing lead times without impacting quality.
Empowering the Purchasing Team
The effectiveness of the purchasing department lies in the hands of its team.
Invest in training programs that equip staff with the latest industry knowledge and skills.
Encourage team members to engage in workshops and seminars focused on procurement best practices.
A knowledgeable team is better equipped to make informed decisions quickly and effectively.
Encouraging a Quality-First Mindset
Cultivating a culture that prioritizes quality is essential.
Communicate the importance of quality assurance across the company, ensuring it is embedded in every process.
This culture should align with speed objectives to ensure that both lead time reduction and quality assurance are integral to the organization’s values.
Continuous Improvement and Feedback
Commit to a strategy of continuous improvement.
Use customer feedback and performance metrics to refine procurement processes.
Devise regular reviews of procurement strategies to adapt to the changing market conditions and technological advancements.
This adaptive approach ensures that the company remains competitive and efficient.
Conclusion
The purchasing department has a crucial role in reducing lead times while ensuring quality assurance.
By adopting strategic methods and leveraging technology, procurement processes can be both efficient and reliable.
Building strong supplier relationships and streamlining both external and internal processes are key to achieving this dual objective.
Ultimately, by fostering a culture that emphasizes quality alongside speed, businesses can satisfy customer demands while remaining a step ahead in their industries.
資料ダウンロード
QCD調達購買管理クラウド「newji」は、調達購買部門で必要なQCD管理全てを備えた、現場特化型兼クラウド型の今世紀最高の購買管理システムとなります。
ユーザー登録
調達購買業務の効率化だけでなく、システムを導入することで、コスト削減や製品・資材のステータス可視化のほか、属人化していた購買情報の共有化による内部不正防止や統制にも役立ちます。
NEWJI DX
製造業に特化したデジタルトランスフォーメーション(DX)の実現を目指す請負開発型のコンサルティングサービスです。AI、iPaaS、および先端の技術を駆使して、製造プロセスの効率化、業務効率化、チームワーク強化、コスト削減、品質向上を実現します。このサービスは、製造業の課題を深く理解し、それに対する最適なデジタルソリューションを提供することで、企業が持続的な成長とイノベーションを達成できるようサポートします。
オンライン講座
製造業、主に購買・調達部門にお勤めの方々に向けた情報を配信しております。
新任の方やベテランの方、管理職を対象とした幅広いコンテンツをご用意しております。
お問い合わせ
コストダウンが利益に直結する術だと理解していても、なかなか前に進めることができない状況。そんな時は、newjiのコストダウン自動化機能で大きく利益貢献しよう!
(Β版非公開)