- お役立ち記事
- A must-see for design department managers in the plastic molding industry! Design and prototyping of high-strength parts using insert molding
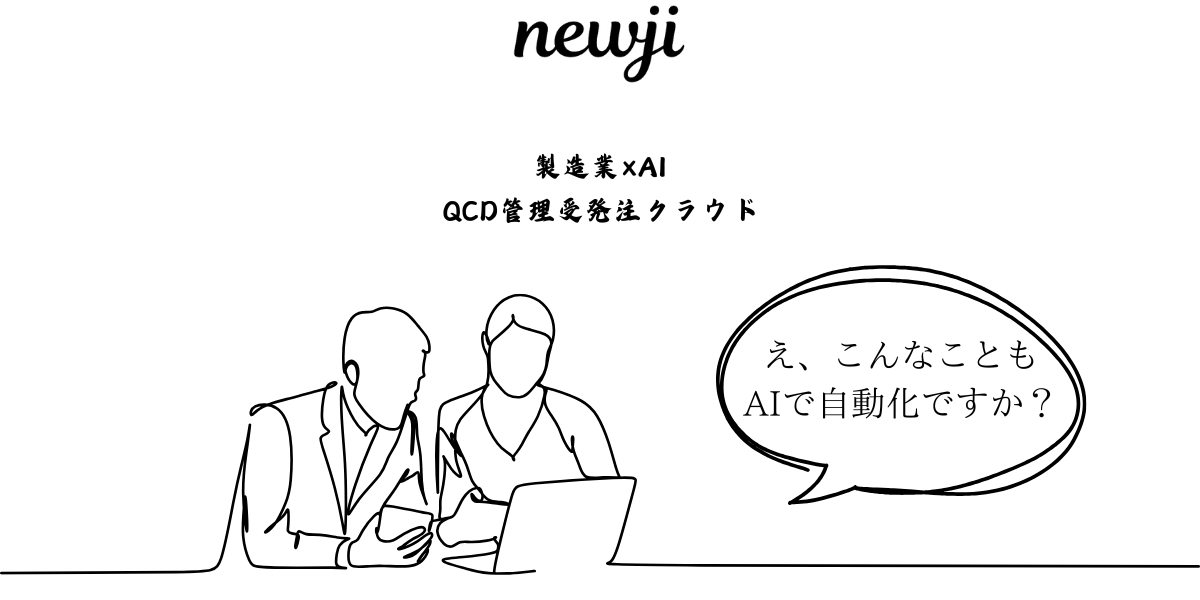
A must-see for design department managers in the plastic molding industry! Design and prototyping of high-strength parts using insert molding
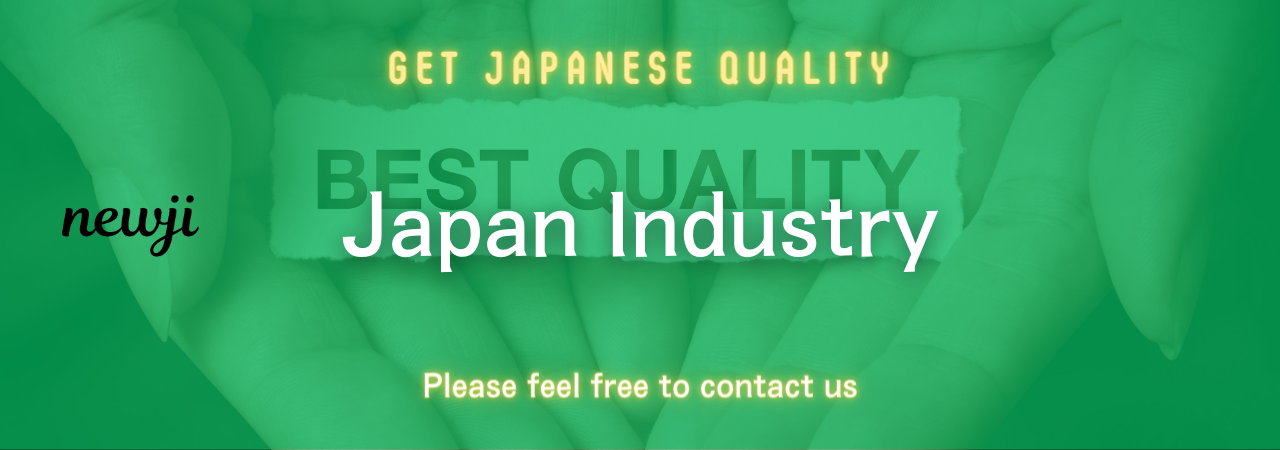
目次
Understanding Insert Molding
Insert molding is an efficient and innovative manufacturing process that combines the potential of plastic molding with the strength and durability of metal inserts.
In the realm of the plastic molding industry, this technique has gained significant traction.
It provides a means to fabricate high-strength parts that cater to various industrial needs.
For design department managers, understanding this process can offer a competitive edge, enabling them to create parts that are both robust and reliable.
Insert molding involves placing a pre-formed metal or different material insert into the mold cavity.
Afterward, molten plastic is injected into the mold, encasing the insert.
Once the plastic cools and solidifies, the result is a single component with enhanced mechanical properties, thanks to the integration of the insert.
This method is particularly beneficial in applications where complex parts with precise performance criteria are required.
The Benefits of Insert Molding
The primary advantage of insert molding is the enhancement of part strength.
By incorporating metal or other durable materials, the final product boasts increased tensile strength, rigidity, and resistance to environmental factors.
This is crucial for industries needing parts that can endure high-stress conditions, such as automotive, aerospace, and consumer electronics.
Insert molding also reduces assembly costs and time.
Instead of manufacturing separate components and assembling them post-production, insert molding integrates components into a single piece.
This simplification cuts down on labor and material costs, and improves production efficiency.
Additionally, it minimizes the potential for part misalignment during assembly, resulting in more consistent quality.
Another significant benefit is the design flexibility insert molding offers.
Designers can experiment with complex geometries and intricate designs that might be challenging with traditional molding processes.
The ability to embed various inserts—metal, ceramic, or even different plastics—opens new avenues for innovation in design.
Applications of Insert Molding
Insert molding is employed in a multitude of industries to create parts that meet specific functional requirements.
In the automotive industry, for example, insert molding is used to produce components like gear knobs, electronic housings, and engine parts that require both plastic and metal features.
In consumer electronics, manufacturers use insert molding to create durable and lightweight handheld devices.
The medical industry also heavily relies on insert molding.
Medical devices often demand components that are strong, lightweight, and biocompatible.
Insert molding meets these needs by incorporating metal shafts or connectors into plastic housings, providing components that are not only strong but also safe for medical use.
The Role of Design Managers
For design department managers in the plastic molding industry, understanding the nuances of insert molding is vital.
These professionals must ensure that design specifications align with the capabilities and limitations of the insert molding process.
Effective communication with the engineering and production teams is key to translating design ideas into production-ready parts.
Design managers should collaborate closely with mold designers to ensure the inserts fit seamlessly within the mold.
This requires a keen understanding of material properties, shrinkage rates, and cooling times which can affect the fit and finish of the final product.
Ensuring compatibility between the insert material and the plastic is also essential to prevent issues like warping or weak adhesion.
Prototyping with Insert Molding
Prototyping is an essential step in the product development process, and insert molding offers unique advantages when creating prototypes.
Prototypes can be produced to test various design iterations and material combinations before committing to full-scale production.
This not only helps in catching design flaws but also in optimizing design for cost, functionality, and manufacturability.
Managers should consider rapid prototyping techniques such as 3D printing for quick iteration and testing of designs.
While 3D printing an insert-molded part is challenging due to the composite materials involved, 3D printing can still be used for initial prototypes to evaluate overall design and fit.
Implementing Insert Molding Strategies
To successfully implement insert molding strategies, design managers must be adept at balancing cost, design complexity, and material properties.
Choosing the right combinations of plastic and insert materials is crucial.
Engineers must consider how these materials behave under various industrial conditions, such as high temperatures or corrosive environments.
A holistic approach to design and prototyping also means exploring potential post-processing needs.
Some insert-molded parts might require additional machining, coating, or assembly once the molding process is complete.
Incorporating these steps into the initial design phase will save time and resources.
Furthermore, quality control measures must be stringent when dealing with insert-molded parts to ensure structural integrity and functionality.
Regular testing and inspection procedures should be in place to catch defects early in the production cycle.
Conclusion
Insert molding stands as a powerhouse technique in the plastic molding industry, offering solutions for creating high-strength, reliable, and complex parts.
For design department managers, mastering this technique means unlocking efficient production processes and innovative design possibilities.
By thoroughly understanding insert molding’s benefits and applications, and by fostering strong collaboration with engineering teams, managers can significantly enhance their company’s competitive edge.
Through careful planning and execution, the effective implementation of insert molding can lead to cost savings, improved product quality, and expanded market opportunities.
資料ダウンロード
QCD調達購買管理クラウド「newji」は、調達購買部門で必要なQCD管理全てを備えた、現場特化型兼クラウド型の今世紀最高の購買管理システムとなります。
ユーザー登録
調達購買業務の効率化だけでなく、システムを導入することで、コスト削減や製品・資材のステータス可視化のほか、属人化していた購買情報の共有化による内部不正防止や統制にも役立ちます。
NEWJI DX
製造業に特化したデジタルトランスフォーメーション(DX)の実現を目指す請負開発型のコンサルティングサービスです。AI、iPaaS、および先端の技術を駆使して、製造プロセスの効率化、業務効率化、チームワーク強化、コスト削減、品質向上を実現します。このサービスは、製造業の課題を深く理解し、それに対する最適なデジタルソリューションを提供することで、企業が持続的な成長とイノベーションを達成できるようサポートします。
オンライン講座
製造業、主に購買・調達部門にお勤めの方々に向けた情報を配信しております。
新任の方やベテランの方、管理職を対象とした幅広いコンテンツをご用意しております。
お問い合わせ
コストダウンが利益に直結する術だと理解していても、なかなか前に進めることができない状況。そんな時は、newjiのコストダウン自動化機能で大きく利益貢献しよう!
(Β版非公開)