- お役立ち記事
- A must-read for purchasing department leaders! Timing and key points of “supplier contract review”
A must-read for purchasing department leaders! Timing and key points of “supplier contract review”
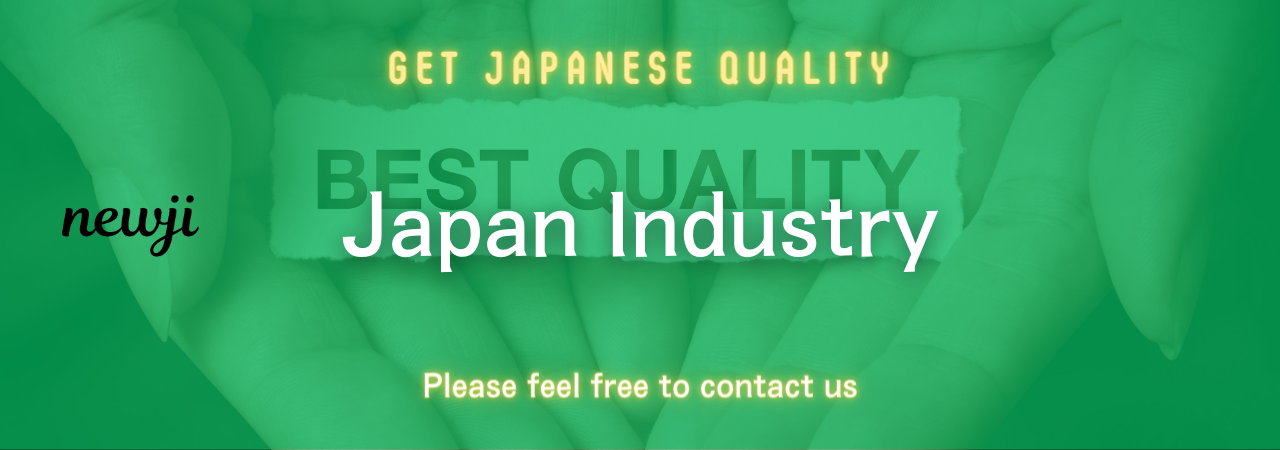
目次
Understanding Supplier Contract Reviews
For leaders in the purchasing department, conducting supplier contract reviews is a crucial part of ensuring smooth operations and cost efficiency.
Reviewing these contracts allows businesses to maintain quality standards, manage risks, and foster strong supplier relationships.
It’s not just about reading through documents; it’s about strategically analyzing the terms to align them with company goals and changing market conditions.
Why Supplier Contract Reviews Are Important
Conducting regular supplier contract reviews helps in identifying areas where terms may need updating.
This includes changes in pricing, delivery schedules, or quality standards that reflect the current business environment.
Effective contract reviews help prevent misunderstandings and potential conflicts with suppliers.
This process ensures that both parties are clear about their roles and responsibilities, which aids in building trust and long-term partnerships.
Timing is Everything: When to Review Supplier Contracts
Annual Reviews
An annual review of supplier contracts can help identify any changes in the market that could affect the terms of the agreement.
This is an opportunity to renegotiate better terms, especially if the company’s purchasing needs have changed or if the supplier’s circumstances have shifted.
Reviews at this frequency help ensure that the contract remains beneficial for both parties and align with the company’s strategic objectives.
Before Contract Renewals
Reviewing contracts before they are up for renewal is vital.
This involves assessing whether the supplier has met their commitments and whether any new market developments should be considered in the renewal terms.
It also allows leaders to decide if moving to another supplier might offer better terms or services.
When Significant Changes Occur
Besides annual reviews and renewals, contracts should be reviewed whenever there are significant changes in the company, supplier, or market.
This could include new product launches, changes in supply chain logistics, or shifts in market trends that could affect the supply and demand balance.
These changes might require an immediate adjustment of terms to maintain competitiveness and maintain a steady supply chain.
Key Points to Consider During a Supplier Contract Review
Price and Cost Structures
Pricing terms are perhaps the most scrutinized part of any contract.
During a review, it’s essential to examine the cost structures to ensure they remain competitive and fair.
Negotiating better pricing or discounts based on volume can significantly impact the bottom line.
It’s also crucial to evaluate whether the cost terms align with market conditions and competitive benchmarks.
Delivery and Lead Times
Timeliness in delivery is critical for maintaining inventory levels and ensuring customer satisfaction.
Analyzing delivery terms can highlight whether lead times are being met or if adjustments are needed.
Considering alternative delivery strategies, like just-in-time shipping, might provide efficiencies that reduce costs and improve service levels.
Quality Requirements
Ensuring that the quality specifications outlined in the contract are met is fundamental for maintaining product standards.
A review allows for an evaluation of supplier performance in terms of quality and the identification of areas for improvement.
This is also a good time to assess compliance with industry standards and regulations.
Performance Metrics
Contracts should include performance metrics or key performance indicators (KPIs) to evaluate supplier performance.
During a review, these metrics can be analyzed to determine if the supplier is meeting expectations.
If they are not, this could be a prompt for renegotiation or seeking alternative suppliers.
Risk Management
Supplier agreements should include risk management clauses covering potential supply chain disruptions or quality issues.
Assessing these terms during a review can help identify and mitigate risks.
Adding or enhancing clauses related to liability, insurance, or contingency plans can protect the company from unforeseen events.
Best Practices for Conducting Supplier Contract Reviews
Involve Multiple Stakeholders
Involving various departments such as legal, finance, and operations in the review process can provide a comprehensive assessment.
Each department might offer unique insights into the effectiveness of contract terms and suggest improvements.
Maintain Clear Documentation
Documenting all changes and negotiations made during the review process is important for maintaining clarity and transparency.
This documentation can serve as a reference for future reviews and assist in resolving disputes.
Use Technology Tools
Leverage technology tools to streamline the contract review process.
Contract management software can help organize contracts, track performance metrics, and manage timelines, making the process more efficient and error-free.
Conduct Regular Training
Regularly train your team on best practices related to contract reviews.
Ensuring that all members are knowledgeable about current procedures can enhance the effectiveness of the review process and improve negotiation outcomes.
Conclusion
Supplier contract reviews are integral to maintaining a healthy supply chain and optimizing purchasing strategies.
By understanding the importance of timing, focusing on key contract elements, and utilizing best practices, purchasing department leaders can ensure that supplier agreements are beneficial and future-proof.
These reviews not only safeguard the company’s interests but also pave the way for stronger, more collaborative supplier relationships.
資料ダウンロード
QCD調達購買管理クラウド「newji」は、調達購買部門で必要なQCD管理全てを備えた、現場特化型兼クラウド型の今世紀最高の購買管理システムとなります。
ユーザー登録
調達購買業務の効率化だけでなく、システムを導入することで、コスト削減や製品・資材のステータス可視化のほか、属人化していた購買情報の共有化による内部不正防止や統制にも役立ちます。
NEWJI DX
製造業に特化したデジタルトランスフォーメーション(DX)の実現を目指す請負開発型のコンサルティングサービスです。AI、iPaaS、および先端の技術を駆使して、製造プロセスの効率化、業務効率化、チームワーク強化、コスト削減、品質向上を実現します。このサービスは、製造業の課題を深く理解し、それに対する最適なデジタルソリューションを提供することで、企業が持続的な成長とイノベーションを達成できるようサポートします。
オンライン講座
製造業、主に購買・調達部門にお勤めの方々に向けた情報を配信しております。
新任の方やベテランの方、管理職を対象とした幅広いコンテンツをご用意しております。
お問い合わせ
コストダウンが利益に直結する術だと理解していても、なかなか前に進めることができない状況。そんな時は、newjiのコストダウン自動化機能で大きく利益貢献しよう!
(Β版非公開)