- お役立ち記事
- A must-read for managers! How to introduce and establish a “quality management system” aimed at by management
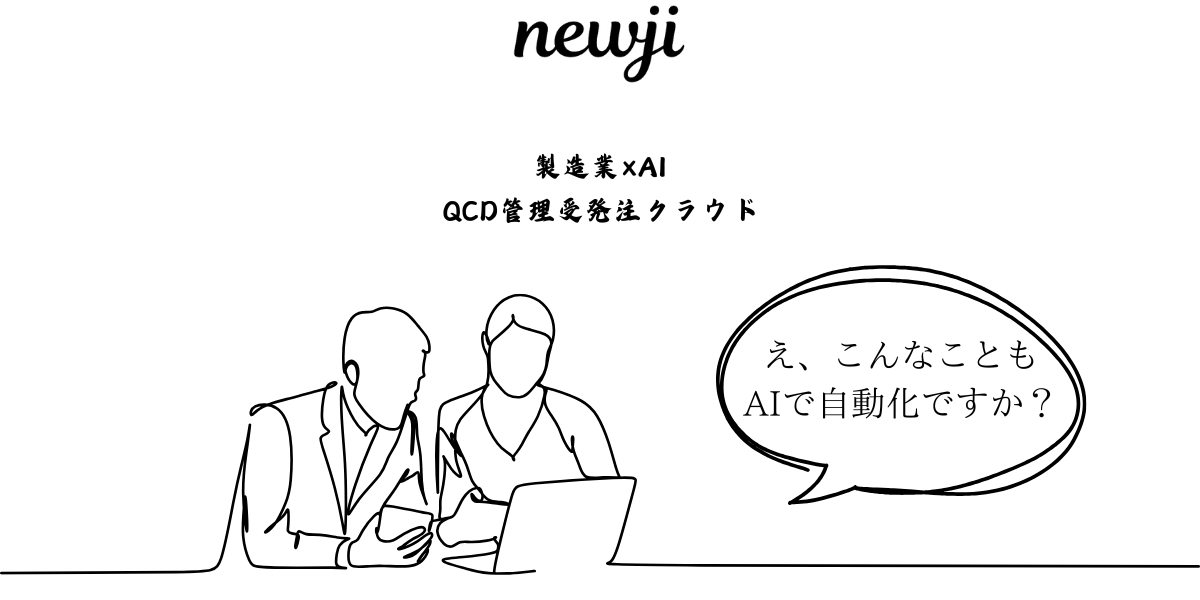
A must-read for managers! How to introduce and establish a “quality management system” aimed at by management
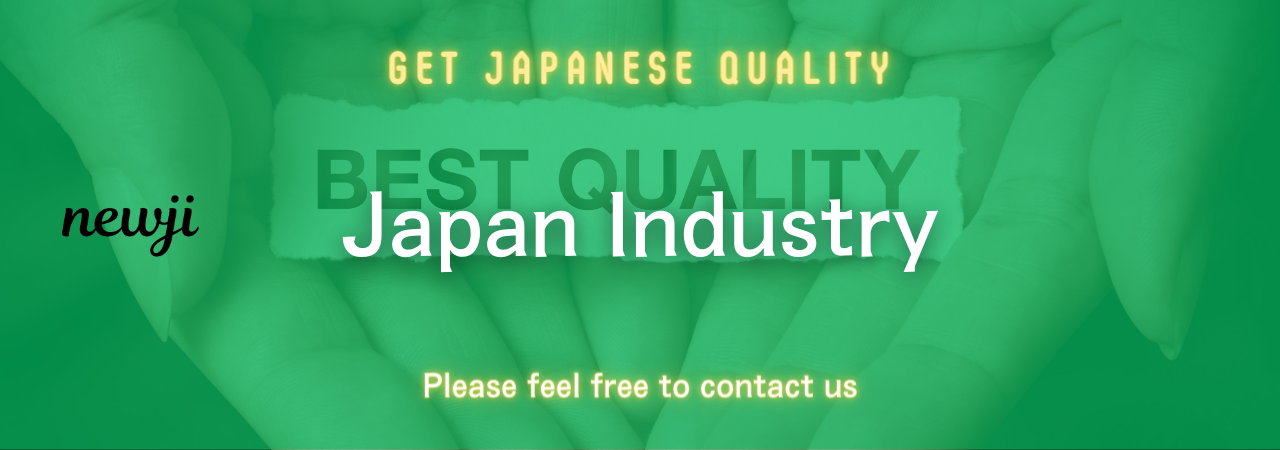
目次
Understanding the Quality Management System
In today’s competitive business environment, maintaining high standards of quality is no longer optional for companies aiming for long-term success.
A robust Quality Management System (QMS) serves as the backbone to ensure products and services meet customer expectations and regulatory requirements.
As a manager, introducing and establishing a QMS is key to achieving organizational excellence and sustainability.
At its core, a QMS is a set of policies, processes, and procedures implemented by an organization to manage and improve their quality performance.
The system is designed to help organizations achieve consistent product quality, enhance customer satisfaction, and streamline operations.
It provides a methodical approach to defect prevention, risk management, and continuous improvement.
Steps to Introduce a Quality Management System
The introduction of a Quality Management System can seem daunting initially, but by following a structured approach, managers can seamlessly integrate it into the organizational framework.
1. Obtain Top Management Commitment
The first and foremost step in implementing a QMS is securing commitment from top management.
A successful QMS implementation hinges on the leadership actively endorsing and participating in the process.
Managers need to clearly communicate the benefits of a QMS, such as increased efficiency, customer satisfaction, and compliance, to secure the necessary support and resources.
2. Conduct a Gap Analysis
Before implementing a QMS, it is crucial to conduct a comprehensive gap analysis.
This assessment helps identify the current practices and procedures in place and their alignment with quality standards.
A detailed gap analysis will reveal areas of improvement and highlight the changes needed to conform to international standards like ISO 9001.
3. Define Organizational Objectives and Quality Policies
Once management is on board and a gap analysis is complete, the next step is to define clear organizational objectives and quality policies.
These should align with the broader strategic goals of the company and provide a roadmap for the QMS implementation.
The objectives should be Specific, Measurable, Achievable, Relevant, and Time-bound (SMART) to facilitate focused efforts.
4. Develop a QMS Framework
Developing a QMS framework involves creating and documenting policies, processes, and procedures that meet quality standards.
This includes designing quality manuals, procedural documents, work instructions, and process maps, among others.
Ensuring that these documents are easily accessible and understood by all employees is essential for effective implementation.
5. Provide Training and Allocate Resources
Training is a critical component of QMS implementation.
Employees at all levels should receive adequate training on the QMS processes, their role in maintaining quality, and the benefits of a sound quality management system.
It is also important to allocate sufficient resources, including human resources, technology, and budget, to support the successful rollout of the QMS.
6. Implement the System
With a well-defined framework and trained personnel, the organization can begin implementing the QMS.
This involves careful execution of documented workflows and processes across various departments.
Regular communication and collaboration between teams enhance understanding and effectiveness of QMS protocols.
Establishing and Maintaining a Quality Management System
Introducing a QMS is only the beginning.
For a QMS to be effective, it requires ongoing monitoring, evaluation, and improvement.
1. Conduct Regular Audits
Audits are essential tools for verifying compliance with the QMS and identifying areas for improvement.
Regular internal and external audits help assess the effectiveness of the QMS by examining processes, reviewing records, and evaluating performance metrics.
These audits provide valuable insights and ensure the system remains aligned with organizational goals.
2. Foster a Culture of Continuous Improvement
Quality management is an ongoing process that requires a commitment to continuous improvement (CI).
Managers should encourage a culture where employees proactively identify opportunities for improvement and innovation.
Techniques such as the Plan-Do-Check-Act (PDCA) cycle and Lean Six Sigma methodologies can support CI efforts effectively.
3. Analyze Customer Feedback
Customer feedback is a valuable source of information for maintaining and improving product quality and service delivery.
By analyzing feedback and addressing grievances, organizations can identify recurring issues and adapt quality processes to better meet customer needs and expectations.
4. Use Data for Decision Making
Data-driven decision-making plays a crucial role in the success of a QMS.
Using data and analytics enables better understanding of process efficiency, product quality, and customer satisfaction.
By leveraging real-time data, managers can make informed decisions that foster a proactive approach to quality management.
5. Continuously Update and Innovate
As business landscapes evolve, so too must the organization’s QMS.
It is essential to stay updated with industry trends, technological advancements, and regulatory changes.
Continuous review and adaptation of the QMS are necessary to ensure it remains relevant and effective in enhancing organizational performance.
Conclusion
Introducing and establishing a robust Quality Management System is crucial for sustaining business growth and achieving operational excellence.
Managers play a pivotal role in advocating for, designing, and implementing a QMS that not only meets regulatory requirements but also enhances customer satisfaction and facilitates continuous improvement.
By gaining top management commitment, conducting thorough analyses, defining clear objectives, and evaluating ongoing performance, organizations can effectively maintain a QMS that aligns with their strategic vision.
Ultimately, a successful QMS implementation can drive competitive advantage and establish an organization as a leader in quality management.
資料ダウンロード
QCD調達購買管理クラウド「newji」は、調達購買部門で必要なQCD管理全てを備えた、現場特化型兼クラウド型の今世紀最高の購買管理システムとなります。
ユーザー登録
調達購買業務の効率化だけでなく、システムを導入することで、コスト削減や製品・資材のステータス可視化のほか、属人化していた購買情報の共有化による内部不正防止や統制にも役立ちます。
NEWJI DX
製造業に特化したデジタルトランスフォーメーション(DX)の実現を目指す請負開発型のコンサルティングサービスです。AI、iPaaS、および先端の技術を駆使して、製造プロセスの効率化、業務効率化、チームワーク強化、コスト削減、品質向上を実現します。このサービスは、製造業の課題を深く理解し、それに対する最適なデジタルソリューションを提供することで、企業が持続的な成長とイノベーションを達成できるようサポートします。
オンライン講座
製造業、主に購買・調達部門にお勤めの方々に向けた情報を配信しております。
新任の方やベテランの方、管理職を対象とした幅広いコンテンツをご用意しております。
お問い合わせ
コストダウンが利益に直結する術だと理解していても、なかなか前に進めることができない状況。そんな時は、newjiのコストダウン自動化機能で大きく利益貢献しよう!
(Β版非公開)